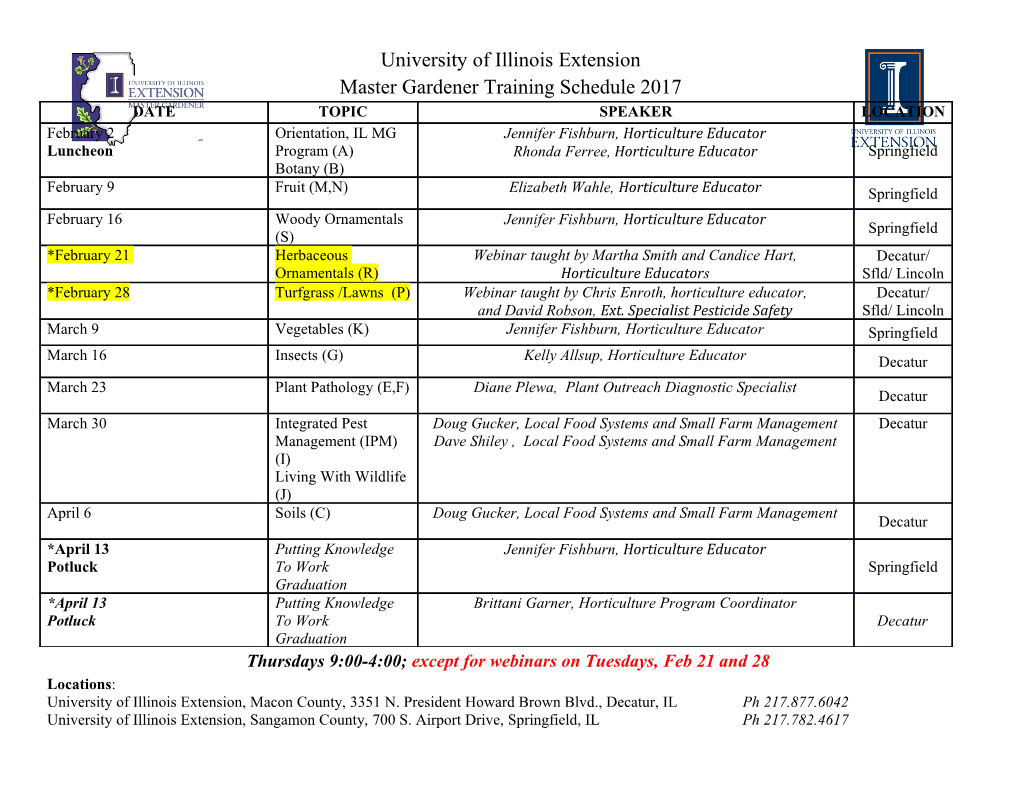
E AMEICA SOCIEY O MECAICA EGIEES 92-GT-405 4 E. 4 S., ew Yok, .Y. 00 h St hll nt b rpnbl fr ttnt r pnn dvnd In ppr r n d n t tn f th St r f t vn r Stn, r prntd In t pbltn. n rnt nl f th ppr pblhd n n ASME rnl. pr r vlbl fr ASME fr fftn nth ftr th tn. rntd n USA Copyright © 1992 by ASME ig essue aio Iecooe uoo Suy C. OGES Downloaded from http://asmedigitalcollection.asme.org/GT/proceedings-pdf/GT1992/78941/V002T02A028/2401669/v002t02a028-92-gt-405.pdf by guest on 23 September 2021 Sundstrand Power Systems San Diego, CA ASAC NOMENCLATURE High altitude long endurance unmanned aircraft impose KFT Altitude Thousands Feet unique contraints on candidate engine propulsion systems and HP Horsepower types. Piston, rotary and gas turbine engines have been proposed for such special applications. Of prime importance is the HIPIT High Pressure Intercooled Turbine requirement for maximum thermal efficiency (minimum specific Mn Flight Mach Number fuel consumption) with minimum waste heat rejection. Engine weight, although secondary to fuel economy, must be evaluated Mls Inducer Mach Number when comparing various engine candidates. Weight can be Specific Speed (Dimensionless) minimized by either high degrees of turbocharging with the Ns piston and rotary engines, or by the high power density Exponent capabilities of the gas turbine. pps Airflow The design characteristics and features of a conceptual high SFC Specific Fuel Consumption pressure ratio intercooled turboprop are discussed. The intended application would be for long endurance aircraft flying TIT Turbine Inlet Temperature °F at an altitude of 60,000 ft.(18,300 m). It is estimated that such a Weight lbm turboprop would be capable of thermal efficiencies exceeding 40% with current state—of—the—art component efficiency levels EI Intercooler Effectiveness and an overall compressor pressure ratio of 66.0. Projected E Regenerator Effectiveness Power (at altitude) to weight ratio is comparable to that of competitive piston and rotary engines. AP/P Cycle Pressure Drop Ratio rntd t th Intrntnl G rbn nd Arnn Cnr nd Exptn Cln, Grn n 4, 2 1.0 INTRODUCTION This paper describes the extension of the HIPIT concept studies to very high altitude long endurance aircraft applications. The study of propulsion systems for very high altitude It discusses engine design point performance optimization, part prolonged endurance aircraft is addressed in References 1.2 and load performance, and preliminary engine design configurations. 3. In summary. these reNrences indicate: • The major engine design constraint is low specific fuel 2.0 GAS TURBINE CYCLE OPTIONS consumption (SFC). Gas turbine engine thermal efficiencies greater than 40% • SFC's below 0.30 lb/hp-hr (thermal efficiency 44%) are (SFC 0.33 lb/hp.hr) can be obtained by the incorporation of desired. compressor intercooling and/or exhaust heat regeneration. • Engine design is optimized at the high altitude (60 KFT or Downloaded from http://asmedigitalcollection.asme.org/GT/proceedings-pdf/GT1992/78941/V002T02A028/2401669/v002t02a028-92-gt-405.pdf by guest on 23 September 2021 The simple cycle (non-heat exchanged) gas turbine has higher) loiter condition, with ambient air temperatures as low dominated in aircraft applications, since the additional weight as -70°F. and volume of the heat transfer surfaces becomes excessive for • Engine weight can be reduced without compromising SFC. typical aircraft operational profiles. Since higher thermal efficiencies are paramount to the operational success of Both liquid cooled spark ignition piston and gas turbine prolonged endurance aircraft, comparative cycle computations engine propulsion systems have been successfully demonstrated were analyzed for intercooled, intercooled and regenerative, and in high altitude aircraft. This is confirmed by the Boeing regenerative engine configurations. Figure 2 shows the results "Compass Cope" and "Condor" aircraft research programs. and the cycle computations for operation above the tropopause, Rotary Wankel stratified change internal combustion engines are and from which the following is concluded: also being studied. The major attribute of both the piston and Wankel engines is essentially flat rated output power with • All three engine configurations are estimated to provide altitude made possible by high pressure turbocharging and/or SFC's in the 0.3 lb/hp.hr realm. turbocompounding. In contrast, gas turbine turboprop output power decreases rapidly with altitude (air density) as typified by • Higher pressure ratio improve the straight intercooled cycle the power lapse rate conditions shown in Figure 1 for constant performance. speed and turbine inlet temperature. Further power decrements • Lower pressure ratios improve the regenerative and occur as a function of operation at extremely low Reynolds regenerative intercooled cycle efficiency. numbers. When constrained to operate at constant speed and turbine inlet temperature with a Reynolds exponent of 0.09, • Turbine inlet temperature has less influence on straight Figure 1 indicates a power lapse rate less than 0.1, accompanied intercooled engine cycle efficiency than the regenerative by increasing SEC. This would imply that a typical turboprop engine configuration. rated at 4000 hp at sea level would deliver less than 400 hp at Reference 5 indicated the feasibility of a very efficient gas altitudes approaching 60 KFT turbine cycle incorporating both intercooling and regenerative Turboprops are, however, capable of delivering very high heat exchange, with moderate pressure ratios for a twin engine specific power hp/lb engine weight and dominate in aircraft light aircraft application. As yet, however, the heat exchanger propulsion applications above 500 hp. has found limited usage in aircraft applications. It presents more mechanical complexity than the lower temperature intercooler. The results of a trade study of various propulsion systems for Fundamental problems with high temperature heat exchangers high altitude, long endurance aircraft are described in Reference are creep, and eventual leakage causing engine performance 1. An advanced intercooled and regenerated gas turbine engine deterioration. The high exhaust volume flows at very high concept was estimated to be capable of delivering SFC's below altitudes also tend to either increase the gas side pressure drop or 0.30. Further investigation of the concept was, however, enlarge the gas side flowpath. recommended to assess geometry and weight of the intercooler and regenerator. Table 1 lists the advantages and disadvantages of all three options. Although the intercooled regenerative cycle Independent studies have been conducted by the author on a incorporates the best of both approaches, it results in the most high pressure intercooled turbine (HIPIT) described in complex flowpath. and also incorporates the worst of both Reference 4. approaches - the regenerator. 2 TABLE 1. COMPARISON OF ENGINE CONFIGURATIONS TYPE ADVANTAGES DISADVANTAGES Intercooled • No high temperature heat • Requires very high pressure ratios transfer surfaces • Reduced leakage potential • High number of stages • Small, responsive high pressure • Intercooling spool • Interco°ler heat rejection Downloaded from http://asmedigitalcollection.asme.org/GT/proceedings-pdf/GT1992/78941/V002T02A028/2401669/v002t02a028-92-gt-405.pdf by guest on 23 September 2021 • High specific air power Regenerative • Low pressure ratio, reduced • Low specific power number of stages • Requires high effectiveness with very large regenerator • High leakage • Poor transient response • Variable geometry for best part load fuel economy • Fouling Regenerative • Lower stage number than • Complicated ducting to Intercooled intercooled both intercooler and regenerator • All regenerative issues including fouling In effect, the choice lies between large hot surface power (hp/w pps) and specific weight (hp/lb), plus aircraft regeneration with simple (single—stage) turbomachinery, lower endurance trends. cold surface intercooling with multistage turbomachinery, or a combination of both. The utilization of very high cycle overall pressure ratios, resulting in lower final exhaust temperatures, has suggested the The use of ultra—high pressure ratios also alleviates the possibility of exhaust reheat. Exhaust reheat would occur prior problem of maintaining high combuster efficiency at high to the final work production expansion stage for power boosting altitudes. Figure 1 shows that the combustor loading parameter purposes during intermittent emergency mode operation. increases up to five times that at sea level. A pressure at 60 K The concept is based on a Brayton cycle machine with very ratio of at least 30:1 would be required to maintain optimum high overall pressure ratio and compressor intercooling. This loading for a given combustor volume. combination produces high thermal efficiency, high specific power and excellent part—load fuel economy. .0 HIP1T CONCEPT Extensive baseline studies of the HIPIT concept have been conducted (Ref 5). They verify that the approach is uniquely Recent applications of small radial (centrifugal) compressors capable of meeting future challenging thermal efficiency and turbines have demonstrated their capability to deliver very directives. high overall pressure ratios when triple spooled with intercoolers. For example, with effective intercooling and a A conceptual HIPIT engine schematic arrangement is shown stage pressure ratio of approximately 4.0, an overall compressor in Figure 4 and comprises
Details
-
File Typepdf
-
Upload Time-
-
Content LanguagesEnglish
-
Upload UserAnonymous/Not logged-in
-
File Pages11 Page
-
File Size-