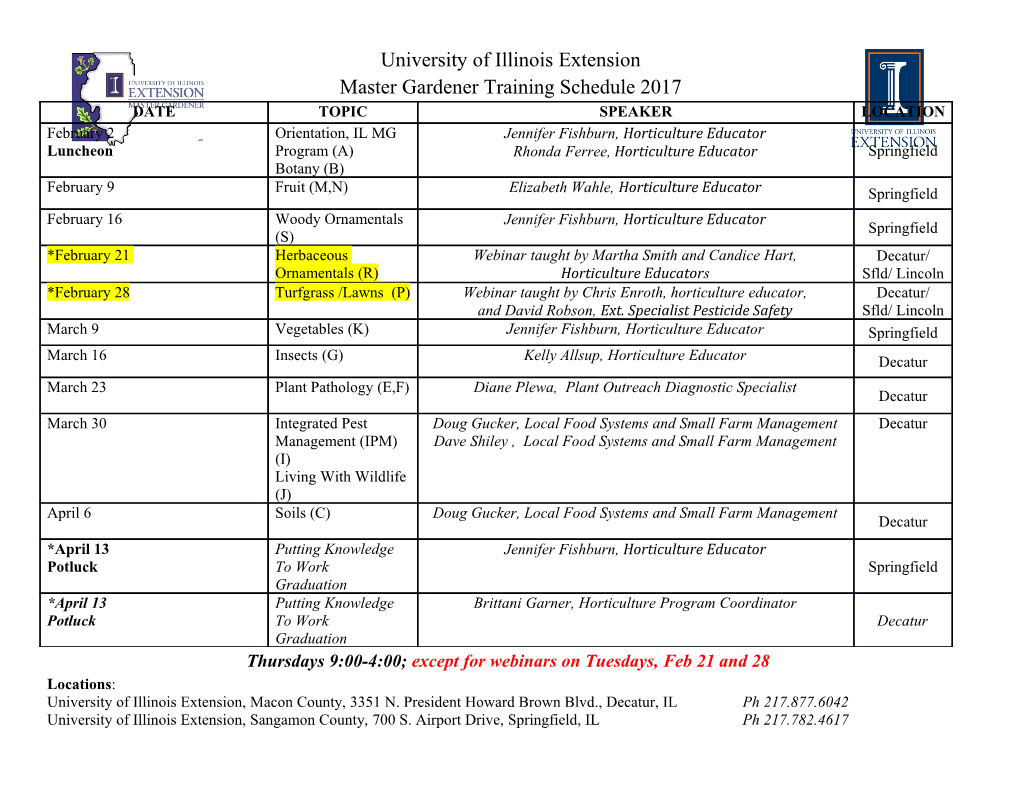
SP700-B UTBiofuelsInitiative Ethanol: A Primer Samuel Jackson, Research Associate Office of Bioenergy Programs Introduction Ethanol has become a major within our nation’s borders. fermenting sugars or converted player in alternative fuels over the The feedstocks, conversion and starch into alcohol. The chemical last few years. Our nation uses distribution all take place within makeup of ethanol is the same, approximately 384 million gallons the country. With recent federal whether it is made from grains of gasoline each day. That amounts legislation, national goals are to or plant materials. It is primarily to more than 140 billion gallons replace 30 percent of our petroleum produced from corn grain, but each year. The United States consumption with biofuels, such as can also be made from the sugar imports approximately 60 percent ethanol. Tennessee currently has, in cellulosic biomass. Cellulosic of the oil it uses. A significant installed or under development, biomass is simply plant material portion of that oil is imported from about 480 million gallons per year from which sugar is extracted. countries that are not stable and of ethanol production capacity. It is Ethanol can be burned, much like are in volatile parts of the world. projected that between corn-based gasoline, to produce energy that Many citizens feel that from a ethanol and cellulosic ethanol, powers vehicles and machinery. national security standpoint, it Tennessee has the potential to is in the nation’s best interests to produce at least 1 billion gallons Producing Ethanol from Grain reduce our reliance on foreign of ethanol each year, replacing 30 Traditionally, alcohols, including sources of energy, such as oil, and percent of its gasoline consumption. ethanol, have been produced from move to renewable, domestically corn and other grains. Corn is the produced fuels. Ethanol is an ethyl alcohol that can primary choice, because a kernel be used as a liquid fuel. It is made of corn is approximately two-thirds Ethanol is one of these renewable up of oxygen, hydrogen and carbon starch, the component that ethanol fuels that can be produced (CH3CH2OH ). Ethanol is made by manufacturers depend upon. In early 2008, production levels of corn ethanol reached 8.1 billion gallons per year at 143 plants in the United States. The type of corn used for ethanol production is called field corn and is not the “sweet” corn used for human consumption. A general expectation of corn ethanol is that one bushel of corn produces 2.8 gallons of fuel. Two primary methods are used to produce ethanol from corn: wet milling and dry milling. The wet milling process begins when the grain is soaked in a dilute water and acid mixture for one to two days. The soaking begins to break Switchgrass is one of the materials that can be used to produce ethanol from the corn down into the more simple cellulose. Credit: Marie Walsh, University of Tennessee compounds and chemicals of which it is made. The resulting mixture, UTBiofuelsInitiative 2 or slurry, is then passed through a most common organic compounds release of cellulose for ethanol variety of separation procedures to on earth. By using cellulose to conversion. A dilute acid solution separate out four main parts: corn oil, create ethanol, a wide variety of can also be used as a pretreatment. gluten, fiber and starch. The corn oil, new sources of sugar are available gluten and fiber are often dried and for ethanol production, and Next, the biomass goes through a sold as animal feeds. This product is producers do not have to rely on a process called enzymatic hydrolysis. very high in protein content and is in specific grain commodity. Materials This process uses plant enzymes to demand by animal producers. commonly used for cellulosic initiate specific chemical reactions. ethanol include corn stalks, wood The pretreatment process allows The starch is put into a fermentation residues and chips, wheat straw, enzymes to gain access to the process, a step that can take up to 50 fast-growing trees, native grasses cellulose in the plant cells. The hours. Yeast is added to the starchy and sugarcane. reactions caused by the enzymes “mash” − as it was called in the break the cellulose molecules moonshine days − and the mixture Cellulosic ethanol technologies, down to simple sugars. Once this is stirred. The yeast metabolizes the however, are not as well developed process is complete, the sugars are starch, in the absence of oxygen, as the grain technologies. The separated and fermented and produces ethanol and carbon primary difference between the into ethanol. dioxide in the process. The resulting two is that it is difficult to access liquid is called “beer,” and it is and free the cellulose in plant Regardless of how the ethanol is transferred to distillation columns cells. Another challenge lies in produced, a key step at the end of where the ethanol is separated from converting cellulose to simple the process is to blend the pure the residual mash. The ethanol sugars for fermenting. Two different ethanol with about 5 percent is then processed to remove any processes, biochemical conversion denaturant, most often regular residual water, and once that is and thermochemical conversion, gasoline. This blending makes complete, the result is pure ethanol. can be used to access cellulose and the ethanol undrinkable and not convert it into simple sugars. Once subject to the alcohol tax placed on In the dry milling process, the corn these processes are complete, the alcoholic beverages. grain is ground into flour called fermentation process is identical to “meal.” The component parts of the ethanol made from grain. Common Concerns about grain are not separated out here, Ethanol Production as in the wet milling method. The In the thermochemical process, Oftentimes, biofuels are evaluated meal is mixed with water and forms cellulosic biomass is gasified. for how much energy it takes to the mash. Enzymes, proteins that Gasification is where the biomass produce the fuel versus the amount accelerate chemical reactions, are is quickly superheated in a of energy provided by the fuel. added to the mixture and convert the low-oxygen environment. This This is called the fossil energy starch to dextrose, a simple sugar. produces a gas called “syngas” and ratio. For corn ethanol, the fossil The mash is then heated to a high a residue called “char.” Syngas is energy ratio is 1.8. For cellulosic temperature to kill any bacteria primarily made up of hydrogen ethanol, the ratio is at least 5 and, prior to fermentation. After heating, and carbon monoxide. The syngas in some studies, as high as 10. In the mash is fermented in a similar is then passed through a specially other words, for every unit of fossil method to wet milling. In dry milling, designed reactor, where catalysts energy it takes to make ethanol, the mash left after fermentation is turn the gas into ethanol. The char at least 1.8 units of equivalent dried and sold as dried distillers grains can be used as fertilizer or in other energy is produced. We get more with solubles (DDGS) as an animal products. energy out of ethanol than it takes feed. The carbon dioxide from the to produce it. Gasoline has a fossil process can be captured and often In the biochemical process, living energy ratio of 0.8, meaning it takes used for other purposes, such as organisms, enzymes, are used more energy to produce than is carbonating soft drinks. to convert cellulosic biomass to provided by the end fuel. ethanol. The biomass is brought Producing Ethanol from into the conversion facility and Another common concern related Cellulosic Materials typically ground or chopped into to ethanol production is odor Another source of sugars to small pieces. It is then subjected to produced in the manufacturing manufacture ethanol comes from a high-pressure steam treatment, process. The primary source of cellulose, which is found in the which starts breaking down the odor in a corn ethanol plant is walls of plant cells and is one of the plant cell walls and begins the the dried distiller’s grains with UTBiofuelsInitiative 3 solubles (DDGS). Prior to being prices increase, so do costs of sold as animal feed, DDGS are things depending upon petroleum. dried. This process produces Fertilizer, herbicides and pesticides aldehydes, ketones and lactic acid, that crop producers depend upon all of which combine to produce a are derived in some way from foul odor. New technologies allow petroleum. Input costs have gone producers to minimize the impacts up dramatically since 2007, with of these odors by using scrubbing some herbicide and pesticide costs technologies to neutralize the smell. doubling. Fuel costs for planting, Cellulosic ethanol facilities do not harvesting and transporting corn have this odor problem as they have also increased. Concern has have no DDGS. Another source also been raised about the amount of odor is from the fermentation of corn exported from the US to procedure, and the exhaust it other countries. Many nations produces. Both corn and cellulosic depend upon our corn for their ethanol plants must contend with food supplies. In reality, though, US this issue. Scrubber technology corn exports have increased, up 6 is used here as well. The exhaust percent between 2006 and 2007, to is passed through the scrubbers, their highest levels since 1990. where organic materials responsible E-85 dispensers are clearly labeled. You for the odor are removed prior to All of these factors, including can see the yellow gas cap indicating a release from the plant. demand, have affected corn prices. flex fuel vehicle in the background. Credit: Higher corn prices may impact food Sam Jackson, University of Tennessee Water usage in producing ethanol markets, as it will cost more to feed is also an issue.
Details
-
File Typepdf
-
Upload Time-
-
Content LanguagesEnglish
-
Upload UserAnonymous/Not logged-in
-
File Pages4 Page
-
File Size-