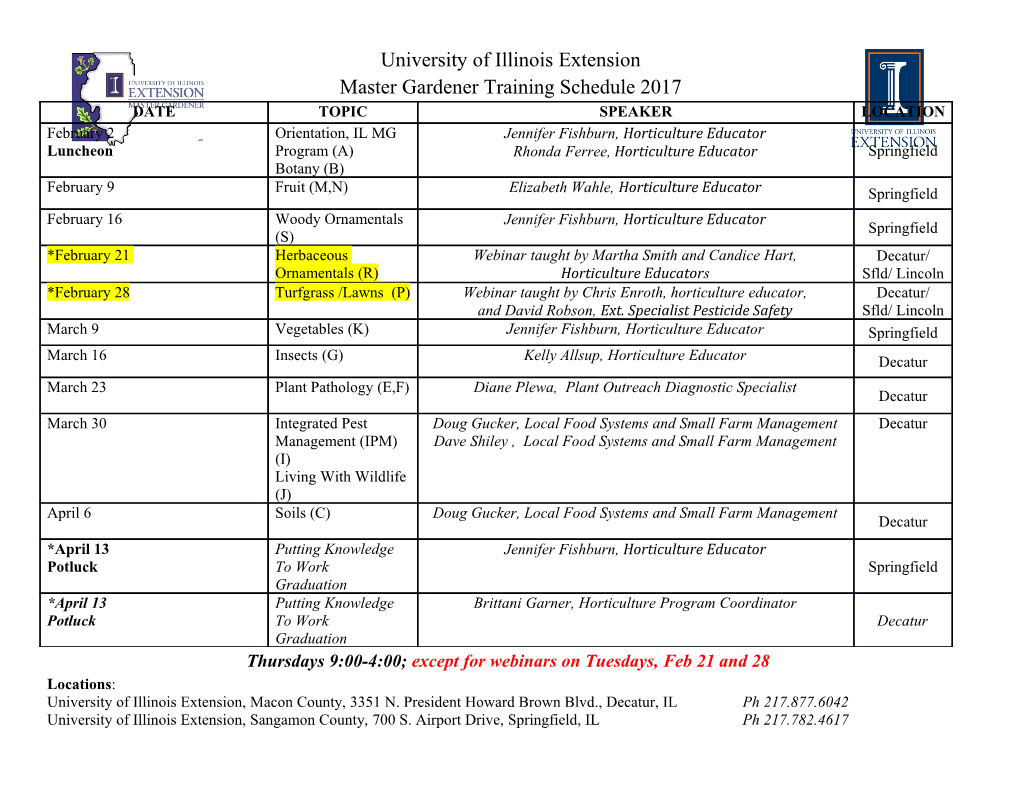
Journal of Oleo Science Copyright ©2011 by Japan Oil Chemists’ Society J. Oleo Sci. 60, (5) 237-265 (2011) REVIEW Development, Characterization and Commercial Application of Palm Based Dihydroxystearic Acid and Its Derivatives: an Overview Gregory F. L. Koay1, 2, Teong-Guan Chuah1, 3* , Sumaiya Zainal-Abidin2, 4, Salmiah Ahmad2, 5 and Thomas S. Y. Choong1 1 Department of Chemical and Environmental Engineering, Universiti Putra Malaysia (43400 UPM Serdang, Selangor Darul Ehsan, MALAYSIA) 2 Advanced Oleochemical Technology Division, Malaysian Palm Oil Board (43650 Bandar Baru Bangi, Selangor Darul Ehsan, MALAYSIA) 3 Institute of Tropical Forest and Forestry Products, Universiti Putra Malaysia (43400 UPM Serdang, Selangor Darul Ehsan, MALAYSIA) 4 Faculty of Chemical and Natural Resources Engineering, Universiti Malaysia Pahang (25000 Kuantan, Pahang Darul Makmur, MALAYSIA) 5 Director General’s Offi ce, Malaysian Rubber Board (50450 Kuala Lumpur, MALAYSIA) Abstract: Hydroxyl fatty acids and their derivatives are of high value due to their wide range of industrial application, including cosmetic, food, personal care and pharmaceutical products. Realizing the importance of hydroxyl fatty acids, and yet due to the absence of the conventional starting raw materials, Malaysia has developed 9,10-dihydroxystearic acid (9,10-DHSA) and its derivatives from locally abundant palm based oils. The aim of this article is to provide a general description of the works that have thus far being done on palm based 9,10-DHSA: starting from its conception and production from commercial grade palm based crude oleic acid via epoxidation and hydrolysis, purification through solvent crystallization and characterization through wet and analytical chemistry, moving on to developmental works done on producing its derivatives through blending, esterifi cation, amidation and polymerization, and completing with applications of 9,10-DHSA and its derivatives, e.g. DHSA-stearates and DHSA-estolides, in commercial products such as soaps, deodorant sticks and shampoos. This article incorporates some of the patent fi led technological knowhow on 9,10-DHSA and its derivatives, and will also point out some of the shortcomings in previously published documents and provide some recommendations for future research works in mitigating these shortcomings. Key words: dihydroxystearic acid, epoxidation, crystallization, characterization, ternary blending, esterifi cation, amidation, polymerization, commercial application 1 INTRODUCTION 9,12-DHSA, with the CAS number 26248-95-3, 93923-70-7 Dihydroxystearic acid(DHSA), molecular formula and 25754-87-4 respectively. -1 th C18H36O4, molecular weight(MW)316.476 gmol , is a long DHSA has appeared in literature as early as end 19 and chain fatty acid with IUPAC name dihydroxyoctadecanoic early 20th century. In 1901, Le Sueur1)revealed some of the acid. The name‘ dihydroxy’ indicates that there are two chemical characteristics of DHSA while trying to fuse po- hydroxyl groups present in the molecular structure. There tassium hydroxide on it. Some of the plant based natural are various confi gurations to the positions of these two hy- sources of DHSA include olive and castor oils2, 3)and Sal droxyl groups and a literature search has revealed that fat4). there are more than 30 different DHSA isomers. However, In Malaysia, due to the absence of the above mentioned most of these isomers are not common, let alone cata- three oils and fats, attempt to source for other means to logued in the authoritative CAS registry. The three most produce DHSA was initiated. Through it R&D efforts, the common of the isomers are 2,18-DHSA, 9,10-DHSA and Malaysian Palm Oil Board(MPOB)has successfully pro- *Correspondence to: Teong-Guan Chuah, Department of Chemical and Environmental Engineering, Faculty of Engineering, Universiti Putra Malaysia, 43400 UPM Serdang, Selangor Darul Ehsan, MALAYSIA Email: [email protected] Accepted December 3, 2010 (received for review October 28, 2010) Journal of Oleo Science ISSN 1345-8957 print / ISSN 1347-3352 online http://www.jstage.jst.go.jp/browse/jos/ 237 G. F. L. Koay, T.-G. Chuah, S. Zainal-Abidin et al. duced the 9,10-DHSA isomer from commercial grade palm tic acid in the presence of hydrogen donor such as water. based crude oleic acid, a low value byproduct of palm oil This process has been patent fi led in Malaysia, Singapore industry. and the United States5-7). The body of this article is outlined as follow: The production of 9,10-DHSA via peracetic acid route □ Production of 9,10-DHSA was measured up from laboratory to pilot plant scale of 500 □ Purifi cation of 9,10-DHSA kg per batch operation8). For pilot plant production, per- □ Characteristics of 9,10-DHSA acetic acid was formed in situ in a batch stirred tank reac- □ Characteristics of 9,10-DHSA blends tor(BSTR)(R1)by reacting glacial acetic acid(stored in □ Characteristics of 9,10-DHSA derivatives storage tank T1)and hydrogen peroxide(stored in storage □ Applications of 9,10-DHSA and derivatives tank T2)in the presence of sulphuric acid. The peracetic acid which acted as an oxidizing agent converted the un- saturation in commercial grade palm based crude oleic acid to form an epoxide in a second BSTR(R2). The epoxide 2 PRODUCTION OF 9,10-DHSA was then hydrolyzed to produce crude 9,10-DHSA in the The 9,10-DHSA isomer was first produced by MPOB same BSTR. The crude 9,10-DHSA was water washed and from C18:1 fraction of commercial grade palm based crude gravity separated from spent acid in a settling tank(T3). oleic acid5). This crude oleic acid, of 70~78% purity(Table Alternatively, commercial grade palm based crude oleic 1)was a low value byproduct during extraction of lauric acid was converted via performic acid route8). Performic (C12:0)and myristic(C14:0)acids from palm kernel oil and acid was formed in situ in R2 by reacting formic acid palmitic(C16:0)acid from palm oil. The C18:1 fraction con- (stored in T1)and hydrogen peroxide(stored in T2)in the tained the unsaturation needed for epoxidation and hydro- presence of sulphuric acid. The performic acid converted lysis for eventual production of 9,10-DHSA. The epoxida- the unsaturation in commercial grade palm based crude tion and hydrolysis reactions were carried out by reacting oleic acid to form an epoxide in the same reactor, R2. The commercial grade palm based crude oleic acid with perace- hydrolysis, washing and separating steps were similar to those of peracetic acid route. Table 1 Fatty acid composition (FAC) of The comparison of 9,10-DHSA production via two differ- commercial grade palm based ent routes is shown in Table 2 and the process flow dia- crude oleic acid5) gram is shown in Fig. 1. Fatty acid Composition, % C8:0 0.1 – 0.8 C10:0 Trace – 1.2 3 PURIFICATION OF 9,10-DHSA C12:0 0.9 – 2.4 Due to the nature of commercial grade palm based crude C14:0 0.3 – 1.5 oleic acid as precursor of 9,10-DHSA and the processes C16:0 3.1 – 5.5 and chemicals involved during reaction stage, there was a C16:1 0.1 – 0.3 need to purify the resultant crude 9,10-DHSA. The objec- C18:0 1.2 – 7.6 tive was to nullify its potency in causing dermal irritancy as C18:1 71.4 – 78.0 its development was meant for use in cosmetic and person- C18:2 11.8 – 17.3 al care products. The purifi cation of 9,10-DHSA involved(i) C18:3 Trace – 0.6 solvent crystallization,(ii)solvent removal and(iii)drying8). C20:0 0.1 – 0.5 A two-stage 9,10-DHSA purifi cation operation was fi rst C others To 100 reported8). The solvent was 80% isopropyl alcohol(IPA); IV 87 – 95 crude 9,10-DHSA:solvent mass ratio 1.0:1.0; the crystalliza- AV 180 – 204 tion carried out at 5℃. The first stage crystallization im- Table 2 Comparison of 9,10-DHSA production via performic- and perace- tic- acid routes8) Parameters Peracetic acid route Performic acid route Production yield, % 72.5 96 Production cost Reference 30% cheaper Batch processing time, h 12 10 No. of BSTR required Two, R1 and R2 One, R2 238 J. Oleo Sci. 60, (5) 237-265 (2011) Overview of Palm Based Dihydroxystearic Acid and Its Derivatives Fig. 1 Simplifi ed process fl ow diagrams of 9,10-DHSA production via (a) peracetic- and (b) performic- acid routes8) proved 9,10-DHSA purity from 56.6~58.0% to 70.9%; the second stage improved to 79.9%. The 9,10-DHSA crystals were then separated from solvent through a mechanical vi- brating screen and water washed before being dried. The two stages purifi cation operation was improved to a single stage operation with varying IPA concentrations and solvent ratios, the solvent removed through vacuum fi ltra- tion and the crystals dried thereafter without requiring any washing9). Carried out at room temperature without tem- perature disturbances, it raised 9,10-DHSA purity to 86~ 92%. Solvent concentration and ratio contributed in im- proving crystal purity. Similar operation was also carried out using ethanol as solvent with a minor alteration at the Fig. 2 Schematic diagram of a custom fabricated si- 10) drying . Solvent crystallization of 9,10-DHSA was better multaneous batch crystallization unit11-13) when carried out at room temperature as rapid cooling (carried out at 5℃)caused solvent entrainment which compromised resultant crystal purity. unit was used to study effects of various parameters on The establishment of preliminary 9,10-DHSA purifying 9,10-DHSA purification, including solvent types, cooling method has led to the development of a custom fabricated modes, solvent concentrations and ratios.
Details
-
File Typepdf
-
Upload Time-
-
Content LanguagesEnglish
-
Upload UserAnonymous/Not logged-in
-
File Pages29 Page
-
File Size-