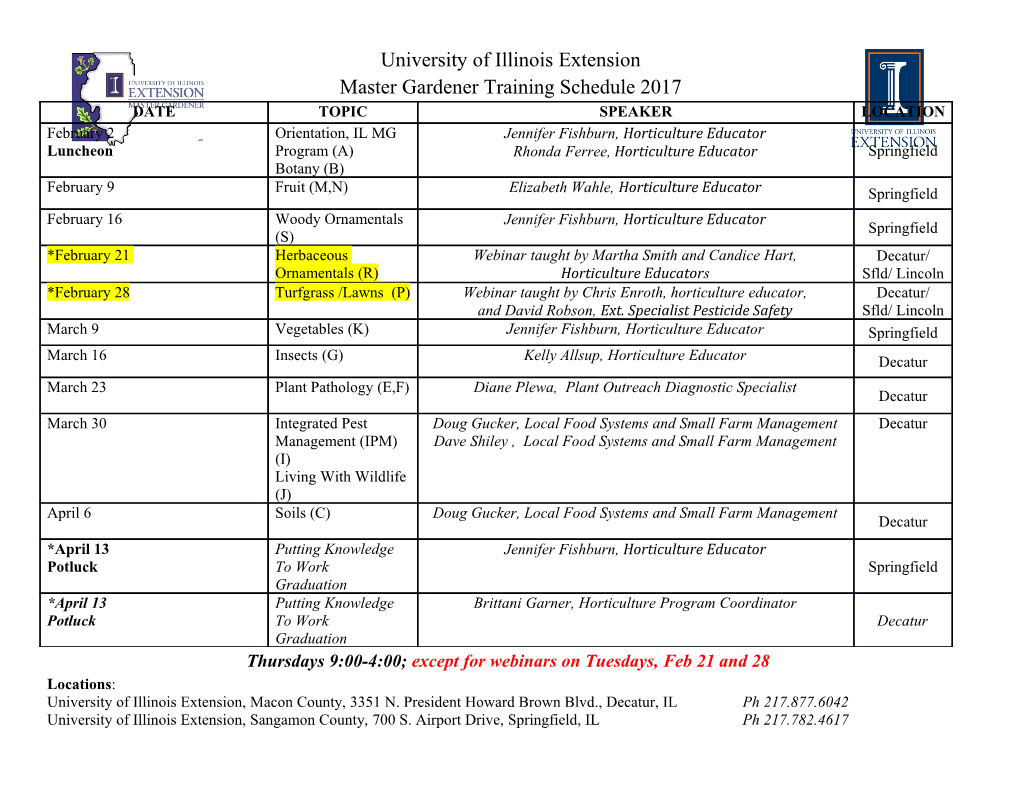
Tri­Rotor Tilt­Wing Remote Controlled Aircraft Final Paper John McNelly & Jeff Barratt Abstract With the announcement of Google and Amazon’s sub­hour product delivery times by using unmanned drones, the public’s focus today has been on quadcopters similar multi­rotor aircraft. However, these multi­copters are inefficient in forward flight and pose many issues with battery weight and overall flight time, unfortunately preventing a long­range delivery service by Amazon, Google, or other companies. The goal of this project is to combine the benefits of both a hover takeoff and landing with efficient forward flight. [1] I. Introduction As the growing Unmanned Aerial Vehicle industry continues to expand into longer­range flights, business ventures like Amazon Prime and Google Wing are looking for aircraft that can perform well in a stable hover (good for dropping packages or loitering in a fixed area) while being capable of efficient, high­speed forward flight (good for getting from a launch point to a destination quickly and with minimal energy use). The typical “drones” that one often sees or hears about consist mainly of a series of motors and propellers fixed upon a solid frame (tricopters, quadcopters, etc). While these multirotor aircraft have few moving parts, making them easy to build and maintain, they are inefficient in fast forward flight. This is due to the fact that multicopters derive 100% of their upwards lifting capability from thrust generated by their propellers. In order to move forward, a portion of the upwards thrust must be devoted to generating horizontal motion, significantly reducing the load­bearing capability of the multicopter unless thrust (and thus power usage) is increased. Fixed­wing aircraft, on the other hand, have no such problem, as they derive most of their upwards lifting capability from lift generated by their airfoils; as their horizontal speed increases, lift generated by the wing also increases, thus increasing the load­bearing capacity with speed. Yet, fixed­wing aircraft lack the ability to hover in place like multicopters can easily do. The ideal solution to this issue would be a combination multicopter and airplane: a VTOL aircraft like the one described in this paper. II. History The idea of a tilt­wing vertical takeoff and landing (VTOL) aircraft that is also capable of short takeoff and landing (STOL) and fast forward flight (FFF) has been explored in the past by a number of military and aerospace agencies. Hiller Aircraft Corp began testing on the X­18 Propelloplane, the first full­scale tiltwing VTOL aircraft, in 1955 (“Hiller X­18,” Wikipedia). That aircraft suffered from stability problems during transitions, and its engines were not cross­shafted, nearly guaranteeing a crash in the event that a single engine failed. Thrust was also controlled by throttle changes, which proved too slow for accurate maneuvers; future aircraft used a cross­linked powertrain to distribute power between multiple engines, and thrust was controlled via propeller feathering. Figures 1 (left):, An X­18 Propelloplane. Figure 2 (right): An LTV XC­142. Images courtesy US Govt. and NASA, respectively. [2] In 1964, Canadair began testing the CL­84 Dynavert, a small twin­engined tiltwing VTOL aircraft with cross­shafted engines, feathering propellers, and a tail rotor (“Canadair CL­84,” Wikipedia). Shortly afterwards, Ling­Temco­Vought began testing its XC­142 VTOL / STOL tiltwing cargo plane. The aircraft also utilized cross­linked engines, feathering props, and a tail rotor, and it was the largest and fastest VTOL aircraft of its time, capable of carrying 32 equipped troops or 8,000 pounds of cargo at speeds of up to 400mph. Similar to the design of the tiltwing described in this paper, the XC­142 had a large, boxy fuselage with a relatively long wingspan and under­wing engine nacelles, and utilized a mix of conventional flight controls (ailerons, elevator, rudder) and differential thrust to maintain control throughout all phases of hover and forward flight. Its main wing was also capable of tilting through an angle of 100 degrees, enabling the aircraft to hover in a tailwind by tilting its wings backwards past 90 degrees vertical. While the XC­142 suffered a few issues stemming from the cross­linked gearbox system, the propellers delivering less­than­expected thrust, and low­altitude instability in STOL mode (some of which, combined with pilot error, resulted in hard landings and crashes), it satisfied all the requirements of the tri­service defense initiative it was designed to fulfill, and the aircraft was supposed to be ordered into production shortly after the 5 prototypes concluded testing. Unfortunately, politics and fiscal problems got in the way, and the XC­142 was never realized, leaving full­scale production of a tilt­wing VTOL as a dream from the past (the X­18 was scrapped due to instability, and the CL­84 never made it into production) (“XC­142,” GlobalSecurity.org). Since then, the Bell­Boeing V­22 Osprey has fulfilled the US Armed Forces’ STOL / VTOL cargo aircraft requirements and has been put into service, but as a tilt­rotor with a fixed wing, its design is wholly different (and much more complex) from the tilt­wing VTOL/STOL aircraft of decades ago. III. Theory Electric Motors Electric Motors are a key component of an aircraft, especially VTOL RC Aircraft. Because they are required for both phases of flight, both in helicopter mode as the main source of lift and thrust, and in forward flight mode as the main source of thrust, the motors must work in a variety of conditions and off of RC parts and batteries. The type of motors used in this project are documented in an earlier paper (Making an Electric Motor; Wong, McNelly, Barratt). However, these motors use back EMF as opposed to Hall sensors to drive the motor. Each motor has an Electronic Speed Control controller (ESC) that calculates which inputs to fire at what times, much like the circuit for our previous motor. The motor spins, also spinning a propellor, which is used to create thrust for the aircraft. Aerodynamics Fixed­wing and tilt­wing aircraft rely on the physical phenomenon of lift to stay aloft. When air flows over a cambered airfoil shape, air is forced to cross a longer distance on the top half of the airfoil than the bottom half of the airfoil. This creates a low­pressure area above the wing and a higher­pressure area below the wing, generating lift that propels the aircraft upwards. This physical phenomenon relies on the airstream remaining connected to the wing during all phases of flight; airflow separation from the trailing edge of the wing results in vortices and turbulent airflow which generate drag and reduce the wing’s lift­generating properties, in an event known as an aerodynamic stall. Sharp [3] edges and other abnormalities in the shape of the wing can cause the airflow to separate easily, especially at larger angles of attack where the airflow is not meeting the wing “straight­on.” Thus, many wings (including the wing on the aircraft described in this paper) use rounded leading edges and long, thin trailing edges in order to prevent the airflow from separating from the surface of the wing. Some aircraft also use vortex generators on their wings in order to stir the air as it passes over the wing, bringing higher­energy airflow from the outer airflow layer closer to the surface of the wing, thus preventing the airflow from separating from the wing surface at low speeds and higher angles of attack. Wings also generate lift through the use of angle of attack relative to the airflow. When the bottom surface of the angled wing encounters an airflow, the airstream is deflected downwards by the wing surface, producing upwards lift. This method of tilting the wing to generate lift can create large amounts of lift (and is thus used by airplanes upon takeoff and in climbout), but also induces a large amount of drag. While this project calculated expected lift utilizing lift­per­unit­area values derived from wind 1 2 tunnel testing, lift can also be calculated via the lift coefficient equation, L = 2ρv ACL , where L is the lift force, ρ is the air density, v is velocity, A is the planform area of the wing, and C is the coefficient L of lift, which is determined by the lift generated by the wing in relation to its surrounding environment (mach number, Reynolds number, angle of attack, etc). Lift can also be calculated using by integrating pressure over the area of the wing, using the equation L = ∮pn ∙ kdA , where L is the lift force, A is the wing surface area, p is the pressure, n is the unit vector normal to the wing, and k is the vertical unit vector normal to the freestream direction (the freestream is the static region of air far enough ahead of the wing that it has not yet been disturbed). Figure 3: Vector diagram of lift generated by an airfoil, where L is the lift force, D is drag, α is angle of attack, N is the unit vector normal to the wing, and R is the resultant force vector. Image courtesy http://www.aerospaceweb.org/question/aerodynamics/systems/airfoil.jpg [4] IV. Design Physical Structure The aircraft’s design is based upon a tri­rotor configuration in VTOL mode, and a twin­engined configuration in fixed­wing mode. During hover, the main wing of the aircraft tilts upwards, allowing the two wing­mounted motors to act in concert with the downward­facing tail rotor to maintain control at zero airspeed.
Details
-
File Typepdf
-
Upload Time-
-
Content LanguagesEnglish
-
Upload UserAnonymous/Not logged-in
-
File Pages17 Page
-
File Size-