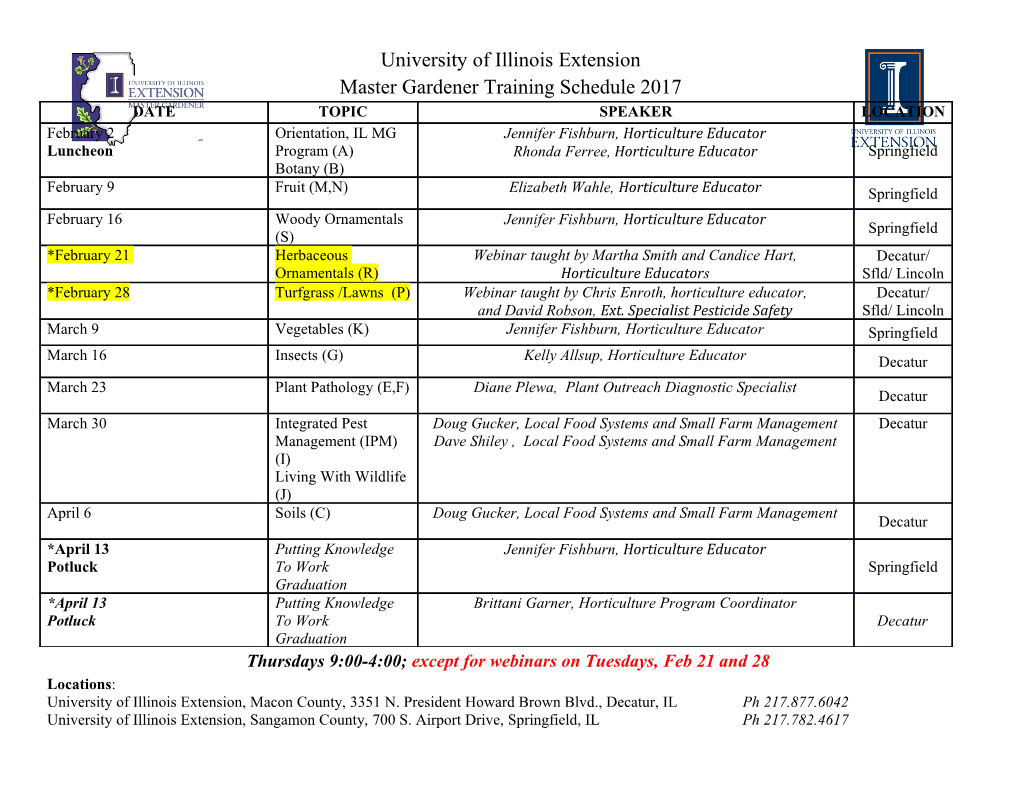
FM&6JIP6 TKK- MK — Xf Thermodynamic analysis of dust sulphation reactions Yongxiang Yang Ari Jokilaakso 7«S» Helsinki University of Technology Publications in Materials Science and Metallurgy ^ _ Teknillisen korkeakoulun materiaalitekniikan ja metallurgian julkaisuja I KK-MK-^7 Helsinki University of Technology Publications in Materials Science and Metallurgy TKK-MK-27 Teknillisen korkeakoulun materiaalitekniikan ja metallurgian julkaisuja TKK-MK-27 Thermodynamic analysis of dust sulphation reactions Yongxiang Yang, Ari Jokilaakso Helsinki University of Technology Department of Materials Science and Rock Engineering Laboratory of Materials Processing and Powder Metallurgy Espoo 1997 Research Program SULA 2 - Energy in steel and metal production Project SULA 2 - 302, Computer simulation of gas-solid reactions in the flash smelting process Financing TEKES - Technology Development Centre, Finland Distribution: Dr. Ari Jokilaakso. Helsinki University of Technology Laboratory of Materials Processing and Powder Metallurgy P.O. Box 6200 FIN-02015 HUT Tel. +358-0-451 2775 Fax.+358-0-451 2799 E-mail: [email protected] ISBN 951-22-3850-0 ISSN 1455-2329 Pica-Set Oy Espoo 1997 DISCLAIMER Portions of this document may be illegible electronic image products. Images are produced from the best available original document. ABSTRACT Sulphation reactions of metal oxides with SO2 and 0% or SO3 play significant roles in sulphation roasting of sulphide and oxide minerals as well as in desulphurisation process of combustion gases. In metallurgical waste-heat boilers for sulphide smelting, the sulphation of the oxidic flue dust in the atmosphere containing sulphur oxides is an unavoidable process, and the sulphation reactions have to be guided in a controlled way in the proper parts of the gas handling equipment. In this report, some thermodynamic analyses were conducted for the oxide sulphation reactions in relation to sulphide smelting processes. The phase stability of Me-S-O systems especially for oxides - sulphates equilibrium was studied under different thermodynamic conditions of gas compositions and temperatures. The sulphate stability was analysed for an example of gas compositions in the copper flash smelter of Outokumpu Harjavalta Metals Oy, in relation to temperature. In the report, most of the information was from literature. Moreover, a number of thermodynamic computations were carried out with the HSC program, and the constructed phase stability diagrams were compared with those from the literature whenever possible. The maximum temperatures for stable sulphates under normal operating conditions of the waste-heat boilers in sulphide smelting processes were obtained. This report will serve as the basis for the kinetic studies of the sulphation reactions and the sulphation reaction modelling in pyrometallurgical processes. CONTENTS 1. INTRODUCTION.......................................................................................................................... 1 2. SULPHATION REACTIONS OF METAL OXIDES WITH SOz AND 020R S03... 3 2.1 Industrial application of oxide sulphation reactions ............................................. 3 2.2 C haracteristics of sulphatton reactions of solid oxides.......................................4 2.3 The need for comprehensive thermodynamics , kinetics and reaction models FOR DUST SULPHATTON............................................................................................................... 5 3. THERMODYNAMICS OF OXIDE - SULPHATE REACTIONS...................................6 3.1 General thermodynamic considerations ........................................................................6 3.2 Analysis of sulphate decomposition in waste -heat boiler environment ............ 8 3.3 Phase stability diagrams for Me-S-0 systems.......................................................... 10 3.3.1 Sulphation of copper oxides.........................................................................................11 3.3.2 Sulphation of nickel oxide.............................................................................................15 3.3.3 Sulphation of cobalt oxides............................................................................................17 3.3.4 Sulphation of zinc oxide................................................................................................20 3.3.5 Sulphation of lead oxide................................................................................................22 3.3.6 Sulphation of iron and manganese oxides................................................................... 23 3.4 Industrial observations ....................................................................................................25 4. SUMMARY....................................................................................................................................26 REFERENCES 27 1 1. INTRODUCTION Pyrometallurgical processing of sulphide concentrates in non-ferrous metallurgical industry involves the production of metals, slags as well as high temperature off­ gases. The generated off-gas contains a significant amount of flue-dust, and it has to be treated properly and economically in order to meet increasingly strict environmental regulation and to minimise the production cost. From operational and process point of view, the off-gas handling is as important as the metal production, and it is actually an integrated part of the whole smelter operation. The flue-gases usually leave the smelting furnace or a converter at about 1200 to 1400°C with high content of S02 and dust loading. They are normally cooled in a waste-heat boiler or in a cooling chamber to capture the dust and optionally to recover thermal energy. Waste-heat boilers have been widely used in copper smelting and in some other non-ferrous pyrometallurgical processes. For example, in Outokumpu flash melting process, the smelting furnaces or converters are always equipped with waste-heat boilers. The waste-heat boilers play a critical role in maintaining the continuous operation of the smelter. As a by-product, smelting and converting operation generates notable amount of flue- dust. The dust, as part of the raw materials, amounts to approximately 1 - 10% of the total feed materials. It has to be captured and returned to the process or treated separately to recover the metal valuables. Dust generation not only reduce the smelting efficiency, but cause a lot of operational problems. Some common problems related the flue-dust in the gas-handling equipment are: (1) build-ups in the uptake conjunction to the boiler or a cooling chamber, needing frequent cleaning; (2) slagging and fouling the heat transfer surfaces in the boilers and gas ducts, which causes substantial cleaning and dust removal work; (3) corrosion and erosion to the heat transfer surfaces and tubes; (4) decreasing heat transfer efficiency due to high resistance from dust layer, which also causes the more serious dust slagging, build-ups and fouling for the increased wall temperature. Therefore, optimised furnace operation with minimised dust rate is one important goal for furnace and smelting development. Under the operation condition of sulphide smelting, the off-gas contains very high S02 such as 10 - 70% in Outokumpu flash smelting process [Biswas and Davenport 1994], and small amount of 02. The flue-dust from the furnace is mainly in oxide forms. The oxide dust will undergo a series of physical and chemical processes along the gas cooling route in this atmospheric thermal environment. In addition to cooling, solidification or agglomeration, the sulphating reactions are unavoidable, which have to be controlled or directed in a preferred way. The metal sulphates normally have lower melting temperature, more sticky and much more corrosive than their parent oxides. The sulphating reaction is substantially exothermic, releasing large amount of heat. The released heat affects the gas cooling and thermal performance of the boiler 2 and subsequent dust capture equipment such as electrostatic precipitator. Because of the gas cooling and increased air in-leakage to the boiler, the dust sulphating is taking place wherever the thermodynamic and kinetic conditions are favourable. The formation of sulphates in flue-gases plays different role in different processes. Because of their high corrosiveness and low melting temperature, their generation and presence are not expected. For instance, in power plant boiler furnaces, the formation and condensation of sulphates from gas phase, especially alkaline sulphates (Na 2S04, K2S04) has very detrimental effect on the boiler tube and other heat transfer surfaces [Cen et al., 1994]. Even the S02 content in the combustion gases is very low (a few per cents) compared to that in sulphide smelting processes, the formation of S03 and sulphates is substantial enough to cause serious corrosion and fouling problems. In copper smelting and other sulphide smelting processes, the formation of metal sulphates differs from those in power plant boiler or other combustion furnaces. The main sulphate components are heavy metals of copper, lead, zinc, nickel or cobalt. The sulphating environment is more supporting, favoured by high S02 or S03, oxygen and catalytic particulate (Fe203, CuO, ZnO etc.). The corrosion problem from those sulphates is not as serious as with alkaline sulphates, and the heat releasing from the sulphating reaction affect boiler operation significantly. As far as the waste-heat boiler is concerned
Details
-
File Typepdf
-
Upload Time-
-
Content LanguagesEnglish
-
Upload UserAnonymous/Not logged-in
-
File Pages35 Page
-
File Size-