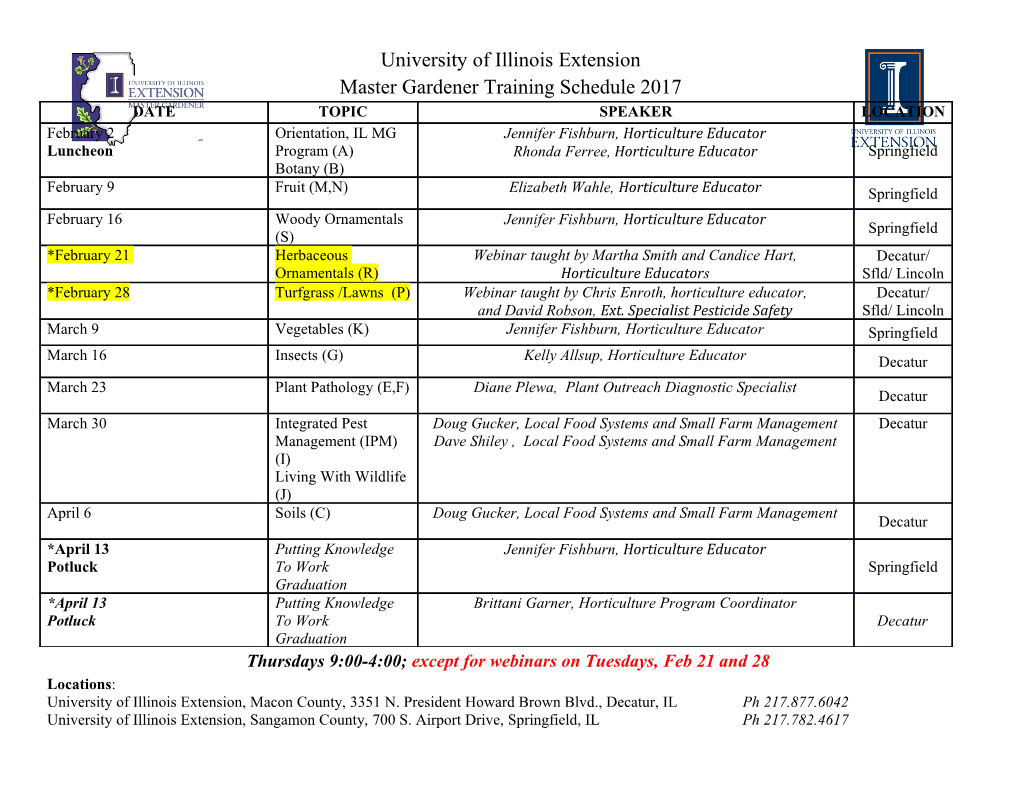
Handbook of Corrosion Data, 2nd Edition Copyright © 1995 ASM International® B. Craig and D. Anderson, Editors All rights reserved. www.asminternational.org Corrosion Concepts/1 Corrosion Concepts lead to complete perforation of the metal with little or no general corrosion of the surface. This section is not meant to be a detailed review of corrosion principles, rather it will briefly present corrosion terms that are Crevice Corrosion: Similar to pitting corrosion in its localized common convention in the field of corrosion science and nature but associated with crevices. Stainless steels and some engineering. For details on corrosion principles the reader is nickel-base alloys are particularly susceptible to this form of directed to Fontana' and H. H. Uhlig2 corrosion. Corrosion is an electrochemical process that results in the Intergranular Attack: The preferential corrosion of grain degradation of a metal or alloy. It is a coupled reaction between boundaries in a metal caused by prior thermal treatments and an anode and at least one cathode. Corrosion (oxidation) related to specific alloy chemistries. occurs at the anode while reduction occurs at the cathode. The various ways (forms) that corrosion manifests itself are myriad Dealloying: The selective removal of one element (usually the but can often be reduced to several basic types. least noble) from an alloy by the corrosive environment. Also referred to as selective leaching or dezincification, denickelifica­ While certain corrosion terms such as pitting or crevice tion, etc. designating the element removed. corrosion are generally recognized nomenclature, the organ­ ization of these forms into a general classification scheme has Corrosion Fatigue: The initiation and extension of cracks by taken several approaches. The most widely accepted categor­ the combined action of an alternating stress and a corrosive 1 environment. The introduction of a corrosive environment ization of corrosion forms was provided by Fontana . More recently Craig and Pohlman3 have presented another cate­ often eliminates the fatigue limit of a ferrous alloy creating a gorization scheme to help emphasize certain important factors finite life regardless of stress level. that contribute to a group of corrosion types. Galvanic Corrosion: Accelerated corrosion of the least noble Certainly more important than the categorization scheme, for metal when coupled to one or more other metals. The more the use of this book, is the considerable variety of terms used noble metals are protected from corrosion by this action. for types of corrosion. The use of so many terms in the literature to define one form of corrosion is the result of several Erosion-Corrosion: Many forms of flow assisted corrosion are factors. Among these are the complexity of corrosion often included in this term such as cavitation, impingement, mechanisms and the tendency for some investigators to invoke and corrosion-erosion. All of these types of attack are the result new names for established phenomenon simply because of a of accelerated corrosion due to flow of solids, liquids or gases. minor variation in the way corrosion is manifested. Probably the greatest variation comes in the areas of stress corrosion Stress Corrosion Cracking: The initiation and propagation of cracking/hydrogen damage. As our understanding of both cracks by the combined action of a corrosive environment and these corrosion phenomena increases, the complexity also a tensile stress. Generally, susceptibility to cracking increases increases. Therefore, much of the corrosion community has wit~ increasing temperature. Not every alloy cracks in every lumped together theseforms along with other mechanisms that environment, however, the list of environment/ alloy combina­ entail cracking (i.e., corrosion fatigue and liquid metal embrit­ !ions t~mt produce stress corrosion cracking is continually tlement) into a more general term: environmentally induced or 1ncreasmg. environmentally assisted cracking. However, certain aspects of st_ress corrosion cracking and hydrogen damage are quite Hydrogen Damage: There are numerous forms of damage different. Yet much confusion exists in the literature because associated with hydrogen which are contained under the some authors carelessly interchange the two. Therefore, it is collective term "hydrogen damage." For hydrogen embrittle­ incumbent on the reader of this book to be familiar with the ment and hydrogen stress cracking, a tensile stress and spe~ific types of corrosion that may be expected in a particular hydrogen atoms are necessary to cause failure. However, envuonment or for a certain alloy and the multitude of names contrary to stress corrosion cracking, susceptibility is greatest by which they may be referenced. Rather than resort to a near room temperature. Other terms and forms are: hydrogen classification system, some of the more common forms of induced cracking, blistering, sulfide stress cracking, hydrogen corrosion are defined below to assist the reader. stress corrosion cracking, hydriding, hydrogen attack. There are many others too numerous to mention. Uniform/ General Corrosion: A form of attack that produced overall umform wastage of the metal. Often associated with Altho:agh these forms are presentep in the context of aqueous atmospheric corrosion and some high temperature oxidation corrosiOn, many of them are also operative at high tempera­ or sulfidation attack. ture. High temperature corrosion by oxidation and sulfidation can take the form of uniform attack, pitting, or dealloying to Pitting Cor~osion: A high localized attack of the metal creating name a few. It is of utmost importance the reader recognize the ptts of varymg depth, width, and number. Pitting may often difference between high temperature corrosion (oxidation) and 2/Pure Irons aqueous corrosion. The mechanisms are different and these, it is important to recognize that the other methods are therefore, the correct alloy choice for resistance to one often used in combination with alloys of lower corrosion environment often is incorrect if applied to another. resistance to retard or eliminate corrosion. Therefore, simply choosing the most corrosion resistant alloy may not be the For those not familiar with corrosion, it is important to most economical choice. recognize that most corrosion rates are reported as a time averaged weight loss (mils per year, millimeters per year, etc.) that implies a uniform corrosion rate. However, in actual fact, References: few metals and alloys corrode in a uniform manner rather, highly localized corrosion (pitting, crevice corrosion, etc.) is 1. M.G. Fontana, Corrosion Engineering, McGraw-Hill Book the rule. Therefore, the corrosion rates reported in this book Co., New York, 1986. and most other books are relative and for purposes of comparison between different alloys. 2. H. H. Uhlig and R. W. Revie, Corrosion and Corrosion Control, J. Wiley and Sons, New York, 1985. In simple terms, corrosion can be controlled by any of four methods: cathodic protection, coatings, inhibitors and/ or 3. Metals Handbook, Vol 13, 9th ed., Corrosion, ASM alloy changes. While this reference only addresses the last of International, Metals Park, OH, 1987, p 79. Pure Iron steels. Therefore, any form of iron that is relatively pure-such as wrought iron-should be coated to ensure acceptable life in The general corrosion behavior of pure iron is nq.t unlike many most atmospheres. other pure metals; that is, in many instances, pure iron has substantially greater corrosion resistance- than many of its Corrosion in Aqueous Solutions alloys, including mild steels and unalloyed cast irons. At the same time, pure iron has little or no resistance against attack by Under some conditions, pure iron does show unusually good such aggressive chemicals as the stronger acids. corrosion performance in various types of waters. The degree of resistance is largely governed by two major factors: oxygen Corrosion in Atmospheres content and the pH level of the water. When the oxygen content of the water is exceptionally low (almost none) and when the Irons of high purity show a remarkably high resistance to pH value is above 5, the corrosion rate is almost nil. However, corrosion. They sometimes remain untarnished in laboratory when the pH values are under 4 to 5, there is a rapid increase in atmospheres for months or even years. Also, pure iron shows a corrosion rate, especially at higher oxygen levels. higher resistance to rusting in rural atmospheres as contrasted with its behavior with mild steel. However, in industrial and/ or Like many other metals, pure iron resists corrosion caused by saline atmospheres, uncoated pure iron has very poor aqueous solutions much better when the surface is completely resistance to corrosion-perhaps little, if any, more than mild and continuously immersed, as occurs in pipes and tanks. Cast Irons The generally used alloying elements that enhance corrosion resistance include silicon, nickel, chromium, copper, and molybdenum. Less frequently, titanium and vanadium are also Cast irons are primarily alloys of iron that contain more than used. 2% carbon and I% or more silicon. With proper alloying, the corrosion resistance of cast irons can be greatly improved. Silicon Thus, this group of materials finds wide application in corrosion-inducing environments. Such service conditions Silicon is not considered an alloying element in cast iron until it include water, soils, acids, alkalis, saline solutions, organic exceeds
Details
-
File Typepdf
-
Upload Time-
-
Content LanguagesEnglish
-
Upload UserAnonymous/Not logged-in
-
File Pages10 Page
-
File Size-