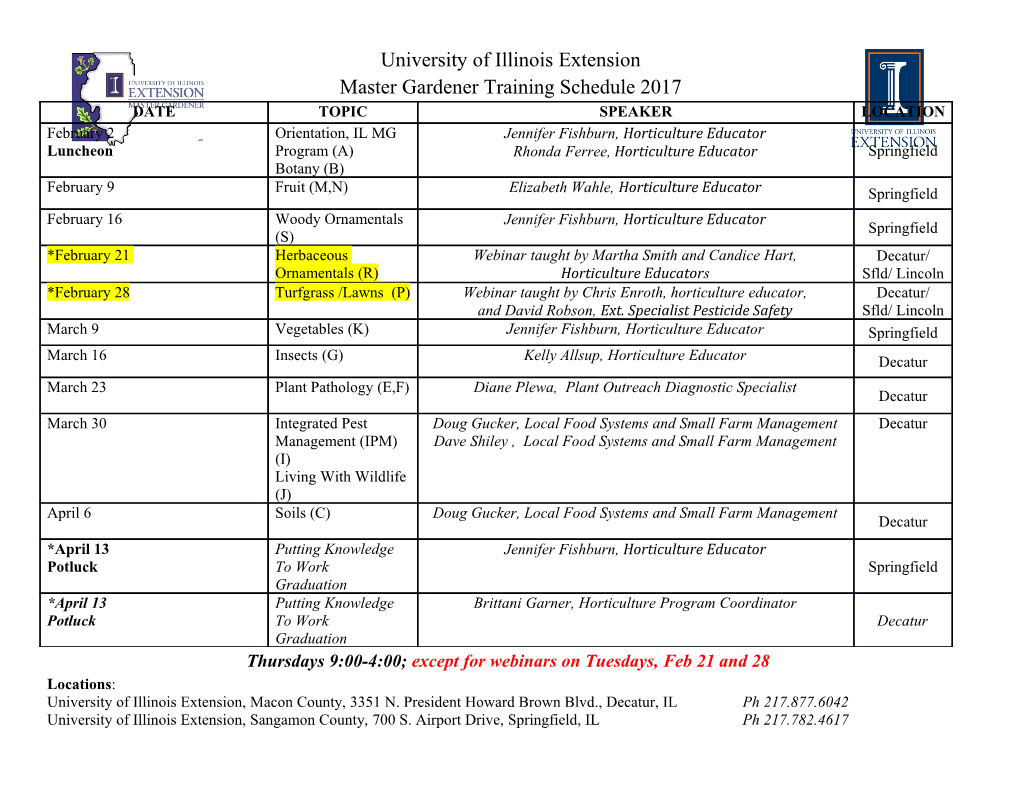
With Blessings of Shreemad Bhagwat Geeta A self-study guide on Crankpin By: Uma Sankar Sahu, B.Tech. Mechanical Engineer Encouraged By: Mr. Santosh Kumar Sahu Dedicated to: Baba (My Ideal), Bou (My Love) & all my readers Content: I. Introduction II. Purpose of Crank Pin III. Location of Crank Pin in the IC Engine IV. Different types of holes and their significance V. Manufacturing process of Crankpin VI. Inspection parameters VII. Load & stress on the Crankpin VIII. Crankpin materials IX. Reason of Crankpin failure X. Manufacturing defects XI. References 2 I. Introduction:- A short cylindrical bearing surface fitted between two arms of the crank and set parallel to the main crank shaft is called a crankpin. In an engine, cranks consist of a main shaft which rotates, crankpin which revolves like a planet and a crank throw to solidly connect them. In a reciprocating engine, the crankpins (also called the crank journals) are the journals of the big end bearings at the end of the connecting rod opposite to the pistons. Crankpin is a separate pin and assembles with the crank (fig .A) or it may be machined in to the crankshaft as one piece (fig. B). Our topic is focused on separate crankpin (fig. A) i.e. Crankpin as an element. Fig. A Fig. B In a multi-cylinder engine, crankpin serves one or more connecting rods at a time. For e.g. in a straight or flat engine, each crankpin serves just one cylinder. In a V-engine, each crankpin usually serves two cylinders, one in each cylinder bank. In a radial engine, each crankpin serves an entire row of cylinders. II. Purpose of Crankpin:- ∑ The main purpose of crankpin is helping to convert the reciprocating motion in to rotational motion. ∑ It provides lubrication to the big end bearing for smooth running of the engine as well as increases the life of bearing. 3 III. Location of Crankpin in the Crank shaft assembly and how it is assembled? Before going through the above question, let’s understand a brief about connecting rod for better understanding of the prescribed answer. Connecting rod (CR):- The name itself explains the meaning and significance. It is simply a rod which connects the piston and the crank. The CR has two ends i.e. one small end & another is big end. One side of the CR is attached to the piston with its small end by a piston pin or gudgeon pin and another side of the CR is attached to the crank with its big end by a crankpin. Earlier the CR is used to convert rotational motion to reciprocating motion; but now in automotive engines, CR is used to convert reciprocating motion to rotational motion. From the design point of view, CR is of 3 types as shown in the figure. Fig. C Fig. D The connecting rod (refer fig.C) for endothermic engine has the modular head and the foot equipped with a bushing, the central rod has the oil drip rod equipped with parts. The connecting rod is very simple to use by passing over big end bearing and then closing another side of the crank. Location of Crankpin at the Crankshaft assembly:- Crank shaft is a shaft which is attached to the crank for rotational motion. Here we are going to discuss two types of assemblies. 4 A. Separate Crankpin at the crankshaft assembly: (refer to fig. A) Attach the Crank shaft LH to crankpin, then the connecting rod with big end bearing is allowed to pass over the crankpin and then attach the crankpin to the Crank shaft RH. Fig. E B. Machined crankpin at the crank shaft assembly: (refer to fig. B) Here the crankpin is already machined with crank shaft; hence there is no need of separate crankpin to use. In this type of crank shaft assembly, the connecting rod with modular head and foot equipped with bushing is used. IV. Holes that are present in crankpin:- o Face hole: It is used for locking purpose. 5 o Dimple hole / OD hole: If there is no inclined hole inside a dimple hole then, dimple buffing is not required and the dimple hole in this case is called OD hole. o Inclined hole: It is always inside the dimple hole. Both dimple hole/ OD hole and inclined hole is responsible for allowing the oil within the crankpin. o Cross hole: Some crankpin have single cross hole & some have double cross hole. Cross hole is the hole directed radially. The oil that comes through center hole or inclined/dimple/OD hole lubricates the big end bearing through cross hole, as the bearing sits on the cross hole. o Centre hole: It is the hole directed axially. Sometimes the center hole is blocked with cap, if dimple/inclined hole is present and in some case the center hole is used to allow the oil through crankpin in the absence of dimple/inclined hole. 6 V. Manufacturing process of Crankpins:- Following process flow is applied for manufacturing of crankpin. A. Raw material inspection B. Move to raw material storage C. Material move to sawing D. Sawing: In sawing process the raw material rods are cut in to small required pieces. E. CNC turning-1: In this process, actual length of crankpin is arrived by turning. F. CNC turning-2: It is the process of reducing outer diameter by turning operation. G. Centre hole drilling H. Face hole drilling I. Face hole chamfering J. OD dimple hole drilling K. Inclined hole drilling L. OD cross hole drilling at 1st side M. OD cross hole drilling at 2nd side N. OD cross hole chamfering O. Punch marking P. Heat treatment: It includes a no. of process as follows; o Visual check( no damage/ rust) o Arranging in fixtures( layer wise in cast tray) o Pre-washing (rinsing 10 minutes, resting 1 minute & spraying 10 minutes) o Pre-heating (4000c., 30 minutes) o Carburizing/ boost diffusion (9400c.) o Vestibule o Hardening o Quenching 7 o Subzero o Post washing (as like pre washing) o Tempering o De-fixturing o Oiling Q. Face cleaning & heat code marking R. Rough OD grinding: It is done on center less grinding machine. Here we can remove up to 55-60 microns of material on the OD & the rest parameters are maintained according to the different control plans for different sizes. S. Pre final OD grinding: It is done on CNC center less grinding machine. Though it is the second pass we are removing less material but maintaining a little bit finishing and accuracy. Here we are removing up to 15-20 microns of material on the OD. T. End chamfers grinding: It is a type of forming process. The grinding wheel used here has many projections and that are used to form end chamfer. Here also we are using center less grinding machine. U. Deburring: It is also called buffing operation, here the sharp edges of the end chamfer, cross holes & dimple holes are removed. Here we are maintaining cross hole chamfer radius up to 0.15-0.3 mm. V. Crack detection: It is also called Magnetic Particle Inspection (MPI). It works on the principle that, if the job is passing through an electric current; then the magnetic field creates & thus magnetic flux occurs. The surface where some corrosion or crack is present, at that place magnetic flux leakage occurs. When it is immersed to oil bath, the oil/powder particles concentrate at the crack. By the UV light we can see the crack. Here we normally check the surface cracks & bar cracks. For detection of burn crack we can use another machine called Burn crack testing machine. W. Eddy current sorter: After the MPI occurs, demagnetization of material is important as we should not use any magnetic element/ parts in the IC engines. Then using eddy current we are checking the hardness of the material for each and every job. X. Finish OD grinding: It is the most important operation. Here we have to use better technology for better surface finishing & maintaining the perfect material removing rate. The customer gives different tolerance level so called grade. We have to maintain the grading system in small microns. The grinding wheel we are using is a coupled wheel having 3-4 layers throughout the length of the spindle having different grades which are responsible for material removing, surface finish etc.. The automated dressing of grinding wheel for 20-40 seconds & metallic regulating wheel 8 are one of the main sources to meet the tolerance level. The coolant concentration has to be maintained @ 3-4% as the grinding operations are not so rough. Y. Super finishing: As its name given its work also similar. During this process, in between 2 rotating metallic rollers crankpins are allowed to pass and from the upper side of the crankpins the force is given through different grade stones (i.e. at station-1 800 grade stone, at station-2 1000 grade stone and at station-3 1200 grade excel abrasive stones). Here maximum 2-3 microns of material is removed in the station 1 & 2. And in station 3 super finishing occurs. Z. Liquid honing: It is also called sand blasting. As per the customer requirement, the two sides of the crankpin should be rough enough to attach the crank tightly as it increases friction. The slurry (Aluminum Oxide powder of 100 grit properly mixes with water) coming from high pressure nozzle with high pressure air when sticks to the end sides of the crankpin, a layer of rough surface comes on the crankpin.
Details
-
File Typepdf
-
Upload Time-
-
Content LanguagesEnglish
-
Upload UserAnonymous/Not logged-in
-
File Pages14 Page
-
File Size-