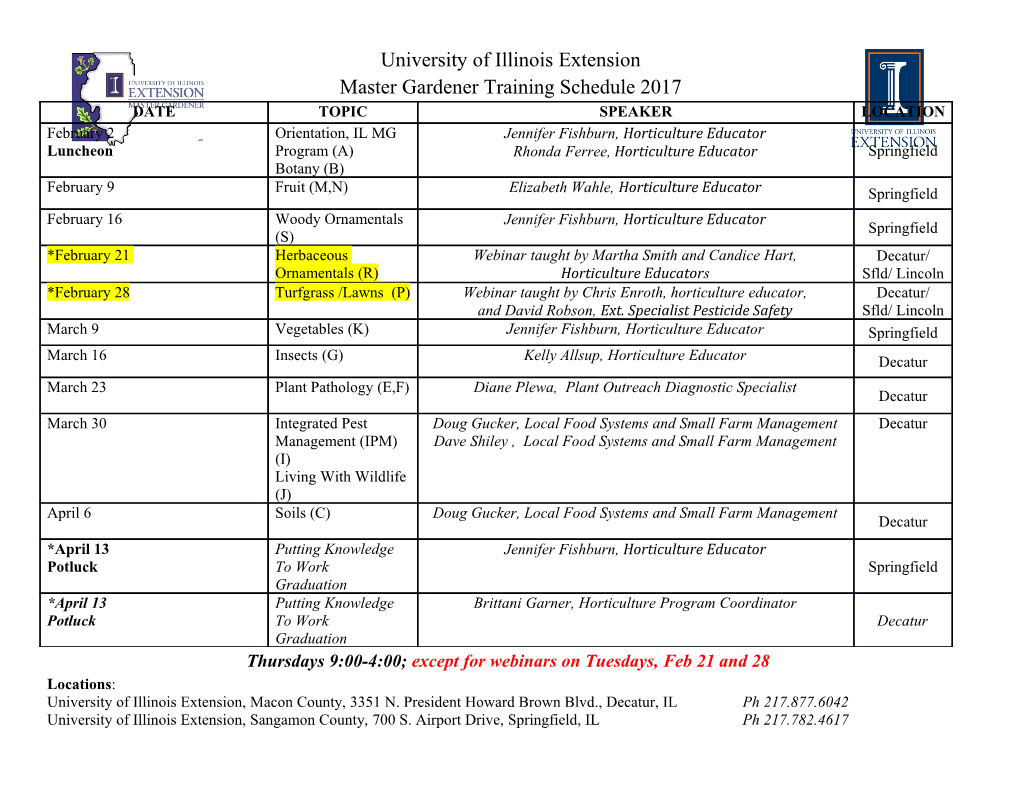
University of Nevada, Reno Modeling of Heat Transfer and Flow Patterns in a Porous Wick of a Mechanically Pumped Loop Heat Pipe: Parametric Study Using ANSYS Fluent A thesis submitted in partial fulfillment of the requirements for the degree of Master of Science in Mechanical Engineering by Md Shujan Ali Dr. Miles Greiner, Thesis Advisor May, 2017 THE GRADUATE SCHOOL We recommend that the thesis prepared under our supervision by MD SHUJAN ALI Entitled Modeling of Heat Transfer And Flow Patterns In A Porous Wick of A Mechanically Pumped Loop Heat Pipe: Parametric Study Using ANSYS Fluent be accepted in partial fulfillment of the requirements for the degree of MASTER OF SCIENCE Miles Greiner, Ph. D., Advisor Mustafa Hadj-Nacer, Ph. D., Co-advisor and Committee Member Sage R. Hiibel, Ph. D., Graduate School Representative David W. Zeh, Ph.D., Dean, Graduate School May, 2017 i ABSTRACT In recent years, NASA space exploration has achieved new feats due to advancement in aerodynamics, propulsion, and other related technologies. Future missions, including but not limited to manned mission to Mars, deep space exploratory missions, and orbit transfer vehicles, require advanced thermal management system. Current state-of-the-art for spacecrafts is a mechanically pumped single phase cooling loop that are not enough to meet thermal-related challenges for future space missions. Loop heat pipes (LHP) are the solution for the required thermal management system that is compact, light-weight, reliable, precise, and energy efficient. These are two-phase systems that employ capillary forces instead of pumps to circulate the coolant. In these devices, the coolant evaporates and condenses in the evaporator and condenser, respectively. The condensed coolant liquid is driven toward the evaporator by capillary action in a wick structure located inside the evaporator. A mechanical pump is added to the liquid line of the loop to reach the distributed heat loads while controlling the temperature to produce an isothermal surface. In this work, flow patterns and heat transfer in the LHP evaporator wick is studied for various flow rates of the working fluid, wick thermal conductivity, porosity and permeability of wick, heat flux, and gravity condition. A CFD model has been developed to predict the performance of LHP due to the change in these parameters. The Volume of Fluid (VOF) model in ANSYS Fluent was modified using a User Defined Function (UDF) to calculate mass transfer between the liquid and vapor phases at the interface. The Lee phase change model was used to calculate the mass flux due to evaporation and condensation. ii Acknowledgement First of all, I would like to express my grateful to the creator ALLAH s.w.t. for the blessing given to me to complete my thesis. I thank my advisor Dr. Miles Greiner for his great supports, advice, guidance and encouragement. I would like to give special thanks to my supervisor Dr. Mustafa Hadj-Nacer for his continuous supports and mentorship. He guided me in every step of my works. I would also like to say thanks to my committee member Dr. Sage R. Hiibel. I would say thanks to my colleague Nishan Pandey, who helped me write the user defined function, and colleague Corey with whom I shared interesting discussions several times about my research. I would acknowledge my family for their supports. Especially, I want to thank my wife for her continuous supports, understanding, and trust. Finally, I would say thanks to NASA EPSCOR Nevada to provide necessary fund for this research project. iii Table of Contents 1 Introduction ................................................................................................................ 1 2 Literature review on Loop Heat Pipe ......................................................................... 3 2.1 LHP operating Principles ....................................................................................... 3 2.1.1 Classification of capillary two-phase loops ................................................... 5 2.1.2 Classification of LHP ..................................................................................... 6 2.1.3 Loop Heat Pipes with flat evaporators ........................................................... 6 2.1.4 Mechanically Pumped LHP ........................................................................... 8 2.1.5 The thermodynamic cycle of an LHP ............................................................ 9 2.1.6 LHP serviceability ....................................................................................... 10 2.1.7 Steady-state operating performance ............................................................. 12 2.2 LHP parametric study .......................................................................................... 13 2.2.1 Effect of fluid charge ................................................................................... 13 2.2.2 Effect of the porous wick characteristics ..................................................... 13 2.2.3 Effect of gravity ........................................................................................... 15 3 CFD Model .............................................................................................................. 17 3.1 Governing Equations ........................................................................................... 17 3.1.1 Porous media model ..................................................................................... 18 3.1.2 Volume of fluid model ................................................................................. 20 3.1.3 Evaporation-Condensation model ................................................................ 22 3.2 Geometry and boundary conditions ..................................................................... 25 3.3 Mesh ..................................................................................................................... 26 3.4 Solver Settings ..................................................................................................... 27 4 Results and Discussion ............................................................................................ 29 4.1 Benchmark problems ........................................................................................... 29 4.1.1 One-Dimensional Stefan problem ................................................................ 30 4.2 Liquid mass flow rate at inlet ............................................................................... 32 4.3 Permeability ......................................................................................................... 33 4.4 Porosity ................................................................................................................ 35 4.5 Heat flux............................................................................................................... 36 4.6 Thermal conductivity ........................................................................................... 39 4.7 Gravity ................................................................................................................. 41 5 Conclusions .............................................................................................................. 43 BIBLIOGRAPHY ............................................................................................................. 44 iv List of Tables Table 2.1: Classification of Loop Heat Pipe (Maydanik [7]) ......................................... 6 Table 3.1. Construction of mass and energy sources.................................................... 24 Table 3.2. Results for mesh sensitivity test. ................................................................... 27 Table 4.1. Base case parameters ..................................................................................... 29 Table 4.2. Properties of working fluid ........................................................................... 29 Table 4.3. Relation between vapor content and Pressure Difference. ........................ 38 v List of figures Figure 2.1. Flow Schematic of an LHP (Ku [6]). ................................................................... 3 Figure 2.2. Schematic of (a) a traditional LHP and (b) a traditional CPL (Butler et al. [13].) .......................................................................................................................................... 5 Figure 2.3. Schematic of (a) active zone of an evaporator with opposite replenishment, (b) active zone of an evaporator with longitudinal replenishment, (c) an evaporator with opposite replenishment, and (d) an evaporator with longitudinal replenishment ( Maydanik [8]) ........................................................................................................................... 7 Figure 2.4. Schematic of a Pumped LHP (Jiang et al. (2014) [52]). ..................................... 8 Figure 2.5. Diagram of: (a) the LHP working cycle; (b) location of the characteristics points in the LHP (Maydanik [7]). ......................................................................................... 9 Figure 2.6. Typical LHP operating curves (Launay et al [24]). ......................................... 12 Figure 3.1. Flow chart summarizing the numerical methodology. .................................... 17 Figure 3.2. Mechanically Pumped Loop Heat Pipe (LHP). ................................................ 25 Figure 3.3. Schematic of the numerical model used in ANSYS/FLUENT
Details
-
File Typepdf
-
Upload Time-
-
Content LanguagesEnglish
-
Upload UserAnonymous/Not logged-in
-
File Pages54 Page
-
File Size-