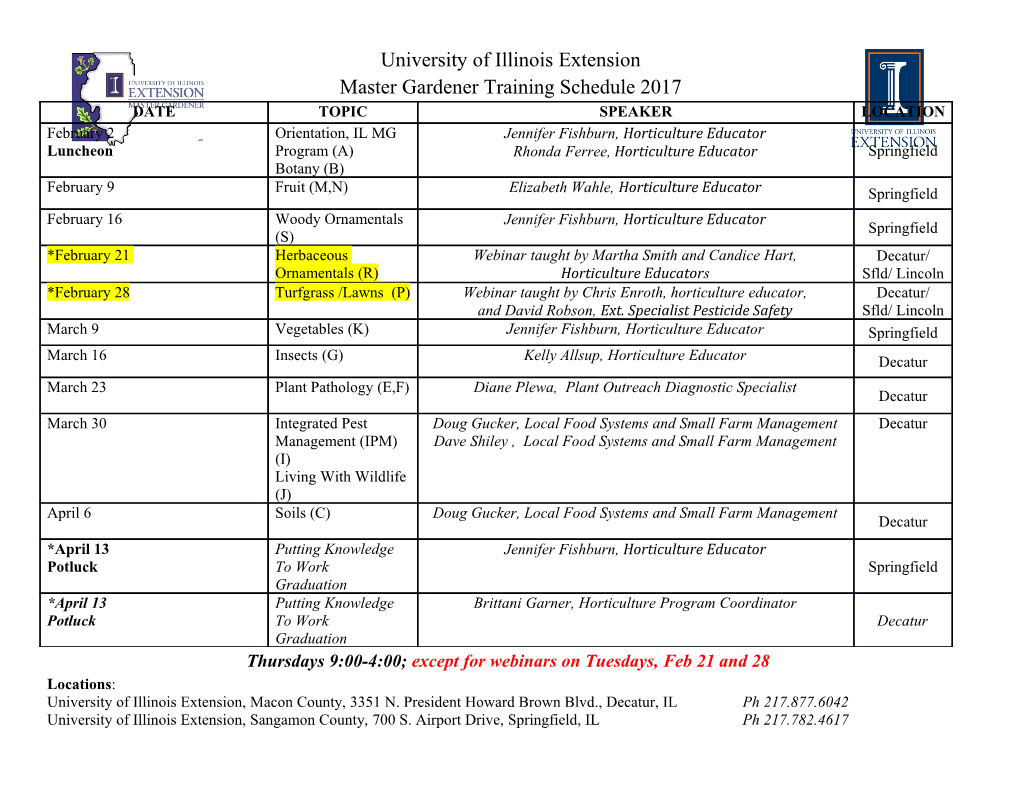
Characterization and Modeling of Lightweight Alloys in the Warm Forming Regime DISSERTATION Presented in Partial Fulfillment of the Requirements for the Degree Doctor of Philosophy in the Graduate School of The Ohio State University By Scott Sutton Graduate Program in Materials Science and Engineering The Ohio State University 2018 Dissertation Committee: Professor Alan Luo, Advisor Professor Rudolph Buchheit Professor Stephen Niezgoda Copyrighted by Scott Christopher Sutton 2018 Abstract Lightweighting is used throughout the transportation industry and is an increasingly popular method to increase fuel economy in both automotive and aerospace applications. Magnesium has the lowest density of any structural metal and is an attractive option for substitution into aluminum or steel structures. Aluminum-lithium alloys are also attractive, as they boast lower density, higher modulus, and relatively good strengths compared to conventional aluminum alloys. For different metallurgical reasons, both materials have significantly anisotropic mechanical properties, which limit their formability and service life applications. For both Mg alloys and Al-Li alloys, improved primary processing can address the properties which restrict these materials’ use. This work aims to make processing recommendations for a Mg-RE alloy and an Al- Li alloy based on relevant deformation traits or microstructural processes in the warm forming regime. Simple mechanical models which can form industrial processing are also presented. In Mg, rare earth elements in solid solution have significant effects which result in reduced or altered texture, which can mitigate mechanical anisotropy of final components. These so-called rare earth texture effects were studied in Mg alloy ZE20 (Mg-2Zn-0.2Ce-0.3Mn) with the conventional Mg alloy AM30 (Mg-3Al-0.4Mn) as a baseline for comparison. In general, ZE20 had a smaller recrystallized grain size, lower ii basal texture intensity for recrystallized grains, and somewhat retarded recrystallization kinetics. Processing map-guided investigation of microstructures revealed two regions of processing interest. One region had conventionally favorable traits from the processing map but did not exhibit the rare earth texture effect. Another potentially allowable region had unfavorable flow characteristics but had favorable recrystallization texture and exhibited the rare earth texture component, both of which could be exploited with post- process annealing. Alloy development is constantly progressing for Al-Li alloys, which suffer strong anisotropy due to the textures that form during processing. Little information is available for the newly-developed AA2070, and its properties were evaluated using simulated forming under warm forming conditions. AA2070 exhibited significant softening or steady-state stress for all elevated temperature tests; this was attributed to dynamic recrystallization at high temperatures and exceptional activity of dynamic recovery at lower temperatures. The initially strong Goss texture and minor β-fiber texture of the billet were not strongly affected by mechanical testing at high temperatures but were reduced in intensity following mechanical testing at lower temperatures. General processing recommendations for AA2070 were made based on pseudo processing maps and experimental microstructures and textures. In order to more fully inform industrial processing, flow stress during mechanical testing was modeled using two empirical constitutive flow stress models: the hyperbolic sine Arrhenius model and a novel formulation of the extended Ludwik hardening model. The modified Ludwik model was found to have superior performance for ZE20 and iii AA2070 with few added model constants. Further modifications and potential improvements on the extended Ludwik model were described. Viscoplastic self- consistent (VPSC) crystal plasticity simulation was applied to ZE20. VPSC-predicted flow curves and textures were found to only be accurate for some temperatures and strain rates. Despite inaccuracy for some conditions, VPSC was used to provide physically- based validation for the extended Ludwik model which was consistent with theory. iv Dedicated to my fiancée, Megan, for her unwavering support. v Acknowledgments I must first acknowledge my advisor, Prof. Alan Luo for his overarching guidance. With his considerable industry experience, he was able to successfully target several grants, rapidly growing a tight-knit research group and fully funding my graduate career as well as several of my coworkers’. He also pushed me into new areas of research, helping me grow as a scientist and an independent scholar. My achievements are in no small part thanks to him. I acknowledge the constant support and dedication of my fiancée, Megan, to whom this work is dedicated. Always by my side, she followed me to Columbus from Michigan State (Go Green), while still making great progress in her own career. For her immeasurable support, both in this and as we plan the next chapter of our lives, I thank her. I would like to thank Prof. Stephen Niezgoda and Prof. Rudy Buchheit of OSU for their guidance toward completion of my degree, especially under an unexpectedly shortened timeframe. I would also like to thank Prof. Niezgoda’s grad students, Thaddeus Low and Denielle Ricciardi, for teaching me the basics of VPSC and helping me run simulations. I acknowledge the support of all my coworkers. Though most worked on cast materials, they were unafraid of helping me solve problems for wrought Mg and Al. vi Among them I thank especially Andrew Klarner, Colin Ridgeway, and Yan Lu for immense help with casting die design and casting simulation, recognized though unfortunately precluded from this work. Thanks to Janet Meier, Emre Cinkilic, and Zhi Liang for our frequent coffee breaks filled with academically stimulating conversation. I acknowledge the MSE Department’s support staff, for always quickly and efficiently solving problems that grad students alone are unable. Especially I would like to thank Ross Baldwin and Pete Gosser for teaching me necessary machining skills and always being willing to help in a pinch. Lastly, I would like to thank my family. My parents have always supported me, no matter the path in life I chose. My sister, who earned her PhD the year I started grad school, was always ready to grouse with me about the academic struggle and was still able to provide advice whenever I needed it. vii Vita 2008.............................................................Troy High School 2013.............................................................B.S. Materials Science and Engineering, Michigan State University 2016.............................................................M.S. Materials Science and Engineering, The Ohio State University 2016 to present ...........................................Graduate Research Associate, Department of Materials Science and Engineering, The Ohio State University Publications [1] S. C. Sutton and A. A. Luo, “Constitutive Behavior and Processing Maps of a New Wrought Magnesium Alloy ZE20 (Mg-2Zn-0.2Ce). Provisionally accepted. [2] X. Shi, A. A. Luo, S. C. Sutton, L. Zeng, S. Wang, X. Zeng, D. Li, and W. Ding, “Twinning behavior and lattice rotation in a Mg-Gd-Y-Zr alloy under ballistic impact,” J. Alloys Compd., vol. 650, pp. 622–632, Nov. 2015. viii [3] S. Sutton and A. A. Luo, “Hot Compression Behavior of Magnesium Alloys ZE20 AND AM30,” in Magnesium Technology 2015, Hoboken, NJ, USA: John Wiley & Sons, Inc., 2015, pp. 25–28. [4] T. R. Bieler, S. C. Sutton, B. E. Dunalp, Z. A. Keith, P Eisenlohr, M. A. Crimp, and B. L. Boyce, “Grain boundary responses to heterogeneous deformation in tantalum polycrystals,” Jom, vol. 66, no. 1, pp. 121–128, Jan. 2014. Fields of Study Major Field: Materials Science and Engineering ix Table of Contents Abstract ............................................................................................................................... ii Acknowledgments.............................................................................................................. vi Vita ................................................................................................................................... viii List of Tables ................................................................................................................... xiii List of Figures .................................................................................................................. xiv Chapter 1: Introduction and Material Properties for Forming ............................................ 1 1.1 Introduction ............................................................................................................... 1 1.2 Literature Review of Magnesium Forming Properties .............................................. 3 1.2.1 Single Crystal Properties .................................................................................... 3 1.2.2 Texture Formation and Textured Mg Polycrystals ............................................. 5 1.2.3 Mitigation of Texture Effects ............................................................................. 9 1.2.4 The “Rare Earth Texture Effect” ...................................................................... 14 1.3 Literature Review of Aluminum Forming Properties ............................................. 17 1.3.1 Deformation Modes in Aluminum ................................................................... 17 1.3.2 Precipitation
Details
-
File Typepdf
-
Upload Time-
-
Content LanguagesEnglish
-
Upload UserAnonymous/Not logged-in
-
File Pages175 Page
-
File Size-