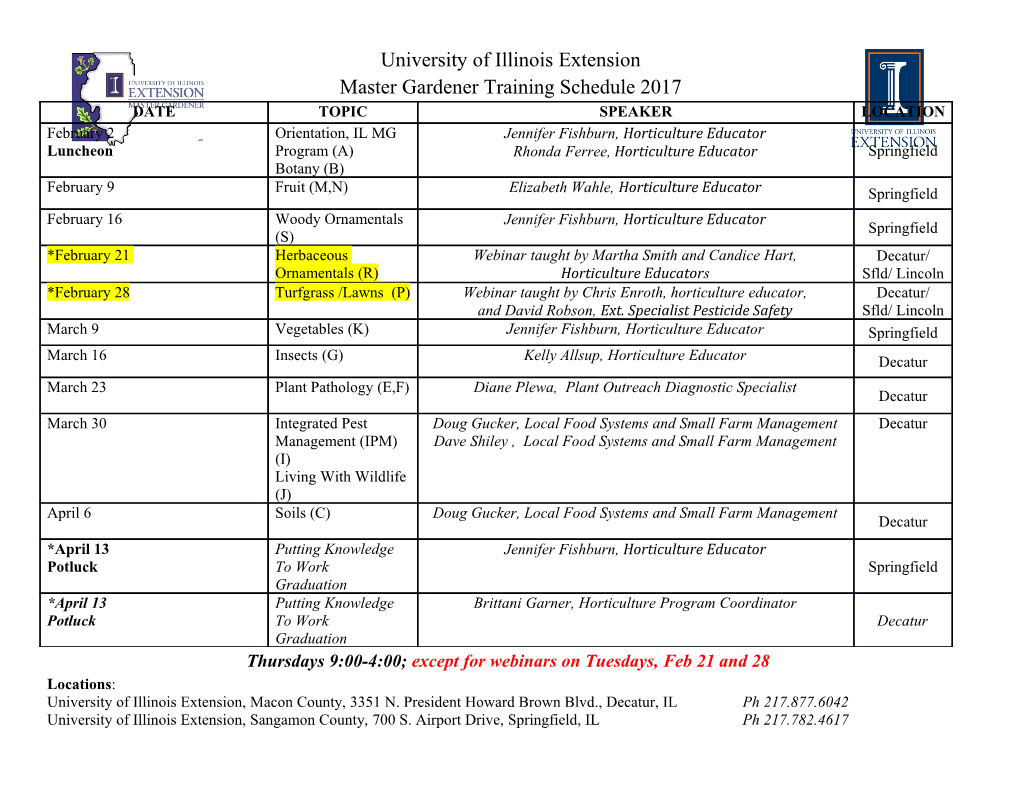
Lead Bullets and Revolvers By Iowegan Most people find lead bullets can be more accurate than jacketed bullets, providing some procedures are followed to prevent bore fouling. Fouling and accuracy go hand-in-hand; as fouling builds up, accuracy diminishes. There are dozens of methods used by reloaders, some good, some not so good. The true test of how well lead bullets perform is when 50 or more rounds are fired in a single session. With a dozen or so rounds, most any bullet will provide adequate performance because fouling hasn’t yet built up enough to alter accuracy. The key to sustained accuracy is having the revolver optimized for lead bullets and to select the proper bullet hardness and diameter. With jacketed bullets, reloading is pretty straightforward. Choose a load from a reputable reloading manual, follow the recipe, and you’re good to go. With lead bullets, there’s a lot more involved in bullet selection and the gun itself. When you have the right combination, accuracy can be superior to jacketed bullets. The first major issue is the gun itself. Most US made revolvers are shipped optimized for jacketed bullets, which is what the average shooter will use. In most cases, the cylinder throats are too tight and the forcing cone is at the wrong angle for lead bullets. Most factory forcing cones are cut to 5 or 8 degrees. A wider 11 degree forcing cone has proven to work better with lead bullets because it helps guide bullets into the bore without damage or distortion. This improves accuracy and minimizes bore fouling. The Small Arms and Ammunition Manufacturers Institute (SAAMI) sets standards for bore, chamber, and cartridge dimensions but do not have specifications for throat diameters, lead bullet diameters or forcing cones. SAAMI has managed to confuse the general public with their nomenclature. According to SAAMI specs, bore diameter is the largest sized rod that can be inserted into a bore. Of course that will be about .012” smaller than advertised bore diameter because of the rifling, also known as “lands”. Example: in a typical 357 revolver (38 Special or 357 Magnum) SAAMI would rate the bore at .345”. Gun manufactures follow this specification but do not advertise their guns this way to avoid confusion. There are actually two bore specifications … the distance between lands, which would be .345” in the above example and the distance between grooves, which is .357” and is the traditional measurement. Another confusion factor, in a bore, the lands extend from the true bore but in a bullet, the lands engrave into the bullet so the high spot in bore is the low spot on bullets. Land diameter is very difficult to measure. Despite the confusion, SAAMII does maintain a very tight specification that all US gun manufacturers subscribe to. With any revolver made in the US after 1950, the bore will be within .0005” of advertised diameter. Of course there are exceptions for worn guns or manufacturing defects. Foreign gun manufacturers do not have to follow SAAMI specs so their bore diameters could be quite different. This is especially true with “clone” models made in Europe or Asia. For the purpose of this document, the bore diameter is defined as the distance between grooves. This is the conventional method of measurement and is much easier to measure. 1 Slugging a Bore: For the most part, this is a fruitless effort that will often yield false information. Unless you have considerable bore wear, a defective barrel, or are dealing with foreign made revolvers, there is really no need to slug a bore because SAAMI specs are tighter than most people can accurately measure. Slugging a bore involves using a “slug” made out of soft lead that is slightly larger in diameter than the actual bore. The slug is driven through the bore with a dowel rod then the outside diameter is measured. Several issues contribute to false measurements. First off, you need a caliper or micrometer accurate to .0001”. Next, you need a set of precise shims that are placed over the slug so the caliper/micrometer doesn’t bite into the soft lead and give a false reading. Of course this means you have to subtract the thickness of the shims to get actual bore diameter. If you use the wrong lead alloy, the slug will be resilient and expand after it is released from the bore. Any constriction in the bore where the barrel threads into the frame will squeeze the bullet smaller and give false readings. So basically, slugging a bore is usually a waste of time and will likely result in a false reading so it’s best to trust the factory’s SAAMI spec dimensions. The above graphic shows the optimum measurements for shooting lead bullets in a revolver. As an example, a revolver with a .357” bore should have a throat diameter of . 358~3585”, a bullet diameter of .358”, with an 11 degree forcing cone. The concept is simple; the bullet needs to be delivered to the forcing cone about .001” larger than bore diameter. If a bullet larger than throat diameter is used, the throat will size it down, which is counterproductive. Depending on the bullet shape, a cartridge with a bullet larger than throat diameter won’t fully chamber. Additionally, if bullets larger than throat diameter are used, chamber pressure will elevate, possibly to damaging levels. Using a bullet smaller than optimum diameter or a having a throat that is too tight will result in the bullet being delivered to the forcing too small, which will cause excess fouling. 2 Assuming the bullet is delivered to the forcing cone slightly oversized, the forcing cone will act like a sizing die and reshape the bullet to fit tightly in the bore. Pressure applied from the powder charge (several tons per square inch) will reshape the lead bullet without shaving and will force the bullet to obturate or “bump up” slightly in diameter. If the bullet hardness matches the chamber pressure, a good seal between the circumference of the bullet and the bore will be maintained until the bullet exits the muzzle. As long as a good seal is maintained, lead fouling will not accumulate in the bore and accuracy will be optimum for at least 100 rounds without cleaning. Bullet Hardness: Bullet hardness is rated in an industry standard called “Brinell Hardness Number” (BHN). Pure lead is BHN 5. As alloys such as tin, arsenic and antimony are added in small percentages, hardness can be increased to BHN 28. There are two common ways to produce lead bullets …. casting and swaging. Swaging: The swaging process is much more expensive due to equipment costs but does produce more consistent weights, diameters and hardness. The process uses a “lead alloy wire” that is slightly under the finished product diameter. The “wire” is cut into precise lengths to get the exact weight, then fed into a punch press die where it is pressure formed into a finished bullet. Because swaged bullets are not melted, they do not develop internal bubbles and maintain the same hardness. The swaging process works very well with soft alloys in the BHN 10~14 range but is not well suited for harder alloys. Both Speer and Hornady produce high quality swaged lead bullets, however the cost is typically more than double of cast bullets. Most swaged bullets have dry power lubrication applied so you must handle them properly or the lube will come off. Casting: The casting process starts with creating the desired hardness by melting lead and adding tin and antimony to get the proper alloy. Pure lead doesn’t cast well so tin may be added to make the molten metal flow better in the molds. Antimony increases bullet hardness. When lead is alloyed, it takes on some strange characteristics. After a lead and tin alloy is cast in molds, it will soften with age. It takes about a month for the molecular structure to reach final hardness. Bullets cast with antimony are just the opposite and tend to harden after casting. Again, it takes about a month for the molecular structure to stabilize. Cast bullets are typically not as precise as swaged bullets. They can develop internal bubbles and because of the way the mold works, they have a spru that can increase weight if it is not cut off properly. Cast bullets are typically molded slightly oversized then run through a sizing and lube die. This sets the diameter to the desired measurement and forces a wax type material in the lube grooves. When cast bullets are within +or- 1% of an average weight, they will produce excellent accuracy. As an example, a bullet sold as a 158 gr could be as light as 156.4 grains or as heavy as 159.6 and still produce consistent accuracy. Of course, the more uniform the weight, the tighter it will chronograph and the more consistent accuracy will be. To determine average weight, weigh a random sample of 20 bullets and jot down the results. Add the weight of all 20 bullets then divide by 20. The average weight is seldom the same as advertised but it should be within a few grains. Cull out any bullets that are significantly light. Light bullets indicate there is an internal bubble or the molten lead did not flow well in the mold and caused a void. A void or bubble will cause the bullet to “whiffle” down range. 3 Most brand name bullets such as “Meister” and “Laser Cast” are typically too hard for lower pressure cartridges or reduced power loads.
Details
-
File Typepdf
-
Upload Time-
-
Content LanguagesEnglish
-
Upload UserAnonymous/Not logged-in
-
File Pages7 Page
-
File Size-