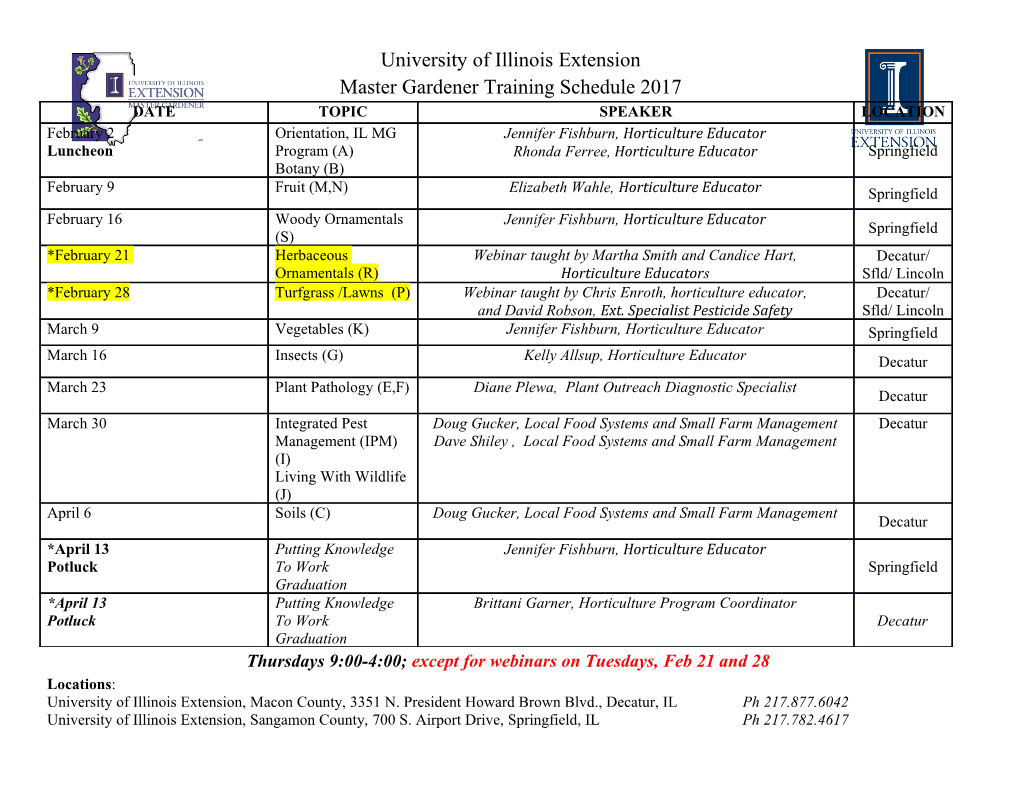
Journal of Science & Technology Vol. (15) No.(1) 2010 JST 3 Flexural Behavior of Lightweight Ferrocement Sandwich Composite Beams Mahmoud Abo El-Wafa + Kimio Fukuzawa ++ Abstract The structural behavior of lightweight ferrocement (LWF) sandwich composite beams is investigated by conducting flexural tests on eight simply supported rectangular beams under three point loads. The main objective of the study is to investigate the comprehensive comparisons of eight beams represented in six lightweight ferrocement (LWF) beams and two reinforced concrete (RC) beams. The performance of the LWF and RC beams is investigated in terms of crack load, load-deflection curves, stiffness, energy absorption capacity, ductility index, ultimate flexural load-to-weight ratio, load-strain curves, crack patterns, number of cracks, average crack width, crack spacing and the failure mode. The method outlined by ACI Building Code is used to compute ultimate moment capacities. The test results reveal the remarkable enhancement in the flexural behaviour and potential application of lightweight ferrocement (LWF) sandwich composite beams to produce lightweight structural elements as compared to that of the reinforced concrete (RC) beams, which leads towards the industrialization of building system and meets with innovation and responsible application of concrete construction technology results in better efficiency of the composite. Keywords: Lightweight ferrocement, sandwich composite, wire mesh ferrocement reinforcement, polystyrene foam block, cracks, ultimate moment capacities. 1. Introduction The development and construction of lightweight sandwich structural elements in building construction is a growing trend in the construction industry all over the world due to its high strength-to-weight ratio, reduced weight, and good thermal insulation characteristics [1,2]. They have been used in the aerospace industry for many years and more recently they are being used as load bearing members in naval structures [3]. Presently, they have gained attention as an effective structural form in the building and construction industries. Sandwich elements are structural members made up of two, stiff, strong skins separated by a lightweight core. The separation of the skins by the lightweight core increases the moment of inertia of the element with little increase in weight, meaning a highly efficient component for resisting bending [4]. The introduction of novel technique of lightweight sandwich composite element presents new possibilities in the design of sandwich construction. This can be done by encasing lightweight polystyrene foam blocks as core with high performance ferrocement wire mesh reinforcement as skin layers and then completely encapsulated in high-flowable high-strength cement grout mortar. Polystyrene foam block is the generic industry name for a white rigid material made by expanding polystyrene beads with steam and bonding the beads together under pressure in a lightweight block or shape mold to achieve closed cell foam that resists moisture. +++Visitor, Dept. of Civil Eng., Faculty of Science and Engineering, University of Science & Technology, Sana’a, Yemen, Lecturer, Dept. of Civil Eng., Faculty of Eng.-Aswan, South Valley University, Egypt E-mail: [email protected]. ++++++Professor, Department of Urban and Civil Engineering, Ibaraki University, Hitachi, Japan. Journal of Science & Technology Vol. (15) No.(1) 2010 JST 4 The polystyrene foam block insulation is preferred by more architects, designers, builders, contractors, and building & homeowners than any other foam brand. It is valued because of its excellent water resistance, high insulation value and superior compressive strength. moreover, it is considered one of the most economical materials and can be cut easily into an unlimited variety of shapes, it is lightweight and easy to handle and stays true to shape and size without any gaps or holes. Ferrocement is one of the relatively new cementitious composite considered as a construction material. It is a type of thin walled reinforced concrete commonly consisting of cement mortar reinforced with closely spaced layers of continuous and relatively small wire mesh [5]. The closely-spaced and uniformly-distributed reinforcement in ferrocement transforms the otherwise brittle material into a superior ductile composite. Thus, ferrocement technology is becoming more attractive to housing construction, particularly for roofs, floors, slabs and walls because of its relatively low cost, durability and weather resistance [6,7]. Its versatility further increases its utility for producing prefabricated components required in housing. The fabrication technique of ferrocement is easy to learn and ferrocement structures, if properly built, are practically maintenance free. It has advantageous properties such as strength, toughness, water tightness, lightness, durability, fire resistance, and environmental stability which cannot be matched by any other thin construction material [6-9]. The ferrocement is the promising composite material for prefabrication and industrialization of the building industry [1,2]. Studies conducted on ferrocement as encasement for structural strengthening [10-13] have also shown great promise. Studies also conducted on the contribution of ferrocement wire mesh reinforcement, with various sizes and volume fractions in direct tension, have also shown great improvement on the service and ultimate tensile crack behavior of the composite plates after sufficient warning, as well as multi- cracking stage elongated and a distinct failure stage [14,15]. Cement grout mortar is designed for critical use where high strength, non-staining characteristics and positive expansion are required. It contains only natural aggregate and an expansive cementitious binder. It is extremely viscous, and when cured, appears similar in appearance to concrete. The cement grout mortar has numerous advantageous properties such as non-staining natural aggregate for better appearance, non-shrink performance for excellent bearing, flowable and self-leveling, high strength, appearance of plain concrete, and does not contain any added chloride ions. A number of research work has been reported on the use of ferrocement as facing or skin over different lightweight materials for a variety of applications. Most recently, its application as core material in FRP-AAC (Aerated autoclaved concrete blocks) sandwich panels has been reported [1,2]. However, the literature is silent and the authors are aware of no systematic investigation reported yet to produce a lightweight sandwich composite with the novel technique; by encasing lightweight polystyrene foam blocks as core with high performance ferrocement wire mesh reinforcement as skin layers and then completely encapsulating this in high-flowable high-strength cement grout mortar. Therefore, the main objective of this investigation is to explore the comprehensive comparisons of flexural behaviour of eight simply supported rectangular beams represented in six lightweight ferrocement (LWF) beams and two reinforced concrete (RC) beams under three point loads. The method outlined by ACI Building Code is used to compute ultimate moment capacities of LWF and RC beams. The results obtained using this method are compared with corresponding experimental results of the RC and LWF beams. Journal of Science & Technology Vol. (15) No.(1) 2010 JST 5 2. Experimental Program The main objective of the study is to investigate the comprehensive comparisons of eight beams representative in six lightweight ferrocement (LWF) beams and two reinforced concrete (RC) beams. The tests of the LWF beam specimens used for the flexural behaviour study have the dimension of the cross-section as 300 x 200 mm & 300 x 250 mm and compared with RC beams have the dimension of the cross-section 300 x 200 mm. All beam specimens were loaded in flexure under a three point loading system, as simply supported beam with center point loads over the span length of 1800 mm up to failure. The details of RC and LWF beams are listed in tabular form in Table 1 and their setup configurations are shown in Figure 1. Table (1): Details of RC and LWF beams Web Beam Cross-Section Tension Reinforcement Compression Unit Weight Beam Specimens Reinforcement b x d (mm) Area (mm 2) - µ (%) Reinforcement (Density - t/m 3) (Stirrups) RC Beams RC-200-3D13 300 x 200 3D13 mm - 398.2 mm 2 - 0.76 % 2D10 mm 8 Str.-D8 mm 2.5 LWF-200-4 300 x 200 4 Layers - 129.2 mm 2 - 0.25 % 3 Layers 3 Layers 1.06 LWF Beams LWF-200-5 300 x 200 5 Layers - 161.5 mm 2 - 0.31 % 3 Layers 3 Layers 1.06 LWF-200-6 300 x 200 6 Layers - 193.8 mm 2 - 0.38 % 3 Layers 3 Layers 1.06 RC Beams RC-200-4D13 300 x 200 4D13 mm - 530.9 mm 2 - 1.01 % 2D10 mm 8 Str.-D8 mm 2.5 LWF-250-4 300 x 250 4 Layers - 129.2 mm 2 - 0.19 % 3 Layers 3 Layers 1.02 LWF Beams LWF-250-5 300 x 250 5 Layers - 161.5 mm2 - 0.24 % 3 Layers 3 Layers 1.02 LWF-250-6 300 x 250 6 Layers - 193.8 mm 2 - 0.29 % 3 Layers 3 Layers 1.02 P 2D10 D8 200 mm 3D13 50 mm 1700 mm 50 mm 300 mm 1800 mm Beam cross-section RC Beams P 3 Layers 25 mm 3 Layers 25 mm 20 mm 275 mm 20 mm 250 mm 200 mm 3 150 mm Polystyrene 150 mm Layers Polystyrene 200 mm foam block 3 Layers foam block 25 mm 5 Layers 5 Layers 50 mm 50 mm 1700 mm 300 mm 1800 mm Beam cross-section LWF Beams Fig. (1): Setup configurations of RC and LWF Beams . Journal of Science & Technology Vol. (15) No.(1) 2010 JST 6 Figure 2 shows the more clearly details of the arrangement of ferrocement wire mesh reinforcement layers of the cross-section of (LWF-200-5) beam that introduce the novel technique of lightweight sandwich composite by encasing lightweight polystyrene foam blocks as core with high performance ferrocement wire mesh reinforcement as skin layers and then completely encapsulated in high-flowable high-strength cement grout mortar. The performance of the LWF and RC beams is investigated in terms of first crack load, load- deflection curves, stiffness, energy absorption capacity, ductility index, ultimate flexural load-to-weight ratio, load-strain curves, crack patterns, number of cracks, average crack width, crack spacing and the failure mode.
Details
-
File Typepdf
-
Upload Time-
-
Content LanguagesEnglish
-
Upload UserAnonymous/Not logged-in
-
File Pages14 Page
-
File Size-