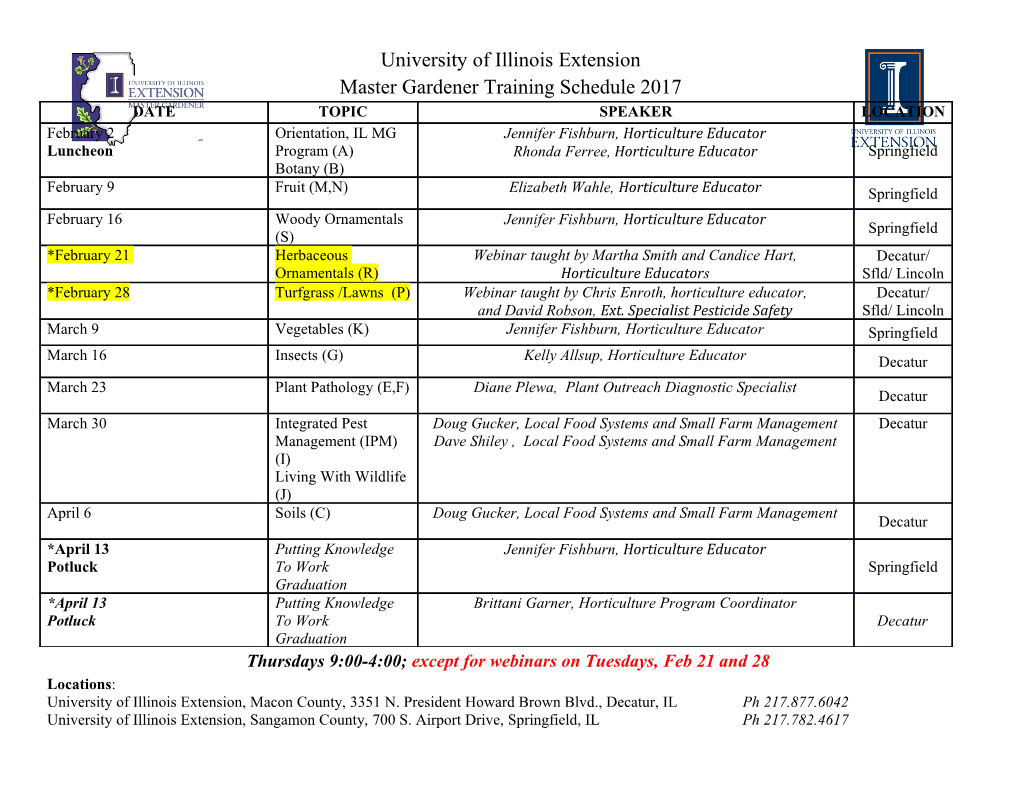
Michigan Technological University Digital Commons @ Michigan Tech Dissertations, Master's Theses and Master's Reports 2016 COMPETITION VEHICLE BASED INTAKE MANIFOLD DESIGN Joshua N. Matiash Michigan Technological University, [email protected] Copyright 2016 Joshua N. Matiash Recommended Citation Matiash, Joshua N., "COMPETITION VEHICLE BASED INTAKE MANIFOLD DESIGN", Open Access Master's Report, Michigan Technological University, 2016. https://doi.org/10.37099/mtu.dc.etdr/281 Follow this and additional works at: https://digitalcommons.mtu.edu/etdr Part of the Automotive Engineering Commons, and the Heat Transfer, Combustion Commons COMPETITION VEHICLE BASED INTAKE MANIFOLD DESIGN By Joshua N. Matiash A REPORT Submitted in partial fulfillment of the requirements for the degree of MASTER OF SCIENCE In Mechanical Engineering MICHIGAN TECHNOLOGICAL UNIVERSITY 2016 © 2016 Joshua N. Matiash This report has been approved in partial fulfillment of the requirements for the Degree of MASTER OF SCIENCE in Mechanical Engineering. Department of Mechanical Engineering – Engineering Mechanics Report Advisor: Dr. Scott A. Miers Committee Member: Dr. James DeClerck Committee Member: Dr. David D. Wanless Department Chair: Dr. William W. Predebon Contents Abstract ..........................................................................................................................................5 1 Introduction .......................................................................................................................6 1.1 Background ...........................................................................................................................6 1.1.1 FSAE Competition .........................................................................................................6 1.1.2 Intake Manifold Tuning ..................................................................................................7 1.2 Hypothesis .............................................................................................................................8 2 Procedure ...........................................................................................................................9 2.1 On-Track Torque Usage Investigation ..................................................................................9 2.2 Engine Model Development ................................................................................................11 2.2.1 Engine Dynamometer Testing ......................................................................................11 2.2.1.1 Engine Instrumentation .........................................................................................11 2.2.1.2 Dynamometer Setup/Testing ................................................................................15 2.2.2 GT-Power Model ..........................................................................................................16 2.3 Intake Design .......................................................................................................................18 2.3.1 Intake Geometry Design of Experiments .....................................................................18 2.3.2 CAD Model Development ............................................................................................19 2.4 Final Validation ...................................................................................................................19 3 Results and Discussion ....................................................................................................21 3.1 On-Track Torque Usage Findings .......................................................................................21 3.2 Dynamometer Testing Results ............................................................................................25 3.3 GT-Power Model Calibration ..............................................................................................26 3.3.1 Model Air and Fuel Flow Calibration ..........................................................................26 3.3.2 Combustion Model Calibration ....................................................................................27 Page 3 of 57 3.3.3 Torque Calibration ........................................................................................................30 3.4 Intake Geometry Refinement Results .................................................................................31 3.5 CAD Model Development and 3-D Printing .......................................................................32 3.6 Performance Comparison ....................................................................................................35 3.6.1 Dynamometer Performance Comparison .....................................................................35 3.6.2 On-Track Performance Comparison .............................................................................36 4 Conclusions and Recommendations ..............................................................................37 4.1 Conclusions .........................................................................................................................37 4.2 Recommendations ...............................................................................................................37 References ....................................................................................................................................39 A Engine Instrumentation Information ............................................................................40 A.1 Encoder, Mount, and Adaptor Shaft Drawings ..................................................................40 A.2 Kulite Pressure Transducer Drawings ................................................................................43 B Yamaha Genesis 80 Information ...................................................................................45 C Additional Torque Usage Information ..........................................................................47 D Matlab Code to Convert ACAP Files to Excel Files ....................................................48 E Cylinder Pressure Traces and Comparison .................................................................50 Page 4 of 57 Abstract A competitive vehicle in Formula SAE needs to be easy for unskilled drivers to extract the maximum performance from. This requires a predictable and manageable torque curve. This report details the development of an intake manifold for a Formula SAE car from a vehicle-based approach to produce this manageable and predictable torque. The current vehicle was instrumented and driven on a representative track to determine the usage of available torque. Based on these findings an ideal torque curve was chosen that favored increased torque at upper engine speed ranges and decreased torque at lower engine speed ranges. A 1-D engine cycle simulation model was developed and calibrated from intake, cylinder, and exhaust pressures measured on a dynamometer. The combustion model used the Wiebe function to model the burn rate and determine the simulated cylinder pressure. A design of experiments was performed with the calibrated 1-D model to find the optimized intake manifold geometry. Primary runner length and inlet diameter as well plenum volume were investigated and sized to produce as close to the ideal torque curve as possible. Based on this geometry a 3-D CAD model was developed and 3-D printed for use on the engine. The fuel delivery and ignition timing of the engine with the 3-D printed intake manifold were tuned on a dynamometer and the torque curve produced was found to be similar to the predicted torque curve at the upper engine speed range but deviate at the mid-range. An on-track vehicle comparison of the new intake manifold to the old intake manifold was attempted but not completed due to cracking of the new intake manifold under vacuum on the vehicle. Page 5 of 57 Chapter 1 Introduction 1.1 Background 1.1.1 FSAE Competition In the Formula SAE (FSAE) collegiate design competition, engineering students from across the globe design and build open-wheel race cars to compete against each other. The drivers for MTU’s FSAE team are members of the team, and engineering students, not professional race drivers. For this reason, it is important to have an easy to drive and predictable vehicle. The torque delivery of the vehicle needs to be manageable and predictable for the driver to consistently drive at the limit. While a predictable and controllable vehicle is important, it is also important to have enough power for the vehicle to perform competitively. This means the torque curve is crucial to the overall performance of both the driver and vehicle. The FSAE rules put many limitations on the engine, including: Four Stroke, Reciprocating Piston Type Maximum Displacement of 710 cc All Intake Air Must Pass Through a Circular 20 mm Diameter Restrictor Throttle Body Must Be Before the Restrictor Due to the limitations put on the vehicle by the rules, the budget limitations of the MTU FSAE team, and the limited high-performance driving experience of the drivers, it is important for the vehicle to be as optimized as possible. Page 6 of 57 1.1.2 Intake Manifold Tuning For a given engine displacement and technology, the amount of integrated torque, or “area under the curve” is largely fixed. The maximum torque generated at a given engine speeds is a product of the air and fuel burned in the cylinder. In a spark-ignited
Details
-
File Typepdf
-
Upload Time-
-
Content LanguagesEnglish
-
Upload UserAnonymous/Not logged-in
-
File Pages58 Page
-
File Size-