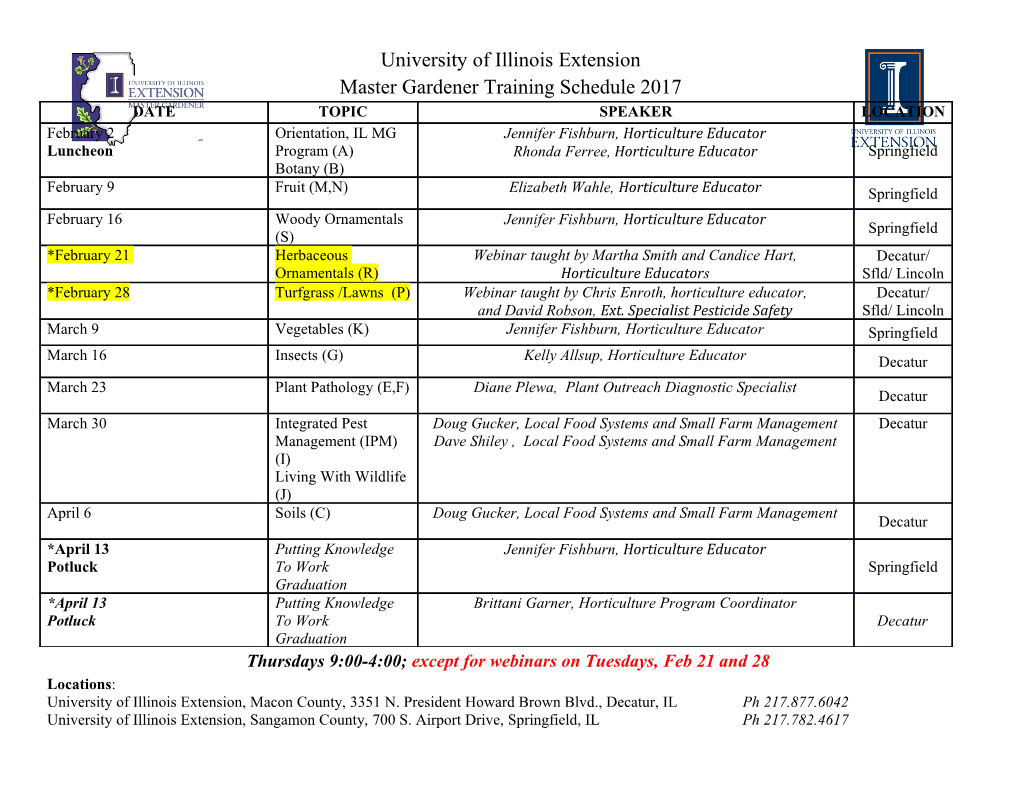
Accepted Manuscript Joining of hybrid AA6063-6SiCp-3Grp composite and AISI 1030 steel by friction welding N. Rajesh Jesudoss Hynes, Associate Professor, M. Vivek Prabhu, Assistant Professor, P. Nagaraj, Senior Professor PII: S2214-9147(16)30162-3 DOI: 10.1016/j.dt.2017.05.014 Reference: DT 251 To appear in: Defence Technology Received Date: 26 December 2016 Revised Date: 5 May 2017 Accepted Date: 24 May 2017 Please cite this article as: Rajesh Jesudoss Hynes N, Vivek Prabhu M, Nagaraj P, Joining of hybrid AA6063-6SiCp-3Grp composite and AISI 1030 steel by friction welding, Defence Technology (2017), doi: 10.1016/j.dt.2017.05.014. This is a PDF file of an unedited manuscript that has been accepted for publication. As a service to our customers we are providing this early version of the manuscript. The manuscript will undergo copyediting, typesetting, and review of the resulting proof before it is published in its final form. Please note that during the production process errors may be discovered which could affect the content, and all legal disclaimers that apply to the journal pertain. ACCEPTED MANUSCRIPT Joining of Hybrid AA6063-6SiC p-3Gr pComposite and AISI 1030 steel by Friction Welding N.Rajesh Jesudoss Hynes 1*, M. Vivek Prabhu 2, P.Nagaraj 3 1* Associate Professor, Department of Mechanical Engineering, Mepco Schlenk Engineering College, Sivakasi, Tamilnadu, India-626005. 2Assistant Professor, Department of Mechanical Engineering, Velammal College of Engineering and Technology,Madurai – 625009 3Senior Professor, Department of Mechanical Engineering, Mepco Schlenk Engineering College, Sivakasi, Tamilnadu, India-626005. Email Id: [email protected] , [email protected] , [email protected] MANUSCRIPT ABSTRACT Joining of metals and aluminium hybrid metal matrix composites has significant applications in aviation, ship building and automotive industries. In the present work, investigation is carried out on Friction Welding of AISI 1030 steel and hybrid AA6063- 6SiC p-3Gr pcomposite, that are difficult to weld by fusion welding technique. Silicon carbide and graphite ACCEPTEDparticle reinforced AA6063 matrix hybrid composite was developed successfully using stir casting method and the joining feasibility of AISI1030 steel with AA6063-6SiC p-3Gr p hybrid composite was tried out by friction stud welding technique. During friction stage of welding process, the particulates (SiC & Graphite) used for reinforcement, tend to increase the viscosity and lead to improper mixing of matrix and 1 ACCEPTED MANUSCRIPT reinforcement. This eventually results in lower strength in dissimilar joints. To overcome this difficulty AA1100 interlayer is used while joining hybrid composite to AISI 1030 steel. Experimentation was carried out using Taguchi based design of experiments (DOE) technique. Multiple regression methods were applied to understand the relationship between process parameters of the friction stud welding process. Micro structural examination reveals three separate zones namely fully plasticized zone, partially deformed zone and unaffected base material zone. Ultra fine dynamically recrystallized grains of about 341nm were observed at the fully plasticized zone. EDX analysis confirms the presence of intermetallic compound Fe 2Al 5 at the joint interface. According to the experimental analysis using DOE, rotational speed and interlayer sheet thickness contribute about 39% and 36% respectively in determining the impact strength of the welded joints. It is found that joining with 0.5mm interlayer sheet provides efficient joints. Developed regression model could be used to predict the axial shortening distance and impact strength of the welded joint with reasonable accuracy. MANUSCRIPT Keywords: Metal matrix composite; Welding; Mechanical properties; Scanning Electron Microscopy 1. INTRODUCTION The welding of composites and ceramics has gathered attention among engineers and scientists in the last decade. It is effectively possible through solid state processes like friction welding and diffusionACCEPTED bonding. In particular, friction welding provides impressive results in joining metals and composites for automotive, ship building and electronic applications [1]. Friction welding process enables the efficient combination of metals and ceramics by harnessing the frictional heat induced by the faying surfaces. A series of thermo-mechanical stages such as generation of heat by friction and bonding due to the upsetting, results in 2 ACCEPTED MANUSCRIPT a unique characteristic weld [2]. The fusion welding techniques for joining dissimilar metals are easily subjected to failure due to their brittle intermetallic compound formation. Moreover, the differences in their melting point results in inappropriate intermetallic structure, poor properties and inferior weld strength [3]. For this study, the hybrid aluminium matrix composite was developed through Stir Casting technique. The SiC present in the hybrid matrix composite increases the thermo- physical and mechanical properties [4] of the composite such as low co-efficient of thermal expansion, higher strength, good specific modulus and so on. The inclusion of graphite [5], a solid lubricant guarantees the usage of hybrid matrix composite in applications demanding high strength and wear resistance. But, there are many other potential problems in welding metal matrix composites with non-metallic reinforcements [6]. The differences in their density can lead to solidification effects such as segregation of the reinforcements in the molten metal. Also, it gives rise to non-uniform packing density which makes conventional techniques not suitable for joining metal matrix coMANUSCRIPTmposites. The other issues are undesirable chemical reactions between the molten metal and the reinforcements during the extended exposure during fusion welding. Being a solid state welding technique friction welding could be employed in crucial situations of joining of dissimilar materials [7]. Morikawa et al. [8] friction welded Stud joints of dissimilar aluminium alloys. Process parameters were varied and joint strength was evaluated and it is found that the tensile strength increased with increase of friction time and friction pressure. Ashfaq et al. [9] studied the influence ofACCEPTED alternate designs of faying surfaces such as providing taper (external and internal) and smoother surfaces on the strength of friction welded Stainless Steel/Aluminium Alloy joints. It was concluded that external taper fayed surfaces could result in improved joint strength. 3 ACCEPTED MANUSCRIPT Moreover, in friction welding process, it has been reported that use of metal interlayer increases the strength of the dissimilar joints by Noh et al [10]. Sassani et al claimed that nearly 40% of the joint strength could be increased when a compatible interlayer is used [11]. The bonding gets better with the use of metallic interlayer [10], since they provide superior flow of the metal during the process. The application of metallic interlayer is considered as essential to produce a strong bond between ceramics and metals. The presence of interlayer is found to be crucial in increasing the strength of the welded joint. It is also discovered that the joints without interlayer have lower strength and lower impact toughness. Moreover, the interlayers act as an active diffusion barrier in preventing the movement of carbon resulting in premature failures [12]. Hence, in the present study, joining feasibility of aluminium hybrid metal matrix composite and AISI 1030 steel is studied by friction stud welding technique using aluminium sheet as interlayer. The micro structural aspects were studied by SEM and EDX analysis and mechanical properties of the dissimilar joints areMANUSCRIPT evaluated. In addition, the current work deals with the study of interaction of various process parameters in determining the impact strength and axial shortening distance of the welded joint. 2. MATERIALS AND METHODS In the present work, investigation on joining of Hybrid AA6063-6SiC p-3Gr p composite to AISI 1030 steel has been carried out using AA1100 interlayer. The composition of AA6063, hybrid composite, AISI 1030 steel and AA1100 interlayer are given in Tables 1, 2, 3 and 4 respectively.ACCEPTED The Aluminium Hybrid metal matrix composite has been developed using stir casting process. Aluminium alloy 6063 is chosen as the matrix material whereas Silicon Carbide (40 µm, average size) and Graphite (60 µm, average size) are selected as the particle reinforcements for the development of HMC. The selection of Aluminium alloy as 4 ACCEPTED MANUSCRIPT the matrix material is due to the optimal presence of magnesium, which affords the coalescence during the welding process. Fig. 1: Dimension of hybrid composite specimen to be held in chuck Fig. 2: Dimension of AISI 1030 steel specimenMANUSCRIPT to be fixed in holder Table 1: Composition of AA 6063 Copper Magnesium Silicon Iron Manganese Zinc Nickel Aluminium 0.25 0.85 0.59 0.22 0.09 0.03 0.01 Remaining Table 2: Composition of hybrid Composite Element Weight/ % AA 6063 91 SiC ACCEPTED6 Graphite 3 5 ACCEPTED MANUSCRIPT Table 3: AISI 1030 composition Carbon Manganese Silicon Nickel Chromium Molybdenum Phosphorous Sulphur Copper Iron 0.30 0.78 0.22 0.10 0.12 0.5 0.02 0.02 0.44 remaining Table 4: AA1100 interlayer composition Copper Magnesium Silicon Iron Manganese Zinc Nickel Aluminium 0.07 0.04 0.59 0.40 0.09 0.03 0.01 remaining 2.1 STIR CASTING OF HYBRID COMPOSITE The composition of hybrid composite
Details
-
File Typepdf
-
Upload Time-
-
Content LanguagesEnglish
-
Upload UserAnonymous/Not logged-in
-
File Pages26 Page
-
File Size-