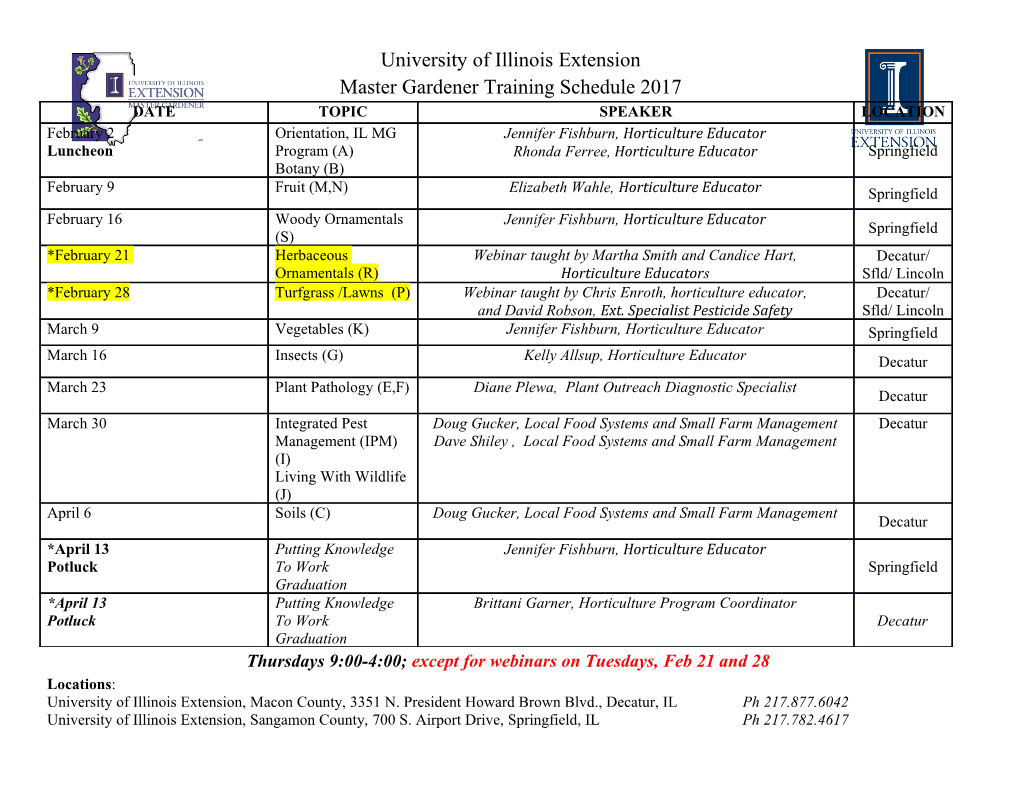
Properties and applications of Epoxy Moulding Compounds 1 Properties and applications of Epoxy Moulding Compounds Due to their excellent electrical properties, Epoxy Moulding Compounds are used for numerous applications in the electrical and automotive industry. Based on the ever increasing miniaturisation of parts and enhanced performance requirements, the challenges for materials used in insulating encapsulation system are increasing dramatically. As well as the high mechanical properties, low water take up and good chemical resistance, there is also a demand for higher thermal and dimensional stability. 1. Thermosetting Materials To better understand the behaviour and the processing demands of thermosetting materials, a short introduction of the general structure of these materials as well as their reaction mechanism can be found below. The typical properties of thermosetting materials are based on their molecular structure. Contrary to the long chain molecules of thermoplastic materials, thermosetting materials show a 3- dimensional cross-linked structure. The moulded part is formed from a melted low molecular and low viscous substance by cross linking as a result of a chemical reaction inside the mould. The reaction is normally activated by heat and is an irreversible process. Thermosetting material meltet cured Thermoplastic material amorph crtistallin Fig. 1 Comparison of thermoplastic and thermosetting materials Hans-Fred Buchmann, Duresco GmbH, CH-4108 Witterswil Properties and applications of Epoxy Moulding Compounds 2 The curing reaction can be described by 3 different mechanisms, depending on the basic resin: Polymerisation: i.e. Polyester (UP) Polycondensation: i.e. Phenol (PF), Melamine (MF), Urea (UF ) Polyaddition: i.e. Epoxy (EP) For the polymerisation (in this case radical polymerisation) double or triple bonds are normally activated by peroxide to enable the molecules to cross link. The polycondensation and polyaddition resins have reactive groups which cross link either with the separation of a volatile substance in the case of a polycondensation mechanism or by simple bonding without any waste products for the polyaddition mechanism. Independent of the basic resin, all thermosetting materials have a comparable composition: matrix composed of resin and hardener filler, inorganic and/or organic strengthening fibers lubricants and mould release agents other additives pigments The cross linking of the molecules results in a different temperature/time behaviour compared to thermoplastic materials. For thermoplastic materials, the viscosity drops with increasing temperature. For thermosetting materials, there are 2 competing effects – the reduction of viscosity due to increasing temperature and an increase in viscosity due to the chemical reaction (see figure 2). This behaviour needs to be carefully considered as it strongly influences the processing of thermosetting materials. Fig. 2 Viscosity of thermosets Hans-Fred Buchmann, Duresco GmbH, CH-4108 Witterswil Properties and applications of Epoxy Moulding Compounds 3 Due to the chemical cross linking, all thermosets show some common characteristic properties such as: irreversible reaction i.e. not possible to melt them high strength and dimensional stability even under load at elevated temperature good chemical resistance Apart from these important basic properties, there are also essential differences which make every type of thermoset suited for specific applications. Below we will discuss those properties that are most relevant for the applications where Epoxy Moulding Compounds are used. 2. Properties of Epoxy Moulding Compounds Epoxy Moulding Compounds consist of a polymer matrix (Epoxy resins, hardeners and accelerators), which are compounded with fillers, reinforcing materials, pigments, release agents etc. to form granulate. Fig. 3 Epoxy Moulding Compound (EMC) Epoxy Moulding Compounds react according to a polyaddition reaction, which means no by- products are formed during moulding (Fig 4). Therefore the same final properties of the moulded part will be reached irrespective of the wall-thickness. When the reaction is finished in the mould no further change of mechanical, electrical or thermal properties takes place. Post curing is not required and the reaction related post shrinkage is virtually zero. This is also one of the reasons for the excellent long-term heat stability of Epoxy Moulding Compounds. Hans-Fred Buchmann, Duresco GmbH, CH-4108 Witterswil Properties and applications of Epoxy Moulding Compounds 4 W1 W2 W3 wall thickness W1<W2<W3 mechanical, thermal and electrical properties mechanical, thermal and electrical T1 T2 T3 Curing time [min] Fig. 4 Final properties dependent on wall thickness The matrix of Epoxy Moulding Compounds forms a three dimensional network during the reaction, which means the end moulded part is effectively one molecule. This three dimensional network shows uniform properties in all directions of the moulded part. With thermoplastic materials, the long chain molecules are generally aligned causing different behaviours in different directions. Figure 5 shows this influence on the basis of the coefficient of thermal expansion comparing glass fibre reinforced epoxy and PPS. PPS 40 % GF ] EP 20 % GF 6 - 10 80 · H L 1 - T height 60 40 height longitudinal 20 transversal transversal longitudinal 0 Coefficient of linear expansion [ K expansion linear of Coefficient -50 0 100 200 [°C] Fig. 5 Coefficient of linear thermal expansion (TMA) Hans-Fred Buchmann, Duresco GmbH, CH-4108 Witterswil Properties and applications of Epoxy Moulding Compounds 5 Epoxy also gives better performance at welding lines. The epoxy reacts across the welding line which results in the mechanical properties remaining close to the 100% level in this area. With thermoplastic materials the situation is completely different with a decrease in mechanical properties down as low as 30 to 50% level at the welding lines due to the parallel orientation of the molecules in this area. The difference between the physical bond in thermoplastics and the chemical cross linking of thermosets also affects the creep behaviour. Figure 6 clearly shows the different performance of thermoplastics compared to an Epoxy Moulding Compound under load and elevated temperature. The effect is already apparent at room temperature and strengthens with increasing temperature. 8 PA66 30% GF 7 PET 30% GF ] % 6 [ e g n 5 a h PBT 30% GF c n 4 o i s n 3 PPS 40% GF e m i d 2 1 EP 20% GF 100 200 300 time [h] Fig. 6 Creep behaviour of different engineering plastics For the analysis of temperature stability, it is necessary to consider 2 different aspects. Firstly, it is necessary to know the relevant properties at the operating temperature, e.g. the mechanical strength, then it is also important to understand how long these properties are preserved at elevated temperature. Thermal endurance properties are described best by IEC 60216. For this test, the test specimen are stored at different temperatures. The test measures how long the specimen can be stored at the measured temperatures, until the tested property drops to a specified percentage of the initial value. These values are measured at room temperature. Figure 7 shows examples of temperature/time graphs measured on the basis of flexural strength for different Epoxy Moulding Compounds. Hans-Fred Buchmann, Duresco GmbH, CH-4108 Witterswil Properties and applications of Epoxy Moulding Compounds 6 Fig. 7 Endurance vs Temperature (IEC 60216) In reality the properties at the operating temperature are important for an application. Figure 8 shows the shear modulus as a function of temperature. 1.E+10 1.E+09 NU 463 NU 514 NU 4414 NU6110 PW126B 1.E+08 shear modulusshear [Pas] 1.E+07 20 40 60 80 100 120 140 160 180 200 220 240 260 280 300 320 340 temperature [°C] Fig. 8 Shear modulus of several Epoxy Moulding Compounds Hans-Fred Buchmann, Duresco GmbH, CH-4108 Witterswil Properties and applications of Epoxy Moulding Compounds 7 Figure 8 shows the wide variations possible with epoxy formulations. All Epoxy Moulding Compounds go through a range, where the mechanical properties drop to a lower level. This lower level is maintained until thermal degradation takes place at very high temperatures. The inflexion point of the curve indicates the glass transition temperature (Tg). Variations to the resin and hardener make it possible to create compounds to achieve a wide range of thermal requirements, starting from quite flexible systems (Tg110°C) up to very rigid systems (Tg250°C). The mould shrinkage of Epoxy Moulding Compounds is influenced by the matrix (resin/hardener) as well as the fillers and the reinforcement materials. As Epoxy Moulding Compounds form a 3 dimensional network when they react, the mould shrinkage is a reproducible physical process and directly dependent on the coefficient of linear thermal expansion. The coefficient of thermal expansion for an Epoxy Moulding Compound can be modified to best match the requirements of the material to be encapsulated. Post shrinkage is insignificantly low at 0,01%. mould shrinkage (%) post shrinkage (%) 0 0.5 1.0 1.5 0 0.5 1.0 1.5 2.0 PF UF MF MPF UP DAP EP Fig. 9 Comparison of mould- and post shrinkage of different thermosets The low shrinkage inevitably causes less tension and results in an excellent dimension stability. It is additionally an important requirement to achieve narrow tolerances which are necessary for functional parts, e.g. sealing areas, electrical insulation or substrate
Details
-
File Typepdf
-
Upload Time-
-
Content LanguagesEnglish
-
Upload UserAnonymous/Not logged-in
-
File Pages13 Page
-
File Size-