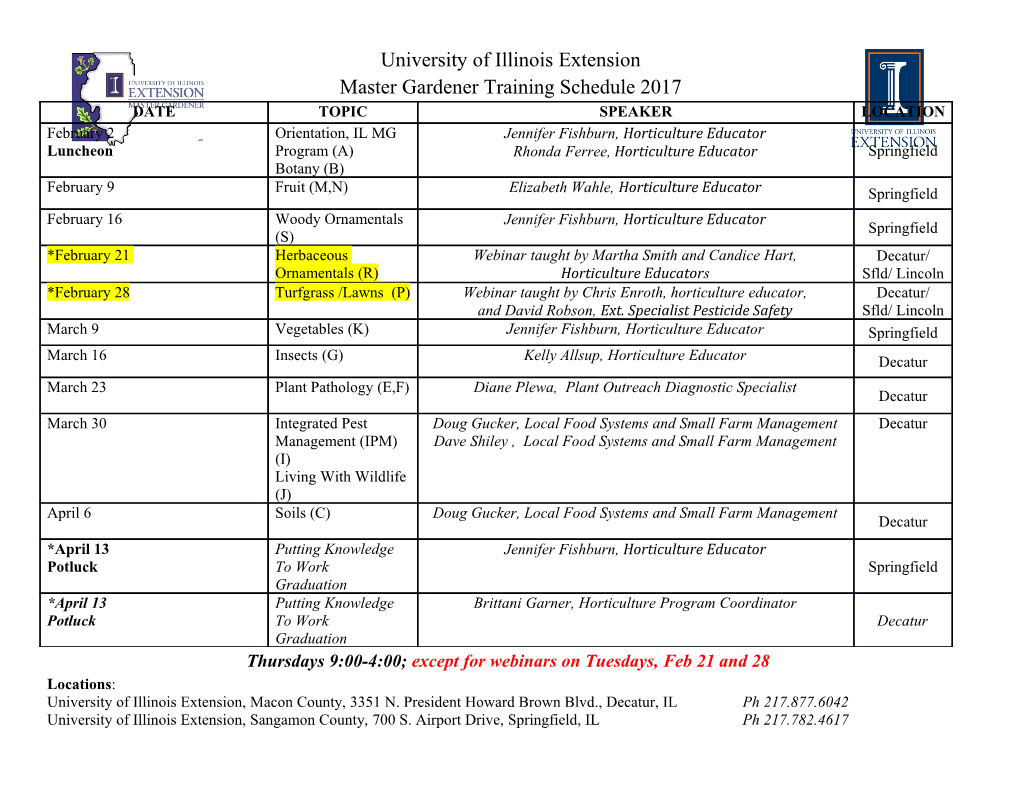
No. 667,198. Patented Feb. 5, 1901. C. F. DICKNSON. MANUFACTURE OF STRUCTURAL BEAMS. (Application filed Feb. 24, 1900.) (No Model.) 2,"WH resses 24-2O Z, Zéozzesoeal eptor UNITED STATES PATENT OFFICE. CHARLES F. DICKINSON, OF WHEELING, WEST VIRGINIA. MANUFACTURE OF STRUCTURAL BEAMS. SPECIFICATION forming part of Letters Patent No. 667,198, dated February 5, 1901. Application filed February 24, 1900, Serial No. 6,391 (No specimens.) To all, whom it. Tay concern: ter to be treated is placed in a metal-planing Beit known that I, CHARLES F. DICKINSON, machine subjected to the action of a cold saw a citizen of the United States, residing at or any other apparatus that has a cutting op Wheeling, in the county of Ohio and State of eration analogous to that set forth. In re 55 West Virginia, have invented a new and use moving the lateral projections or balls of the ful Method for Treating Railroad-Rails, &c., tread the ordinary Web of a railroad-rail is of which the following is a specification. increased in width by cutting off the parts This invention relates to a method of mak stated in Wardly to the plane of the opposite ing various forms of ironwork members or faces of the web, and thereby obtain the ad IO beams out of iron and steel railroad or car ditional extension provided by the usual ver rails whether the latter be new, discarded, or tical thickness of the tread portion of a rail. second-hand or scrap rails, or what is com In the use of railroad-rails for forming iron monly known as “seconds’ in rail-mills; and work members or beams as heretofore prac the object of the same is to cheaply and eco ticed it has been common to work the rail nomically produce various forms of beams by through a rolling-mill and generally reorgan a simple and effective operation and preserve ize its structure and in some instances to en and protect the original flange of the rails at tirely cut off the tread portion of the rail, and the time the several rails are treated and thereby lose the extension of what afterward when joined to construct different forms of becomes the stem of the beam. In other op beams by utilizing a welding heat and a pres erations mechanical coupling devices have sure or blow, and, furthermore, to avoid all been directly riveted or bolted over the abut rolling, molding, and mechanical coupling op ting tread portions of rail-sections; but this erations and devices, as well as dispense with has produced a highly inefficient article in the use of steel billets, pig-iron, or other pri View of the fact that the two tread-surfaces 75 25 mary new material or stock, as in ordinary would form a movable bearing and soon work manufactures of ironWork beams or members. the rivets or bolts loose and render the beam The invention consists in the several steps or member so constructed of very little value which will be more fully hereinafter described from a practical standpoint. It will be ob and claimed. served that in removing the lateral tread pro In the drawings, Figure 1 is a perspective jections or balls of the rails while cold and view of a railroad-rail. Fig. 2 is a similar in accordance With my method the metal of view of a rail as it appears after the tread pro the rail is not in the least changed or weak jections or balls have been removed by one ened and a material saving in material re step of the improvement and forming a T sults by utilizing the extra metal between the 85 beam. Fig. 3 is a sectional view showing the lateral tread projections or balls. Moreover, 35 manner of protecting the rail-flange during the portions that are cut off can be disposed the heating operation previous to welding two of by the manufacturer with profit, and the rail-sections together and of holding the rail first cost of the rails used in forming the sections in positive shape during the Welding beams will be essentially reduced. The beam step to produce another form of beam. Fig. resulting from the removal of the lateral tread 4is a detail sectional view of an I-beam formed projections or balls of the rail can be used by my improved method. Fig. 5 is a detail alone for many purposes without any further sectional view of a Z-beam formed by my im treatment, or the flanges of two of the rails proved method. Fig. 6 is a detail sectional thus prepared can be placed back to back and 95 view of a channel-iron made from the pre securely bolted or otherwise fastened, and 45 pared rail, as shown by Fig. 2. thus produce another combination and a dif The first step of the method is to remove ferent form of beam or support. Further the lateral projections or balls of the tread more, a plurality of the beams thus prepared portion of the rail without the use of heat or can have their flanges or the original rail Oo the operation of a rolling mechanism, and to flange disposed at an angle to each other and 5 O accomplish this the rail of whatever charac the edges joined to thus produce an effective s - 667,198 column, and these combinations could be car point than the line of weld or jointure, and ried on indefinitely, as will be obviously ap by uniting two of the prepared rail-sections in parent. the manner set forth an exceptionally strong Though the rail as prepared and shown by ironwork member or beam will be produced, Fig. 2 may be used alone, as indicated, the and in addition care will be taken in all the progressive steps of the method contemplate steps of the method to avoid detracting in the production of a more serviceable and de the least from the desirable properties and sirable combination, and after the rail has characteristics as to strength and durability been subjected to the cold-cutting operation of railroad-rails and which a rises from their 75 IO to remove the tread projections or balls the original manufacture. Hence the tread pro rail-sections are then in closed within suitable jections or balls are removed by cold-cutting, metallic casings 1, which are case-hardened and in heating the sections to join them the and made in sections, so that they can be degree of heat employed will be that neces easily applied or withdrawn or disconnected sary for welding only, and therefore the hard froin the stock being operated upon. In ar ness of the metal will not in the least be af ranging the prepared rails in these casings fected. In carrying out the steps of the the original rail-flanges are fully inclosed and method it is proposed to use any desired ap completely protected and the extended web paratus or machinery best adapted for the or stem is left projecting a suitable distance purpose, and the casings for holding the pre from one side of each casing. Two of these pared rail-sections during the heating step casings are applied over as many prepared may be varied indefinitely. rails which are to be joined, and after being It will be understood that the beams will firmly clamped or locked the said casings car vary in size and weight proportionately to rying the prepared rails are inserted in a fur the size and weight of the rails from which 90 25 nace and subjected to a high heat or of a de they are formed, and forms of beams or mem gree sufficient to permit a practical welding bers other than those mentioned may be pro operation to be pursued. It will be seen that duced at will without departing from the Sev the flange of each prepared rail will be pre eral steps disclosed. The cheapness of the vented from burning off or losing its shape character of the railroad-rails used in form 95 by reason of the inclosure within the casing, ing the beams and the simplicity and in and, moreover, the said prepared section will expensive character of the method pursued be retained in its shape and prevented from will materially reduce the cost of manufac buckling or twisting by the action of the heat. ture of ironwork members or beams. More The casing will have its exterior portion in over, the simplicity of the method will result OO 35 tensely heated, and this heat will extend par in a quick production, and as the quantity tially into the body of the casing, but will of railroad-rails of the character set forth is not be of sufficient degree at the core or ad almost inexhaustible the manufacturer em jacent the inclosed portion of the prepared ploying the foregoing method will not be con rail to have any injurious effect on the latter fronted with the serious difficulty incident to whatever. After the projecting portions of a scarcity of material or stock. the webs or stems have been heated suffi Eaving thus described the invention, what ciently the two casings are withdrawn from is claimed as new is the furnace and the edges or exposed ends of 1. The method of forming ironwork mem the said webs or stems are brought to bear bers or beams consisting in longitudinally re IIO 45 against each other and so held during the moving the lateral portions or projections of third step of welding, which may be carried the treads or heads of railroad-rails to the on by any of the well-known processes and in plane of the opposite sides of the web by a any preferred manner.
Details
-
File Typepdf
-
Upload Time-
-
Content LanguagesEnglish
-
Upload UserAnonymous/Not logged-in
-
File Pages4 Page
-
File Size-