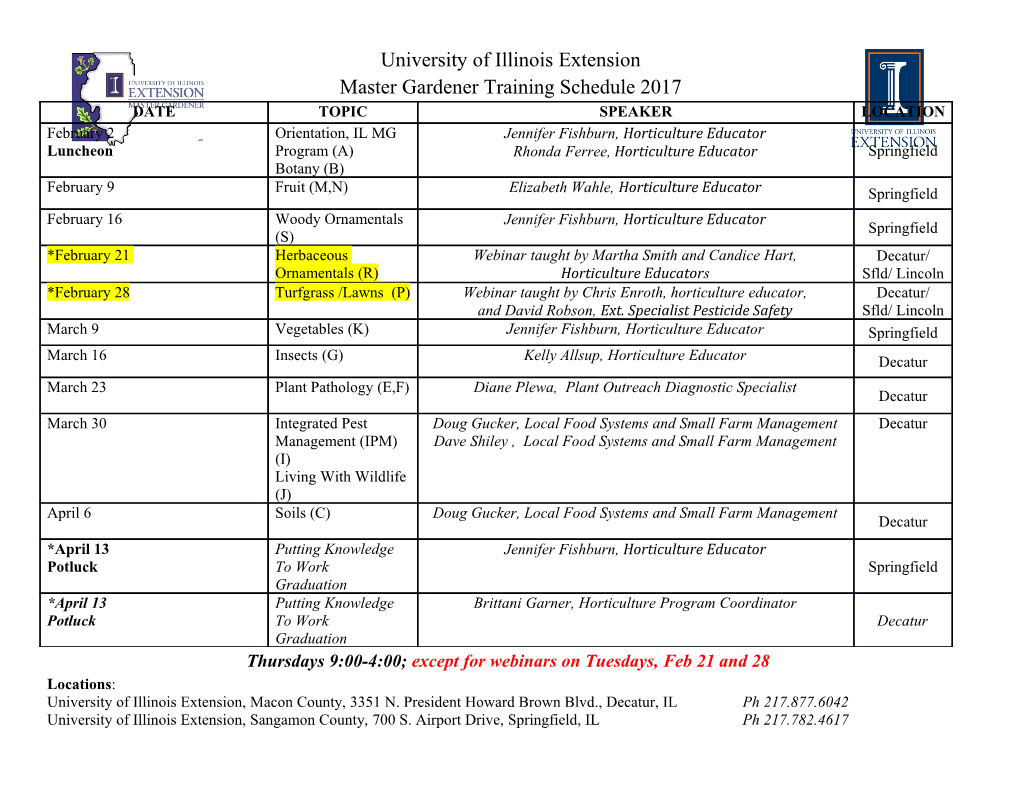
Master of Science Thesis in Electrical Engineering Department of Electrical Engineering, Linköping University, 2018 Estimation of Air Mass Flow in Engines with Variable Valve Timing Elina Fantenberg Master of Science Thesis in Electrical Engineering Estimation of Air Mass Flow in Engines with Variable Valve Timing Elina Fantenberg LiTH-ISY-EX--18/5116--SE Supervisor: Christian Andersson Naesseth isy, Linköpings universitet Erik Höckerdal Scania CV AB Examiner: Martin Enqvist isy, Linköpings universitet Division of Automatic Control Department of Electrical Engineering Linköping University SE-581 83 Linköping, Sweden Copyright © 2018 Elina Fantenberg Abstract To control the combustion in an engine, an accurate estimation of the air mass flow is required. Due to strict emission legislation and high demands on fuel consumption from customers, a technology called variable valve timing is inves- tigated. This technology controls the amount of air inducted to the engine cylin- der and the amount of gases pushed out of the cylinder, via the inlet and exhaust valves. The air mass flow is usually estimated by large look-up tables but when introducing variable valve timing, the air mass flow also depends on the angles of the inlet and exhaust valves causing these look-up tables to grow with two dimen- sions. To avoid this, models to estimate the air mass flow have been derived. This has been done with grey-box models, using physical equations together with un- known parameters estimated by solving a linear least-squares optimization prob- lem. To be able to implement the models in the electronic control unit in the future, only sensors implemented in a commercial vehicle are used as much as possible. The work has been done using an inline 6-cylinder diesel engine with mea- surements from steady-state conditions. All four models derived in this project are based on the estimation methods in use today with fix cam phasing, and are derived from the ideal gas law together with a volumetric efficiency factor. The first three models derived in this work only include sensors provided in commercial engines. The measurements needed as input signals are engine rotational speed, crank angle resolved pressure in the intake manifold, intake and exhaust valve angles and intake manifold temperature. The fourth and last model is divided into three sub-models to model different parts of the four-stroke engine cycle. This model also includes crank angle resolved exhaust manifold pressure and exhaust manifold temperature, where the temperature is the only sensor used in this project that is not provided in a commercial engine. It has been concluded how influential it is to use correctly measured values for the input signals. Since the manifold pressure and the cylinder volume vary dur- ing one four-stroke cycle, it is essential that these signal measurements are taken at the right crank angle degree. With wrong crank angle degree, the estimation is worse than if the cylinder volume is constant for all operating points and the pressure signals are taken as a mean value over the whole four-stroke cycle. Fur- ther development to reach better estimation results with lower relative error is needed. However, for the work in this thesis, the model with best model fit is estimating the air mass flow well enough to use it as a basis for further control. iii Acknowledgments First of all, I would like to thank my supervisor Erik Höckerdal at Scania for the guidance and for always having time for me. You have helped me with all kinds of questions and how to proceed the work. I would also like to thank my supervisor Christian Andersson Naesseth and my examiner Martin Enqvist at Linköping University. A big thank you to my family and friends without whom I wouldn’t have gotten this far. Last of all I would like to thank Pontus for all the support both during the past few years but most of all during this work. Linköping, February 2018 Elina Fantenberg v Contents Notation ix 1 Introduction 1 1.1 Problem formulation . 1 1.2 Method . 2 1.3 Related work . 2 1.4 Thesis outline . 3 2 System description 5 2.1 The four-stroke diesel engine . 5 2.2 Variable valve timing . 6 2.3 Valve timing strategies . 8 2.4 Experimental setup . 10 2.5 Assumptions . 11 3 Modeling 13 3.1 Parameter estimation . 13 3.2 Model validation . 13 3.3 Cylinder volume . 15 3.4 Gas law . 16 3.5 Volumetric efficiency . 17 4 Reference model 19 4.1 Validation with fix valve timing . 19 4.2 Validation with variable valve timing . 21 5 The extended models 25 5.1 Model 1 – Dynamic IVC volume . 25 5.1.1 Modeling . 25 5.1.2 Result and discussion . 26 5.2 Model 2 – Cam phase angle augmentation . 28 5.2.1 Modeling . 28 5.2.2 Result and discussion . 28 vii viii Contents 5.3 Model 3 – Dynamic IVC pressure . 29 5.3.1 Modeling . 30 5.3.2 Result and discussion . 31 6 Model 4 – Division into sub-models 33 6.1 Total mass trapped in cylinder at IVC . 34 6.1.1 Assumptions . 34 6.1.2 Results . 34 6.2 Mass flow during valve overlap . 36 6.2.1 Overlap factor . 36 6.2.2 Assumptions and limitations . 37 6.2.3 Results . 37 6.3 Total mass trapped in cylinder at EVC . 38 6.3.1 Assumptions . 38 6.3.2 Results . 39 6.4 Results and discussion . 40 7 Discussion and conclusions 43 7.1 Sensitivity analysis . 43 7.2 Discussion . 44 7.3 Future work . 46 7.4 Conclusions . 46 Bibliography 49 Notation Abbrevation Meaning BDC Bottom dead center CAD Crank angle degree CI Compression ignition ECU Electronic control unit EVC Exhaust valve closing EVO Exhaust valve opening IVC Inlet valve closing IVO Inlet valve opening OF Overlap factor SI Spark ignition TDC Top dead center VVT Variable valve timing Symbol Description Unit αe Exhaust valve angle ◦ αi Inlet valve angle ◦ ηvol Volumetric efficiency nc Number of cylinders Ne Engine rotational speed rpm pem Exhaust manifold pressure Pa pim Intake manifold pressure Pa Rspec;air Specific gas constant for air J/kgK Rspec;burned Specific gas constant for burned gases J/kgK Tem Exhaust manifold temperature K Tim Intake manifold temperature K 3 Vc Clearance volume m 3 Vd Displaced volume m ix 1 Introduction Fuel consumption, emissions and performance largely depend on the amount of air in the engine cylinder. Measuring air mass flow into the cylinder directly is not cost effective and therefore accurate models are needed. To meet the increas- ingly strict emission legislations, high demands on fuel consumption and perfor- mance from customers, research on new technologies is an ongoing process. One of these technologies is called variable valve timing (VVT), which gives the oppor- tunity to control the opening and closing of the inlet and exhaust valves. These valves control the amount of fresh air inducted into and the amount of gases ex- pelled out of the engine cylinder, respectively. VVT gives the opportunity to have good performance at all operating points. Even higher demands on the air mass flow estimation is required with VVT to be able to control the valves accurately. The air mass in the cylinder must also be known to control the amount of fuel injected to get optimal combustion. The goal of this work is therefore to estimate the air mass that flows through the engine with VVT. 1.1 Problem formulation An accurate estimation of the engine air mass flow is vital to optimize engine operation with respect to emissions, fuel consumption and performance. The air mass flow into the cylinder is important for combustion and the mass flow out of the cylinder is important for after treatment. One example is to keep emissions within allowed limits (García-Nieto et al., 2009). One way to increase the performance of the engine is with VVT of the inlet and exhaust valves (Gray, 1988). This makes it possible to control the amount of air mass in the cylinder. However, this will add two dimensions to the now ex- isting methods for estimating the air mass flow, which are based on large lookup tables that grow exponentially with each additional variable. Therefore, the pur- 1 2 1 Introduction pose of this work is to estimate the air mass flow when VVT is present, as well as to reduce the model complexity. This will be done using grey-box models, combining physical insights with parameters learned from data. 1.2 Method Measurement data from the engine were provided by Scania CV AB. The ap- proach was to first do a reference model that corresponds to the mapping used in the electronic control unit (ECU) today. Then expanded models were devel- oped and validated. Finally another approach was used, where the estimation of the air mass flow was divided into sub-models. Each model derived in this work includes several unknown parameters, which were trained with data by solving a linear least-squares optimization problem. Cross-validation was used to vali- date the models and several methods, e.g. relative error, were used to validate the accuracy of each model. 1.3 Related work Most studies which estimate the air mass flow in an engine are done with fix cam phasing instead of VVT. Also, the studies regarding variable valve timing are often done on spark ignition (SI) engines instead of compression ignition (CI) engines, which is the engine used in this work. This is because there are higher benefits of variable valve timing on SI engines. In Wahlström and Eriksson (2011), a mean-value model of a diesel engine is determined, with the purpose to describe the dynamics of the gas flow in the engine.
Details
-
File Typepdf
-
Upload Time-
-
Content LanguagesEnglish
-
Upload UserAnonymous/Not logged-in
-
File Pages60 Page
-
File Size-