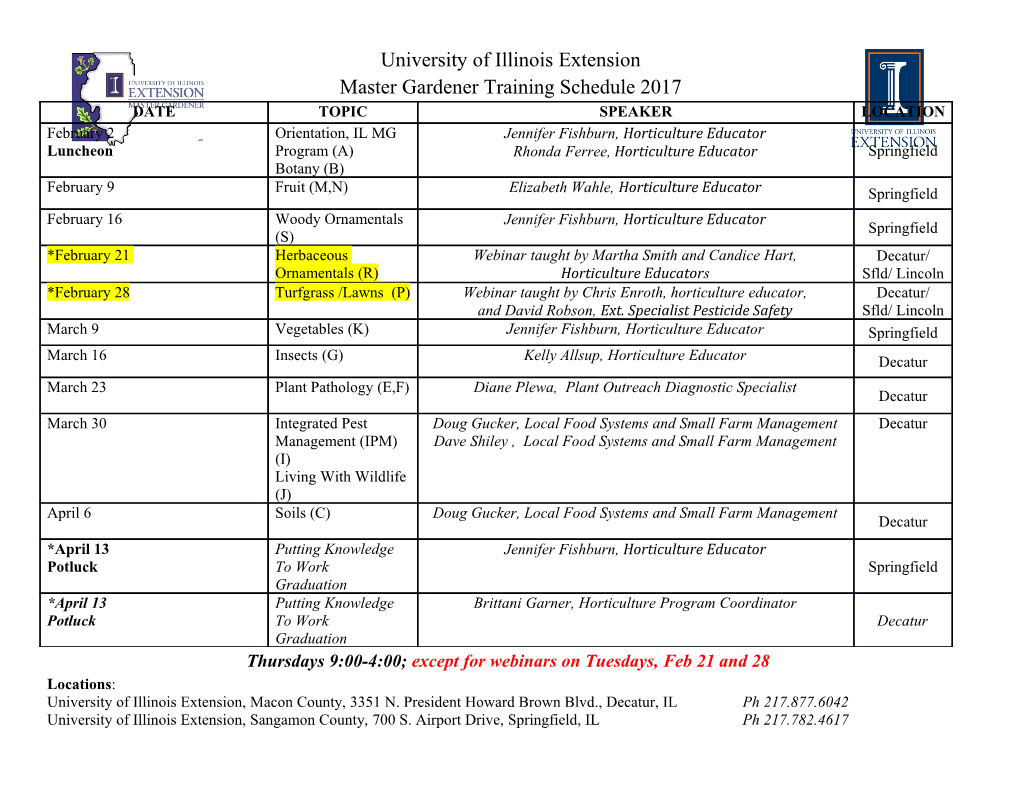
metals Article The Optimum Electrolyte Parameters in the Application of High Current Density Silver Electrorefining Arif T. Aji, Jari Aromaa and Mari Lundström * Department of Chemical and Metallurgical Engineering, School of Chemical Engineering, Aalto University, P.O. Box 16200, FI 00076 Aalto, Finland; arif.aji@aalto.fi (A.T.A.); jari.aromaa@aalto.fi (J.A.) * Correspondence: mari.lundstrom@aalto.fi Received: 5 October 2020; Accepted: 24 November 2020; Published: 28 November 2020 Abstract: Increasing silver production rate has been a challenge for the existing refining facilities. The application of high current density (HCD) as one of the possible solutions to increase the process throughput is also expected to reduce both energy consumption and process inventory. From the recently-developed models of silver electrorefining, this study simulated the optimum electrolyte parameters to optimize the specific energy consumption (SEC) and the silver inventory in the electrolyte for an HCD application. It was found that by using [Cu2+] in electrolyte, both objectives can be achieved. The suggested optimum composition range from this study was [Ag+] 100–150 g/dm3, 3 2+ 3 2 [HNO3] 5 g/dm , and [Cu ] 50–75 g/dm . HCD application (1000 A/m ) in these electrolyte conditions result in cell voltage of 2.7–3.2 V and SEC of 0.60–1.01 kWh/kg, with silver inventory in electrolyte of 26–39 kg silver for 100 kg per day basis. The corresponding figures for the conventional process were 1.5–2.8 V, 0.44–0.76 kWh/kg, and 15.54–194.25 kg, in respective order. These results show that, while HCD increases SEC by app. 30%, the improvement provides a significant smaller footprint as a result of a more compact of process. Thus, applying HCD in silver electrorefining offers the best solution in increasing production capacity and process efficiency. Keywords: high current density; silver electrorefining; energy consumption 1. Introduction Silver is used in many applications such as coins, jewelry, medicine, dentistry, plating, electrical technology, chemical equipment, catalyst, and photography [1]. The recorded production of silver from 1950 to 2018 shows a linear trend with an increasing rate of approximately 300 tons of silver product per year as can be seen in Figure1a [ 2]. In order to meet the increasing demand, increase in the existing capacity or higher kinetics of processing is required. Accordingly, developments in the existing silver electrorefining process were more focused on the increase of processing rate, reduction of metal inventory, and increase of metal recovery rate [3]. One of the developments was high current density (HCD), or the application of current density over 1000 A/m2 silver electrorefining, which offers a logical solution for the increasing capacity demand. Started in 1980 in Sweden, this process development path has recorded 11 installations of HCD silver electrorefining worldwide until 2014 [4]. Furthermore, the reported- and published research and development of the process shows that recent investigations [4–10] were focused on the implementation of higher current density as shown by Figure1b, making it the most renowned improvement in the recent years. Metals 2020, 10, 1596; doi:10.3390/met10121596 www.mdpi.com/journal/metals Metals 2020, 10, x FOR PEER REVIEW 2 of 13 In conventional silver electrorefining free acid [HNO3] is within the range of 0–10 g/dm3 [8], meanwhile for HCD, even though it is not clearly stated, the electrolyte should be less acidic with pH > 2 [4,5]. With the assumption that HNO3 is the only pH regulator, the pH > 2 values correspond to [HNO3] of lower than 0.63 g/dm3. Thus, the electrolyte of HCD has higher [Ag+] and lower [HNO3] in Metalscomparison2020, 10, 1596to the conventional process. The high [Ag+] in electrolyte increases the Ag inventory2 of 14, being one of the disadvantages of the HCD application. FigureFigure 1.1. ((a).). Annual production of silver in the period of 1950–20181950–2018 [22]] andand ((bb)) publishedpublished studiesstudies onon silversilver electrorefiningelectrorefining showingshowing thethe correlationcorrelation ofof currentcurrent densitydensity toto thethe concentrationconcentration ofof silversilver inin thethe electrolyteelectrolyte [[1,41,4––1010].]. Similar to the conventional electrorefining, HCD silver electrorefining uses cast anodes and Another distinct difference of the conventional and HCD process is the current density with AgNO -HNO electrolyte with the arrangement of Moebius cell [4]. Nevertheless, the processes conventional3 silver3 electrorefining current density is within the range of 200–800 A/m2 as shown in difference in electrolyte parameters. Conventional process uses [Ag+] = 40–150 g/dm3 Table 1 [1,5–9,12] whereas the HCD current density targets to 1000 A/m2 [4,5]. As shown in the same (as AgNO )[1,6–12] while the HCD process uses higher concentrations of [Ag+] = 100–150 g/dm3 table, conventional3 cell voltage within the range of 1.5–2.8 V [1,7,8] leads to specific energy in the electrolyte [4]. In conventional silver electrorefining free acid [HNO ] is within the range of consumption of 0.6–0.8 kWh/kg [11,12]. Meanwhile, HCD cell voltage is approximately3 5 V [4] which 0–10 g/dm3 [8], meanwhile for HCD, even though it is not clearly stated, the electrolyte should be less equal to 1.27 kWh/kg. This higher energy consumption of the silver electrorefining process is another acidic with pH > 2 [4,5]. With the assumption that HNO is the only pH regulator, the pH > 2 values disadvantage of the application of HCD. 3 3 + correspond to [HNO3] of lower than 0.63 g/dm . Thus, the electrolyte of HCD has higher [Ag ] and + lower [HNO3] in comparisonTable 1. Conventional to the conventional silver electrorefining process. The process high [Ag parameters] in electrolyte. increases the Ag inventory, being one of the disadvantages of the HCD application. ParametersAnother distinct [1] di fference[5] of the conventional[6] and[7] HCD process[8] is the current[9] density[12] with conventional[Ag+] silver electrorefining50 150–200 current 65– density120 is150 within the30 range–150 of 200–80050 A/m2 as50 shown in Table[HNO1[ 13],5 –9,12] whereas10 the2.5 HCD current0.6–10 density 2–6.2* targets to0 1000–10 A/m2 [4,5-]. As shown10 in the same table,T (°C) conventional- cell voltage35–50 within35 the range32 of 1.5–2.825 V [1,7,8] leads45 to specific- energy consumptionwt%Ag (%) of 0.6–0.895 kWh/kg99.3 [11, 12]. Meanwhile,96.5 HCD86–92 cell voltage86–92 is approximately98 5 V [˃4 99] which equal to 1.27 kWh/kg. This higher0.04 energy– consumption of the silver electrorefining process is another wt%Au (%) 4 0.01 8–9 8–9 0.5 - disadvantage of the application0.07 of HCD. wt%Cu (%) 1 0.4–0.6 3 0.5–1 0.5–1 1 - j (A/m2) 400Table–500 1. Conventional1000 500 silver–800 electrorefining 300# process200– parameters.400 400 400–500 Vcell (V) 2.0–2.5 - - 2.7 1.5–2.8 - 2.0–2.5 Parameters [1][5][6][7][8][9][12] * calculated from the pH information, and # was unit conversion from amps/sq feet. [Ag+] 50 150–200 65–120 150 30–150 50 50 At the[HNO current3] state of10 increasing 2.5 industrial 0.6–10 demand, 2–6.2 improvement * 0–10 to the process - throughput 10 is getting moreT (◦C) important than - ever before. 35–50 On the 35 other hand, 32 the conventional 25 silver 45 electrorefining - processwt% itselfAg (%)has a very wide95 range 99.3 of operating 96.5 parameters. 86–92 Thus, 86–92 optimization 98 for the >process99 is requiredwt% toAu take(%) into account 4 both 0.04–0.07opportunity of 0.01 improvements 8–9 of increasing 8–9 the 0.5 process throughput - wt%Cu (%) 1 0.4–0.6 3 0.5–1 0.5–1 1 - and to havej (A/ mwell2) -designed400–500 process parameters 1000 500–800 for an optimal300 # process.200–400 400 400–500 TheV disadvantagescell (V) 2.0–2.5of high cell voltage - and high - energy 2.7 consumption 1.5–2.8 of the HCD - application 2.0–2.5 in comparison to the* calculated conventional from the process pH information, consequently and # was unitraised conversion a question from amps of whether/sq feet. HCD could be adapted in the existing silver electrorefining to increase the productivity. The process integration At the current state of increasing industrial demand, improvement to the process throughput is getting more important than ever before. On the other hand, the conventional silver electrorefining process itself has a very wide range of operating parameters. Thus, optimization for the process is required to take into account both opportunity of improvements of increasing the process throughput and to have well-designed process parameters for an optimal process. Metals 2020, 10, x FOR PEER REVIEW 3 of 13 probably has been the cause for the low implementation of HCD from the time it was introduced almost four decades ago. In this investigation, the decisive parameters for the HCD application are defined for the optimum silver electrorefining process based on the current industrial conditions. Metals2. Methods2020, 10 , 1596 3 of 14 Investigation on the applicability of HCD process to silver electrorefining is conducted through the simulation of the published models as shown by Figure 2. The models in consideration are The disadvantages of high cell voltage and high energy consumption of the HCD application regression models from the following publications: in comparison to the conventional process consequently raised a question of whether HCD could a. Empirical model of electrolyte conductivity as a function of electrolyte concentrations and be adapted in the existing silver electrorefining to increase the productivity.
Details
-
File Typepdf
-
Upload Time-
-
Content LanguagesEnglish
-
Upload UserAnonymous/Not logged-in
-
File Pages14 Page
-
File Size-