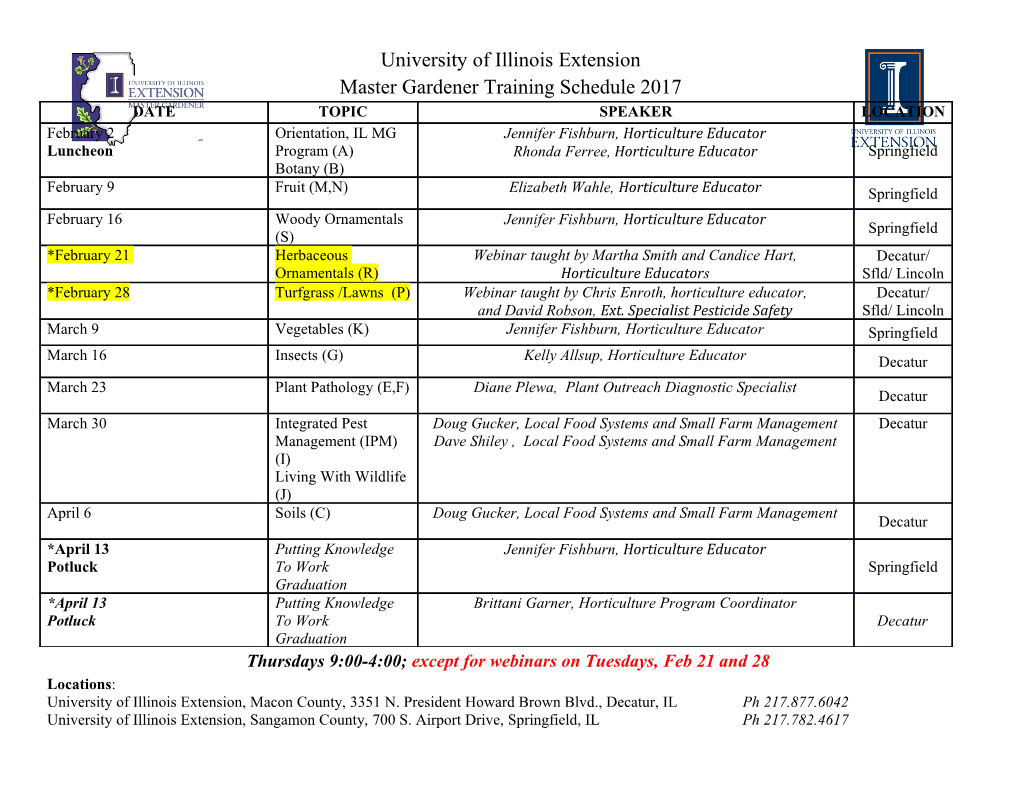
Reversible Solid Oxide Fuel Cell Technology for Green Fuel and Power Production by Nguyen Q. Minh and Mogens B. Mogensen reversible solid oxide fuel cell or syngas (H2+CO) (from mixtures of H2O of practical fuels and has been under (RSOFC) is a device that can and CO2). The chemicals produced can be development for a broad spectrum of A operate efficiently in both fuel used to generate power by the same RSOFC power generation applications. The key cell and electrolysis operating modes. operating in the fuel cell mode or can be features of the SOFC are its all solid state Thus, in the fuel cell mode, an RSOFC stored or converted to other chemicals/fuels construction (ceramic and metal) and high functions as an SOFC, generating electricity for subsequent uses. Similarly, the RSOFC operating temperature (600o-1000oC). by electrochemical combination of a can generate power from biomass-derived The combination of these features leads fuel (hydrogen, hydrocarbons, alcohols, fuels and the electricity generated can then to a number of distinctive and attractive etc.) with air (oxygen in the air). In the be used for a variety of power generation attributes for the SOFC including cell and electrolysis mode, an RSOFC functions applications. stack design flexibility, multiple fabrication as an electrolyzer (in this case, referred The RSOFC is both the SOFC and SOEC options, multi-fuel capability, and operating to as a solid oxide electrolysis cell or incorporated in a single unit. Since the SOEC temperature choices. SOEC), producing hydrogen (from is the SOFC operated in reverse mode and SOFC cells can be configured to be self water) or chemicals such as syngas (from traditionally derived from the SOFC, the supporting (electrolyte-supported, anode- mixtures of water and carbon dioxide) RSOFC being developed is typically based supported, cathode-supported) or external when coupled with an energy source (fossil, from the more technologically advanced supporting (interconnect-supported, sub- nuclear, renewable). Figure 1 illustrates SOFC. Thus, materials for the RSOFC are strate-supported). Stack designs being the operating principles of the RSOFC. those commonly used in the SOFC, i.e., yttria developed for the SOFC include the tubular The RSOFC has the following attractive stabilized zirconia (YSZ) for the electrolyte, design, the segmented-cells-in-series design, features (demonstrated or potential): perovskites (such as lanthanum strontium the monolithic design, and the planar design, compatibility (environmentally compatible manganese oxide or LSM, lanthanum with the planar design currently being with reduced CO2 emissions in power strontium cobalt iron oxide or LSCF) for the most common. These design options generation mode), flexibility (fuel flexible the oxygen electrode, nickel/YSZ cermet permit flexibility to shape the SOFC into a and suitable for integration with any type for the hydrogen electrode and for stacking, structure having the desired electrical and of energy sources), capability (useful for conductive oxides (such as lanthanum electrochemical performance along with different functions), adaptability (suitable strontium chromium perovskite or LSC) required thermal management, mechanical for a variety of applications and adaptable or stainless steels for the interconnect integrity, and dimensional constraint (if any) to local energy needs), and affordability (depending on the operating temperature). to meet operating requirements of specified (competitive in costs).1 The RSOFC thus Like the SOFC, the RSOFC operates in the power generation applications.4 possesses all the desired characteristics temperature range of 600o-1000oC. Specific A wide range of fabrication processes to serve as a technology base for green, operating temperature depends on cell/stack have been investigated for making SOFC flexible, and efficient energy systems in the designs and selected materials.2,3 cells. Fabrication processes developed for future (Fig. 2). the SOFC include conventional ceramic Sustainable energy systems based on the Solid Oxide Fuel Cell Technology processing methods (e.g., tape casting, RSOFC for the future is feasible. An example tape calendering, screen printing, and of such a system is shown schematically The RSOFC is fundamentally and extrusion) and deposition techniques in Fig. 3. In this system, the RSOFC, technologically based on SOFC technology. (e.g., plasma spraying, spin coating, dip operating in the electrolysis mode, uses a In the past 20 years, the SOFC has received coating, electrochemical vapor deposition, 4 renewable energy supply (e.g., solar, wind, significant attention as a clean and efficient electrophoretic deposition). The key step hydro) to produce hydrogen (from H2O) energy conversion technology for a variety in any selected process is the fabrication of (continued on next page) FIG. 1. Operating Principles of an RSOFC (written for hydrogen fuel in SOFC mode and steam electrolysis in SOEC mode). The Electrochemical Society Interface • Winter 2013 55 Minh and Mogensen (continued from previous page) dense electrolytes and the fabrication process selected depends on the configuration of the cells in the stack. One of the key attributes of the SOFC is its multi-fuel capability. For fuels other than pure hydrogen, the SOFC can operate on reformates (via external reformation) or on hydrocarbons and other fuels (via internal reforming or direct utilization).5 The operating temperature of the SOFC can be varied by modifying electrolyte material and/or electrolyte thickness. Examples include operating temperatures of 900o-1000oC for thick (>50 micrometers) YSZ electrolytes,2 700o-800oC for thin (<15 micrometers) YSZ electrolytes2 or doped lanthanum gallate electrolytes,6 500o-600oC for thin doped ceria electrolytes,7 and 400o-500oC for thin doped ceria/bismuth oxide bilayer electrolytes.8 The SOFC has been considered for FIG. 2. Characteristics of a future energy system. a broad spectrum of power generation applications and markets. Applications include power systems ranging from watt-sized devices to multimegawatt power plants and potential markets for the SOFC cover portable, transportation, and stationary sectors. Many of the applications for the SOFC have progressed to hardware demonstration and prototype/ pre-commercial stages while several applications, especially those with large power outputs, are at the conceptual/design stage (Fig. 4). Significant advancements have been made in the past few years in several technological areas critical to the development and commercialization of the fuel cell: performance, fabrication scale-up and miniaturization, fuel utilization, and performance degradation and durability. Performance.—SOFC single cells have exhibited peak power densities as high as 2 W/cm2 at temperatures as low as 650oC (with hydrogen fuel and air oxidant, low fuel and air utilizations).8 SOFC stacks have demonstrated electrochemical performance under operating conditions appropriate for practical uses. For example, a 96-cell planar stack shows a power density of about 0.3 W/ cm2 (voltage of about 0.82 V per cell at 0.364 A/cm2), 715oC on air (15% air utilization), and fuel containing 25.2% H - 22.4% 2 FIG. 3. An example of an RSOFC-based sustainable energy system. N2-14.5% natural gas (NG)-37.8% H2O (68% fuel utilization).9 For state-of-the-art SOFC single of yttria-doped ceria (YDC) into LSM/YSZ the SOFC at reduced temperatures (e.g., cells (having minimal ohmic resistance cathode increased peak power density from <600oC) or stabilizing the nanostructure are contributions from the components), cathode 208 to 519 mW/cm2 at 700oC and power potential approaches to maintain sufficient (oxygen electrode) polarization is generally density at 0.7V from 135 to 370 mW/cm2.12 long-term stability.12,15 the major contribution to cell performance Infiltration of active components as dispersed In SOFC stacks, especially planar losses. Thus, many cathode studies have been particles or connected nanoparticulate stacks with metallic interconnects, contact conducted to obtain a better understanding networks to form nanostructures enhances resistance between the electrodes, especially of the oxygen reduction reaction cathode performance by modifying catalytic the cathode, and the metallic interconnect is mechanisms and develop approaches to 16 10,11 activities and/or conduction pathways of the the major factor in stack performance losses improve cathode performance. One electrode. Use of nanostructures has also and long-term performance degradation. major development in recent cathode R&D been shown to improve anode performance.14 The contact between the ceramic cathode work is the demonstration of infiltration as The main issue is the stability of the and the metallic interconnect tends to a potent means for electrode performance 12,13 nanostructure over extended periods of time change due to thermodynamic driving enhancement. For example, infiltration at high operating temperatures. Operating forces and other operating characteristics 56 The Electrochemical Society Interface • Winter 2013 FIG. 4. SOFC power systems (hardware demonstrators, prototypes and pre-commercial systems up to 200 kW, concepts at 1MW and above). such as temperature distribution, thermal expansion mismatch as operation proceeds. These factors can lead to degradation in long-term operation. It is highly possible that during long-term operation, chemical interaction develops and electrical contact between the cathode and the interconnect
Details
-
File Typepdf
-
Upload Time-
-
Content LanguagesEnglish
-
Upload UserAnonymous/Not logged-in
-
File Pages8 Page
-
File Size-