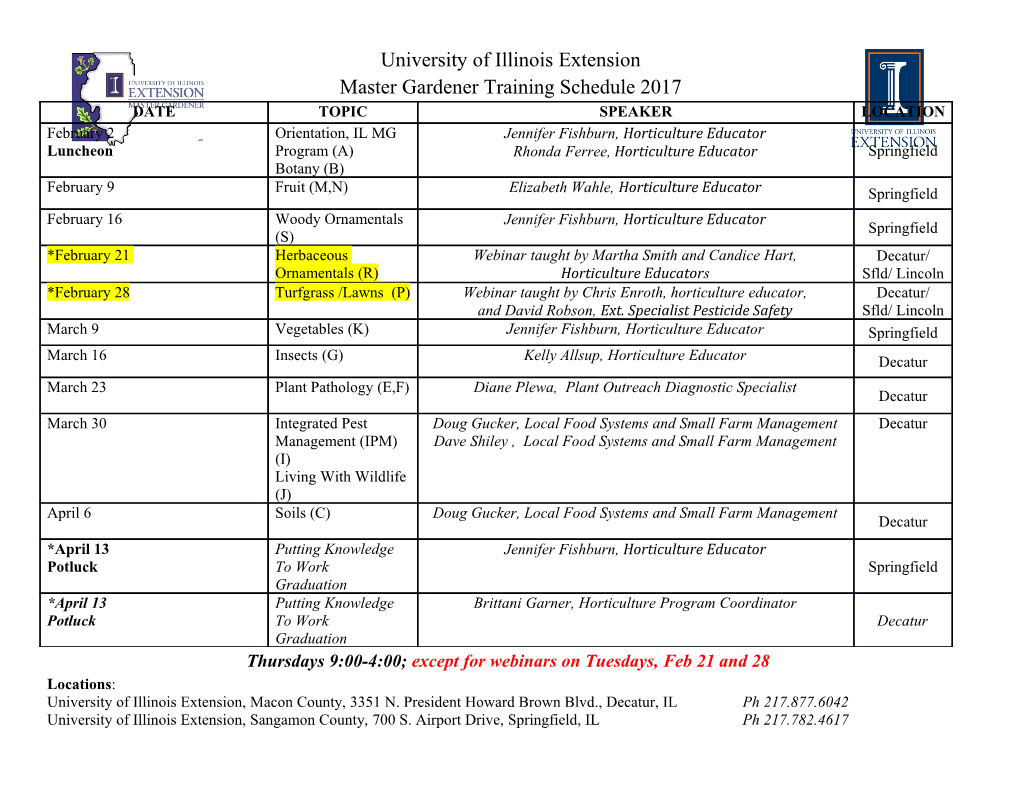
ARTICLE IN PRESS http://www.paper.edu.cn Biosystems Engineering (2006) 93 (4), 383–391 doi:10.1016/j.biosystemseng.2006.01.008 PH—Postharvest Technology Molecular Distillation for recovering Tocopherol and Fatty Acid Methyl Esters from Rapeseed Oil Deodoriser Distillate S.T. Jiang1,2; P. Shao1; L.J. Pan1,2; Y.Y. Zhao1,2 1School of Biotechnology and Food Engineering, Hefei University of Technology, Hefei 230009, China; e-mail of corresponding author: [email protected] 2The Key Laboratory of Agricultural Production Biochemistry of the Ministry of Education, Hefei 230069, China (Received 28 February 2005; accepted in revised form 10 January 2006; published online 9 March 2006) Tocopherol and fatty acid methyl esters (FAME) were recovered through a process involving acid-catalysed methyl esterification and crystallisation of sterols followed by molecular distillation from rapeseed oil deodoriser distillate (RODD), a by-product of vegetable refining edible oil. The effects of evaporating temperature, feed flow rate and wiper rolling speed on yield of tocopherol were systematically studied by response surface methodology (RSM) based on the separation of fame previously. The first fraction, which was collected at 50 1Cat2Á66 Pa, contains mainly hydrocarbons, ketones and aldehydes. The second fraction, which was collected at 100–110 1Cat5Á32 Pa, contains mainly FAME and the content of FAME in the second distillate was above 90% by analysis of gas chromatography–mass spectrometry (GC–MS). The fraction collected at 200–230 1Cat2Á66 Pa was rich in tocopherol (nearly 35%). The overall recovery of tocopherol and FAME were around 50% and 90%, respectively, of the original content in RODD. r 2006 Silsoe Research Institute. All rights reserved Published by Elsevier Ltd 1. Introduction are palm oil for obtaining provitamin A, oils of rice for the oryzanol recovery and natural tocopherols from Molecular distillation is characterised by short vegetable-oil deodoriser distillate, a by-product of the exposure of the distilled liquid to elevated temperatures, vegetable oil-refining process, composed of fatty acids, high vacuum in the distillation space, and a small sterols, tocopherol, sterol esters, hydrocarbons, break- distance between the condenser and evaporator (Shima- down products of fatty acids, aldehydes, ketones and da et al., 2000; Ibanez et al., 2002). The short residence acyl glycerol species. Compounds such as tocopherol, of the liquid on the evaporating cylinder, in the order of sterol and fatty acid methyl esters (FAME) are of a few seconds to 1 min, is guaranteed by distributing the interest as high value-added products because of their liquid in the form of a uniform thin film. By reducing the nutraceutical activities (Kusdiana & Saka, 2004). pressure of non-condensable gas in the evaporator to Fatty acids constitute 25–75% of the distillate lower than 0Á1 Pa, a reduction in distillation tempera- depending on the raw material being refined, the type tures can be obtained. Molecular distillation shows of refining process and the conditions employed therein. promise in the separation, purification and concentra- Recently, fatty acids from deodoriser distillate are only tion of natural products, usually composed of complex limited to the use of non-food, low-cost applications and thermally sensitive molecules. Furthermore, this because they are contaminated. Within the past three process has advantages over other techniques that use decades, interest in reducing air pollution and in solvents as the separating agent, avoiding problems with developing domestic energy sources has encouraged toxicity (Lutisan et al., 2002). research in many countries toward developing non- The substitution of conventional materials used in the petroleum fuels for internal combustion engines; it has nutrition, pharmaceutical, and cosmetic areas by natural been shown that the simple alcohol esters of fatty acids products has gained interest and importance. Examples (FA) are acceptable alternatives diesel fuels. Biodiesel is 1537-5110/$32.00 383 r 2006 Silsoe Research Institute. All rights reserved Published by Elsevier Ltd 转载 ARTICLE IN PRESS 中国科技论文在线 http://www.paper.edu.cn 384 S.T. JIANG ET AL. made from agricultural materials, which are produced standard. All other chemicals and reagents were of via photosynthetic carbon fixation; its combustion does analytical grade. Rapeseed oil deodoriser distillate came not contribute to net atmospheric carbon dioxide levels. from Fenda Oil and Fat Ltd (Hefei, China). Its immediate application would be in the blend with diesel, with a value that can reach up to 20%. Initial efforts at producing biodiesel employed refined edible 2.2. Esterification of rapeseed oil deodoriser distillate oil and animal fats as feedstocks for fuel synthesis. More recently, methods have been developed to produce Rapeseed oil deodoriser distillate contained free fatty FAME from cheaper material, such as spent restaurant acids (FFA), neutral glycerides including monoacylgly- grease and waste edible oil (Hass et al., 2003). In this ceride (MAG), diacylglyceride (DAG) and triacylglycer- study, the potentiality of the process for recovering ide (TAG), and unsaponifiable matters. Sulphuric acid catalysed methylation of the FFA in deodoriser distillate biodiesel (FAME) from rapeseed oil deodoriser distillate À1 (RODD) was presented by converting the fatty acids to (methanol/deodoriser distillate in ml g at 100/100) was biodiesel (FAME). conducted in vigorously shaken glass screw-capped containers at 65 1C in the presence of sulphuric acid Some technical information is available pertaining to À1 the recovery of tocopherol, sterols and FAME, invol- (sulphuric acid/deodoriser distillate in ml g at 4/100) ving a series of chemical and physical processing steps with N2 in gas (Shao et al., 2004). (Ibanez et al., 2002; Mendes et al., 2002). These techniques are used alone or in combination with 2.3. Crystallisation of sterols others, including solvent extraction (Iglesias & Lozano, 2004), urea complexation (Udaya & Fereidoon, 1999). The yield and recovery for crystallisation of sterols However, they involved energy consuming, labour- have been studied as follows: the acetone was used as intensive and low recovery of tocopherol. Recently, it solvent, with crystallisation temperature at 5 1Cand was reported that lipase-catalysed methyl esterification crystallisation time of 3 h. A recovery of sterols as high as followed by molecular distillation are very effective for 85% was achieved by using a single-stage batch crystal- enrichment or purification of useful components in lisation of the solvent/material mixture (mass ratio of deodoriser distillate (Ghosh & Bhattacharyya, 1996; 10:1) (Moreira et al., 2004).The products were defined as Kusdiana & Saka, 2004; Ramamurthi & McCurdy. RODD fatty acids and tocopherol concentrate. 1993). However, the large scale of the lipase reaction is difficult because of lipase characteristics and high costs of lipase. Hence, industrial purification of tocopherols 2.4. Distillation of tocopherol and ester fraction often adopts the acid-catalysed esterification to enhance the profit in the developing countries. Few studies on the The FAME and tocopherol, obtained from RODD optimisation of recovering tocopherol and FAME from sample by the combination of methyl esterification and RODD have appeared in the literature. There appears crystallisation of sterols were fractionally distilled in a to be a need for the optimisation of methyl esterification wiped-film molecular distillation (Fig. 1). The first that is more suitable for the guidance of production. fraction, which was collected at 50 1Cat2Á66 Pa, Taking all of these concerns into consideration, in the contains mainly hydrocarbons, ketones and aldehydes. present work, a molecular distillation process for The fraction from 100 to 140 1Cat5Á32 Pa was collected recovery of tocopherol and FAME from RODD has as the second fraction, which was rich in FAME. And been put forward by a combination of acid-catalysed the third fraction was collected at 170–230 1Cat2Á66 Pa methyl esterification and crystallisation, followed by was rich in tocopherol and collected by changing the fractional distillation of the derived product. collecting flask. The evaporating temperature, wiper rolling speed, feed temperature and feed flow rate were investigated systematically on the recovery of FAME 2. Materials and methods and tocopherol. The feed, residue and two fractions were cooled to room temperature, weighed and analysed 2.1. Materials and reagents for FAME, tocopherol, and sterol content according to the methods described below. Palmitic, stearic, oleic, linoleic acid methyl esters, a,g,d-tocopherol, b-sitosterol, stigmasterol, and campes- 2.4.1. Experimental design for the separation of fatty terol were obtained from Sigma Chemical Co.(St Louis, acid methyl ester and tocopherol USA). They were mixed in amounts proportional to The effects of evaporating temperature, feed flow rate, their mass abundance in RODD which served as vacuum and wiper rolling speed were investigated on the ARTICLE IN PRESS 中国科技论文在线 http://www.paper.edu.cn RECOVERING TOCOPHEROL AND FATTY ACID ESTERS 385 Table 1 Independent variables and their levels for central composite b a design Independent variables Variable levels À10+1 Evaporating temperature X1, 1C 170 200 230 À1 Wiper rolling speed X2, min 50 150 250 À1 c Feed flow rate X3,ml min 30 90 150 responses, namely Y1 and Y2. The model proposed for d each response of Y was h j Y ¼ A þ A X þ A X þ A X þ A X X þ A X X e i 0 1 1 2 2 3 3 4 1 2 5 1 3 f 2 2 2 k þ A6X 2X 3 þ A7X þ A8X þ A9X ð2Þ g 1 2 3 Fig. 1. Schematic diagram of wiped-film molecular still:(a) where: A0 is a constant; A1, A2, and A3 are linear motor drive; (b) feed flask; (c) wiper; (d) residue receiver; (e) coefficients; A4, A5, and A6 are cross-product coeffi- distillate receiver; (f) one-stage condenser inlet; (g) one-stage cients; and A , A and A are quadratic coefficients. condenser outlet; (h) two-stage condenser inlet; (i) two-stage 7 8 9 condenser outlet; (j) cold trap; (k) rotary vane vacuum pump The goodness of fit of the model was evaluated by the coefficient of determination R2 and the analysis of variance (ANOVA).
Details
-
File Typepdf
-
Upload Time-
-
Content LanguagesEnglish
-
Upload UserAnonymous/Not logged-in
-
File Pages9 Page
-
File Size-