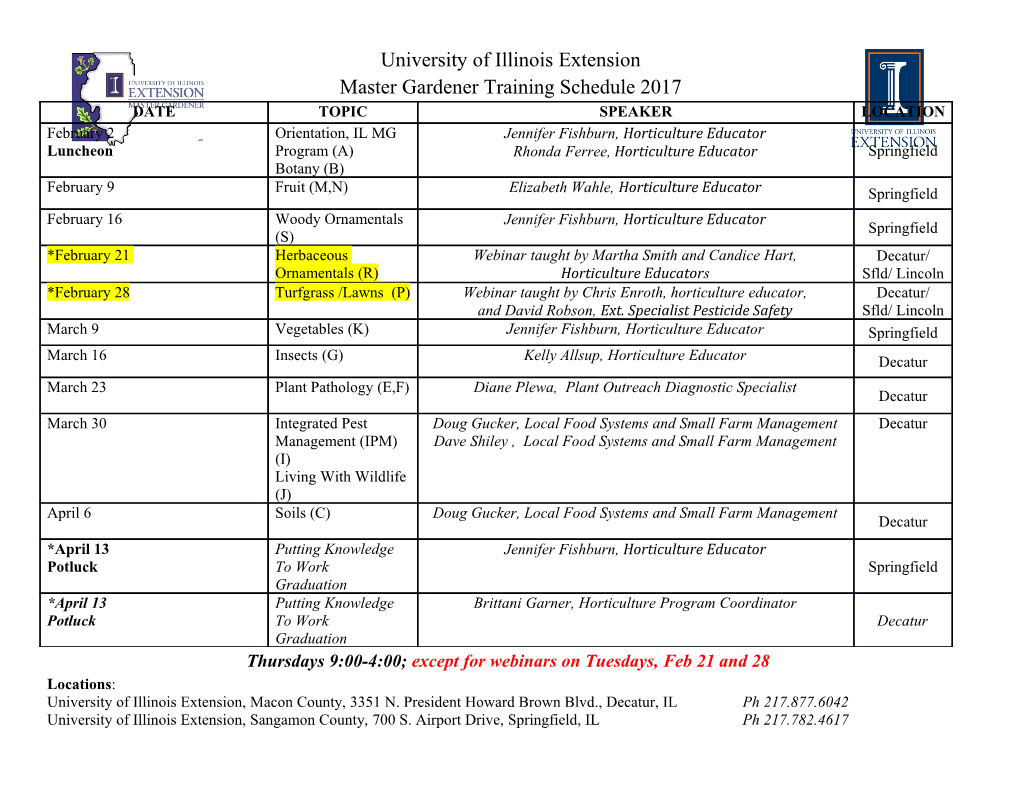
The goals of these developmental efforts were (and still are) to improve efficiency and maximize electrical power output while minimizing power system weight, all the while striving for the highest level of safety. 40 Advanced Isotope Power Systems 3 Expanding RPS Boundaries s RTG technology continued its evolution through the 1970s and 1980s, development of advanced isotope power systems remained an important goal within DOE and NASA. e goals Aof these developmental efforts were (and still are) to improve efficiency while minimizing power system mass, all the while striving for the highest level of safety. With these goals in mind, the agencies sought to take advantage of advancements in materials, power conversion technolo- gies, and fabrication and production techniques. In so doing, their efforts served to expand the knowledge base of RPS technology and provided a platform from which future development efforts might build. A Modular RTG roughout the 1980s, development and production of the new GPHS- RTG for the Galileo and Ulysses missions were the primary focus for DOE. With its modular heat source and improved power conversion system, the GPHS-RTG was a marked improvement over the MHW and SNAP-19 RTGs, especially in terms of specific power. Soon, however, RTG visionaries began to evaluate the viability of a variation of the design that would bring modularity to the converter level as well as the heat source level. In 1980, DOE contracted with Fairchild Space and Electronics Company to develop and analyze a new RTG design based on advanced materials and fabrication techniques, as well as the new GPHS that was under development by LANL, Fairchild, and GE. e RTG concept subsequently developed by Fairchild was called the modular isotopic thermoelectric generator (MITG). As conceived, the MITG concept included a single GPHS module surrounded axially by eight multicouples, as well as a standardized section of thermal insulation, housing, radiator fins, and electrical circuit. With a projected electrical power output of approximately 20 watts, individual MITG units could be combined to create an RTG that would be scalable over a range of power levels. Power-level increments of less than 20 watts would be accommodated by adjusting the size of the heat rejection fins located on the outside of the generator housing.1 A composite of the Jovian system, including the edge of Jupiter with its Great Red Spot, and Jupiter’s four largest moons, known as the Galilean satellites. From left to right, the moons shown are Io, Europa, Ganymede, and Callisto. The Jupiter, Io, Europa, and Ganymede images were obtained by the Galileo spacecraft and the Callisto portrait was obtained by the Voyager spacecraft. (Photo: NASA/JPL/DLR) Photo Credit 41 Advanced Isotope Power Systems Expanding RPS Boundaries e cornerstone of the MITG the gallium-phosphide additive weight, the 12-module MITG was a thermoelectric concept would improve the efficiency of the would weigh roughly half of the called the multicouple. Developed thermoelectric material by reducing GPHS-RTG. With such promising by the Syncal Corporation, the its thermal conductivity. e performance, fabrication and multicouple concept consisted anticipated benefit of the MITG testing of the new thermoelectric of an array of p- and n-type was improved power conversion materials and multicouples were thermoelectric legs that were efficiency over the unicouple design performed during 1981 through connected to a common hot shoe, employed in the GPHS-RTG. 1983 to determine performance or heat collector, and cold-shoe and viability under conditions that mounting stub. In addition to the Based on an initial concept, simulated operational temperatures multicouple concept, Syncal had an MITG consisting of 12 of the GPHS-RTG.1 Among other also developed a modified silicon- power modules would generate things, test engineers sought to germanium thermoelectric alloy approximately 280 We, which determine the performance of that included a small amount of was comparable to the electrical the gallium-phosphide-doped gallium phosphide. Early testing output of the GPHS-RTG and its 18 silicon-germanium thermoelectric indicated that the presence of GPHS modules. Relative to system material relative to the standard silicon-germanium used in the GPHS-RTG and to estimate module lifetime through measurement of the degradation of individual multicouples. e testing would also serve to confirm adequacy of fabrication and manufacturing techniques associated with the thermoelectric materials and multicouples. Two test assemblies, each consisting of eight MITG multicouples positioned inside a prototypic section of the generator housing, were subsequently fabricated and tested. Multicouples made from the modified silicon- germanium were used in one test module, while standard silicon- germanium multicouples were used in the second test module. e test MITG converter unit concept. (Graphic developed by GE; provided by INL RPS Program) 42 Atomic Power in Space II Chapter 3 assemblies were heated electrically MOD-RTG the gallium phosphide, and using a heater that was enclosed in thermoelectric degradation faster an insulated graphite box having Managed for DOE by GE, the goal of than expected. In its attempt to the same outer dimensions as a the MOD-RTG program was to address the thermoelectric issues, GPHS module. develop a ground demonstration DOE suspended fabrication of the system to test the modular RTG ground demonstration system in e tests served their purpose, concept. Beginning in October 1983, mid-1986. Efforts to address the as a number of issues were a three-year plan was developed to multicouple performance issues subsequently identified. For fabricate and test an electrically stretched into a multi-year task and example, crack formation was heated MOD-RTG demonstration were the primary focus of project observed in the multicouples. unit based on six GPHS converter efforts through 1992 when the Subsequent investigation revealed units.5 By mid-1985, GE (with the project was finally terminated. In the cause of the cracking to be help of Fairchild) had completed spite of the difficulties encountered thermal stresses occurring at the a reference flight design and a and technical challenges that joints of the thermocouple array ground demonstration system remained at the time of project and the hot and cold shoes. e design. With a single thermoelectric termination, the nine-year MOD- multicouple was subsequently multicouple device designed to RTG effort did see some significant redesigned to incorporate stress- produce 19 We from one GPHS accomplishments, including the relief features at the problem module, the reference design development of reproducible areas.2, 3 In addition to the stress- consisted of 18 GPHS modules and manufacturing processes for cracking problem, independent 144 thermoelectric multicouples multicouple fabrication, resolution testing of the gallium-phosphide- to produce 340 We.6 With a of mechanical and electrical- doped silicon-germanium projected specific power of shorting problems that had been thermoelectric material, performed approximately 7.9 We/kilogram identified early in the project, at DOE’s request, revealed material (based on a weight of approximately and an understanding of the efficiencies that were lower than 42 kilograms [92 pounds]), the degradation mechanisms associated those previously reported (although MOD-RTG reference flight design with the multicouples. Although they were higher than those of was significantly higher than the follow-on work was recommended, the standard silicon germanium 5.4 We/kilogram GPHS-RTG. DOE priorities shifted to alloy). Lessons learned from the Fabrication of a ground production of the GPHS-RTGs for testing were incorporated into a demonstration system began in the Cassini mission slated for flight revised MITG design as well as the summer of 1985. in 1997.7 fabrication and manufacturing processes. With improvements Although initially optimistic, the underway, DOE decided to test MOD-RTG project soon found the MITG technology in a ground itself facing problems similar to the demonstration system as part of a MITG effort. Multicouple testing follow-on modular (MOD) RTG revealed continued performance development program (MOD- issues, including mechanical and RTG). e MITG program ended in electrical shorting problems, September 1983.4 material issues associated with 43 Advanced Isotope Power Systems Expanding RPS Boundaries Taking Energy From Heat Thermodynamic cycles are the basis for many common technologies, including refrigeration, car engines, and aircraft jet engines. A thermodynamic cycle is a process that manipulates the temperature, pressure, and volume of a working uid to either convert heat into energy or use energy to remove heat. Each cycle has its own intricacies but shares four common processes: compression, heat addition, expansion, and heat removal (cooling). Three thermodynamic cycles are of key interest to the space program due to their high eciency and compatibility with various energy sources (e.g., solar and nuclear). Rankine—Often used in steam Brayton—Jet engines and power- Stirling—As with other cycles, the power plants where water is boiled producing gas turbines often use this working gas is compressed, heat is to produce superheated steam, cycle. A working gas is compressed, added, the gas is expanded, and heat which is expanded through a turbine heated to increase its pressure, is removed to restart the process. A to produce electricity; the steam
Details
-
File Typepdf
-
Upload Time-
-
Content LanguagesEnglish
-
Upload UserAnonymous/Not logged-in
-
File Pages44 Page
-
File Size-