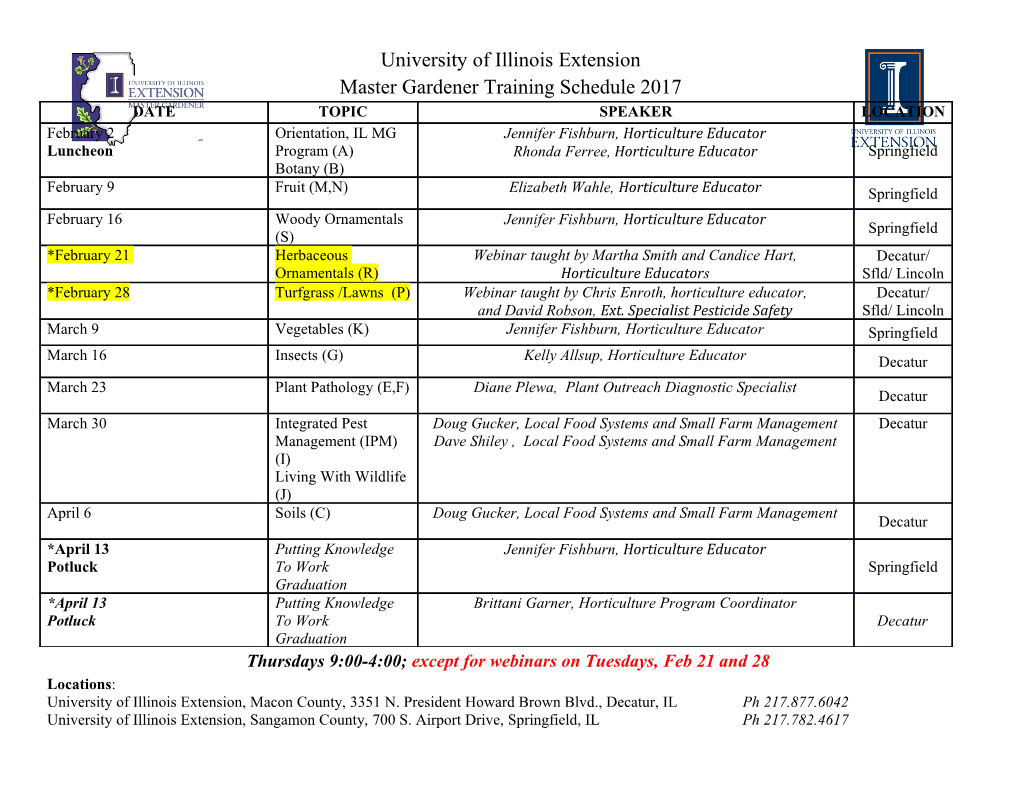
28 April 2006 Challenge X Year 2: Spring Technical Report University of Tulsa Challenge X Team The University of Tulsa Copyright © 2006 The University of Tulsa ABSTRACT performance under selected control strategies are being used to project how well the actual vehicle will meet the Using General Motors’ Vehicle Development Process, team’s vehicle technical specifications (VTS). Testing is the University of Tulsa’s Challenge X team (TUCX) has underway for comparing actual vehicle performance to designed, modeled, and implemented a novel vehicle simulation results. architecture that will increase the fuel economy of a 2005 Chevrolet Equinox while simultaneously OVERVIEW OF COMPONENT SELECTION AND maintaining performance. All of the major new and HYBRID CONTROL modified components are installed in the vehicle, and the control system can operate all of them at a basic Previous TUCX reports described the decision to use a level. TUCX is now optimizing the control system for diesel-electric through-the-road parallel hybrid economy and user-friendliness via on-road testing. architecture with fuel cells providing additional power. A schematic of this architecture is shown in Figure 1. At INTRODUCTION the present time, the project-specific major components have been received through the sponsor donation The University of Tulsa is one of seventeen university program and have been integrated into the vehicle teams in the Challenge X advanced vehicle design infrastructure, as well as locally-built support and competition. The challenge of the event is to reduce the infrastructure components. fuel consumption and lower the emissions of a crossover sport utility vehicle without compromising its Internal Combustion Engine performance or utility characteristics. The competition is managed by the Department of Energy’s Center for TUCX selected and received a GM 1.9 l four-cylinder Transportation Research at Argonne National 150 hp (112 kW) CDTI (common rail direct injected Laboratory (ANL) in partnership with General Motors turbocharged) diesel engine for the internal combustion (GM) with the cooperation of many industrial sponsors. engine (ICE). This state-of-the-art compression ignition The target vehicle is the 2005 Chevrolet Equinox. engine was developed by the GM/Fiat partnership and is used in Opel Vectra passenger cars in Europe. It was The three-year program follows a vehicle development made available through the GM Parts program. This process similar to that used in the automotive industry to engine drives the front axle, and, while it is not powerful develop new products. For the first year, the team’s enough to meet all of the VTS alone, it provides enough focus was on simulation and design studies with limited power to meet basic propulsion needs for cruising and hardware testing. This optimized the design before towing. The TUCX strategy is to run the diesel engine investment in major hardware assembly and testing. only when it is most efficient, and to shut it off when it is This year is devoted to refining, installing, and testing not needed. The engine will run on a mixture of 80% the design innovations developed during the first year petroleum-based diesel and 20% bio-diesel (B20), which studies. The third year provides for refinement of the is stored in the competition-mandated liquid fuel tank. design and enabling all of the vehicle’s original utility and This tank is mounted under the rear of the vehicle and functionality. can be easily removed for fueling or fuel measurement. In this report, the Tulsa team will briefly describe their Electric Motor vehicle architecture, describe how the proposed design of the first year study is being integrated into the The electric motor driving the rear axle is a Ballard Equinox, and summarize the progress of Integrated Power Train (IPT) induction motor provided implementation. The report will also analyze the control through the Ballard component donation program. The strategy and subsystem architecture models. Although IPT includes the electric motor, controller, gearing, and much of the work has been completed, continuous differential in one unit. It provides up to 2500 Nm of improvement on the control systems will continue until propulsion torque or 1250 Nm of braking torque at shaft the competition. Continued simulation studies of vehicle speeds less than 300 rpm, and decreasing amounts of 1 torque at progressively higher speeds up to 1200 rpm. With TUCX’s parallel through-the-road design, the The motor has a maximum short-term output power vehicle will have all-wheel drive when both the diesel capability of 65 kW. The motor provides torque to the engine and the electric motor are running. rear wheels when the diesel engine is disengaged, assists the engine during peak torque demands, and recaptures energy through regenerative braking. Regenerative braking (a negative torque demand) Fuel Cells recaptures kinetic energy and stores it in the Energy Storage System (ESS) when braking by using the motor Two 1.2 kW Ballard Nexa proton exchange membrane as a generator. (PEM) fuel cells are installed for onboard electricity generation. These fuel cells were acquired through the Ballard component donation program. The output of the fuel cells charges the traction battery and powers 12 V accessories via the energy conversion subsystem. Manual Diesel Transaxle Engine 6-speed 4 cyl, 112 kW A Quantum H2 tank stores gaseous hydrogen for the fuel cells. This tank is plumbed to a WEH fill receptacle on the exterior of the vehicle for refueling. The tank, fuel cells, and related plumbing are mounted H2 B20 in the rear cargo space, but are totally enclosed and 30 l F vented only to the exterior of the vehicle. Gas sensors, R both stand-alone and built into the fuel cells, monitor for O N hydrogen leaks. T Energy Conversion Fuel Cells Energy Conversion 2 x 1.2 kW 40 VDC to 120 VAC 120 VAC to 120 VAC to The output from each fuel cell, which ranges from about 350 VDC 14 VDC 30 to 40 V DC, is converted to 120 V AC with an Analytic NiMH Battery Systems LVS 1000 inverter. Since the fuel cell is very 8.5 Ah sensitive to voltage ripple, a filter circuit is installed between the fuel cell and the inverter. This 120 V AC is then rectified and converted to 350 V DC to recharge the 12 V traction battery, using two Vicor 500 W DC-DC Accessories converters. The 120 V AC is also rectified and converted to 14 V DC to power 12 V nominal accessories with a Vicor DC-DC converter. Finally, the Electric Motor/ Generator 120 V AC is also available directly to power standard with Transaxle appliances. 65 kW peak There are two identical halves to the system for a total of two filter circuits, two LVS 1000 inverters, four 500 W Vicor DC-DC converters with 350 V DC output, and two Figure 1. Powertrain Architecture Vicor DC-DC converters with 14 V output. The total output power available is 2000 W. Transmission Electrical Energy Storage System (ESS) TUCX has chosen a manual transmission over a conventional automatic or continuously variable The main ESS is the Cobasys NiMHax 288-60, which is transmission for the diesel because of its higher a nickel metal hydride (NiMH) battery designed for use in small SUVs. It has a nominal voltage of 288 V at efficiency and its ability to optimize the performance o potential of the diesel engine using “driver-in-the-loop” 35 C, a nominal capacity of 8.5 Ah and a maximum control. The chosen six-speed F40 manual transmission instantaneous power output of 60 kW. The battery is used in several vehicles including the Opel Vectra, supplies energy to the electric motor for propulsion and and was acquired through the GM Parts program with stores energy generated by regenerative braking and by the diesel engine. the fuel cells. It was received through the Cobasys component donation program. The Ballard IPT includes its own gearing for wheel speeds up to 110 mph, so no external transmission is This battery was initially installed under the vehicle, required for the rear axle. between the frame rails and just ahead of the rear wheel wells. Since then, Cobasys supplied a replacement 2 battery with enhanced safety features, which had a would be needed to drive the compressor. For Year 3, slightly larger housing that would not fit in the original TUCX is considering using the energy generated by the location. The battery is now located in the floor of the fuel cells to power an electric compressor in order to vehicle just in front of the rear seat. This creates some make the HVAC system fully hybrid. issues with passenger comfort and seating, but this location does not require modifications that would affect Control System the structural integrity of the vehicle. Special housings have been added to ensure passenger safety. The control and data acquisition system is implemented using National Instruments’ LabVIEW software and A conventional 12 V flooded lead-acid battery runs compactRIO real-time controller. Both the hardware and standard 12 V accessories, including the starter motor software were donated by National Instruments. A block for the ICE. This battery is recharged by the ICE diagram of the system design is shown in Appendix A. alternator and the 14 V output of the energy conversion Much of the communication between the new hybrid subsystem. system components and the existing Equinox systems is by the high-speed CAN (Controller Area Network) Cooling Systems protocol, but there is also a system of non-networked analog and digital I/O. The system can run completely The stock radiator, filled with standard non-Dexcool autonomously, or a laptop can be connected for antifreeze and water, cools the diesel engine.
Details
-
File Typepdf
-
Upload Time-
-
Content LanguagesEnglish
-
Upload UserAnonymous/Not logged-in
-
File Pages14 Page
-
File Size-