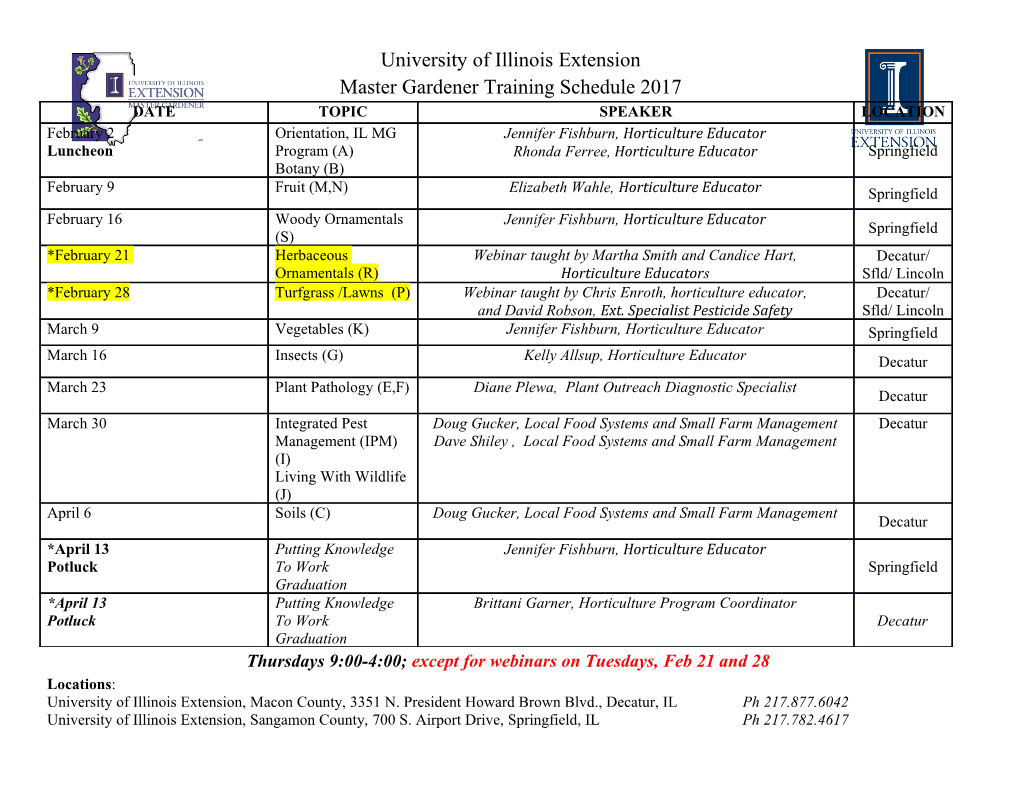
2008:106 MASTER'S THESIS Blends of EPDM rubber/Thermoplastics Jinxia Li Luleå University of Technology Master Thesis, Continuation Courses Advanced material Science and Engineering Department of Applied Physics and Mechanical Engineering Division of Polymer Engineering 2008:106 - ISSN: 1653-0187 - ISRN: LTU-PB-EX--08/106--SE TABLE OF CONTENT PREFACE ...................................................................................................................................I ABSTRACT.............................................................................................................................. II LIST OF TABLES AND FIGURES........................................................................................ III ABBREVIATION..................................................................................................................... V I. INTRODUCTION .................................................................................................................. 1 I.1. Recycling of rubber.......................................................................................................... 1 I.2. Rubber Recycling by Blending with Plastics................................................................... 3 I.3. Compatibilization............................................................................................................. 5 I.3.1 nonreactive compatibilizers ....................................................................................... 9 I.3.2 reactive compatibilizers ........................................................................................... 11 I.4. Blending methods .......................................................................................................... 16 II. OBJECTIVES...................................................................................................................... 18 III. MATERIALS AND METHODS....................................................................................... 19 III.1. Materials...................................................................................................................... 19 III.2. Methods....................................................................................................................... 20 III.2.1. Specimens............................................................................................................. 20 III.2.2. Mechanical testing procedures............................................................................. 20 III.2.3. SEM analysis........................................................................................................ 23 III.2.4. DSC analysis ........................................................................................................ 23 III.2.5. Compressive set testing........................................................................................ 23 IV RESULTS AND DISCUSSION ......................................................................................... 25 IV.1 Non-reactive compatibilization.................................................................................... 25 IV.2 Reactive compatibilization........................................................................................... 31 IV.3 Effect of pressing pressure during plate production .................................................... 38 IV.4 Effect of unvulcanized rubber...................................................................................... 39 IV.5 Microstructure analysis................................................................................................ 41 IV.6 Comparison of the properties between LDPE/EPDM and EMA/EPDM blends ......... 43 A V. CONCLUSIONS ................................................................................................................. 49 VI. FUTURE WORK............................................................................................................... 51 VII. REFERENCES ................................................................................................................. 52 Appendix A1. Low density polyethylene data sheet................................................................ 56 Appendix A2. EMA copolymer data sheet .............................................................................. 57 Appendix B. EXACT 0210 data sheet ..................................................................................... 59 Appendix C. SP-1045 & HRJ -10518 data sheet ..................................................................... 60 Appendix D. SAMPLE LIST (wt%)........................................................................................ 62 Appendix E. Price Index list of materials (reference value only) ............................................ 64 B PREFACE This thesis was carried out at the Division of Polymer Engineering at Luleå University of Technology during the period from February 2008 to October 2008. First of all, I would like to give my special thanks to my supervisor Dr. Lennart Wallström, for his academic instructions and all the support during this thesis. I also thank Mr. Johnny Grahn, Lars Frisk and Roberts Joffe for their technical support and instructions. I also would like to thank all my colleagues at the Polymer Division for all the help they gave me. This thesis is part of AMASE Master Program, which is financed by European Commission and is gratefully acknowledged. Finally, I wish to express my gratitude to my family for all their support and encouragement. I ABSTRACT Blends containing recycled EPDM rubber and thermoplastics, EMA and LDPE were studied. Two compatibilization methods, reactive and non-reactive, were evaluated. Ethylene octene copolymer (EXACT 0210) was used as non-reactive compatibilizer. Phenolic resins (SP1045 & HRJ10518) were reactive agents. There existed an optimal composition of compatibilizers which were 25wt% in the case of reactive and non-reactive agents added to 15wt%EMA and 55-60wt% EPDM rubber. EXACT-compatibilized blends gave high elongation at break while phenolic resin-compatibilized mixtures gave high stiffness in comparison with the chosen reference material. Comparison in compatibilizing capabilities HRJ-10518 and SP-1045 was carried out. The former one had better capabilities than the latter at high compatibilizer content. Talcum was used as anti-agglomeration agent but failed to work properly. Pressing pressure could be minimized without any adverse effect. Non- vulcanized rubber was used to enhance tear strength but its effect was small by assuming that there exists degradation of the interfacial surface at high temperature. SEM analysis revealed homogeneous microstructure in both kinds of compatibilization. EXACT 0210-compatibilized blends showed more plastic deformation of the matrix than reactive blends. Stable connection between phases was also observed. Tensile strength of the LDPE based blends were a little lower than that of EMA based blends and the hardness was a little higher. Compared to EMA based blends, the elongation at break was much lower while the young’s modulus was much higher with LDPE based blends. Compression set of both LDPE and EMA based blends was high compared to the reference materials. Key words: Recycled EPDM rubber, unvulcanized rubber, LDPE, EMA, reactive compatibilization, non- reactive compatibilization, ethylene octene copolymer, phenolic resins, tensile properties, tear strength, microstructure, pressing pressure II LIST OF TABLES AND FIGURES Figure 1.1: Chemical structure of EPDM 2 Figure 1.2: Image of recycled EPDM rubber under microscopy 3 Figure 1.3: Various copolymer grades visible at the boundary layer of two 8 polymers Figure 1.4: Effect of polar compatibilizer type and compatibilizer loading on 9 Charpy notched impact strength (kJ/m2) of PP/ midsole compounds Figure 1.5: Effect of nonpolar compatibilizer type and compatibilizer loading on 10 Charpy notched impact strength (kJ/m2) of PP/scrap dust compounds Figure 1.6:Reactive groups commonly encountered in reactive compatibilization 14 Figure 1.7: Tensile strength of thermoplastic vulcanizates of 60/40 NR/HDPE 15 blends with various types of blend compatibilizers Figure 1.8: Elongation of thermoplastic vulcanizates of 60/40 NR/HDPE blends 15 with various types of blend compatibilizers Figure 3.1: Standard dumbbell die C for tensile strength test (ASTM-D412-06a) 22 Figure 3.2: Standard die T for tear strength test (ASTM-D 624-91) 22 Figure 4.1: Comparison of tear strength between different non-reactive 25 compatibilizers Figure 4.2: Tensile strength of recycled EPDM rubber/EMA blends 26 compatibilized by EXACT Figure 4.3: Elongation at break of recycled EPDM rubber/EMA blends 26 compatibilized by EXACT Figure 4.4: Young’s Modulus of recycled EPDM rubber/EMA blends 27 compatibilized by EXACT Figure 4.5: Tear strength of recycled EPDM rubber/EMA blends compatibilized 27 by EXACT Figure 4.6: Hardness of recycled EPDM rubber/EMA blends compatibilized by 28 EXACT Figure 4.7 : Stress-elongation relationship of recycled EPDM rubber/EMA 30 blends compatibilized by EXACT Figure 4.8: Effect of talcum on the mechanical properties of 70wt% EPDM 31 rubber + 15wt%EXACT+ 15wt% EMA Figure 4.9: Molecular structure of reactive agents 33 III Figure 4.10: Tensile strength of recycled EPDM rubber/EMA blends 33 compatibilized by reactive agent Figure 4.11: Elongation at break of recycled EPDM rubber/EMA blends 34 compatibilized by reactive agent Figure 4.12: Tear strength
Details
-
File Typepdf
-
Upload Time-
-
Content LanguagesEnglish
-
Upload UserAnonymous/Not logged-in
-
File Pages72 Page
-
File Size-