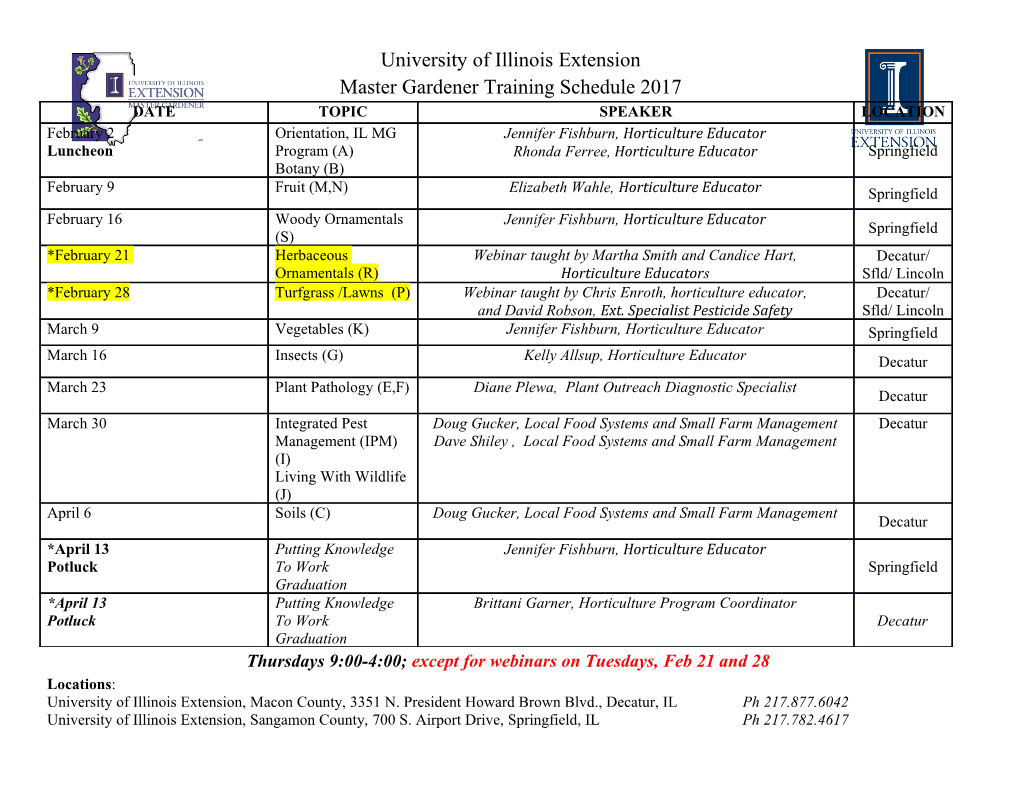
2812_Principles covers.qxd 9/21/07 11:49 AM Page 1 Austin, Texas 2007 NPRA Q&A and Technology Forum: Answer Book Hilton Austin Austin, Texas October 9 – 12, 2007 FCC Reliability and Safety Question 2 Which type of valve technology or design is typically utilized in units with high catalyst withdrawal rates? Do you continuously withdraw catalyst? From a reliability and safety perspective, what type of hardware are you using for control? What is the best withdrawal line design? Ralph Thompson (Chevron Products Company) Valve selection for FCC catalyst withdrawal service is dictated by temperature and erosion considerations. FCC catalyst is very erosive, and when withdrawn from the Regenerator is typically 1200 F+. These considerations, coupled with high velocities when purge and carrier air are injected, lead to very aggressive conditions. We have developed a Best Practice for catalyst handling systems, and the information presented here generally follows those guidelines. We have experience with 4 types of valves in catalyst withdrawal service: Conventional gate valve with and without hard facing Tapco ―Mini Slide‖ Everlasting Rotating Disc valve High performance ball valve Gate valves have generally been poor performers, giving 1-3 year life, even with upgraded trim and coatings. Both the Tapco ―Mini-Slide‖ and the Everlasting Rotating Disc valve have provided good service, lasting multiple runs between replacements. We have limited experience with high performance ball valves in this service. Continuous catalyst withdrawal from the Regenerator has been suggested as a way to even out the swings in level and catalyst activity which occur when batch withdrawal is used. We have no experience with using continuous catalyst withdrawal but have several locations interested in trying it. Locations with PRTs use a form of continuous catalyst withdrawal for third stage separator underflow. For intermittent or semi-batch operation, the valve types described earlier are used for throttling. Block valves are most commonly low-chrome gate valves with hard-faced seats. Temperature monitoring of the withdrawal line is recommended to prevent over-temperature of downstream equipment. Some units have added fins to the withdrawal line to aid in cooling the catalyst. Carrier air also acts as a cooling aid. 1 Catalyst withdrawal lines are subject to leaks due to erosion at wear points. Coatings such as boronizing have been suggested for mitigating erosion but have not been widely applied. Erosion generally occurs at turns. We recommend using cushion tees in place of sweep ells to reduce erosion. Air purging of valves can create localized erosion and should only be used to clear the seat area when opening or closing the valve. We have experienced severe erosion and short life of primary regenerator catalyst withdrawal valves when the purge air has been used continuously. Question 3 Carbonate stress corrosion cracking (CSCC) has been identified as a cause of failure in FCC main fractionator overhead systems. What changes in feed quality, unit operation, or configuration would lead to increased risk of CSCC? What parameters do you monitor to determine whether a system is susceptible to CSCC? While CSCC can be alleviated through post-weld heat treating, has the problem been significant enough to warrant either comprehensive PWHT in potentially affected areas or localized PWHT when problem areas are identified? Ralph Thompson (Chevron Products Company) Carbonate stress corrosion cracking (CSCC) is characterized by intergranular, somewhat branchy, scale-filled cracks. It is believed that ammonium carbonate (NH4CO3) is the main contributor to the cracking mechanism. The scale is typically black magnetite (Fe3O4) corrosion product and sometimes iron carbonate (FeCO3). This is unlike sulfide stress corrosion cracking, where the scale is iron sulfide. Chevron finds that the work reported by Kmetz and Truax* in 1989 still holds true. Very briefly, carbonate SCC (CSCC) is a threat under the following conditions: – Susceptible material: (i.e., non post-weld heat treated or poorly PWHT'd carbon steel) – pH levels above 9.0 and carbonate concentrations above 100 ppm, or – pH levels between 8.0 and 9.0 and carbonate concentrations above 400 ppm – Electrochemical potentials between -500 and -600 mv (SCE) Stainless steels are immune and have been used selectively as an upgrade where CSCC and other corrosion issues were an identified. We primarily monitor the parameters of pH and carbonate levels to determine if we are in the SCC range, especially if we have non-PWHT'd equipment. As a practical matter it is easiest to monitor the pH. If we have a good sense of carbonate ranges with a particular plant feed and process conditions the pH may be the only parameter requiring periodic monitoring as long as it is outside the SCC range. 2 Higher nitrogen levels will lead to higher ammonia levels and could increase the pH into the SCC range. Similarly, anything that promotes CO2 will increase carbonate levels. The move from non-promoted, partial-burn operation to fully-promoted, full-burn operation was a significant contributor to the increased CSCC risk in many units. We recognize that some other companies pay particular attention to the S/N ratio, and while that can be useful we still put the most stock in the direct measurement of pH and carbonate as outlined above. Regarding the use of PWHT as mitigation against CSCC, we are convinced it is very effective if the heat treatment itself is done thoroughly, and there are not unusual externally applied stresses. We found that we needed to beef up our PWHT practices for CSCC, primarily in going somewhat above the Code minimum temperature requirements, ensuring that we had good temperature measurement, and increasing the heating band widths. Our standard practice is to call for PWHT for all new systems, and even for existing systems that may be coming into the CSCC range we seriously consider it on a risk-basis. We try not to wait for leaks to force our hand and (without trying to "jinx" ourselves) in the past ten years we have not had significant CSCC issues. *Reference: Kmetz and D.J. Truax, Carbonate Stress Corrosion Cracking of Carbon Steel in Refinery Main Fractionators Overhead System, NACE Paper #206 CORROSION 90.) Sam Lordo (Nalco Energy Services) The most identified change in operation that may have resulted inn carbonate stress corrosion cracking (CSCC) was the reduction of H2S through FCCU feed hydrotreating and an increase in ammonia from total feed nitrogen. Operational differences such as full or partial burn do not seem to increase CSCC potential. From API 581 and NACE the identified environmental factors that increase the risk of CSCC are: >50 ppm H2S in the liquid water or pH>7.6 Non-stressed relieved carbon steel 2- PH >9.0 and carbonate (CO3 ) >100 ppm, or 2- 8.0<pH<9.0 and CO3 >400 ppm Another parameter that may play a factor is the ratio of total feed sulfur to total nitrogen (S/N) on a ppm basis. It has been reported that cracking occurred in units with a S/N ratio of 0.7, while units that had no cracking had a S/N ratio of >6.0. 3 NACE has a task group, TG347, which is generating a document concerning this phenomenon. It is currently under review. The title of the report is ―Review and Survey of Alkaline Carbonate Stress Corrosion Cracking in Refinery Sour Waters‖. Post weld heat treating (PWHT) appears to reduce the potential, however, there were several industry reported cases of PWHT equipment developing CSCC damage. This may be attributed to a low metal surface temperature during the PWHT process. Another effective mitigating approach is the use of specialized filming amine products. Nalco has applied these products in units that have shown to be susceptible to CSCC. Question 4 Does your refinery/company adopt a time-based rather than inspection-based replacement strategy for FCC reactor and regenerator hardware such as feed nozzles, air distributor, cyclones, cyclone support systems, and flue gas expansion joint bellows? If so, what is the planned service life for this equipment? Ralph Thompson (Chevron Products Company) The service life of each component is highly dependant on the application, and varies from unit to unit. As a result, we generally use inspection-based replacement frequency as opposed to time-based. We use results of the unit inspection coupled with run history to predict the need for replacement of key components at the next (or subsequent) turnaround. Unit monitoring is very important, since we want ―no surprises‖. As an example, cyclone erosion predictions are used to forecast wear and identify ―at-risk‖ systems. We have adopted an upgrade strategy for high wear/low reliability components. We generally plan for a minimum of a 5 year turnaround interval when evaluating need for upgrades. We address the root cause of failure to extend service life where possible. We also identify high wear/low reliability components and selectively upgrade them. We have developed Best Practices to address critical components and systems. Our expectations of the typical service life for well-designed/operated/maintained components are as follows: Feed nozzles: 5-10 years Air distributor: 15-20 years Reactor and Regenerator cyclones: 15-20 years Cyclone support systems: 15-20 years Flue gas expansion bellows: 15-20 years 4 Obviously operating conditions and run history have a major bearing on these service lives. In general, we find that frequent shutdowns have a significant adverse affect on service life and, in particular, component life predictability. NPRA 2000 Q&A FCC Operations Question 1 addressed a similar issue and is a suggested reference. Question 5 What is the shortest possible time between oil out and entry for maintenance on large inventory, high capacity FCC units? How is this achieved? Regan Howell (Holly Corporation) Holly has two FCCs, neither of which would be described as large inventory or high capacity.
Details
-
File Typepdf
-
Upload Time-
-
Content LanguagesEnglish
-
Upload UserAnonymous/Not logged-in
-
File Pages131 Page
-
File Size-