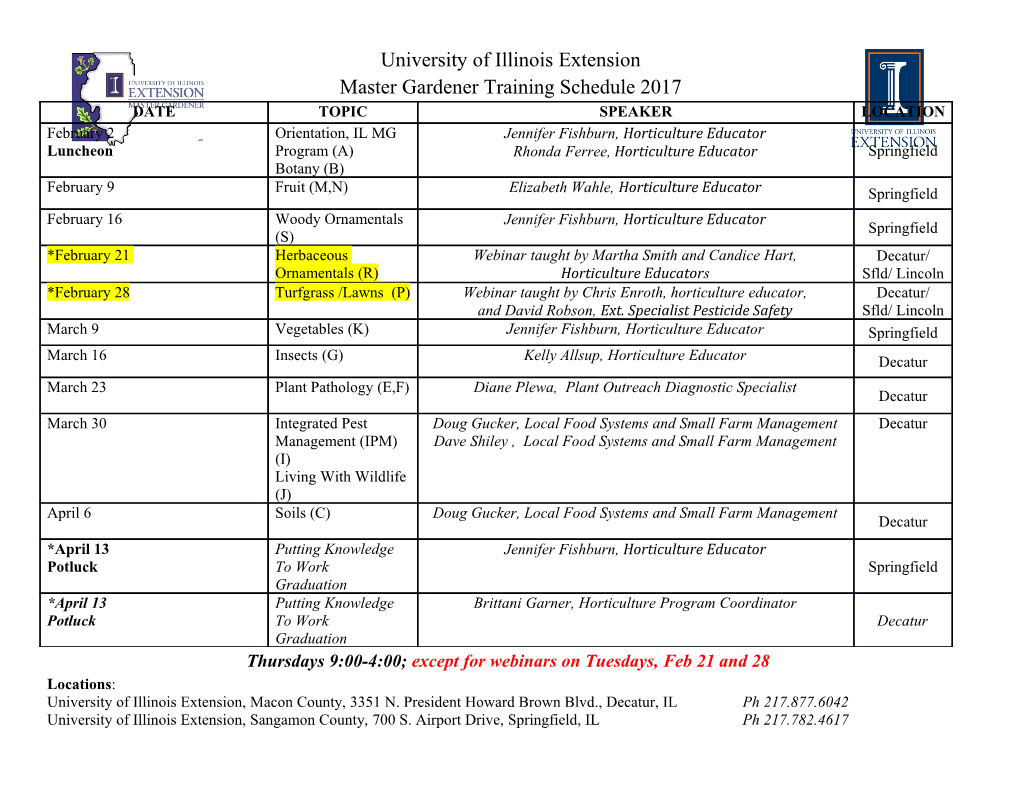
TORSIONAL VIBRATION OF MACHINE SYSTEMS by Ronald L. Eshleman, Ph.D., P.E. Director Vibration Institute Clarendon Hills, Illinois part of a drive train, therefore, excess noise and vibration can Ronald L. Eshleman is director of the . indicate trouble. Vibration Institute and a vibration con­ sultant to industry. His areas of expertise Shaft vibration criteria are usually quantiiedf in terms of include the design and development of motions; i.e., displacement, velocity, or acceleration. Motions machinery and fault diagnosis and cor­ are rarely a concernwith torsional vibration, however, because rection. He has published experimental they do not affectsystem function. Rather, it is the stresses that and analytical work in the fields oftor­ determine the structural integrity and life of components. Tor­ sional vibrations, rotor dynamics, shock sional vibratory motions, unlike shaftwhirling, always produce isolation, and vehicle dynamics. Dr. Esh­ stress reversals, thereby causing fatigue. Components tolerate leman is the technical editor ofthe Shock less reversed stress than steady stress. In addition, stress con­ and Vibration Digest - a monthly jour­ centration factors associated with machined members reduce nal containing abstracts of published articles and reports, re­ the effectiveness of load-bearing materials. Figure l illustrates view articles, and news. He is active in the Acoustical Society of the twisting of a shaft and the torsional mode shape of an elec­ America and the American Society of Mechanical Engineers tric motor-compressor system. A coupling in the power train and serves as chairman of American National Standards Insti­ allows fi>r misalignment in assembly. Note the mode shape ­ tute Committee S2 and as vice chairman of International it shows that the stillness of the coupling is much less than that Standards Organization Committee TC 108. of the other shaft sections. Although the torsional vibration shown in Figure 1 occurs in the form of a single harmonic component, this is not usually the case with real systems. Torsional vibration usually takes the ABSTRACT form of a complex vibration signal having many different fre­ This paper is concerned with torsional vibration in the quency components. Shock from abrupt start-ups and unload­ design, development, and fault diagnosis and correction of ing of gear teeth cause transient torsional vibrations in some machine systems. The physical behavior of torsional vibrations systems, and start-up of synchronous electric motor systems in shafting systems and sources of torsional excitation are re­ can cause torsional resonanee. Random torsional vibration of viewed. The concepts of torsional natural frequencies, critical rotating machines is relatively common due to gear inac­ speeds, resonance, and response (fiJrces, stresses, and motions) curacies and ball bearing defects. Self�exeited vibration- that are explained. The following methods for modeling and cal­ is, the addition of energy to a system by its motion until it culating natural frequencies and responses are described: reaches a limit cycle or destructs - is not common in power lumped and continuous parameter models, the Holzer transmission and generation systems; eleetrical-mechanical in­ method, the modal response method, and direct integration of teraction can bring on this problem. Shear failures in shafts equations of motion. The solution of a transient torsional vibra­ caused by torsional vibration usually occur near a stress con­ tion problem of a synchronous motor drive system is explained. centration point such as a keyway or the point at which the The measurement of torsional vibration in both the field and shaft diameter changes abruptly. Torsional failure is manifest the laboratory is described; monitoring and problem correction by gear wear, gear tooth fatigue, key failure, and shrink fit are emphasized. Systems subjected to torsional vibrations are slippage. Noise that occurs when gear teeth unload indicates a used to illustrate measuring techniques. severe torsional vibration problem. Allowable levels of torsional vibration have not yet been established for general machine systems because so many var­ INTRODUCTION iables are involved. Allowable torsional vibration levels depend All rotating machinery undergoes some form of torsional on the amount of steady torque being carried by the power vibration. In some cases the vibration cannot be detected with­ transmission component. Torsional motions such as shaft de­ out special measuring equipment - even when the level is flections per se are not restricted by function; stresses must close to destructive amplitude. Many aspects of torsional vibra­ thus be calculated and a complete failure analysis conducted. tion are analogous to shaft vibration after the. twisting stiffness Tolerable motions in most systems are dependent upon the and polar moment of inertia have been subs�ituted for the shaft stiffness and relative twist across the component: one degree of bending stiffness and diametral moment of inertia, respec­ torsional vibration amplitude is usually unsatisfactory, but typ­ tively. Torsional vibration can be sensed by noise level and ically an order of magnitude less is satisfactory. Torsional vibra­ vibration (perceptible to touch) when something mediates in­ tion levels usually cannot be controlled and reduced by de­ teraction of the vibration with the ground or gear teeth or creasing the source excitation because it is typically induced by coupling jaws unload. Gear sets that are used to alter speeds of the machine function. Exceptions include gear tooth inac­ power transmission systems allow the interaction of torsional curacies and engine balancing (gas and inertia forces). Damp­ vibration with the ground; slider crank mechanisms in engines ing devices can be used to dissipate energy; however, tuning and compressors provide the path to the ground in reciprocat­ by stiffness and inertia rearrangement in the system seems to ing machines. If gear boxes and/or reciprocating machines are be the best method for reducing torsional vibration. 13 14 PROCEEDINGS OF THE SIXTH TURBOMACHINERY SYMPOSIUM This paper is an overview of torsional vibration technology and includes engineering guidelines for applying the technol­ ogy to solving problems. The physical nature of torsional vibra­ tion is described, as well as methods for calculation and mea­ surerpent, techniques for measurement and analysis, fault diagnosis and correction, and important design considerations. Practical cases involving electric motors, engines, and com­ pressors are reviewed. PHYSICAL ASPECTS Physically, torsional vibration is similar to lateral vibra­ I I tion, after shaft twist has been substituted for shaft bending. !1PUMP OR COMPRESSOR Torsional excitations and stress and motion mechanisms, in­ cluding critical speeds, simple and complex harmonic motions, MODEL transient and self-excited motions are described in this section. Torsional Excitations Table l shows some sources of torsional vibration excita­ tion. It should be noted that most of these sources are related MODE SHAPE to the work done by the machine and thus cannot be removed or reduced. Certain construction and installation sources - Figure 1. Torsional Vibration of an Electric Motor -Com­ gear runout, coupling unbalance, coupling misalignment, and pressor Unit. gear tooth machining errors -can be reduced. Fan or impel­ ler passing excitations can be characterized by the number of TABLE 1. SOURCES OF TORSIONAL VIBRATION EXCITATION Source Amplitude Frequency %Average Torque Mechanical Gear Runout l X, 3 X RPM Gear Tooth Machining Tolerances No. of Gear Teeth X RPM Coupling Unbalance I x RPM !Hooke's Joint 2 X, 4 X, 6 X RPM Coupling Misalignment No. of drive elements x RPM System Function Synchronous Motor Sta1t-up 2 X slip frequency Surge Depends on Surge Rate Eccenhicity of Impeller Scrolls Blade Passing 20-40 No. Blades X RPM Motor Air Gap Eccentricity Engine Firing Rate - Depends on Engine Design and Operating Conditions Pumps 10-40 No. Vanes X RPM Compressors with Vaned Diffusers 3-10 No. Vanes x RPM Motor or Turbine Driven Systems 5-10 No. of Poles or Blades x RPM Engine Geared Systems with 15-30 Depends on Engine Soft Couplings Design and Operating Conditions (can be %n and n X RPM) Engine Geared Systems with 50 or Depends on Engine StiffCoupling greater Design and Operating Conditions TORSIONAL VIBRATION OF MACHINE SYSTE.MS 15 blades or vanes on the wheel: the frequency of excitation 3rdNATURAL equals the number of blades times shaft speed. The amplitude FREQUENCY of pulsating torque is often given in terms of percentage of average torque generated in the systems. In more complex 2nd NATURAL cases, engines, for example, the multiple frequency compo­ FREQUENCY nents depend on engine design and power output. The rela­ tionship behveen gas harmonics and inertia torque harmonics � has a bearing on the level of torsional excitation. Pressure un­ u --------- -_,P balance excitation is a function of inlet pressure sources and z 1st NATURAL w extent of casing distortion. The harmonics of torsional excita­ :::> FREQUENCY 0 tion from surge (a shock condition) arc dependent on higher w a: than normal pressure for a short time and rate of pressure LL increase and decrease. z Q 1- <t a: Torsional Response Q) The components of a typical rotating machine are con­ > nected either directly by couplings and shafts or indirectly by gears, belts, and/or other speed-changing devices. When sub­ CRITICAL jected to excitation
Details
-
File Typepdf
-
Upload Time-
-
Content LanguagesEnglish
-
Upload UserAnonymous/Not logged-in
-
File Pages10 Page
-
File Size-