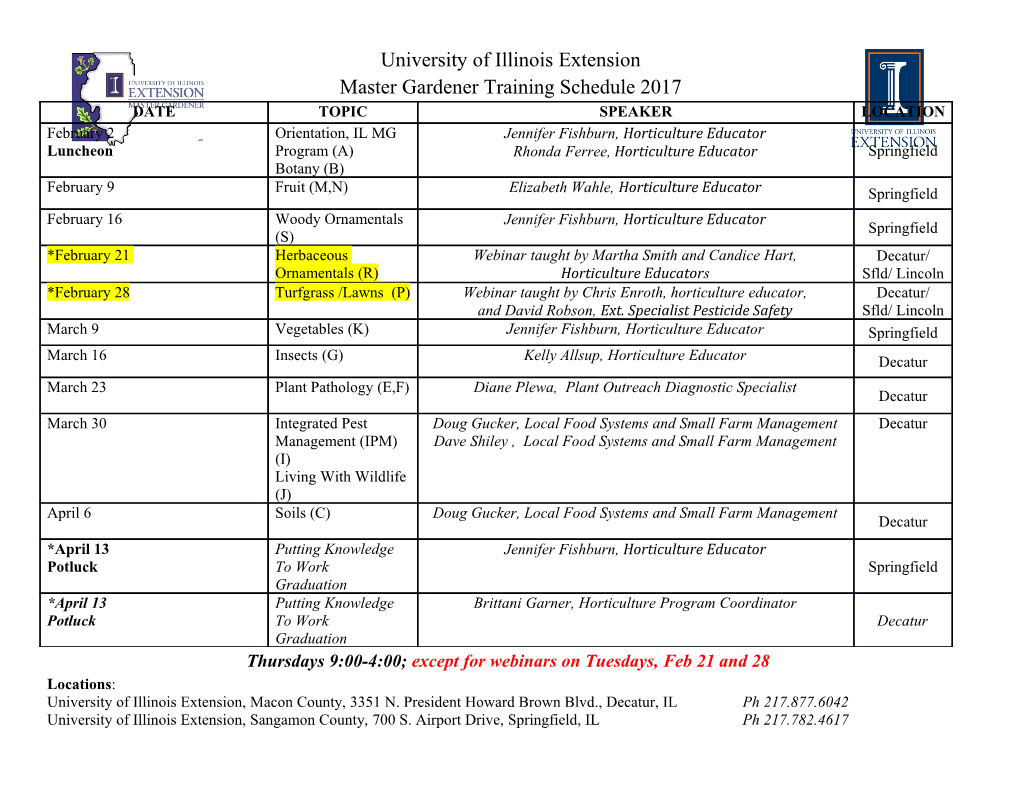
Review Use of Dynamic Mechanical Analysis (DMA) for Characterizing Interfacial Interactions in Filled Polymers Muhammad Ahsan Bashir Jotun AS, Hystadveien 167, 3209 Sandefjord, Norway; [email protected] Abstract: Dynamic mechanical analysis (DMA) provides reliable information about the viscoelastic behavior of neat and filled polymers. The properties of filled polymers are relevant to different indus- tries as protective organic coatings, composites etc. Interfacial interactions in filled polymers play an important role in determining their bulk properties and performance during service life. In this brief review article, studies that used DMA to characterize the interfacial interactions in filled polymers have been reviewed. The available open literature provides a mixed opinion about the influence of interfacial interactions on the glass transition temperature of filled polymers. Nevertheless, it appears that in the case of strong interfacial interactions between the filler particles and the polymeric matrix, the peak value of tan δ is reduced in comparison to that of a filled polymer where these interactions are weak. Keywords: DMA; glass transition temperature; organic coatings; interfacial interactions; interphase 1. Introduction Interfaces play an important role in determining the bulk properties and performance Citation: Bashir, M.A. Use of during the service life of filled polymers. Filled polymers generally refer to polymers Dynamic Mechanical Analysis (DMA) blended with different particles, which are commonly called fillers. Certain additives are for Characterizing Interfacial also used in filled polymers to improve their properties. Organic coatings are a special case Interactions in Filled Polymers. Solids of filled polymers. As commercial organic coatings are composed of binders, co-binders, 2021, 2, 108–120. https://doi.org/ dispersing agents, defoaming agents, extenders/fillers, pigments, solvents, co-solvents, 10.3390/solids2010006 curing agents etc., the interface(s) between different constituents of an organic coating influences the uniform dispersion of each ingredient, which then translates into good Academic Editor: Joaquim Carneiro film formation and isotropic properties of the final coating. In a broader sense, all other components of a commercial coating are liquid (or get dissolved into the solvent(s)) except Received: 28 December 2020 the extenders/fillers/pigments. After application and curing, the extenders are consid- Accepted: 23 February 2021 Published: 1 March 2021 ered as the dispersed phase, whereas the binder (including cross-linked curing agent, residual solvents, additives such as dispersing agents, defoamers etc.) is considered as Publisher’s Note: MDPI stays neutral the matrix. A variety of extenders are used in the organic coatings commercially e.g., inor- with regard to jurisdictional claims in ganic particles (such as titanium dioxide, silica, talc, feldspar, calcium carbonate, kaolin etc.), published maps and institutional affil- metallic particles (such as zinc, zinc oxide etc.), carbonaceous materials (carbon black, etc.). iations. Nanoparticles (non-functionalized or functionalized) of various materials such as silica, carbon (graphene, graphene oxide, reduced graphene oxide, carbon nanotubes etc.), Fe, Zn, etc. are being heavily investigated for the enhancement of various properties (e.g., hy- drophobicity, anti-corrosivity etc.) of organic coatings, but their commercial application is limited mainly due to the dispersion and high cost-related issues [1–3]. An interface is Copyright: © 2021 by the author. Licensee MDPI, Basel, Switzerland. formed between the matrix and the surface of solid extender particles. It is believed that This article is an open access article the interfacial interactions (in the interphase region) between the matrix and the exten- distributed under the terms and der(s) play a major role in deciding the performance of an organic coating (or a composite) conditions of the Creative Commons during service. The interphase region is supposed to consist of two nanolayers, as shown Attribution (CC BY) license (https:// schematically in Figure1. The first nanolayer (around 1–20 Å from the surface of the creativecommons.org/licenses/by/ nanoparticle) contains polymer chains that are highly immobile due to strong attachment 4.0/). with the surface of the particles. The second nanolayer is thicker than the first one, which Solids 2021, 2, 108–120. https://doi.org/10.3390/solids2010006 https://www.mdpi.com/journal/solids Solids 2021, 1, FOR PEER REVIEW 2 consist of two nanolayers, as shown schematically in Figure 1. The first nanolayer Solids 2021, 2 (around 1–20 Å from the surface of the nanoparticle) contains polymer chains that are109 highly immobile due to strong attachment with the surface of the particles. The second nanolayer is thicker than the first one, which is formed around 25–90 Å away from the surface of the particles and contains polymer chains that are considered to be loosely is formed around 25–90 Å away from the surface of the particles and contains polymer boundchains to that the are nanoparticles. considered to Th bee looselythickness bound of the to interphase the nanoparticles. region depends The thickness upon ofpoly- the mer/matrixinterphase regiontype, dependssurface chemistry upon polymer/matrix of the extenders, type, surfacevolume chemistryfraction of of the the extenders,extenders used,volume particle fraction size of (and the distribution) extenders used, of the particle extenders size, (andand the distribution) quality of ofdispersion the extenders, of ex- tendersand the inside quality the of matrix dispersion [4–8] of. Properties extenders of inside the inte therphase matrix region [4–8]. are Properties known to of be the dif- in- ferentterphase from region the bulk are known of the topolymer. be different For example, from the bulka diffusion of the polymer.coefficient For of example,50 Å thick a filmdiffusion of polystyrene coefficient deposited of 50 Å thick on filmsilicon of polystyrenewafers was depositedfound to be on 1 silicon–2 orders wafers of magnitude was found lessto be than 1–2 ordersthat of of magnitudethe bulk polymer less than that[9]. ofThe the g bulklass polymertransition [9 ].temperature The glass transition (Tg) of Å poly(propylenetemperature (Tg )glycol) of poly(propylene confined in glycol) controlled confined pores in controlledof 100 poreswas found of 100 to Å wasbe higher found thanto be that higher of the than bulk that polymer of the bulk [10] polymer. [10]. FFigureigure 1. SchematicSchematic representation representation of inner and outer nanolayer formed in nanocomposites. Once closer to the surface of the (micrometer and/or nanometer) extender particles, Once closer to the surface of the (micrometer and/or nanometer) extender particles, the polymer chains can be tied strongly to the surface via a series of interactions devel- the polymer chains can be tied strongly to the surface via a series of interactions devel- oped via dangling tails, loops and adsorbed segments slowing down and broadening the oped via dangling tails, loops and adsorbed segments slowing down and broadening the segmental relaxation process. Segmental relaxations are related to the glass transition segmental relaxation process. Segmental relaxations are related to the glass transition temperature (Tg), which defines the flexibility of an organic coating (or composite) [11]. temperature (Tg), which defines the flexibility of an organic coating (or composite) [11]. Typically, the change (i.e., increase or decrease) in Tg of the filled polymers is attributed to Typically, the change (i.e., increase or decrease) in Tg of the filled polymers is attributed the nature of interactions (i.e., attractive, repulsive, or neutral) between the polymer and tothe the extender nature particles.of interaction Fors example, (i.e., attractive, attractive repulsive interactions, or neutral) (i.e., the between hydrogen the bonding)polymer andbetween the extender the hydroxyl particles groups. For example, of hydrophilic attractive silica interactions and carbonyl (i.e., groups the hydrogen of poly(vinyl bond- ing) between the hydroxyl groups of hydrophilic silica and carbonyl groups of acetate) have been shown to influence the Tg of the nanocomposite [5]. Similarly, covalent poly(vinyl acetate) have been shown to influence the Tg of the nanocomposite [5]. Simi- bonding between the filler surface and the resin has been shown to increase the Tg of the larly,composite covalent with bonding increasing between filler volumethe filler fraction surface inand the the composite resin has [12 been]. Covalent shown to bond in- creaseformation the betweenTg of the the composite particle surface with increasing and the polymer filler volume matrix can fraction be achieved in the bycomposite different [1ways2]. Covalent e.g., by the bond surface formation treatment between of the the extender particle particles surface with and a the polymer-reactive polymer matrix group, can bethe achieved addition by of chemicalsdifferent ways such ase.g., silanes by the to thesurface filled treatment system that of arethe capableextender of particle reactings withboth a with polymer the polymer-reactive and group the, extenderthe addition particles, of che ormicals by grafting such as the silanes polymer to the chains filled withsys- temfunctional that are groups, capable which of reacting can react both with with the the functional polymer and groups the presentextender on particles the surface,
Details
-
File Typepdf
-
Upload Time-
-
Content LanguagesEnglish
-
Upload UserAnonymous/Not logged-in
-
File Pages13 Page
-
File Size-