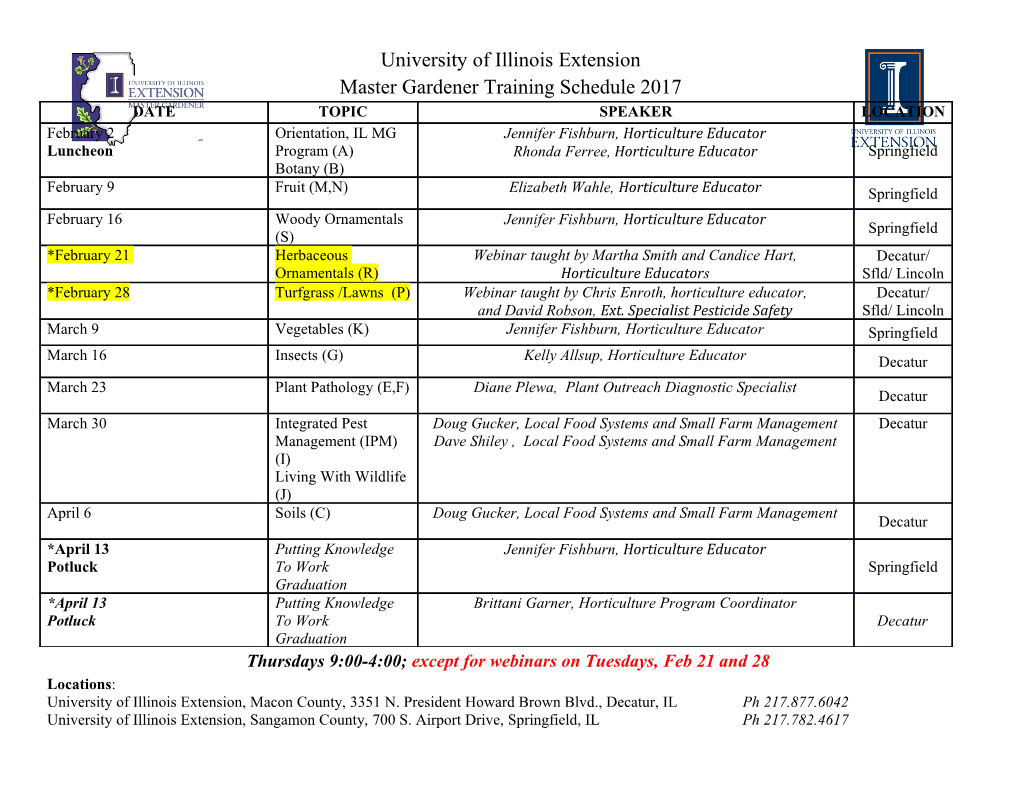
OPTIMAL DESIGN AND COMPARATIVE ANALYSIS OF MULTI-PHASE PERMANENT MAGNET ASSISTED SYNCHRONOUS RELUCTANCE MACHINES A Thesis Presented to The Graduate Faculty of University of Akron In Partial Fulfillment of the Requirement of the Degree Master of Science Sai Sudheer Reddy Bonthu August, 2015 OPTIMAL DESIGN AND COMPARATIVE ANALYSIS OF MULTI-PHASE PERMANENT MAGNET-ASSISTED SYNCHRONOUS RELUCTANCE MACHINES Sai Sudheer Reddy Bonthu Thesis _____________________________ __________________________ Advisor Dean of the College Dr. Seungdeog Choi Dr. Rex D. Ramsier _____________________________ _____________________________ Committee Member Interim Dean of the Graduate School Dr. Malik Elbuluk Dr. Chand Midha _____________________________ _____________________________ Committee Member Date Dr. S.I. Hariharan ____________________________ Department Chair Dr. Brain L. Davis ii ABSTRACT Optimal Design and Comparative Analysis of Multi-Phase Permanent Magnet Assisted Synchronous Reluctance Machines (August 2015) Sai Sudheer Reddy Bonthu Chair of Advisory Committee: Dr. Seungdeog Choi PMa-SynRMs are similar to interior permanent magnet (IPM) motors in structure but are more economical due to reduced permanent magnets. This thesis presents an optimal design of five-phase permanent magnet assisted synchronous reluctance motor (PMa-SynRM) for low torque ripple applications and its comparison with a three-phase PMa-SynRM. The research on the five-phase PMa-SynRM has been expanded to develop a 15kW integrated starter generator (ISG). In this study, the design of five-phase permanent magnet assisted synchronous reluctance motor (PMa-SynRM) for low torque ripple. PMa-SynRMs are similar to interior permanent magnet (IPM) motors in structure but are more economical due to reduced permanent magnets. In this study, lumped parameter model (LPM) is used in the approach to initially design the five-phase PMa-SynRM. Numerical equations are integrated with the LPM to design the machine with its given range of design parameter values. Thousands of designs are generated by LPM, which are then converged to iii optimized model using differential evolution strategy (DES). Optimization is done with maximum efficiency and minimum torque ripple as objective. The optimized 3 kW five- phase PMa-SynRM is then analyzed by finite element method (FEM) for fine tuning. Simulation results for back electromotive force (EMF), flux linkage, developed torque, torque ripple, cogging torque, torque speed characteristics and necessary motor parameters such as d and q-axis inductances variation over respective axis currents are verified by fabricated prototype. In addition, comparison of three-phase and five-phase permanent magnet assisted synchronous reluctance motors (PMa-SynRM) in terms of their design and performance characteristics is presented. With higher fault tolerant capability, efficiency, and reliability, the five-phase PMa-SynRM can be a better substitute when compared to the three-phase PMa-SynRM in critical applications where safety is top priority. In this study, for a fair comparison, same design procedure using LPM is followed in developing the three-phase and five-phase PMa-SynRMs. Performance characteristics such as torque pulsation, back-EMF, flux linkage, etc. are intensively simulated through FEM. The optimized three-phase and five-phase PMa-SynRMs are fabricated with the same power rating (3kW) and same volume. Experimental tests are conducted on the prototypes to validate the simulation results. A 15kW five-phase PMa-SynRM integrated starter generator (ISG) has been proposed in this study. Initial model in LPM and procedure to be followed to develop the final optimized model with DES optimizer has been presented. iv DEDICATION To my parents Mr. Raghu Rami Reddy Bonthu Mrs. Rama Devi Bonthu v ACKNOWLEDGEMENTS I would like to express my deepest gratitude to my advisor Dr. Seungdeog Choi for his encouragement, support and advice during the course of my graduate studies. It would not have been possible to work on my research and write the thesis without his help and support. I would like to sincerely thank my committee members, Dr. Malik Elbuluk and Dr. Hariharan for their support, guidance and motivation. Thanks to Dr. Jeihoon Baek, Korean Railroad Research Institute, and Dr. Sangshin Kwak, Chung-Ang University, for collaborating with me in this project. I would also like to thank my colleagues in Advanced Energy Conversion Lab (AECL) Dr. Kibong Jang, Han Yang University, A.K.M Arafat and Elham Pazouki for their help and support. I would like to thank Mrs. Gay Boden, Department of Electrical and Computer Engineering and Department of College of Engineering for supporting throughout my graduate studies. I would like to thank Mr. Eric Rinaldo for his help in designing the setup for the experimental testing in this project. Last but not least, I would like to thank my parents for their encouragement and eternal love towards me. My family, friends, Drishti-Indian Student Association and Akron Cricket Club has the greatest ability to motivate me and help me throughout my graduate studies. I cordially thank all of them. vii TABLE OF CONTENTS Page LIST OF FIGURES...................................................................................................... viii LIST OF TABLES........................................................................................................ xi CHAPTER I. INTRODUCTION................................................................................. 1 1.1 Introduction....................................................................................... 1 1.2 Evolution of PMa-SynRM................................................................ 2 1.3 Research Objectives.......................................................................... 4 1.4 Thesis Outline................................................................................... 5 II. MODELING AND OPTIMAL DESIGN OF FIVE-PHASE PMA- SYNRM.................................................................................................. 8 2.1 Introduction....................................................................................... 8 2.2 Mathematical modeling.................................................................... 8 2.3 Machine modeling using LPM......................................................... 10 2.4 Machine modeling using FEA.......................................................... 13 2.5 Optimization using DES................................................................... 14 2.6 Simulation results............................................................................. 16 2.7 Conclusions....................................................................................... 23 vii III. DESIGN OF THREE-PHASE PMA-SYNRM...................................... 25 3.1 Introduction....................................................................................... 25 3.2 Overview of Previous Research........................................................ 25 3.3 FEA and LPM models for Three-Phase PMa-SynRM..................... 27 3.4 Conclusions....................................................................................... 28 IV. COMPARISON OF THREE-PHASE AND FIVE-PHASE PMA- SYNRMS................................................................................................ 29 4.1 Introduction....................................................................................... 29 4.2 Modeling of Three-Phase and Five-Phase PMa-SynRMs................ 32 4.3 LPM, FEA Modeling and Optimization using DES......................... 33 4.4 Simulation Results............................................................................ 36 4.5 Conclusions....................................................................................... 45 V. EXPERIMENTAL SETUP AND RESULTS........................................ 46 5.1 Introduction....................................................................................... 46 5.2 Design Materials............................................................................... 46 5.3 Dimensions and Ratings................................................................... 49 5.4 Experimental Results for Back-EMF................................................ 49 5.5 Conclusions....................................................................................... 53 VI. RESEARCH EXPANSION TO INTEGRATED- STARTER/GENERATOR APPLICATION.......................................... 54 6.1 Introduction....................................................................................... 54 6.2 Comparison of LPM and FEA modeling.......................................... 55 6.3 Simulation Results............................................................................ 57 ix 6.4 Conclusions....................................................................................... 60 VII. CONCLUSIONS AND FUTURE WORK............................................ 61 7.1 Conclusions....................................................................................... 61 7.2 Future Work...................................................................................... 63 REFERENCES.................................................................................................... 64 ix LIST OF FIGURES Figure Page 1 IPM, SynRM and PMa-SynRM rotor structures..................................................... 3 2 Phasor diagram of PMa-SynRM.............................................................................
Details
-
File Typepdf
-
Upload Time-
-
Content LanguagesEnglish
-
Upload UserAnonymous/Not logged-in
-
File Pages79 Page
-
File Size-