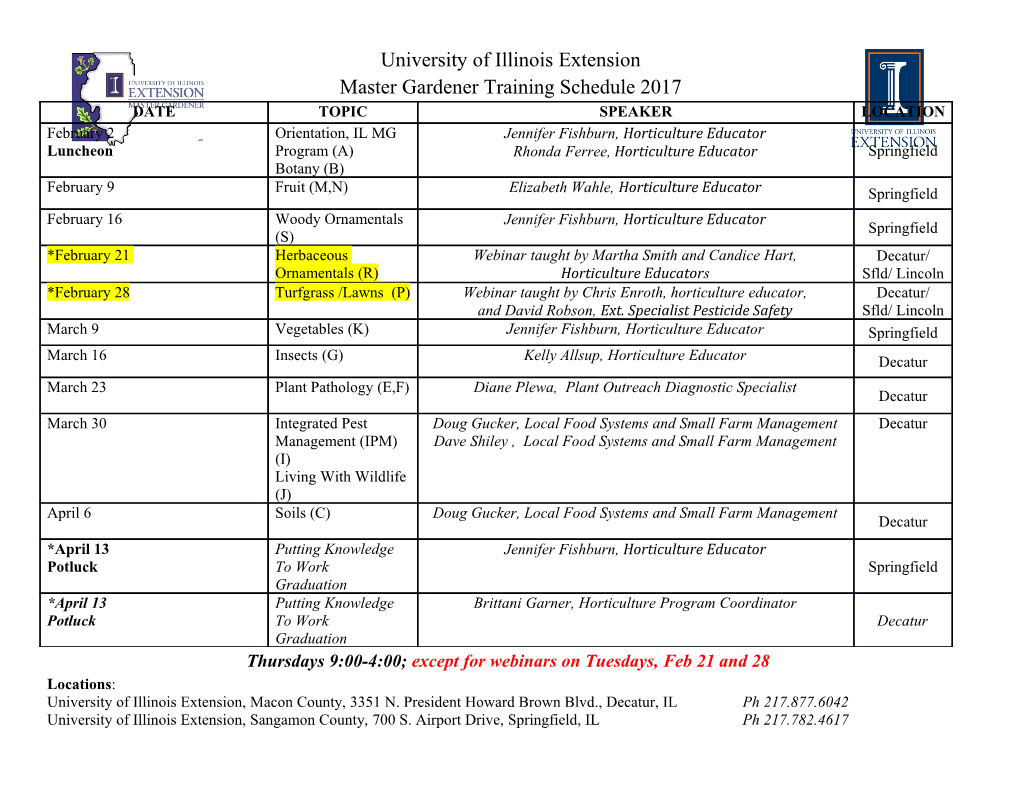
ICAS 2000 CONGRESS AN EXPERIMENTAL STUDY ON WINGTIP DEVICES FOR AGRICULTURAL AIRCRAFT Rogério F. F. Coimbra§ and Fernando M. Catalano* Aircraft´s Laboratory, University of São Paulo, São Carlos, BRAZIL Abstract CLmax maximum lift coefficient dCL/dα wing lift curve slope The induced drag is responsible for nearly 50% (dCL/dα)∞ wing profile lift curve slope of aircraft total drag and can be reduced Di induced drag through modifications to the wing tip. Some e Oswald efficiency factor models displace wingtips vortices outwards L lift diminishing the induced drag. Concerning L/b wing span loading agricultural airplanes, wing tip vortex position L/D aerodynamic efficiency is really important, while spreading products (L/D)b basic wing aerodynamic over a plantation. In this work, wind tunnel tests efficiency were made in order to study the influence in M b wing configuration root bending aerodynamic characteristics and vortex moment position, over Brazilian agricultural aircraft, by Mb b basic wing root bending moment the following types of wing tips: delta tip, α wing angle of attack or incidence winglet and down curved. The down curved tip ∆Ef wing configuration aerodynamic was better for total drag reduction, but not good efficiency factor, referring to vortex position. The delta tip gave ∆Ef = (L/D)/(L/D) b moderate improvement on aerodynamic ∆M wing configuration root bending characteristic and on vortex position. The b moment factor, ∆M = M /M winglet had a better vortex position and lift b b b b ϕ lift curve slope ratio, increment, but caused an undesirable result ϕ α α referring to the wing root bending moment. = (dCL/d )∞ /(dCL/d ) However, winglet showed better development potential for agricultural aircraft. 1 Introduction Nomenclature With the increasing need for fuel economy, all possible areas of drag reduction need to be ASEF aerodynamic-structural efficiency investigated. A form which offers considerable promise is the induced drag. Induced drag is factor, ASEF = ∆E / ∆M f b associated with the shedding of vorticity along AR wing aspect ratio the span of a finite lifting wing and, in b wing span particular, in the wingtip region. For most b wing tip span T subsonic airplane configurations, induced drag c wing chord contributes nearly 50% of the total drag in C drag coefficient D optimum cruising flight and contributes much C minimum drag coefficient Dmin more than 50% of the total drag in climbing CL lift coefficient § Doctorate Student, University of São Paulo * Ph.D. Professor, University of São Paulo 771.1 Rogério F. F. Coimbra and Fernando M. Catalano flight. Consequently, a strong interest has structural characteristics and vortex position, always existed in the effects of wing planform over Brazilian agricultural aircraft, by the and wingtip shape on induced drag, because any following types of wing tips: delta tip, winglet reduction on the induced drag would directly and down curved. The results and discussion are reduce the operating costs of existing aircraft. presented below. It is well know that induced drag Di is a function of the square of the span loading: Di ∝ (L / b)². The level of the induced drag can be 2 Experimental Apparatus and Procedure decreased by increasing the wing span b for constant lift L. When the wing span is The tests were made at Aircraft's Laboratory in constrained, induced drag reduction can be University of São Paulo, during spring of 1996, achieved by improving the aerodynamic in an open circuit wind tunnel which has efficiency of the wing, which would allow an hexagonal test section with a cross section area aircraft to have lower wing areas and weight. of 0,526 m² and 1,63 m length. The wing profile Past researches efforts have resulted in several used was a NACA 23015 with drooping leading successful aerodynamic concepts, including edge, which increases the maximum lift of endplates [1,2], winglets [3], tip-sails [4,5] and original airfoil. The wing model has rectangular vortex diffusers [6]. The potential gains from planform, without end caps, and it has 0,138m some of these devices are limited by the wing- chord, 0,389m half span and no geometric twist. root-bending-moment and wetted-area The aspect ratio (AR) of the basic wing was considerations. 5,63. The wing tips tested were 'delta tip', In generating lift the wing of an aircraft 'winglet' and 'down curved tip'. The delta tip was causes the airflow near each wingtip to swirl selected because of its good results shown round the tip from lower to upper surface. This recently [7], and for its structural simplicity. The swirling motion increase is directly proportional winglet was chosen to be tested because of its to the increase of the wing lift and varies an successful use in commercial planes. The down inverse relation to the aircraft speed at a given curved tip was chosen to be compared for its use lift and flying height. Thus, a crop spraying in Brazilian agricultural aircraft. Figure 1 shows aircraft, which is generally heavy loaded and has the tested models and Table 1, the geometric to fly relatively slowly, generates a strong characteristics. swirling motion near each wingtip. If the aircraft The winglet, which was canted outward has nozzles near this tips, the spray from them 20°, was tested at 5° incidence angle; and it was will be swept into these swirling flows, and constructed with a GA(W)-2 airfoil section, some of it will be thrown into the air above and from wood, with a total winglet area of 12% of behind the tips, to be blown away from the the wing area. The winglet planform was tapered target area, if there is slight cross wind, causing with 15° sweep angle; its root chord and span serious environmental damage adjacent to the had the same geometric value: 66,6% of wings working area. Even if the spray boom is chord. It should be noted that the winglet test significantly smaller than the wing span, the was exploratory and limited in scope; no attempt smaller droplets from the outer nozzles can be was made to optimize winglet geometry for entrained and thrown upwards. With volatile maximum aerial application benefits. sprays, such as those with a large water content, The delta tip was made from 1mm thick evaporation can occur so quickly, that quite a aluminum plate and had a leading edge sweep large number of the smaller sized droplets angle of 70°. This tip had 0,91% of the wing generated can be affected. If the aircraft flies area and its root chord was corresponding at close to the crop, ground proximity effect 37,7% of the wing chord. The leading edge of materially increases the swirl velocity. In this the delta tip was sharp to enforce flow work, wind tunnel tests were made, in order to separation. study the influence in aerodynamic and 771.2 AN EXPERIMENTAL STUDY ON WINGTIP DEVICES FOR AGRICULTURAL AIRCRAFT Both configurations were positioned near 3.1 Aerodynamic Results of wing trailing edge. Figure 2 presented the lift curves and shows an The down curved tip was made from increase in lift coefficient for all tips styrofoam and had 8,6% of the wing area. configurations compared to the basic wing. The This tip device equipped the second generation lift curve slope, dCL/dα, was increased by 3,9%, of Brazilian agricultural aircraft ( from EMB- 11,1% and 17,3% over the basic wing for the 201A to EMB-202, all called Ipanema ). delta tip, down curved tip and winglet, The aerodynamic forces were measured respectively. The maximum lift coefficient was with a strain gauge balance and your shifted by 8,9% for the winglet and down curved repeatability was estimated at tip; the delta tip shown little effect on CLmax . Figures 3 and 4 show drag curves and CL = ± 0,003 drag polars, respectively. To quantify the CD = ± 0,001 induced drag performance in the most useful lift range, the drag polar may be approximated by: The forces from the tests were corrected for blockage [8]. Tare and interference effects, as CD = CDmin + CL²/( π.AR.e ) (1) well as the tunnel flow angularity, were established using an image system [8]. The Where CDmin is the minimum drag coefficient, balance was not able to measure pitching and e is the Oswald efficiency factor. The first moment. Tests were conducted at a freestream effect in the induced drag is primarily due to lift velocity of ~ 28m/s (equivalent to a Mach and can be thought of as a change in the Oswald number of ~ 0,08 ). The set angle of attack was efficiency factor. The shape of the tip, including varied from 0 to 15 degrees. The wing Reynolds the sharpness of the edge and the trailing edge of number was 2,7 x 105, based on a reference the wing tip are all important in directing the chord length of 138mm. The forces were vortex as far outward as possible, thus nondimensionalized using their respective increasing the span efficiency. The constant e planform area. Boundary-layer transition strip incorporates both vortex and profile drag, which was fixed at 5% of the chord on the upper and are difficult to separate as both vary with CL² . lower surface along the entire wing span. To calculate values of the Oswald efficiency for Smoke visualizations were made to each of the wing tips tested, the relationship verify the wing tip vortex position (because of used was [9]: its importance to aerial crop spraying operations) as well as surface visualizations e = 57,3.( dCL/dα∞ )/[( ϕ - 1 ).π.. AR ] (2) were made to verify the wing's flow.
Details
-
File Typepdf
-
Upload Time-
-
Content LanguagesEnglish
-
Upload UserAnonymous/Not logged-in
-
File Pages9 Page
-
File Size-