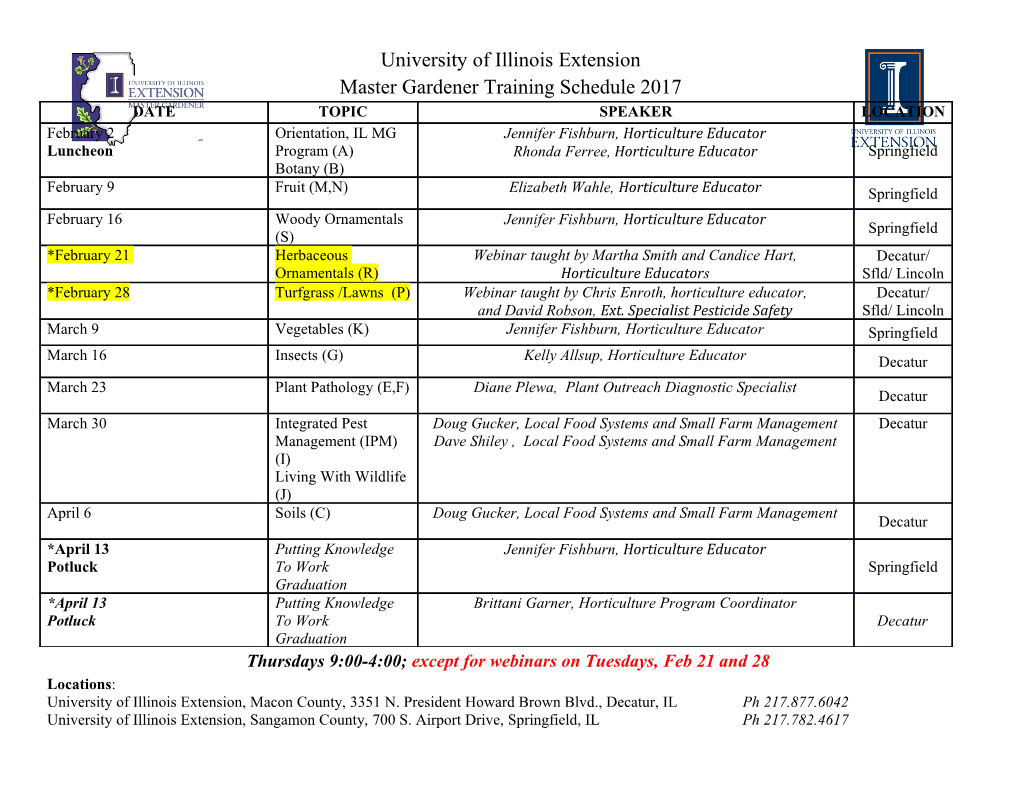
The production, properties, and selection of ferrosilicon powders for heavy-medium separation by B. COLLlNS*. B.Se. Eng. (Rand) (Fellow). T. J. NAPIER-MUNNt. B.Sc. (Eng.). A.R.S.M. (Visitor). and M. SCIARONEt. M.Se. Eng. (Delft) (Visitor). SYNOPSIS There are basically two types of ferrosilicon powder available to operators of heavy-medium plants in South Africa: spherical and milled grades. The production processes are described, and the properties of the two types are examined and compared. Guidelines are given for the selection of the correct grade of ferrosilicon for any particular application. SAMEVATTING Daar is basies twee so::>rte ferrosilikonpoeier beskikbaar vir diegene wat swaarmediumaanlegginge in Suid-Afrika bedryf: steriese en gemaalde grade. Die produksieproses word beskryf en die eienskappe van die twee soorte word ondersoek en vergelyk. Daar word leidrade aangegee vir die keuse van die korrekte graad ferrosilikon vir enige bepaalde gebruik. INTRODUCTION THE PRODUCTION OF of milled ferrosilicon. The following FERROSILICON POWDERS Ferrosilicon of 14 to 16 per cent are the characeristics of this furnace: Shell diameter 6400 mm silicon has become widely accepted At present there are basically Hearth diameter 4000 mm as the most suitable medium for the two types of ferrosilicon available Electrode diameter 890 mm heavy-medium separation of ores in South Africa to the operators of Secondary voltage 90 to 120 v having a specific gravity in the heavy-medium plants. These are Resistance 0,85 m 0 range of approximately 2,5 to 4,0. milled and spherical grades. Ferrosilicon has many properties Reactance 1,0 m o. essential to a metal or alloy powder Milled Ferrosilicon The power consumption (including that is to be usei as a heavy medium, The standard method is to melt steel auxiliaries) for 1 tonne of ferrosilicon some of the more important being scrap, quartz, and a reductant in a (15 per cent silicon) amounts to the following: submerged-arc furnace. The molten 2100 kWh. The furnace is charged (a) resistance to abrasion, alloy is tapped into a sandbed, on a semi-continuous basis and is usually tapped into a ladle every two (b) resistance to corrosion, allowed to cool, and then broken into hours. The temperature of the melt (c) high specific gravity, lumps, after which it is crushed in two stages and milled to the required on tapping is 1600°0. (d) magnetism, which allows easy Slze range. The liquid ferrosilicon from the magnetic recovery with subse- At the Kookfontein Works of ladle is granulated into small part- quent easy demagnetization, Amcor, a 7,5 MVA bubmerged-arc icles in a high-pressure water jet. and f..unace is used for the production This granulation process, developed (e) low cest. Ferrosilicon contain:n~ between TABLE I 14 and 16 per cent silicon is foun:! SPECIFICATIONS FOR MILLED FERROSILICON 14 TO 16 PER CENT SILICON to have the optimum combination Size Analysis of these propertiesl. If the silicon content is lower than 14 per cent, Tyler me3h 48D 65D 1O0D 150D 270D the specific gravity and magnetic + 65 5 0,5 0 0 0 properties are improved, but resist- +100 15 3,0 0,2 0 0 ance to corrosion decreases rapidly. +150 30 8,0 1,2 0,5 0 +200 50 20,0 5,0 2,0 0,2 Above 16 per cent silicon, the corros- +325 75 55 35 25 10 ion resistance of the alloy is not -325 (typical) 25 45 65 75 90 significantly improved, but the mag- -325 (limits) 20-30 42-49 60-70 70-80 90+ netic properties and specific gravity deteriorate. Chemical and Physical Specification.. Silicon 14-16 % Carbon 1 % max. Sulphur 0,05 % max. Phosphorus 0,10% max. *Hoechst South Africa (pty) Ltd. Rust Index 1,0% max. t De Beers Industrial Diamond Division. Non-magnetics 0,75% max. :j:Metalloys Limited. Specific gravity 6,7-6,95 JOURNAL OF THE SOUTH AFRICAN INSTITUTE OF MINING AND METALLURGY DECEMBER 1974 103 by Iscor, eliminates the breaking and TABLE n crushing stages and is believed to SPECIFICATIONS FOR ATOMIZED FERROSILICON 14 TO 16 PER CENT SILICON have the added advantage of pre- Size Analysis venting segregation in the alloy on cooling. The granulated material Sishen ISCOR Cyclone Cyclone Tyler mesh Coarse Coarse Coarse Fine 60 40 is recovered by spiral classifier and * t dried in a gas- fired rotary dryer. + 65 3 4 3 1 0 0 The final powder is obtained by +100 13 13 11 8 0 0 milling in a ball mill in closed circuit +150 30 31 28 18 2 0 with an air classifier, which is set +200 49 44 40 33 7 2 to yield a product of required size +325 74 67 62 55 27 10 -325 (typical) 26 analysis. 33 38 45 73 90 -325 (limits) 23-30 30,1-35 35,1-40,5 40,6-50 65-75 A list of the grades of milled -400 (typical) 65 85 ferrosilicon available in South Africa, together with their chemical and Cyclone 60: * + 100 mesh 0,02 % max. size specifications, is given in Table I. +200 mesh 12% max. t Cyclone 40: Is not produced at this stage because there is no local demand. Spherical Ferrosilicon Chemical Specification There are two methods for the Normal Grades Special Grades Cyclone Grades Si 14-18% 14-16% 14-16% production of spherical grades of C :tI % 1 0,5 % 1,5 % max. ferrosilicon. S 0,05 % max. 0,05 % max. 0,0.5 % max. P 0,1 0,1 Atomized Ferrosilicon % max. 0,1 % max. % max. A!. 10,8% 0,5% max. 0,5 % max. Knapsack AG, a subsidiary of Ma 0,75% max. 0,75% max. 0,75% max. Cu 0,8% max. 0,5% max. 0,5 % max. Hoechst AG, was the first to apply Cr. 0,5% max. 0,5% max. 0,5 the atomizing process to the product- % max. ion of ferrosilicon for heavy-medium Physical and Physiochemical Specification: separation2. This process is now also Content of spheres: Normal grades : 1 50 % used in the Hymat plant at Amcor's Cyclone and special grades: 190% Magnetic contont : 99%+ Kookfontein works. Pyknometer density : 6,6-7,0 gfcm3 Ferrosilicon of 75 per cent silicon Bulk density : 3,5-4,2 gfcm3 is diluted with high-grade steel scrap in an induction furnace. Character- aI, and size specifications, is given in fine fraction of the final product. istics of this furnace are as follows: Table H. In spheroidizing, the milled Holding capacity 3 tonnes Spheroidized Ferrosilicon powder is allowed to fall through a Electrical capacity 750 kW A second method for the product- flame that has an oxidizing centre Power consumption 600 kWh/t ion of spherical ferrosilicon was and a 'reducing outer zone, which Type Mains frequency. developed by IscorI. Test" have permits each individual particle to By means of a tilting device, the shown that in many respects this be melted without being oxidized. furnace is tapped at approximately material is identical to that pro- The surface tension and fluidity of 3-hourly intervals at a charge tem- duced by the Knapsack method. ferrosilicon are such that each part- perature of approximately 1550 °C. Spheroidized ferrosilicon is pro- icle contracts into a sphere. The The molten material flows into a duced initially in the same induction design of the burner prevents ceramic tundish, which ensures that furnace. However, the stream of agglomeration, and, after spheroid- the alloy stream entering the atom- molten alloy is broken up in a series izing, the powder is quenched in izing steam cone has a constant of concentric cones of high-pressure waste gas to prevent oxidation. diameter and velocity. water. Clearly, the energy available It is claimed that the water- In the atomizing nozzle, the in this system is not as great as in granulated fraction of the final stream of molten ferrosilicon comes steam atomizing, and consequently product is superior to the correspond- into contact at its apex with a cone the water-granulated product is ing fraction of the atomized product, of steam, and the melt is immediately coarser. making it possible to operate at broken into fine particles, which are In fact, only a fraction of this higher pulp densities1. quenched in water. material (about 30 per cent) consti- THE PROPERTIES OF FERRO- The resultant ferrosilicon pulp is tutes the final product. The granu- SILICON 14 TO 16 PER CENT filtered in a drum filter, dried in a lated product is dried and screened SILICON gas dryer, then screened for the at 48 mesh, and the screen oversize removal of oversize material. This (about 70 per cent) is milled to the Premier Mine installed the first. oversize fraction (approximately 3 required size in a ball mill in closed heavy-medium separation plant in to 10 per cent of the atomized circuit with an air classifier. The South Africa in 1948, the complete ferrosilicon) is milled in the ball mill. milled fraction is then spheroidized, specification for the ferrosilicon used A list of the grades of atomized and the two fractions are combined in that plant being 25 per cent minus ferrosilicon available in South Africa, in the desired proportions. The 325 mesh. Since then, considerable together with their chemical, physic- spheroidized powder constitutes the progress has been made both in the 104 DECEMBER 1~74 ,",OURNAL OF THE SOUTH AFRICAN INSTITUTE OF MINING "NO MHALLURGY production and quality control of medium separation itself and in the does affect the performance of a miI1ed ferrosilicon. handling of the medium with regard heavy-medium cyclone, and this Notwithstanding these advances, to pumping and storage.
Details
-
File Typepdf
-
Upload Time-
-
Content LanguagesEnglish
-
Upload UserAnonymous/Not logged-in
-
File Pages17 Page
-
File Size-