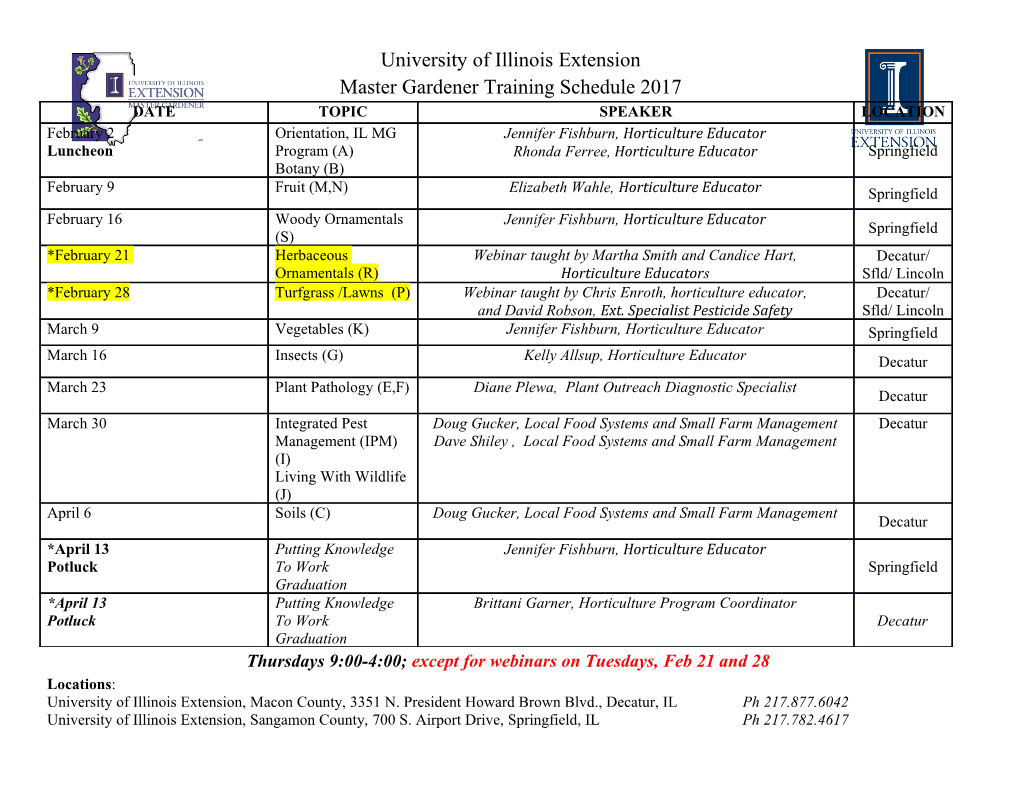
ASM Handbook, Volume 11: Failure Analysis and Prevention Copyright © 1986 ASM International® ASM Handbook Committee, p 563-585 All rights reserved. DOI:10.1361/asmhba0001814 www.asminternational.org Failures of Tools and Dies George F. Vander Voort, Carpenter Technology Corporation FAILURE MECHANISMS in tool and die Tool Steels" in Volume 4 of the 9th Edition examination of the fracture features by materials that are very important to nearly all of Metals Handbook. In addition to controlling opening tight cracks (when present). Because manufacturing processes are discussed in this the heat-treatment process, tool and die design quench cracking is a very common cause of article. A wide variety of tool steel composi­ and steel selection are integral factors in failures, the fracture surfaces should always tions are used. Properties and selection of tool achieving tool and die integrity. be checked for temper color. Scale on steels are described in the Section "Tool a crack wall would indicate that it was ex­ Materials" in Volume 3 of the 9th Edition posed to temperature higher than those used of Metals Handbook; microstructures and Analytical Approach in tempering. metallographic techniques for tool steels are Analysis of tool and die failures is substan­ Visual inspection of the damage done to a detailed in the article "Tool Steels" in Volume tially aided by knowledge of the manufacturing tool and die is usually adequate to classify the 9 of the 9th Edition of Metals Handbook. This and service history of the failed part. In many type of tool and die failure, as illustrated by the article is primarily devoted to failures of tool instances, however, such information is examples in this article. High-magnification steels used in cold-working and hot-working sketchy, and the analyst must rely on experi­ fractographic examination is required in only a applications. ence and engineering judgment. The examples small percentage of the cases. A simple ste- discussed in this article are typical of tool and reomicroscope generally suffices. Microstructural examination at and away Tool and Die die failures and illustrate many of the features specific to such failures. Additional informa­ from the damage and at the origin is imperative. Characteristics tion can be found in the Selected References This generally requires good edge-retention preparation, which is relatively easy for tool Steels used for tools and dies differ from that follow this article. steels. A large percentage of tool and die most other steels in several aspects. First, they A basic approach can be followed for most failures are due to heat-treatment problems, as are used in the manufacture of other products tool and die failures that will maximize the illustrated by the examples in this article; the by a variety of forming processes (stamping, likelihood of obtaining reasons for the failure. shearing, punching, rolling, bending, and so At times, however, no reason for failure can be value of proper metallographic procedures can­ on) and machining processes (drilling, turning, discovered. In such cases, the failures are not be stressed enough. milling, and so on). Second, tools and dies normally attributed to unknown service condi­ Other techniques are also very important. are generally used at higher hardnesses than tions. Hardness testing is used to confirm the quality most other steel products; 58 to 68 HRC is a Before beginning the investigation, a com­ of the heat treatment and often reveals prob­ typical range. Dies for plastic molding or hot plete history of the manufacture and service lems. Macrostructural examination, either by working are usually used at lower hardnesses, life should be compiled. This is often difficult cold etching (more common) or hot etching, is typically from 30 to 55 HRC. to accomplish. Next, the part should be very useful for detecting gross problems. Prior- austenite grain size is frequently evaluated by These high hardness requirements are needed carefully examined, measured, and photo­ the Shepherd fracture grain size technique, a to resist anticipated service stresses and to graphed to document the extent and location of simple but accurate approach. X-ray diffraction provide wear resistance. However, the steels the damage. Relevant design features, as well must also be tough enough to accommodate as some machining problems, are generally can be used to determine the amount of retained service stresses and strains without cracking. apparent after this study. The origin of the austenite present. Premature failure due to cracking must be failure, when due to fracture, will also usually In some cases, it is necessary to perform avoided, or at least minimized, to maintain be determined. Only after careful visual simulations or to conduct experimental heat minimum manufacturing costs. Unexpected examination has been completed should any treatments to determine if a part was tempered. tool and die failure can shut down a manufac­ destructive work be considered. In certain Chemical analysis of millings or turnings from turing line and disrupt production scheduling. cases, various nondestructive examination the surface will define variations in surface- This leads to higher costs. techniques—for example, ultrasonics, x-ray, or carbon content. Electron metallographic de­ vices using either wavelength- or energy- Tools and dies must also be produced with magnetic-particle inspection—should be imple­ dispersive x-ray analysis can be used to identify the proper size and shape after hardening so mented before cutting to obtain a more that excessive finishing work is not required. complete picture of the damage, either internal inclusions or segregates. It is also helpful in Heat-treatment distortion must be controlled, or external. some studies to compare the characteristics of good parts to those of failed parts. and surface chemistries must not be altered. When this work is completed, several other Because of the careful balance that must be phases of the study can begin. First, the com­ When these data are compiled and analyzed, maintained in heat treatment, control of the position of the component should be verified the analyst is ready to prepare a report that heat-treatment process is one of the most by a reliable method. Tool and die failures details the cause of failure with the supporting critical steps in producing successful tools and occasionally result from accidental use of facts. In many such cases, it is also necessary to dies. Heat treating of tool and die steels is the wrong grade of steel. While this work is make recommendations regarding corrective discussed in the Section "Heat Treating of underway, the analyst continues macroscopic action for future parts or for existing parts. 564 / Manufactured Components and Assemblies Causes of Fig. 1 AISI Wl (0.85% C) tool steel Fig. 2(a) Front view of an AISI Ol Tool and Die Failures concrete roughers that failed after tool steel die that cracked during short service (2 min for S, 7 min oil quenching A number of factors are responsible for tool for SI 1) and die failures including: The die face contains holes that are too close to the Failures of these and other concrete roughers all edge for safe quenching. See also Fig. 2(b). 0.6 '■' occurred at the change in section (arrows indicate • Mechanical design: Must be compatible cracks). with the steel grade selected, the procedures required to manufacture the tool or die, and the use of the tool or die • Grade selection: Must be compatible with the design chosen, the manufacturing pro­ cesses used to produce the tool or die, and the intended service conditions and desired life • Steel quality: Must be macrostructurally sound, free of harmful inclusions to the degree required for the application, and free of harmful surface defects • Machining processes: Must not alter the surface microstructure or surface finish and must not produce excessive residual stresses that will promote heat-treatment problems or service failures • Heat-treatment operation: Must produce the desired microstructure, hardness, tough­ ness, and hardenability at the surface and the interior • Grinding and finishing operations: Must not Fig. 2(b) Side view of broken die impair the surface integrity of the compo­ halves showing the mating nent fracture surfaces and temper color • Tool and die setup: Alignment must be (arrow) on the crack surfaces precise to avoid irregular, excessive stresses that will accelerate wear or cause cracking A front view of this component is shown in Fig. 2(a). • Tool and die operation: Overloading must be avoided to ensure achievement of the desired component life The above classification of factors, while helpful in categorizing problems, will not nec­ essarily deduce the cause of a particular failure. For example, a failure due to one of the above factors may have been caused by other prob­ lems earlier in the processing sequence. To illustrate, the majority of cracking problems attributed to abusive grinding practices are caused by failure to temper the part or are due to overaustenitization. Both of these problems will make a tool steel virtually impossible to grind without producing surface burning and cracking regardless of the care taken during grinding. Thus, the above factors are interde­ to obtain compressive yield strength data to aid pendent, much like the links of a chain. If one the designer. However, such tests are quite step is poorly executed, the tool or die will difficult to perform, and few useful data are exhibit limited service life regardless of how available. Consequently, the simple indentation used, but most test specimens either are not carefully all of the other steps are conducted. hardness tests, generally the Rockwell C test or notched or have a C-type notch rather than This sensitivity to processing stems from the the Vickers test, are used to define strength the more common V-notch. Use of the latter use of tools and dies at these very high hardness differences.
Details
-
File Typepdf
-
Upload Time-
-
Content LanguagesEnglish
-
Upload UserAnonymous/Not logged-in
-
File Pages23 Page
-
File Size-