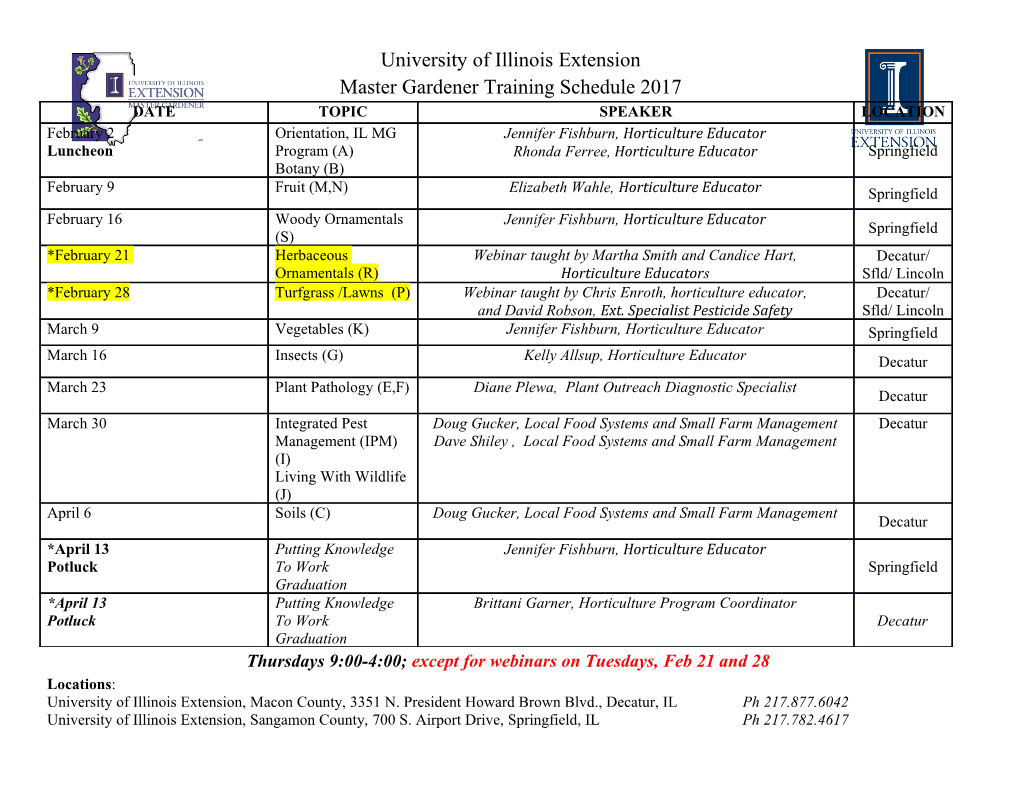
High Temperature Roasting of Sulphide Concentrate and its Effect on the Type of Precipitate Formed. A dissertation submitted to the School of Mines, Faculty of Engineering, Technikon Witwatersrand, Johannesburg, South Africa, for the fulfilment of the degree of MAGISTER TECHNOLOGIAE: EXTRACTION METALLURGY. By Fortunate Magagula Supervisor: Dr. A.F. Mulaba-Bafubiandi Department of Metallurgy, Technikon Witwatersrand, Johannesburg December 2002. Declaration I Fortunate Magagula, hereby declare that this dissertation is my own unaided work. It is being submitted to the Technikon Witwatersrand for the degree MAGISTER TECHNOLOGIAE Extraction Metallurgy. It has not been submitted before by myself or any other person to any institution for any degree or examination. Author's signature Date20421 eiq ii Acknowledgements I sincerely thank my supervisor, Dr Mulaba for his academic guidance and logistical support and for making this study a success. I would also like to thank the Technikon Research Committee for the financial support. I thank the University of the Witwatersrand for allowing me to use their facilities. I am so grateful to my colleagues for their moral support. I would like to extend my gratitude to my husband for loving and motivating me throughout this study. iii Dedication To my husband who made everything possible and bearable. Thank you for your tireless support. iv Abstract The most commonly used route in the hydrometallurgical extraction of zinc and copper is the roast-leach-electrowin process. During the roasting process, the concentrate is subjected to either relatively low temperatures (partial roasting) or high temperatures (to achieve dead roasting) to produce a calcine that will be leacheable to extract zinc and copper. The resulting calcine contains zinc and copper in a form of oxides (ZnO, CuO), sulphates (ZnSO4, CuSO4) and ferrites ((Zn,Cu 1-x, Mx)0Fe203) or Zn,CuFe2O4) in the case of partial roasting. In the case of dead roasting, mostly the oxide forms are produced but in most cases ferrites will form as well. The means of avoiding the ferrites completely have not yet been achieved. Attempts in the past had only been focusing on either partial roasting or dead roasting without actually finding the optimum roasting conditions to minimise the ferrite formation. In this study the main objective was to identify optimised conditions for roasting, i.e. the possibility of producing these ferrites in minimum amounts as compared to the targeted zinc/copper oxides. Optimised roasting conditions were achieved in this study on a Zinc-copper ore from Maranda mine, where the sulphur removal test was used to ensure a dead roasting. This was done by analysing the amount of sulphur remaining after each roasting condition. Characterisation of the calcine has been done using the XRD and the Mossbauer spectroscopy. More zinc oxide than zinc ferrite was obtained at conditions of 800 °C for 3 hours as per the XRD analyses. The sulphur removal test however, showed a dead roasting at 900 °C (2% remaining sulphur) and this is attributed to the inadequate (not designed as in industry) supply of oxygen by the laboratory furnaces used. The precipitation of iron from the three acids (HCI, H2SO4 and HNO3) was done using NH4OH and NaOH. The Mossbauer and XRD characterisation techniques were used, where the XRD characterisation showed different spectra of the precipitate attributing to different compounds. The results of the precipitates from the optimised roasting conditions are those precipitates that are not commonly found in industry. The effect of the acids and the cations showed goethite to be formed from H2SO4 and HNO3, with NH4+ and Na+ respectively. The possibility of the selective leaching of the concentrate has been investigated. This eliminates the roasting process completely and thus provides a possibility of leaving the pyrite (FeS2) in the residue and thus minimising the amount of iron to be handled. Selective leaching has been done using Mn02 and Na2S208 in the presence of H2SO4. It was observed that starting with Mn02 as an oxidising agent does not achieve good selective leaching results between the sphalerite and the chalcopyrite. It was however possible to preferable leach sphalerite over chalcopyrite with the use of Na 2S2O8 as a starting oxidising agent. So the choice of the oxidising agent plays a role in selectively leaching different minerals. The optimised roasting conditions at high temperatures resulted in some type of precipitates, (mohrite, ferrihydrite and akaganeite) that are not commonly formed in industry. Jarosite, which is the most common precipitate formed in industry, could not be precipitated. Goethite was also fcund to be present. vi Table of Contents Declaration ii Acknowledgements iii Dedication iv Abstract Table of Contents vii List of Tables List of Figures xiii List of Abbreviations xvi CHAPTER 1 — INTRODUCTION 17 CHAPTER 2 - LITERATURE REVIEW 20 2.1 Introduction 20 2.2 Iron in Sulphide ores 20 2.3 Roasting of sulphide ores 21 2.3.1 Partial roasting 21 2.3.2 Dead roasting 24 2.4 Leaching 25 2.4.1 Conventional leaching of sulphide ores 25 2.4.2 Selective leaching of sulphide ores 25 2.5 Precipitation 28 2.5.1 Hydrolysis of Iron in Aqueous Media 29 2.5.2 Iron precipitate products 32 2.6 Mossbauer 37 vii Chapter 3 — EXPERIMENTAL 38 3.1 Research Method 38 3.2 Materials 38 3.2.1 Ore and its origin 38 3.3 Reagents and Apparatus 39 3.3.1 Flotation Reagents 39 3.3.2 Leaching Reagents 39 3.3.3 Apparatus 40 3.4 Experimental Procedures 40 3.4.1 Flotation procedures 40 3.4.2 Roasting procedure 40 3.4.3 Sulphur determination 40 3.4.4 X Ray Diffraction (XRD) 42 3.4.5 Mossbauer Effect Spectroscopy (MES) 42 3.4.6 Leaching procedures 43 3.4.7 Selective Leaching procedures 43 Chapter 4—RESULTS AND DISCUSSION 45 4.1 Introduction 45 4.2 Flotation Results 45 4.3 Roasting Results 49 4.3.1 Sulphur removal 49 4.3.2 X-Ray Diffraction (XRD) 52 4.3.3 Mossbauer Results 60 4.4 Leaching Results 74 4.4.1 Neutral leaching 74 4.4.2 HCI Neutral leach 75 4.4.3 H2SO4 Neutral leach 76 4.4.4 HNO3 Neutral leach 77 4.4.5 CONCLUSION 82 4.5 Selective leaching 83 4.5.1 Conclusions 90 viii 4.6 Precipitation results 92 4.6.1 Procedure 92 4.6.2 Results 94 4.6.3 XRD characterisation of precipitates 101 4.6.4 Mossbauer characterisation of precipitates. 102 Chapter 5 — Conclusions 104 5.1 Recommendations 105 References 106 Appendices 111 ix List of Tables Table 2.2.1.1: Comparison of Iron Precipitation Processes 35 Table 3.1.1.1: Mineral and metal abundances in the Run Of Mine. 39 Table 4.2.1: Results showing mass recovery with respect to variation of modifiers types and ratios 46 Table 4.2.2: Table showing zinc and copper recoveries 47 Table 4.3.1.1: Percentage sulphur from varying roasting conditions. 50 Table 4.3.2.1: XRD spectral Intensities of phases at different ... roasting conditions. 57 Table 4.3.3.2: Hyperfine interaction parameters of the components in the concentrate sample. 61 Table 4.3.3.3: Hyperfine interaction parameters components in calcines roasted for 2 hrs at different temperatures . 63 Table 4.3.3-4: Comparison of component abundances (2hrs) ... 65 Table 4.3.3.5: Hyperfine interaction parameters of the components in the calcines, roasted for 4 hrs at different temperatures 67 Table 4.3.3.6: Comparison of component abundances (4 hrs) .. 69 Table 4.3.3.7: Hyperfine interaction parameters of the spectral components in the spectrum of calcines roasted at 800°C for different durations. 70 Table 4.3.3.8: Comparison of component abundances (800 °C). 72 x Table 4.4.1.1: Table showing neutral leaching results 74 Table 4.4 4.1: Percentages of elements remaining after neutral leaching. 81 Table 4.4.4.2: Dissolution of elements during hot acid leaching8l Table 4.4.4.3: Table showing percentages of elements remaining after hot acid leaching. 82 Table 4.5.1: Percentage Extraction in 5M H 2SO4 and 10% (w/v) Mn02 83 Table 4.5.2: Percentage Extraction in 7M H 2SO4 and 10% (w/v) Mn02. 85 Table 4.5.3: Percentage Extraction in 5M H 2SO4 and 20% (w/v) Mn02. 85 Table 4.5.4: Percentage Extraction in 7M H 2SO4 and 20% (w/v) Mn02 85 Table 4.5.5: Percentage Extraction in 5M H 2SO4 and 10% (w/v) Na2S2O8 . 86 Table 4.5.6: Percentage Extraction in 7M H 2SO4 and 10% (w/v) Na2S2O8. 87 Table 4.5.7: Percentage Extraction in 5M H 2SO4 and 20% (w/v) Na2S2O8. 88 Table 4.5.8: Percentage Extraction in 7M H 2SO4 and 20% (w/v) Na2S2O8. 88 Table 4.5.9: Percentage Extraction of residue in 7M H 2SO4 and 20% (w/v) Mn02 89 Table 4.6.1.1: Table summarising the amount of iron (in %) remaining from precipitation at 80 °C and filtration after 24 hours. 94 xi Table 4.6.1.2: Results summarising the amount of iron (in %) remaining from precipitation at 95 °C and filtration after 24 hours 96 Table 4.6.3.1: Hyperfine interaction parameters of the spectral components in the spectrum of samples. 103 Table A: Hyperfine interaction parameters at room temperature of candidate Fe-bearing phases that may occur in the samples 111 Table B: Hyperfine interaction parameters at room temperature of candidate Fe-bearing phases that may occur in the precipitate samples 112 xii List of Figures Figure 2.5.1.1: Schematic representation of the hydrolysis- precipitation process 30 Figure 4.2.1: Effect of conditioning time on mineral recoveries.
Details
-
File Typepdf
-
Upload Time-
-
Content LanguagesEnglish
-
Upload UserAnonymous/Not logged-in
-
File Pages120 Page
-
File Size-