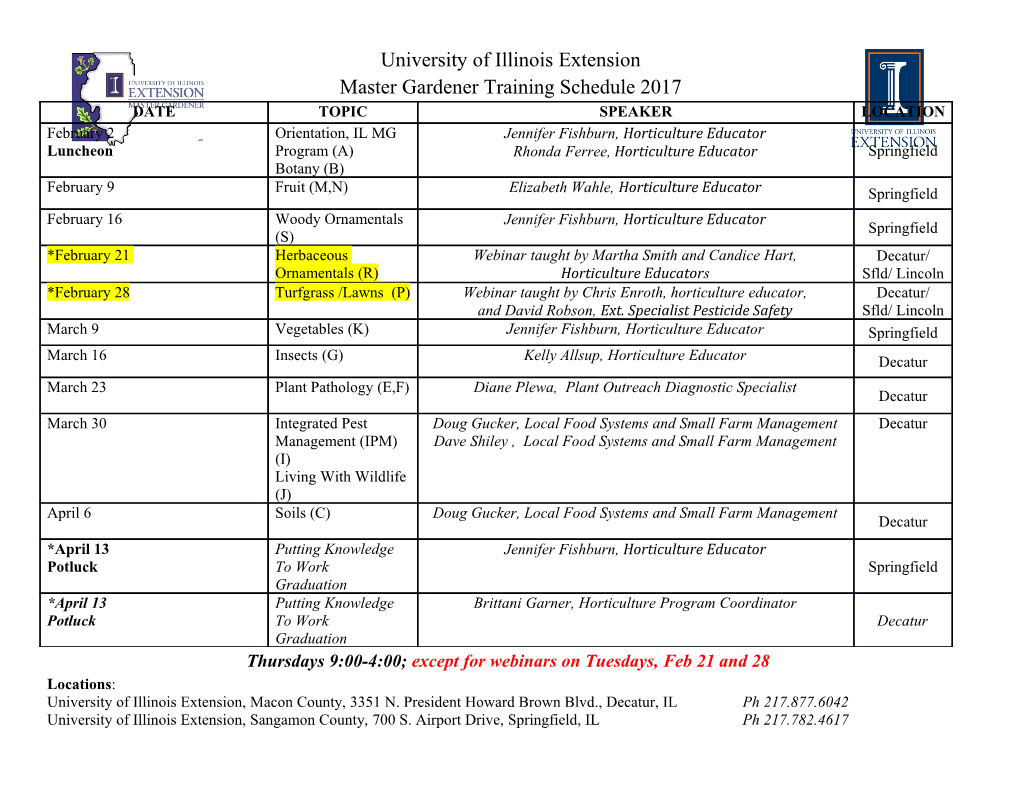
SPINNING PEER REVIEWED The Process Dynamics of Egyptian Cotton G-86 with a Compact Spinning Machine Ibrahim A. Elhawary1* & Mohamed Y. Naeim2 1Alex Univercity, Egypt 2SETT-COR Spin Mill, Egypt Abstract In the present work, Giza 86 cotton (long staple cotton) was used to produce a different fine yarn with counts 14.7, 11.8, 10.5, 9.8, and 7.4tex on both of compact and ring spinning frames. The different yarn properties like, CVm%, tenacity, elongation, and hairiness were measured for both the two type of yarns. The relative yarn quality factor RYQF was calculated to detect the more suitable range of yarn counts for the compact spinning it was found that it ranges from 1.1 to 1.3 for range of yarn tex from 14.7 to 7.4 referring to the hairiness reduction it was found to be 31% for yam tex 9.8 the improvement in the yarn breaking elongation was 10%, the improvement in the yarn tenacity was 14%, while the reduction in the turns per meter in the compact spinning was 4%. And improvement in the yam mass variation was about 5%. On the other hand it was found that the improvement in the single compact yarn total imperfections was not statistically significant, But generally it was found that the yarn total imperfections of the single yarn were less for the compact spun yarns compared with the conventional ring spun yarns especially for the fine counts. 1. Introduction applied onto the yarn. Fibers are caught by the air Compact spinning is a new conversion for the ring current in the perforated drum soon after they leave spinning and it started to be applied in the Egyptian the nip point until they reach the nip point. The air spinning industry in the last few years but it is still not current influences the fibers to pass along the slot and commonly used. Nowadays some of new spinning mills therefore the fibers are condensed by means of the in Egypt started to install more updated compact spin- aerodynamic forces caused by the air current [5]. (See ning machines as Rieter K44 compact spinning. figure -1.1) So studying & evaluating the fine yarn quality pro- There have been numerous studies performed on the duced by the new ring spinning technology of com- different compact spinning systems in order to study pact spinning from Egyptian cotton, within long term and compare the compact yarn characteristics with the period of time (5 years) could be a key for gaining a conventional ring spun yarn, Guldemet Basal [1], competitive advantage over companies in an industry. Chang et al. [2], Cheng et al. [4], Krifa et al. [6,7], With the ever-changing textile industry and many Stalder [10] Momir et al. [9], Nasir [8], Cankut et al. manufacturers moving overseas, the compact spinning [3]. These researches concluded that the Compact yarns technology could lead to the competitive edge the are claimed to be stronger and have better breaking Egyptian spinning industry needs for producing super elongation compared with the conventional ring spun quality fine yarns. yarns, also stated that compact spinning greatly re- duced the hairiness of yarns. Rieter compact spinning principle depends on replac- ing the bottom delivery roller with a perforated drum with larger diameter. Inside the perforated drum, there is a stationary suction insert having a slot in direction of fiber flow so that an extra transverse force could be Association TEXTILE *All the correspondence should be addressed to, Prof. (Dr.) Ibrahim Elhawary, Faculty of Eng, Alex Univercity, Egypt. E-mial : [email protected] Figure 1.1: Rieter compact spinning principle [5] Journal of the March - April 2016 361 SPINNING Our practical experience with compact spinning for sured by Uster Tensorapid 4. The measured results of more than 5 years working with 41,000 Rieter com- conventional and compact spinning were compared and pact spinning spindles (K44 M/C) producing different statistically analyzed by SPSS program (Statistical fine yarn counts produced from Egyptian cotton make Package for Social Science). our aim in this investigation is to study how far the compact spinning improve the quality of the Egyptian Table 2.2: Processing parameters for yarn counts from 14.7tex to 7.4tex G86 fine cotton yarns. 2. Material and methods Parameter Count Doubling Speeds Notes Process (output) HVI spectrum Bale Manger Software tests was used Carding 4.54 ktex ......... 83 m/min Cylinder which selects sixty four bales from long staple Egyp- Speed = 400rpm tian cotton G86. Table 2.1 summarized the average Lickerin speed = 1300rpm fiber test results for the selected bales. Breaker Draw Table 2.1: Physical fiber Characteristics of G86 cotton Frame 4.54 ktex 5 600 m/min from HVI spectrum Unilap 70 ktex 28 120 m/min Lap length = 300m. Combing 4.9 ktex 8 350 Noil=17% Spinning Fineness Maturity Upper half Uniformity Short Strength Elongation nips/min Consistency (μg/inch) (%) mean length index fiber (gm/tex) (%) Index (mm) index Finisher Draw SCI MIC. Mat. Len. Unf. SFI Str. Elg. Frame 4.9 ktex 8 400m/min 200 4.66 95 32.42 86.9 5.78 45,4 5.78 Speed frame 491.6 tex 1 1000rpm atex=960.2 The selected cotton bales were preceded in the spin- TPI= (1.1 ) ning mill under the mill running condition to produce combed yarn of counts 14.7, 11.8, 10.5, 9.8, and 7.4tex 3. Results and discussions on both a conventional ring spinning machine, and a The summary of the test results for several cotton spun compact spinning machine as sown in Table 2.2. The yarn counts produced on both of the compact and the yarns produced were tested according to ASTM. The conventional ring spinning M/c are given in Table 3.3. mass irregularity, yarn hairiness, and yarn faults were The results were statistically tested by t -test and given measured by Uster tester 4 (UT4). Yarn tenacity (cN/ in Table 3.4. tex)*, and yarn breaking elongation (%) were mea- Table 3.3: The average results of Warp combed yarns Count Cotton TPM a_tex U% CVm% `Thin Thick Neps/ Total Hairiness Elong. Elong. Tenacity Tenacity Compact Spinning (tex) -50% +50% +200% IPI Index % Cv% cN / tex Cv% / Km / Km Km 14.7 G86 945 3630 9.49 11.94 0.48 9.13 7.24 16.85 3.13 4.99 8.52 26.09 7.33 11.8 G86 1102 3780 9.84 12.42 1.00 16.05 12.50 29.55 2.76 4.76 9.09 26.20 7.84 10.5 G86 1130 3660 9.48 11.83 1.13 9.00 22.00 32.13 2.87 4.48 9.20 25.28 8.00 9.8 G86 1175 3680 9.82 12.35 1.67 11.42 19.57 32.66 2.50 4.73 9.20 26.38 8.40 7.4 G86 1408 3820 11.65 14.00 22.62 34.40 42.00 99.02 2.46 4.41 9.70 24.17 10.45 Ring Spinning Conventional 14.7 G86 996 3820 9.68 12.17 1.09 7.55 8.95 17.59 3.86 4.64 8.33 24.27 7.51 11.8 G86 1122 3850 10.28 12.94 3.04 16.30 17.42 36.76 3.63 4.43 9.27 23.04 7.81 10.5 G86 1130 3660 9.93 12.45 2.90 9.10 25.50 37.50 3.75 3.92 8.80 22.62 8.50 9.8 G86 1220 3820 10.60 13.37 9.90 23.09 43.20 76.19 3.63 4.09 8.90 21.90 8.90 7.4 G86 1496 4040 11.83 14.90 57.80 49.00 47.60 154.40 3.33 4.22 10.10 20.70 10.40 TEXTILE Association JTA : An effective marketing tool for strengthening business promotion Journal of the 362 March - April 2016 SPINNING Table 3.4: Statistical analysis results of Warp compact & ring spun yarn properties (t-test) Yarn Count (tex) 14.7 11.8 10.5 9.8 7.4 Yarn type Ring Comp. Ring Comp. Ring Comp. Ring Comp. Ring Comp. Twist Multiplier 3820 3630 3850 3780 3660 3660 3820 3680 4040 3 820 (atex) Yarn Prop. P* P* P* P* P* Mass Variation 0.004*** 0.000*** 0.000*** 0.000*** 0.011*** [CVm%] Thin Places 0.009*** 0.000*** 0.000*** 0.000*** 0.025*** [+50%/ Km] Thick Places [+50%/Km] 0.075** 0.146** 0.18** 0.465** 0.012*** Neps [200%/ Km] 0.018*** 0.000*** 0.000*** 0.000*** 0.228** Total Imperfections 0.611** 0.056** 0.000*** 0.000*** 0.007*** Yarn Hairiness [H] 0.000*** 0.000*** 0.000*** 0.000*** 0.005*** Yarn Tenacity 0.000*** 0.000*** 0.000*** 0.000*** 0.002*** [cN/ tex] Yarn Elongation [E %] 0.24*** 0.53** 0.000*** 0.000*** 0.000*** (*Significance values, ** the results are not statistically significant, *** the results are statistically significant) 3.1 Yarn mass variation These figures illustrates that, the yarn mass variation Figure 3.2 shows the relationship between the yarn of the single compact spun yarn is lower than the yarn mass variation of compact and conventional ring spun mass variation of the single conventional ring spun yarn versus yarn count. yarn by about 5%. That improvement in the single yarn mass variation was found to be statistically sig- nificant as shown in Table 3.4. This may be related to the compact yarn structure and more fibers integrated to the yarn body.
Details
-
File Typepdf
-
Upload Time-
-
Content LanguagesEnglish
-
Upload UserAnonymous/Not logged-in
-
File Pages96 Page
-
File Size-