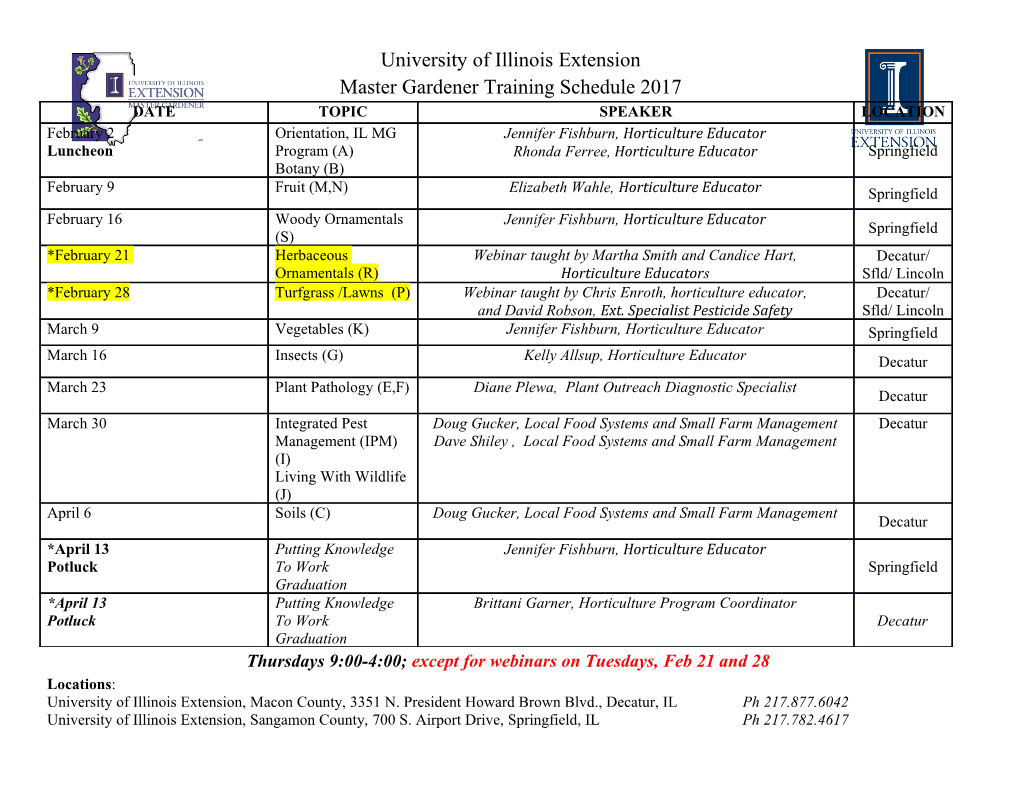
N 7 a - 1 9 46 5 NASA CR-120967 MODERN METHODOLOGY OF DESIGNING TARGET RELIABILITY INTO ROTATING MECHANICAL COMPONENTS by Dimitri B. Kececioglu and Louie B. Chester THE UNIVERSITY OF ARIZONA College of Engineering Engineering Experiment Station FILE COPY Prepared for NATIONAL AERONAUTICS AND SPACE ADMINISTRATION NASA Lewis Research Center Grant NCR 03-002-044 1. Report No. 2. Government Accession No. 3. Recipient's Catalog No. NASA CR-120967 4. Title and Subtitle 5. Report Date MODERN METHODOLOGY OF DESIGNING TARGET January 31, 1973 6. Performing Organization Code RELIABILITY INTO ROTATING MECHANICAL COMPONENTS 7. Author(s) 8. Performing Organization Report No. Dimitri B. Kececioglu and Louie B. Chester 10. Work Unit No. 9. Performing Organization Name and Address The University of Arizona 11. Contract or Grant No. Tucson, Arizona 85721 NCR 03-022-044 13. Type of Report and Period Covered 12. Sponsoring Agency Name and Address Contractor Report National Aeronautics and Space Administration 14. Sponsoring Agency Code Washington, D.C. 20546 15. Supplementary Notes Project Manager, Vincent R. Lalli, Spacecraft Technology Division, NASA Lewis Research Center, Cleveland, Ohio 16. Abstract Theoretical research done for the development of a methodology for designing specified reliabilities into rotating mechanical components is referenced to prior reports submitted to NASA on this research. Experimentally determined distributional cycles-to-failure versus maximum alternating nominal strength (S-N) diagrams, and distributional mean nominal strength versus maximum alternating nominal strength (Goodman) diagrams are presented. These distributional S-N and Goodman diagrams are for AISI 4340 steel, R 35/4' hardness, round, cylindrical specimens 0.735 in. in diameter and 6 in. long with a circumferential groove 0.145 in. radius for a theoretical stress concentration K = 1.42 for Phase I research and 0.034 in. radius for a K =2.34 for Phase II research. The specimens are subjected to reversed bending and steady torque in specially built, three complex-fatigue research machines. Based on these results,the effects on the distributional S-N and Goodman diagrams and on service life of superimposing steady torque on reversed bending are established, as well as the effect of various stress concentrations. In addition a computer program for determining the three-parameter Weibull distribution representing the cycles-to-failure data, and two methods for calculating the reliability of components subjected to cumulative fatigue loads are given. 17. Key Words (Suggested by Author(s)) 18. Distribution Statement Mechanical Reliability Distributional S-N Unclassified - unlimited Design by Reliability Diagrams Probabilistic Design Distributional Goodman Diagram Cycles-to-Failure Distributions 19. Security Classif. (of this report) 20. Security Classif. (of this page) 21. No. of Pages 22. Price* Unclassified Unclassified xiii + 183 ' For sale by the National Technical Information Service, Springfield, Virginia 22151 ii NASA CR - 120967 FINAL REPORT MODERN METHODOLOGY OF DESIGNING TARGET RELIABILITY INTO ROTATING MECHANICAL COMPONENTS by Dimitri B. Kececioglu and Louie B. Chester THE UNIVERSITY OF ARIZONA College of Engineering Engineering Experiment Station prepared for NATIONAL AERONAUTICS AND SPACE ADMINISTRATION NASA Lewis Research Center Grant NCR 03-002-044 111 TABLE OF CONTENTS Page TITLE PAGE iii LIST OF FIGURES vi LIST OF TABLES x SUMMARY xiii 1. INTRODUCTION 1 1.1 BACKGROUND 1 1.2 EXPERIMENTAL RESEARCH OPERATION 3 2. EXPERIMENTAL RESEARCH 7 2.1 PHASE I RESEARCH COMPLETION 7 2.2 PHASE II RESEARCH 10 2.2.1 GEOMETRY AND HARDNESS OF RESEARCH SPECIMENS 10 2.2.2 STRENGTH CHARACTERISTICS OF RESEARCH SPECIMENS 12 2.2.3 ANALYSIS OF TENSILE TEST RESULTS 14 2.2.4 RECALIBRATION OF NASA COMPLEX-FATIGUE RESEARCH MACHINES 16 2.2.4.1 REQUIREMENTS 16 2.2.4.2 PROCEDURES AND RESULTS 17 2.2.5 UNGROOVED SPECIMENS FATIGUE RESEARCH ... 18 2.2.6 GROOVED SPECIMENS FATIGUE RESEARCH .... 21 IV TABLE OF CONTENTS (Continued) Page 3. THEORETICAL RESEARCH 26 3.1 GENERATION OF FINITE LIFE DISTRIBUTIONAL GOODMAN DIAGRAMS FOR RELIABILITY PREDICTION 26 3.2 THE WEIBULL DISTRIBUTION AS A DESCRIPTION OF FATIGUE LIFE 27 3.3 RELIABILITY OF COMPONENTS SUBJECTED TO CUMULATIVE FATIGUE • . 34 4. OVERALL CONCLUSIONS . .' 47 5. RECOMMENDATIONS 53 ACKNOWLEDGEMENTS 55 REFERENCES 56 FIGURES 59 TABLES 97 APPENDIX A POP PROGRAM TO CALCULATE VISICORDER DIVISIONS FOR DESIRED LEVELS OF BENDING AND TORQUE 129 APPENDIX B PROGRAM STRESS 131 APPENDIX C PROGRAM CYTOFR 142 APPENDIX D PROGRAM WEIBULL 160 APPENDIX E POP PROGRAM TO CALCULATE ENDURANCE STRENGTH PARAMETERS FROM STAIRCASE TESTS 178 APPENDIX F POP PROGRAM TO CALCULATE PAN WEIGHTS FOR DESIRED BENDING STRESS LEVELS FOR THE ANN ARBOR RESEARCH MACHINE . 179 DISTRIBUTION LIST 180 LIST OF FIGURES Figure No. Page No. 1 Schematic front view of combined reversed bending-steady torque fatigue-reliability research machine 60 2 Schematic top view of combined reversed bending-steady torque fatigue-reliability res ear ch machine 61 3 Bending stress strain gage bridge 62 4 Shear stress strain gage bridge 63 5 Flow chart of steps in cycles-to-failure and stress-to-failure fatigue tests 64 6 Phase I research specimen geometry 65 7 Phase II research specimen geometry 66 8 Cycles-to-failure distributions at the stress ratio of 0.44 for AISI 4340 steel Rc 35/40 Phase I grooved specimens 67 9 Cycles-to-failure distributions at the stress ratio of ~ for AISI 4340 steel Rc 35/40 Phase I grooved specimens 68 10 Cycles-to-failure distributions at the stress ratio of 3.5 for AISI 4340 steel Rc 35/40 Phase I grooved specimens 59 11 Cycles-to-failure distributions at the stress ratio of 0.83 for AISI 4340 steel Rc 35/40 Phase I grooved specimens 70 12 Endurance strength data obtained by the staircase method for stress ratio of 0.45 for AISI 4340 steel, MIL-S-5000B, Condition C4, Rockwell C 35/40, with Phase I grooved specimens 71 13 -Distributional Goodman strength diagram for 2.5 x 106 cycles of life Phase I results with AISI 4340 steel Rc 35/40 grooved specimens (See Table 10) 72 14 Endurance strength data obtained by the staircase method for stress ratio of °° for AISI 4340 steel, MIL-S-5000B, Condition C4, Rockwell C 35/40, with Phase I grooved specimens 73 vi LIST OF FIGURES Figure No. Page No. 15 Endurance strength data obtained by the staircase method for stress ratio of 3.5 for AISI 4340 steel, MIL-S-5000B, Condition C4, Rockwell C 35/40, with Phase I grooved specimens ........... 74 16 Endurance strength data obtained by the staircase method for stress ratio of 1.0 for AISI 4340 steel, MIL-S-5000B,Condition C4, Rockwell C 35/40, with Phase I grooved specimens ........... 75 17 Grooved specimen sections used for hardness measurements .................................... 75 18 Specimen sections and locations for hardness measurements .................................... 77 19 Bending stress bridge calibration setup ........... 73 20 Torque (shear) stress bridge calibration setup ........................................... 79 21 Ungrooved endurance strength specimen 22 Endurance strength data obtained by staircase method in Ann Arbor machine for the stress ratio of « for AISI 4340 steel Rc 35/40 Phase I research. Specimens with no groove and a test section diameter of 0.3150 in ........ 81 23 Endurance strength data obtained by the staircase method in the Ann Arbor machine for the stress ratio of » for AISI 4340 steel Rc 35/40 Phase II research. Specimens with no groove and a test section diameter of 0.2500 in ........ 32 24 Normal cycles-to-failure distribution of 35 grooved specimens for an alternating stress level of 108,900 psi at a stress ratio of infinity and nominal groove diameter of 0.491 inches ..... 83 25 Lognormal cycles-to-failure distribution of 35 grooved specimens for an alternating stress level of 108,900 psi at a stress ratio of infinity and nominal groove diameter of 0.491 inches ..... 34 VII LIST OF FIGURES Figure No. Page No. 26 Cycles-to-failure distributions at the stress ratio of » for AISI 4340 Rc 35/40 Phase II grooved specimens 85 27 Cycles-to-failure distribution at the stress ratio of 1.06 for AISI 4340 Rc 35/40 Phase II grooved specimens 86 28 Cycles-to-failure distribution at the stress ratio of 0.40 for AISI 4340 Rc 35/40 Phase II grooved specimens 87 29 Cycles-to-failure distribution at the stress ratio of 0.25 for AISI 4340 Rc 35/40 Phase II grooved specimens • 88 30 Cycles-to-failure distribution at the stress ratio of 0.15 for AISI 4340 Rc 35/40 Phase 11 grooved specimens 89 31 Endurance strength data obtained by the staircase method for Phase II grooved specimens of AISI 4340 steel Rc 35/40 for stress ratio of °° 90 32 Endurance strength data obtained by the staircase method for Phase II grooved specimens of AISI 4340 steel Rc 35/40 for stress ratio of 1.06 91 33 Endurance strength data obtained by the staircase method for Phase II grooved specimens of AISI 4340 steel Rc 35/40 for the stress ratio of 0.40 92 34 Endurance strength data obtained by the staircase method for Phase II grooved specimens of AISI 4340 steel Rc 35/40 for stress ratio of 0.25 93 35 Endurance strength data obtained by the staircase method for Phase II grooved specimens of AISI 4340 steel Rc 35/40 for stress ratio of 0.15 94 36 Distributional Goodman strength diagram for 2.5 x 106 cycles of life Phase II results with AISI 4340 steel Rc 35/40 grooved specimens (See Table 30) 95 viii LIST OF FIGURES Figure No. Page No. 37 Weibull cycles-to-failure distribution of 35 grooved specimens for an alternating stress level of 108,900 psi at a stress ratio of infinity and nominal groove diameter of 0.491 inches 96 IX LIST OF TABLES Table No.
Details
-
File Typepdf
-
Upload Time-
-
Content LanguagesEnglish
-
Upload UserAnonymous/Not logged-in
-
File Pages197 Page
-
File Size-