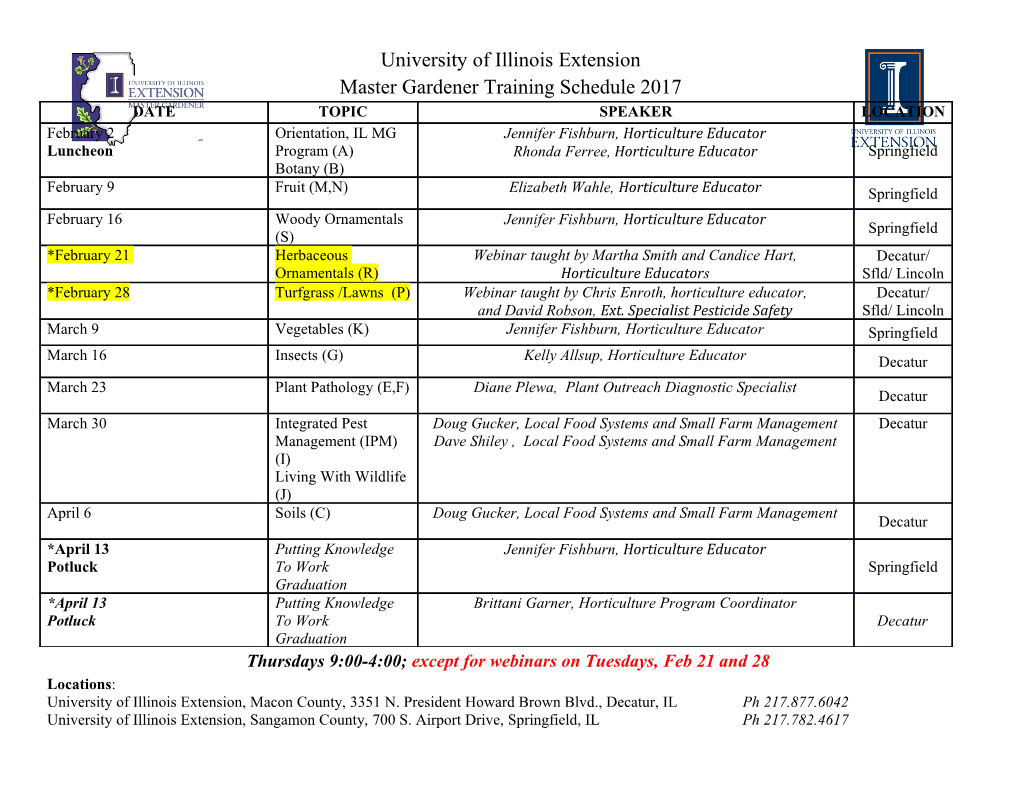
9th Int. Beam Instrum. Conf. IBIC2020, Santos, Brazil JACoW Publishing ISBN: 978-3-95450-222-6 ISSN: 2673-5350 doi:10.18429/JACoW-IBIC2020-THPP21 DESIGN AND DEVELOPMENT OF A NOVEL STRIPLINE FAST FARADAY CUP TO MEASURE ION BEAM PROFILE A. Sharma1†, R. K. Gangwar, Indian Institute of Technology (ISM), Dhanbad, India B. K. Sahu, Inter-University Accelerator Centre, New Delhi, India 1also at Inter-University Accelerator Centre, New Delhi, India Abstract interaction hole and used for very high current, high energy beam species, the proposed design is provid- Present day heavy ion accelerators use bunched ion ed with larger beam interaction hole to cater even for low beams of sub-nanosecond time scale for beam accelera- beam currents produced at IUAC which are of the order tion. In order to monitor the longitudinal beam bunch to 10-100 nA. Extensive studies on via fencing suggested profile, Fast Faraday Cups (FFC) are employed. Owing to [4-7] for suppression of spurious modes in stripline ge- the advent of microstrip technology and its fabrication ometry using ground-to-ground stitching via filled with process, planar structures have become easier to fabricate. copper / metalized rods has been extended for the present A novel planar design using the same is developed with a case as well. special provision for mounting edge launch connectors through a microstripline feed, followed by a microstrip to stripline transition to again a microstrip structure in the beam interaction hole. The entire structure is symmetrical and bidirectional with 50 Ω transmission lines. An exper- imental study on via placement around central stripline has also been conducted to not only ensure the field con- tainment around the strip but also for bandwidth en- hancement. To measure ion beam currents from 10-100 nA and a bunch width of < 1ns, device has a beam inter- action hole of around 10mm. 3 dB bandwidth is measured > 6 GHz resulting in a pulse rise time of ~60 ps or less. Figure 1: Beamline Test Setup. The proposed device is also provided with a bias ring on the topmost layer of the 3 layer architecture for electron Various sections of this paper deals with design equa- suppression. In this paper, design, fabrication and RF tions and novelty implied therein. Emphasis has been testing of stripline fast faraday cup is presented. given on stitching via placement and its mode suppres- sion-cum-bandwidth extension effects. Paper is concluded 2020). Any distribution of this work must maintain attribution to the author(s), title of the work, publisher, and DOI INTRODUCTION by comparison of results of EM simulations done in An- © soft’s HFSS with measured results obtained on VNA. The 15 UD Pelletron and the upcoming High Current Injector produces pulsed ion beam to be further energized DESIGN DETAILS by the Superconducting LINAC of IUAC. The bunch The proposed configuration of stripline device is shown length acceptance of the superbuncher cavity of LINAC is in Fig. 2. It is realized as a 3 layer, stacked-up structure of ~1-2 ns which further reduce it to 200-500 ps. In order to two planar substrates. Upper one has two rectangular determine the time and energy structure of the beam notches at both edges so as to connect two SMA edge bunches, it is essential to measure the longitudinal profile launch connectors. A beam interaction hole of the order of and Time of Flight of the beam. By employing Fast Fara- 10 mm diameter has been made at the center of the device day Cups, longitudinal profile of a beam can be measured. for the beam sizes of the order 3-4 mm in diameter. Low- Stripline FFCs are interceptive devices made up of a er substrate has a grounded transmission line structure. printed circuit transmission line of 50Ω or any given impedance [1] which can produce picosecond pickup pulse response when ion beam bunches strike on it. Figure 1 shows typical application of FFC device at IUAC where response times of the order of 50-60 ps or > 6 GHz bandwidth are well suited. Aim of this paper is to design such a novel stripline FFC as per IUAC require- ment. The most notable works on stripline FFC design are found in [2-3] which have used multilayer structure with stitching vias to maintain signal integrity, and bandwidth enhancement. While these devices have a small beam ___________________________________________ † [email protected] Figure 2: Proposed Stripline FFC Design. Content fromTHPP21 this work may be used under the terms of the CC BY 3.0 licence ( 246 Longitudinal Diagnostics and Synchronization 9th Int. Beam Instrum. Conf. IBIC2020, Santos, Brazil JACoW Publishing ISBN: 978-3-95450-222-6 ISSN: 2673-5350 doi:10.18429/JACoW-IBIC2020-THPP21 After the removal of notches and central cylinder, the If (W/H) > 1 geometry essentially becomes a microstrip based at these locations. So, we use the 50Ω microstripline design for- mula to calculate the width at these three locations while (5) RR11 eff rest of the central trace is composed of 50Ω stripline. In 2 H 2112 order to transform the fields from microstrip-to-strip line W and vice-versa, tapered transition is employed [8]. Addi- tionally, along the tapered line, the copper pour on the 120 (6) upper substrate is etched in the same tapered fashion so Zo that impedance of the line is still maintained to 50Ω. WW2 eff 1.393 ln 1.444 The stitching via fence is placed on both side of central HH3 trace, shorting the top and bottom ground planes to su- press leakage of unwanted modes. In order to further Figure 3 shows the basic stripline geometry while via- reduce reflections at the transition from microstrip-to- fences. Following considerations are taken into account stripline, via fences are placed around the SMA connector while designing vias [2-6]: closer than other points along the trace [3]. The part of the Via pitch ‘p’ should be randomly varied and is kept central trace at the beam interaction hole is called as Far- less than λd ( cf/( rd ))to prevent effective RF aday Cup. In order to suppress the secondary electron emission, a bias ring can also be provided around the boundary. Typically less than λd /8, so as to prevent a potential difference between the ground planes lead- central beam interaction hole to which a negative voltage supply can be connected. To accommodate this ring on ing to a parallel plate mode. the top ground layer, a portion of copper pour is etched The via fence-to-fence separation ‘s’, should be a and bias trace is insulated from ground plane. minimum 3 to 5 times the strip width. The substrate used is of Teflon class which is preferred If via fence-to-fence separation is too great, a pseudo for high to ultra-high vacuum conditions. All the mi- rectangular waveguide mode can be excited. crostrip line components are 50Ω, λd/4 line lengths. This is done to ensure that the phase shift experienced by the signal while traversing through the line is between -180 deg. to +180 deg. Design Formulae Impedance of planar stripline structure is computed us- ing Eq. (1), (2) [1]: 2020). Any distribution of this work must maintain attribution to the author(s), title of the work, publisher, and DOI 30 b © Zo . (1) r Wbe 0.441 Figure 3: Stripline Structure with Via-Fence. W 0 for 0.35 Mode Suppression W W b e The study in [7] has been extended to the stripline ge- bb W (0.35Wb / )2 for 0.35 ometry considering that both the ground planes are get- b (2) ting excited by the fringe fields of the central transmission line like a rectangular patch. This rectangular patch now Where ‘We’ is the effective width of central conductor, behaves like a parallel plate type of resonant cavity with ‘W’ is the physical width of central conductor and ‘b’ is higher order modes in the absence of via-short. The high- the total height of the substrate. Similarly, impedance er order modes follow the Eq. (7) for determination of based geometry calculations are done for microstrip struc- cut-off frequency of resulting structure: ture per Eq. (3)-(6). If (W/H) > 1 2 22 cm n q frmnq (7) 2 2 LWg b RR111 W r eff 0.04 1 22H H 112 W (3) Where L, Wg, and b represents the length, width and height of the substrate respectively. Eq. (7) can be simpli- fied further due to b << λ and can be re-written as: 60 HW d (4) ZlnHo 80.25 eff WH THPP21 Content from this work may be used under the terms of the CC BY 3.0 licence ( Longitudinal Diagnostics and Synchronization 247 9th Int. Beam Instrum. Conf. IBIC2020, Santos, Brazil JACoW Publishing ISBN: 978-3-95450-222-6 ISSN: 2673-5350 doi:10.18429/JACoW-IBIC2020-THPP21 2 2 cm n frmn0 (8) 2 LW r g In the Eq. (8), different values of ‘m’ and ‘n’ decide the spurious mode that may propagate inside the geometry. Upon the HFSS simulation study for the cases shown in Fig. 4, it is seen that in the absence of via, 3 dB band- width is highly restricted to a very low value. However, with the introduction of stitching vias and subsequent variation in the via-fence spacing, the spurious low fre- quency resonant modes are progressively shifted to higher Figure 5: S21 vs Freq. with and without via-fence (top), frequencies thereby increasing the usable 3 dB bandwidth parametric study with variable via-fence spacing (bot- of the resulting device.
Details
-
File Typepdf
-
Upload Time-
-
Content LanguagesEnglish
-
Upload UserAnonymous/Not logged-in
-
File Pages4 Page
-
File Size-