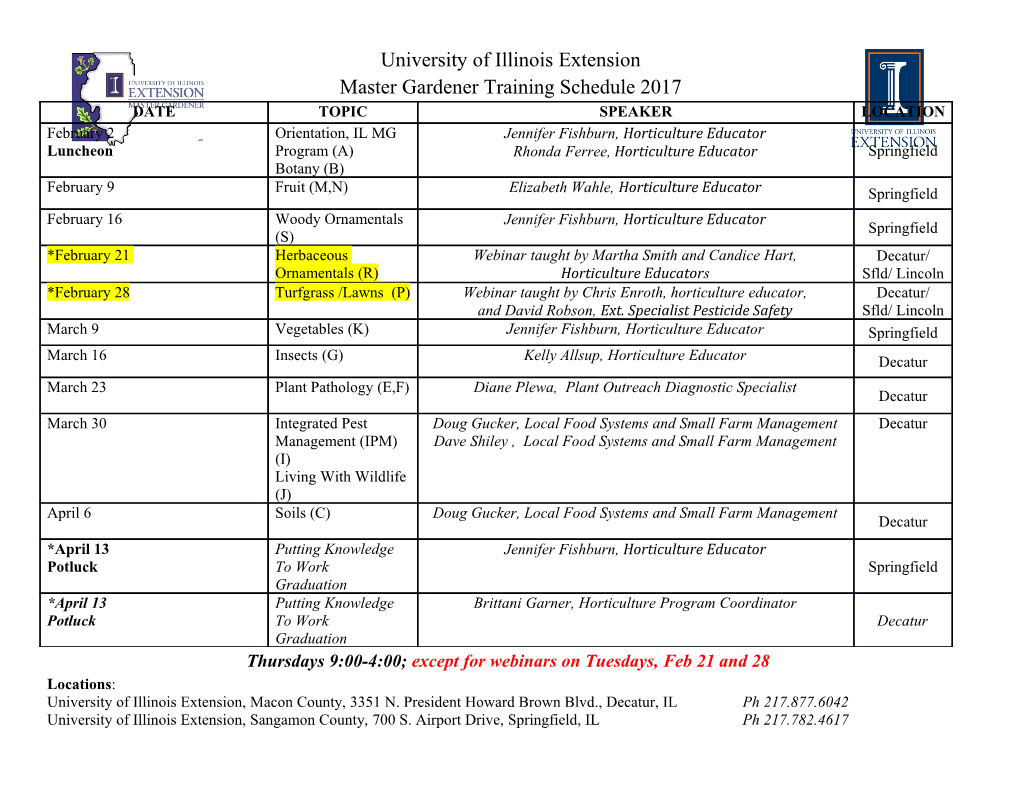
bulletin cover story Laser-driven chemical vapor deposition for high-performance fibers and powders By Shay Harrison and Mark Schaefer Laser-driven chemical vapor deposition is a remarkably innovative technology that significantly improves the quality of high-performance fibers and powders and broadens the input laser into hundreds of parallel beams, allowing for simultane- ous fabrication of many fibers. This patented opto-mechanical design catalog of compositions available to the materials community. unlocked the potential for the LCVD technology to positively impact a range of material-focused markets, including semiconductors, jet engines, power turbines, hypersonics, ceramic windows, nuclear clad- ding, armor material, and lightweighting of polymer matrix composites for the aircraft and aerospace industry. he company Free Form TFibers (FFF), located in What is LCVD? The fundamental basis of LCVD entails a laser directed at a substrate Saratoga Springs, New York, has spent located in a reaction chamber that also contains a planned mixture of 15 years perfecting the process of fiber precursor gases. The focused laser beam induces a heterogeneous chemi- cal reaction amongst the precursors, leading to a solid deposit forming growth using laser-driven chemical on the substrate. As solid material deposits, the laser or the substrate vapor deposition (LCVD), with par- can be pulled away to continuously form the fiber format. Similarly, ticular expertise and understanding in solid coatings can be formed on the fiber surface using the same LCVD concept in subsequent stages, creating layers of uniform thickness. In fabricating silicon carbide fibers. this manner, LCVD can be viewed as the only gas-to-solid additive man- The integral development at FFF in transitioning ufacturing-based approach to high-value material fabrication. LCVD from a laboratory-scale technique to a scalable LCVD technology is part of a family of chemical vapor deposition manufacturing process was the parallelization of the (CVD) based processes that differ primarily in the energy delivery 38 Celebrating 100 years www.ceramics.org | American Ceramic Society Bulletin, Vol. 100, No. 7 approach used to drive the gas phase reaction. The most well-known example is hot wall CVD, employed in micro- electronics chip fabrication, in which the entire volume of a large chamber is SiC uniformly heated to drive deposition of Filament precisely controlled layers on a substrate positioned in the chamber. Similarly, a Laser--Printed Induced Laser number of related techniques use various Plasma energy sources, such as microwaves, heat Filament Array Laser Array lamps, ultraviolet radiation, and plasma Beam enhancement of the hot wall approach, 1 mm to achieve different deposition aims. Most of these microelectronics-focused x15 Mag. 100100 µmµm methods yield deposition rates that range from tens to several hundreds of microns thickness per hour.1,2 PATENTS:PATENTS: In contrast to these techniques, x5 Mag. JPJP Pat.Pat. 63533686353368 EPEP 22 804804 969969 B1B1 LCVD uses a focused laser beam with 250 µm 250 µm CNCN Pat.Pat. ZLZL 20132013 88 0015183.80015183.8 a spot size on the order of 20 microns USUS 10,047,01510,047,015 B2B2,, 9,938,3939,938,393 B2,B2, 9,896,3859,896,385 B2,B2, 10,876,22710,876,227 B2B2 Credit: Free Form Fibers to deliver the energy required for gas Figure 1. Schematic of the laser-driven chemical vapor deposition process. decomposition. The resulting tempera- ture gradient is on the order of 105 K/m, are essentially impossible using the and developed into commercial SiC fiber whereas CVD is essentially isothermic.3 polymer-based route. Similarly, preci- products by Nippon Carbon and Ube. This temperature gradient drives fiber sion control of the fiber diameter offers The use of polymer-based polycarbosi- deposition rates that can range from 30 a flexibility of production not available lanes as a precursor unlocked the prom- to 300 microns per second, with rates in in spinneret-based production. ise of a high-temperature nonoxide com- the millimeter/second range for some As stated previously, a significant posite material system, leading to various material systems such as carbon. technical advance made by FFF in scaling SiC fiber reinforcement products; howev- Because of the CVD “DNA” that is LCVD is the parallelization of the input er, there are material limitations inherent central to LCVD, the range of materials laser beam (Figure 1), which allows for in batch chemical mixing and forming that can be fabricated in fiber format multiple fibers to be grown simultane- and the subsequent thermal processing is broad, based on 70+ years of precur- ously. Fibers are self-seeded. The pull rate of green fibers. A broad array of advanta- sor development for the semiconductor of the substrate matches the deposition geous features and properties arise from industry, which required delivery of spe- rate of material onto the formed fiber. LCVD-based fabrication of fibers. cific chemical elements to the functional Because material builds from the bottom The most fundamental characteristic, layers needed for chip operation. This up, LCVD is analogous to additive man- particularly evident in SiC fibers, is delivery method provides an essential ufacturing (AM), but the main difference the presence of a gradient microstruc- difference from polymer precursor-based is the capability of LCVD to produce ture across the fiber radius. The center approaches to fiber fabrication, which solid material directly from the gas phase. reveals elongated grains in the direction are limited to polymer chemistries that Also similar to AM, through its efforts of the fiber axis, on the order of 50 nm can be developed to successfully yield to recycle the gas precursors and access long and 10 nm wide. At the mid-radial the targeted final composition. maximum utilization of these raw mate- point, the grains are nominally 5 nm LCVD fiber composition is tailored rial feedstocks, FFF aims to achieve a and equiaxed, transitioning to amor- through the selection of gas precursors waste-less process with any produced by- phous at the fiber edge. This feature and only those desired elements are product gases capable of being employed stands in contrast to the homogeneous, incorporated. Polymer-derived fibers in other applications, such as redirecting invariant microstructure found in the contain unreacted or partially reacted extra hydrogen generated from the pro- polymer precursor-based SiC fibers. contaminant species, in addition to duction of silicon carbide products for The impact of this inhomogeneous the possible inclusion of metal catalysts use in the H2-based transportation sector. distribution is hypothesized to drive the in some fiber products to drive the tensile and creep behavior found in the polymer conversion process, that nega- Advantages of LCVD LP30-SC material. For other materials, tively impact the ultimate temperature LCVD technology stands in signifi- understanding and control of the LCVD capability. Precision control of the cant contrast to the chemical conversion process parameters can yield variations fiber composition also allows LCVD processing that was patented in the late in the fabricated microstructure. For to produce complex chemistries that 1970s, known as the Yajima method,4,5 example, boron fiber has been produced American Ceramic Society Bulletin, Vol. 100, No. 7 | www.ceramics.org Celebrating 100 years 39 Laser-driven chemical vapor deposition for high-performance fibers and powders 1 mm Credit: Free Form Fibers Figure 2. “Sausage-link” variable diameter LP30-SC fibers. 71:29 composition. The 77:23 The physical characteristics of fibers fiber chemistry, while limited to produced by LCVD also highlight the temperatures below the silicon unique capabilities of the technology. melting temperature of 1,412°C, Electron microscopy at multiple labora- revealed a very high single fiber tories showed a very high cross-sectional tensile strength at room temper- density with no porosity evident. This 80 micron diameter fiber ature, on the order of 7–8 GPa. structure obviously drives mechanical 2 1/2" diameter coil This flexibility opens up design performance by limiting the number of considerations for composites in internal crack initiation sites. Precision tailoring the fiber composition control of the laser leads to a range of to the desired property perfor- functional modifications that can be mance by component function embedded into the fiber geometry. The and location. filament diameter can be varied during Related to the fiber composi- growth. Figure 2 illustrates a SiC fiber Credit: Free Form Fibers tion, the LCVD process yields produced with periodic discontinuous Figure 3. LP30-SC fiber coil. materials without contamination diameter changes. Similarly, the fila- in both amorphous and nanocrystalline of undesired chemical species. ment axis needs not be straight. Lateral states by using different precursor gases. For instance, a LCVD silicon nitride fiber motions of the laser can be tracked Another critical capability of the has only silicon and nitrogen present. (within limits) via fiber growth to create LCVD technology, harnessed through This advantage is crucially important in a curvilinear filament. This feature is years of developed expertise, is the precise reference to oxygen, which drives deleteri- illustrated by the coil shown in Figure 3. control of the final stoichiometry of the ous oxidation behavior at high tempera- produced fibers, which reveals itself in tures in a range of ceramic materials. In LCVD products and performance several ways. Focusing on the SiC chem- particular, oxygen contamination impacts FFF has embraced LCVD technology istry, a nominally stoichiometric fiber will the temperature capability range for SiC to deliver state-of-the-art high-perfor- have a composition of 70 weight percent fibers. NGS, the U.S. manufacturer of Hi mance materials in either fiber or pow- silicon and 30 weight percent carbon Nicalon-Type S, presently reports the level der format to the high-tech marketplace, 6 (referred to as 70:30). FFF has produced of residual oxygen at 0.8 wt.%.
Details
-
File Typepdf
-
Upload Time-
-
Content LanguagesEnglish
-
Upload UserAnonymous/Not logged-in
-
File Pages7 Page
-
File Size-