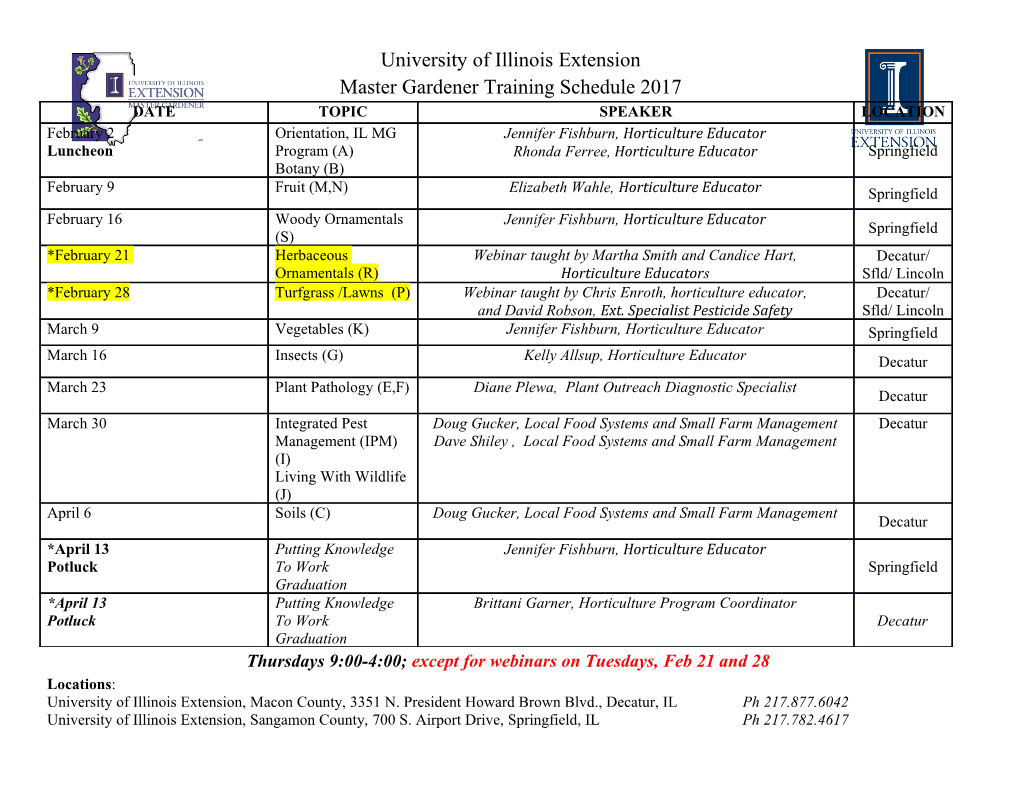
Nitriding (Ferritic Nitrocarburizing) – fundamentals, modeling and process optimization Report No. 13-01 Research Team: Mei Yang [email protected] (508) 831-5825 Xiaolan Wang [email protected] Richard D. Sisson, Jr. [email protected] (508) 831-5335 Focus group: 1. Project Statements Objectives Develop a fundamental understanding of the nitriding process in terms of: Mass transfer kinetics from the atmosphere into the surface. The nitriding potential in the atmosphere is determined by the initial gas mixture (NH3/H2) and can be calculated from thermodynamics. The transfer of nitrogen from the atmosphere to the surface of the steel is controlled by the nitriding potential in the atmosphere as well as the surface condition (chemistry/contamination, and roughness) and the steel composition. The mass transfer may be modeled by either a mass transfer coefficient, or a flux as a function of time. Develop a computational model to determine the nitrogen concentration and nitride profiles in the steel in terms of temperature, atmosphere composition, steel surface condition, alloy composition and the pre- nitriding steel microstructure. This tool will be designed to predict the nitride profile as well as the nitrogen concentration profile (i.e. case depth) based on the input of the process parameters of temperature (time), NH3/H2 (time), the alloy designation (4140 or Nitralloy – 135) and the surface condition of the steel. • NitrideTool will be created by simulating the nitrogen uptake and diffusion into ferrite and the precipitation of nitrides and conversion of carbides to carbonitrides during the process. The fundamentals of these phenomena as described above will be used for the model generation. The model will include multiple boosts and diffuse type cycles. The model will also rely on the isopleths and Lehrer diagrams from Thermo-Calc. • Verify the model by comparison with experimental results. The verification will initially be conducted by comparison with results in the literature and results from CHTE member companies. Selected experiments will also be conducted to test the model’s accuracy and capabilities. Report 1201 Page 1 Develop a model-based optimization process to determine the optimum process parameters for several process goals: minimum cycle time, minimum cost, maximum productivity, minimum gas consumption. Strategy 1. Literature review – a. Nitriding practices in industry b. NH3/H2 thermodynamics – effects of H2O c. N solubility in steel – alloying effects including C d. N diffusion in steel – alloying effects including C e. Nitride precipitation in steels – kinetics and size f. N adsorption, decomposition and absorption g. Nitride hardening mechanisms h. Effects of steel microstructure – tempered Martensite carbide distribution – on diffusion and nitride precipitation 2. Determine the boundary conditions for nitriding of steel a. Flux? b. Mass transfer coefficient? c. Constant surface concentration? 3. Create Nitridetool for N diffusion and nitride precipitation in steels a. Nitralloy – 135 b. 4140 4. Verify computer model a. Literature data b. Selected experiments 5. Develop optimization methods for nitriding a. Minimum cycle time b. Minimum cost 6. Test optimization methods 2. Achievement to date Gas nitriding is a thermochemical surface treatment in which nitrogen is transferred from an ammonia atmosphere into the surface of steels at temperatures within the ferrite and carbide phase region. [1, 2] After nitriding, a compound layer and an underlying diffusion zone (i.e. the case) are formed near the surface of the steel (Figure 1). The compound layer, also known as the white layer, consists predominantly of ε - Fe2-3(C, N) and/or γ΄ - Fe4N phases and can greatly improve the wear and corrosion resistances. [3] The hardened diffusion zone, which is composed of interstitial solid solution of nitrogen dissolved in the ferrite lattice and nitride and/or carbonitride precipitation for the alloy steels containing the nitrides forming elements, Report 1201 Page 2 is responsible for a considerable enhancement of the fatigue endurance. Furthermore, being a low temperature process, nitriding minimizes the distortion and deformation of the heat treated parts. [1] Therefore, gas nitriding is an important surface treatment for ferritic steels. Figure 1. Schematic compound layer and diffusion zone structure of nitrided iron/steel Although the industrial use of the gas nitriding began in the 1930s, it has not gained wide applications mainly due to its low performance reliability [4]. The properties of nitrided steels are determined by the nitrided case microstructures. To ensure the reproducible and desirable properties from batch to batch, the gas nitriding need to be controlled to ensure the microstructure evolution. The successful gas nitriding process control depends on: 1) process parameters selection to meet the specification, 2) accurate process parameters control during the process. The gas nitriding process parameters include temperature, time, and the nitriding atmosphere. For the nitriding atmosphere control, the ammonia dissociation rate was traditionally adopted as the controlling parameter. It represents the percentage of ammonia dissociated into hydrogen and nitrogen and is manually measured by using a burette in the furnace exhaust gas. Since dissociation rate is not an in-situ measurement and the measurement is done manually, it introduces operator induced variability and cannot provide the accurate control on the nitriding process. A new control parameter, the nitriding potential, was introduced in the 1990’s [5]. The nitriding potential is defined by; Report 1201 Page 3 p K = NH3 n p3/ 2 (1) H2 where p and p are the partial pressures of the ammonia and hydrogen gases respectively. NH 3 H 2 By utilizing the thermal conductivity hydrogen sensor in conjunction with the two-loop controller/programmer, the nitriding potential can be calculated and controlled automatically and accurately. [6] With the development of measure and control systems, the gas nitriding process parameters can be controlled accurately. How to pre-define the nitriding process parameters to meet the specifications becomes the main challenge of the gas nitriding process control. Conventionally, trial and error methods were used to define the nitriding process parameters to meet the specifications. This method is expensive, time consuming, and hard to control. Therefore, an effective simulation tool is needed to define the process parameters based on the performance specifications of various steels. By using this tool, the properties of the nitrided steels based on the phase constitution, surface nitrogen concentration, nitrogen concentration profile, case depth, as well as growth kinetics can be simulated through variation of process parameters (temperature, time, and the nitriding atmosphere). [7] There has been ongoing effort on the simulation of the gas nitriding process since 1990s and most of the work has been done to simulate the nitriding process of pure iron [8-10]. However, the pure iron is never used for nitriding in industry while the simulation for nitridable steels is greatly needed. In the present work a computational model is developed to determine the nitrogen concentration and nitride profiles in the nitrided steels in terms of temperature, atmosphere composition, steel surface condition, alloy composition and the pre-nitriding steel microstructure. Based on this model, the nitride profile as well as the nitrogen concentration profile can be predicted from the input of the process parameters such as nitriding potential, temperature, time, and the steel composition. 2.1. Experiments 2.1.1. Materials and experimental procedures The AISI 4140 bars used in the experimental study were acquired from Peterson Steel Corporation and their composition determined by optical emission spectroscopy (OES) is reported in Table 1. Report 1201 Page 4 Table 1. Composition of AISI 4140 in wt.% C Mn P S Si Cr Mo Fe 0.399 0.91 0.01 0.029 0.266 0.88 0.166 Balance Before nitriding, the cylindrical steel bars were heat treated to harden the core by heating to 843oC and keeping at this temperature for 1.5 hours in Endothermic gas at 0.4% carbon potential, followed by quenching in agitated 54oC mineral oil, and were washed in hot water and tempered in air at 579oC for 3 hours (Bodycote, Worcester, MA, USA). The hardening process is shown in Figure 2. T T=1550F (843oC) 1.5hrs Quenching in Mineral oil T=1075F (579oC) 3hrs Quenching Tempering Room T Figure 2 Hardening process for steel bars The bars were machined into disks with a diameter of 3.175 cm and thickness of 1 cm. Figure 3 shows the schematic of the sample and its loading configuration for the nitriding process. Before the nitriding process, the disks were washed with alcohol and half of the disks were pre- oxided in air at 330oC for 3 hours to investigate the effect of the surface condition on the gas nitriding process. In this report, as-washed and pre-oxided are used to refer the different surface conditions before the gas nitriding process. !! Both as-washed and pre-oxided samples were nitrided at 550°C with 8 ��� ! nitriding potential for three different times 14hours, 30 hours, and 45 hours (Bluewater Thermal Solutions, Reidsville, NC, USA) as shown in Figure 4. Figure 5 shows the schematic setup of the Report 1201 Page 5 gas nitriding process. The gas nitriding furnace is 48 inches in diameter and 96 inches in depth. The samples were heated up in nitrogen to the processing temperature before
Details
-
File Typepdf
-
Upload Time-
-
Content LanguagesEnglish
-
Upload UserAnonymous/Not logged-in
-
File Pages51 Page
-
File Size-