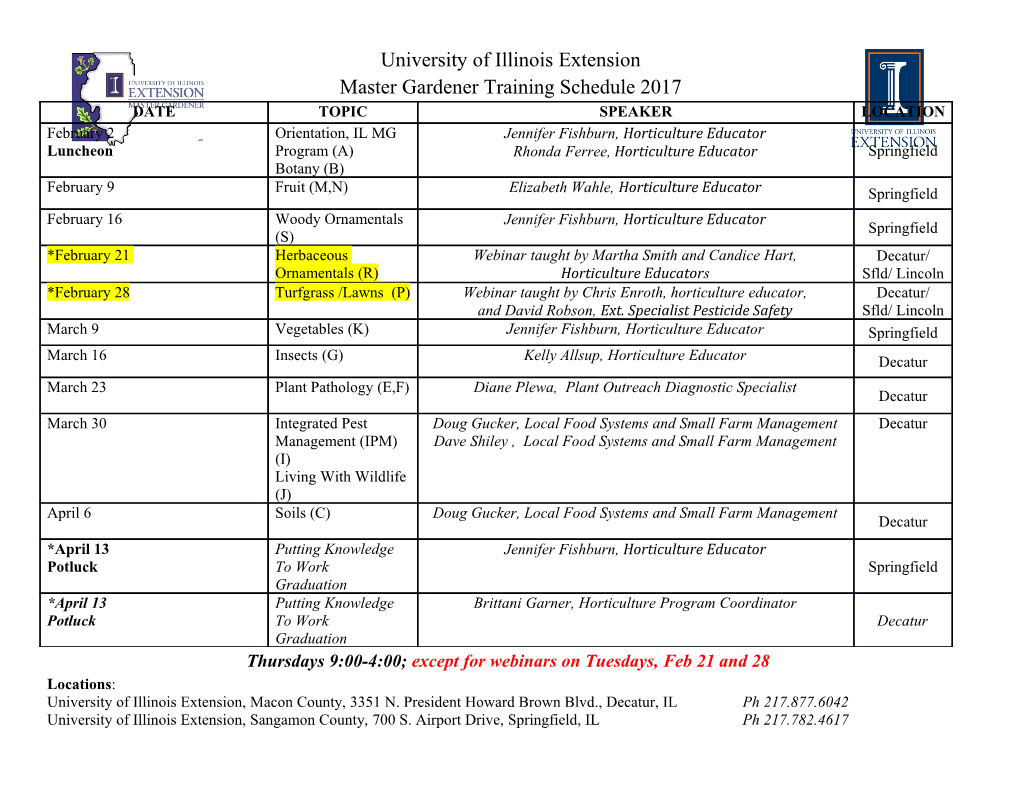
Journal of Composite Materials http://jcm.sagepub.com Surface Texture and the Stress Concentration Factor for FRP Components with Holes D. Arola and M. L. McCain Journal of Composite Materials 2003; 37; 1439 DOI: 10.1177/0021998303034462 The online version of this article can be found at: http://jcm.sagepub.com/cgi/content/abstract/37/16/1439 Published by: http://www.sagepublications.com On behalf of: American Society for Composites Additional services and information for Journal of Composite Materials can be found at: Email Alerts: http://jcm.sagepub.com/cgi/alerts Subscriptions: http://jcm.sagepub.com/subscriptions Reprints: http://www.sagepub.com/journalsReprints.nav Permissions: http://www.sagepub.com/journalsPermissions.nav Citations (this article cites 7 articles hosted on the SAGE Journals Online and HighWire Press platforms): http://jcm.sagepub.com/cgi/content/abstract/37/16/1439#BIBL Downloaded from http://jcm.sagepub.com at UNIV OF MARYLAND BALTIMORE CO on March 19, 2007 © 2003 SAGE Publications. All rights reserved. Not for commercial use or unauthorized distribution. Surface Texture and the Stress Concentration Factor for FRP Components with Holes D. AROLA* AND M. L. MCCAIN Department of Mechanical Engineering University of Maryland, Baltimore County 1000 Hilltop Circle, Baltimore, MD 21250, USA (Received June 25, 2002) (Revised January 8, 2003) ABSTRACT: The influence of hole quality on the mechanical behavior of fiber reinforced laminates was studied. Holes were introduced in tensile specimens of a graphite/epoxy (Gr/Ep) laminate using an abrasive waterjet and commercial drills (diamond coated tungsten carbide twist drills or tungsten carbide drill-reamers). The machined surfaces were characterized using contact profilometry and the surface texture was used in estimating the effective stress concentration factor (KKt). Utilizing the macroscopic stress concentration posed by the hole and KKt, the total stress concentration was estimated using the principle of superposition. The Gr/Ep specimens were then loaded in tension and acoustic emission was used to monitor the failure process. The apparent stress concentration factor (KtðappÞ) of the tensile specimens was determined from the ratio of tensile strengths of coupons without holes to that of specimens with holes. Based on results from tension tests the KtðappÞat first fiber failure ranged from 2.50 to 3.40. The stress concentration factors determined from experiments were within 6% of that predicted using superposition and KKt. Although the hole quality was dependent on the method of machining and drilling, results from this study confirm previous reports that there is no correlation between the surface texture and first fiber failure or ultimate tensile strength of Fiber Reinforced Plastics (FRPs) with open holes. Holes introduced using worn diamond coated twist drills exhibited the lowest surface roughness but resulted in a significant reduction in first fiber failure strength. Results from this study indicate that surface texture and KKt cannot be used for a reliable estimate of hole quality in FRPs, especially for holes produced with worn cutting tools. KEY WORDS: drilling, fiber reinforced plastics, hole, stress concentration, surface texture. *Author to whom correspondence should be addressed. E-mail: [email protected] Journal of COMPOSITE MATERIALS, Vol. 37, No. 16/2003 1439 0021-9983/03/16 1439–22 $10.00/0 DOI: 10.1177/002199803034462 ß 2003 Sage Publications Downloaded from http://jcm.sagepub.com at UNIV OF MARYLAND BALTIMORE CO on March 19, 2007 © 2003 SAGE Publications. All rights reserved. Not for commercial use or unauthorized distribution. 1440 D. AROLA AND M. L. MCCAIN INTRODUCTION IBER REINFORCED PLASTICS (FRPs) are used in the design of primary and secondary Fstructural components for a variety of applications. Component parts are molded to near net-shape and often require finish machining and secondary features to facilitate assembly. Adhesives, rivets, and bolts are used in joining FRP components but mechanical fasteners generally offer sustained reliability [1–4]. Therefore, postmold drilling is by far the most common machining process used in the development of FRP structures [2,5,6–9]. Several problems have been reported in drilling FRPs including entrance and exit ply delamination, matrix depletion, tool wear, and fiber pullout [5,7,9–13]. Inferior hole quality accounts for an estimated 60% of all part rejections and represents a costly manufacturing concern [14]. In addition to the economic burden, drilling damage may reduce the component’s strength. Delamination, waviness and roughness of the holes interior, axial curvature, and roundness errors may influence the mechanical behavior of laminates with holes [6–8,14–16]. While considerable effort has been placed on establishing drilling parameters that minimize damage, the influence of hole quality on part performance has received less attention. According to experimental results Wood [17] postulated that hole quality does not affect the ultimate strength of FRPs. Similarly, Tagliaferri et al. [18] concluded that the tensile strength of polymer composites with open holes was not affected by the hole quality whereas the bearing strength was. Persson et al. [19] found that while the compressive strength of carbon/epoxy laminates was not dependent on the hole quality the monotonic and fatigue strength was significantly reduced under pin loading. Though experimental studies have concluded that there is no effect of surface texture on the tension or compression behavior of FRP laminates with open holes, the effects of hole quality on the strength of FRPs cannot be disregarded. The influence of surface texture and surface integrity of holes on the mechanical behavior of component parts must be considered in a thorough design evaluation. The primary objectives of this study were to quantify the influence of hole quality on the tensile properties of FRP components with open holes and to evaluate an analytical approach to account for hole quality in design. A simple methodology is presented to account for hole quality on the strength of FRP components with drilled and machined holes. The approach is evaluated through a comparison of predictions with experimental results. BACKGROUND The influence of machining and the resulting machined edge quality on the mechanical behavior of component parts is a concern that accompanies the development of all new structural materials. Machined edge quality comprises the surface texture, surface integrity and process dependent defects that result from material removal. The surface texture describes external features of the machined surface geometry (e.g. lay and roughness) while the surface integrity encompasses subsurface qualities (e.g. heat affected zone, subsurface cracks, fiber pullout, etc). Downloaded from http://jcm.sagepub.com at UNIV OF MARYLAND BALTIMORE CO on March 19, 2007 © 2003 SAGE Publications. All rights reserved. Not for commercial use or unauthorized distribution. Surface Texture and the Stress Concentration Factor for FRP Components 1441 Machined Edge Effects The effects of machined edge quality on the strength and stiffness of FRPs without holes has been studied in detail. An early study of machined edge quality compared the effects of laser machining and abrasive waterjet (AWJ) machining on the strength of several FRP laminates [20]. Though laser machining was found to be detrimental to the tensile strength, there was no degradation in strength resulting from AWJ machining. Colligan and Ramulu [21] evaluated the ultimate compression strength of graphite/epoxy (Gr/Ep) laminates machined using diamond abrasive cutters and found that the strength decreased with increasing surface roughness. However, the reduction in strength resulting from edge ply delamination was more significant than the effects of surface roughness. The influence of machining defects and edge quality on the strength of FRPs has also been examined under quasi-static and dynamic flexure [22,23]. In an evaluation using Gr/Ep and graphite bismaleimide (Gr/Bmi) laminates the flexure strength was found to be significantly dependent on the manufacturing process, surface texture and surface integrity. Laminates trimmed with single-point cutting tools underwent the largest reduction in strength due to subsurface damage that was introduced in off-axis plies [23]. Net-shape machining, surface texture and their influence on the fatigue behavior of Gr/Bmi laminates have also been evaluated under fully reversed flexural fatigue loading [24]. At two different amplitudes of cyclic loading it was found that the reduction in stiffness increased with the machined edge surface roughness. A complete review of machined edge effects in composite materials is presented in [25]. Based on results from past studies on edge effects, the quality of drilled holes is expected to affect the mechanical behavior of FRPs with open holes. An analytical treatment of holes must consider the effects of edge quality and the change in stress distribution posed by the macroscopic notch. Notches and Holes The influence of notches and holes on the mechanical behavior of FRP materials has been approached using linear elastic fracture mechanics (LEFM) and stress concentration factors. In fact, several models have been proposed for estimating the strength of composite materials with holes [26–29]. A comprehensive review of notches in composite materials and their treatment is available in [30]. The primary objective
Details
-
File Typepdf
-
Upload Time-
-
Content LanguagesEnglish
-
Upload UserAnonymous/Not logged-in
-
File Pages23 Page
-
File Size-