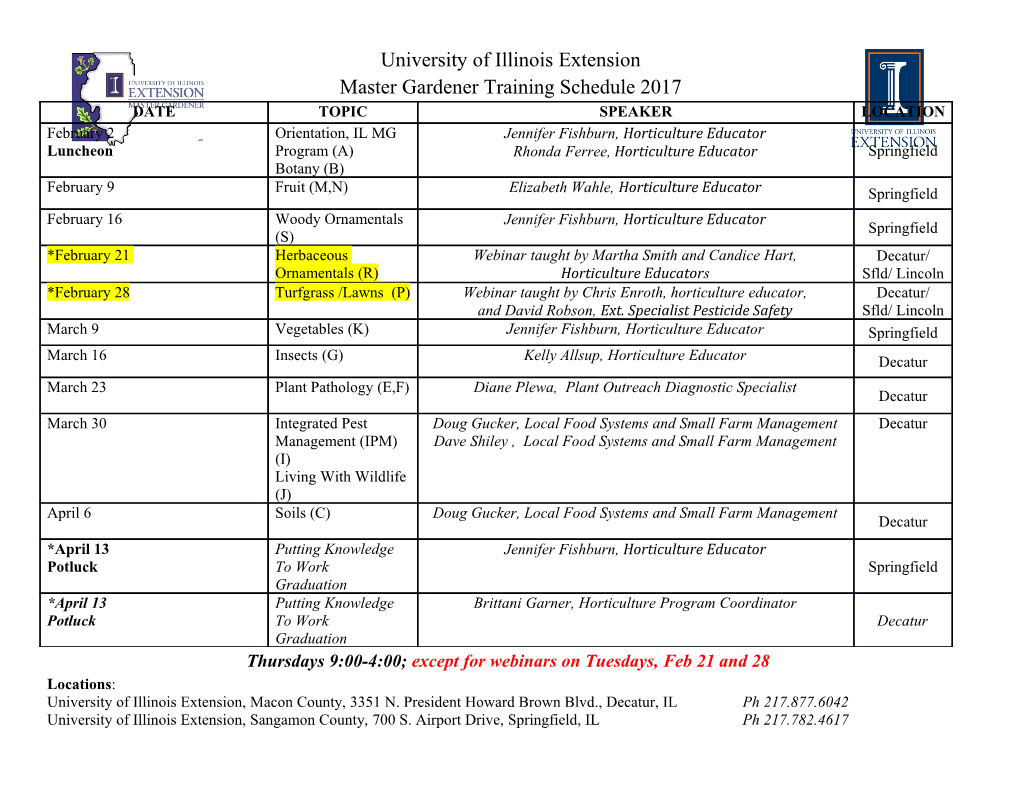
INDUCTION HARDENING OF GEARS OFFERS VARIOUS APPROACHES Fast, clean, highly nduction hardening offers a must when considering the method. practical alternative technique to Hardening under a quench press repeatable, and thermochemical methods such (die quenching) is used when very inexpensive when as carburizing or carbonitriding strict tolerances are required in the I to improve the mechanical prop- part design and need to be obtained properly sized for the job, erties of gears. Advancements in gear after the hardening operation. The induction heating offers a materials and the development of best approach is to use a press with new induction heating simulation specific dies. Depending on part de- desirable production and prediction tools have led to im- sign and accuracy requirements, the solution for gear proved induction systems that ex- press can use single or multiple dies tend the induction hardening process (Fig. 2). hardening regardless of capability to include very demanding The balance of the article will re- part size and geometry. gear configurations. This article de- view other gear hardening technolo- scribes the various induction proc- gies, focusing on whole gear hard- esses for hardening gears. ening processes. Induction hardening can meet pro- Fabien Marquis Hardening methods duction needs in processing a range Dr. Hans Stiele Interest in using induction hard- of gears designs, from small EFD Induction GmbH ening of gears continues to increase sprockets to very large gears used in Freiburg, Germany as process capabilities advance with transmissions. Two main concepts the development of larger power are to harden only the gear tooth or sources for manufacturing facilities. part of it (only where the tooth makes At the same time, users want faster contact, for example) and to harden and more flexible and repeatable the entire gear circumference in- hardening solutions. Hardening with cluding the tip and root of each tooth or without specific tooling were the (Fig. 3). Other considerations such as two main methods for hardening. gear size, module, production rate, Hardening methods using quench power availability influence the tooling include an operation using a choice of the process. specific tool and an operation under a quench press (die quenching). Tooth-by-Tooth Hardening Hardening using a specific tool is This technique is commonly used used with components where dimen- to harden flanks and/roots; for ex- sional tolerances are very ample, large sprockets such as those tight. A simple OD or ID found in off-road equipment, or ring calibration tool (Fig. 1) gears found in transmissions. In the keeps dimensions within process, the coil comes onto the tooth an acceptable range. to harden root and flanks, or flanks The process is simple to and tip. Possible approaches are integrate into induction single shot and scanning operations. machines and provides a Some processing, such as the so- quick solution when called NATCO approach, performs simple distortion needs the hardening operation under water, to be corrected. How- which minimizes the distortion re- ever, die hardening is sulting from the transformation. Fig. 1 — Example of tooling used in gear hardening. not an easy technique, and experi- A current method used for large ence and know-how are definitely a gears (e.g., slewing rings) uses more 22 HEAT TREATING PROGRESS • JULY 2007 Fig. 2 — Examples of quench-die configurations. Fig. 3 — Tooth by tooth hardening. measuring devices, which make it possible to guarantee a perfect loca- tion of the coil vs. the part even when part is not well centered. This also provides the necessary process re- peatability. The air gap between coil and tooth must be constant during the heating process, but more important is the re- peatability of positioning from one tooth to another. To achieve regular control using measuring probe, a CNC axis gives the best result. Other solutions used to ensure a constant gap between coil and tooth flanks and/or root include mechanical when using a contact probe in neigh- boring teeth and ground-fault detec- tion in connection with the control system (CNC or PLC) giving a set Fig. 4 — Classification of the different gear spin-hardening methods. point when approaching the root of ferent heating techniques for induc- the tooth. tive gear spin hardening. Gear Spin Hardening Through Hardening on Gear Teeth In spin hardening, the entire gear For gears that are predominantly is brought up to the austenitizing subject to wear (e.g., sprockets), the temperature via an encircling coil tooth is through hardened using a and subsequently quenched, which relatively low specific power [2]. If the allows either through hardening of frequency is too low, there is the risk the gear down to the tooth root (sim- that beyond the Curie temperature ilar to case hardening) or hardening (point where the material changes the outer surface at a uniform or ir- from magnetic to nonmagnetic) the regular distance from the face. Figure induced eddy current largely flows 4 shows different methods for con- only in the root circle, and the tem- Fig. 5 — Hardened pattern on submerged- tour hardening corresponding to dif- perature of the tooth lags behind. hardened gear. HEAT TREATING PROGRESS • JULY 2007 23 Quenching for through hardening can be either submersion or spraying depending on the material [3]. De- pending on factors from the module to the frequency, it is recommended to delay the quenching sequence to achieve a uniform temperature be- tween the tooth and the root circle. Tempering after through hardening is essential for crack prevention. An example of a submerged hardened gear is shown in Fig. 5. Fig. 6 — Time-temperature profile of Gear Hardening on Tooth Perimeter Fig. 10 — Example of gear hardened using single-frequency contour hardening with in- (Contour or No Contour) two separate frequencies. duction preheating. When hardening at an irregular working frequency is higher rather distance from the tooth face, or (ide- than lower for the given module. ally) at a uniform distance from the If the frequency is higher than in tooth face, one can choose between the ideal case, it is possible to heat the the single frequency concept (SFC), root circle by means of thermo-con- in which an single frequency power duction during the preheating phase supply is used, and the dual fre- to subsequently achieve hardening quency method (including multiple results at an irregular distance from frequency concept, or MFC) using the face with a final heating impulse Fig. 7 — Hardened pattern on single-fre- two frequency levels (either simul- using a high specific power (Fig. 7). quency hardened gear taneously or not). On the other hand, if the generator frequency is too low for a given Single Frequency Concept module, through hardening of the In the process, the inductor is fed tooth or an inadequate austenitizing from a single power supply using a temperature of the tooth tip is un- frequency selected according to the avoidable for physical reasons. In ad- module. Heating (austenitizing) is dition, if the initial microstructure is done either via single shot in one step not suitable for gear hardening, fur- or with preheating using reduced ther improvement in the hardening power to reach a temperature be- result may be achieved via induction tween 550 to 750°C (1020 to 1380°F) initial hardening and tempering op- and subsequent final heating using erations before the actual hardening a higher specific power to the hard- itself. For this, heating of the entire ening temperature. Preheating can gear area to an austenitizing temper- Fig. 8 — Time-temperature profile of also consist of several pulsed cycles. ature corresponding to the material single-frequency contour hardening, prehard- The purpose of preheating is to reach is carried out. Cooling by self- ened and tempered by induction. an adapted high austenitizing tem- quenching (mass quenching) is fol- perature in the root circle during final lowed by a short inductive tem- heating, without overheating the pering of the entire gear. The actual tooth tip. The schematic principle can hardening zone at an irregular dis- be seen in Fig. 6. To achieve hard- tance from the face is then generated ening profiles at an irregular distance by a short final heating. The from the tooth face using a single fre- schematic time-temperature graph quency, short heating times com- for single frequency contour hard- bined with a high specific power is ening, prehardened, and tempered usually required. Both parameters by induction, is shown in Fig. 8. (time and power) depend on the hardened gear module. Dual-Frequency Methods It is not always certain that the user Dual-frequency hardening using has the optimum power supply with separate frequencies allows achiev- Fig. 9 — Time-temperature profile of dual- respect to available frequency, or ing hardening profiles similar to frequency contour hardening with induction whether it can be correspondingly those achieved using case hardening. preheating. adjusted. In this case, better results Two different frequencies, one after can be achieved for contour hard- the other, are applied to the gear. The ening using a generator in which the tooth part is preheated (depending 24 HEAT TREATING PROGRESS • JULY 2007 Fig. 11 — Time-temperature profile of Fig. 12 —General principle of the multiple frequency concept, or MFC. dual-frequency contour hardening, pre- quenched and tempered by induction. on the material) using a low fre- quency and limited power to a tem- perature between 550 and 750°C. The frequency should be such that the preheating preferably takes place in the root circle region. After a short delay, austenitizing using a higher frequency and higher power density is then provided. Heating times are measured in tenths of seconds or seconds (depending on the module Fig. 13 —Example of MFC application on and gear thickness/length) in this a gear.
Details
-
File Typepdf
-
Upload Time-
-
Content LanguagesEnglish
-
Upload UserAnonymous/Not logged-in
-
File Pages6 Page
-
File Size-