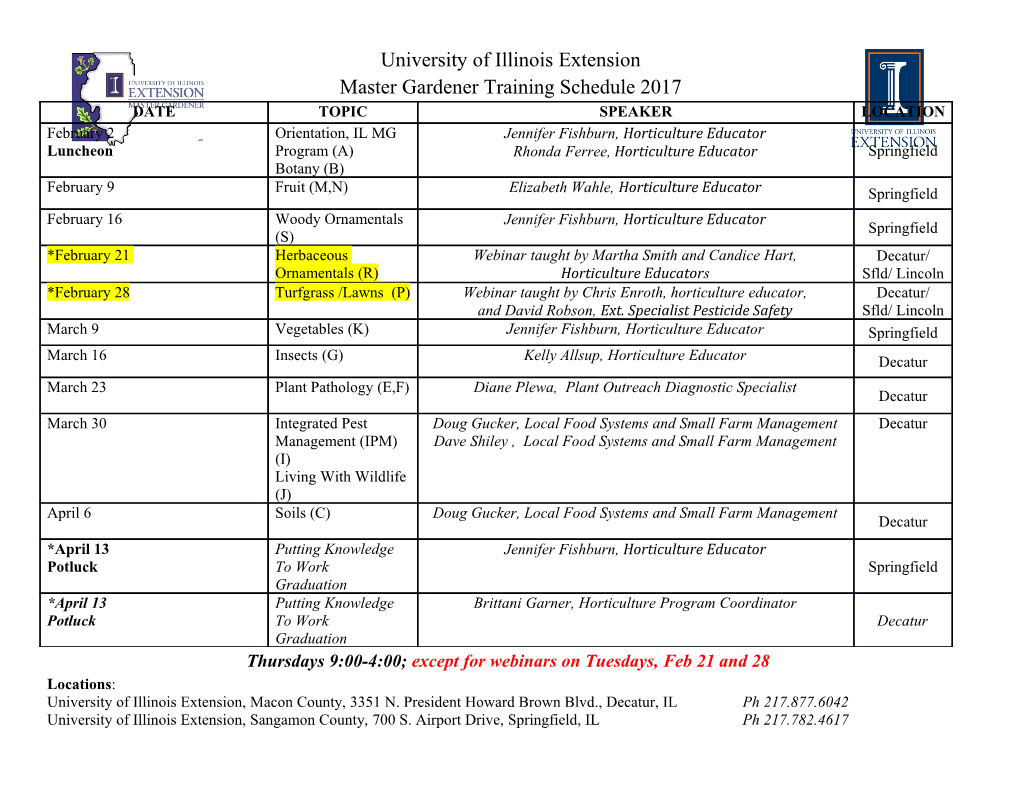
energies Article Study on Insulation Breakdown Characteristics of Printed Circuit Board under Continuous Square Impulse Voltage Quan Zhou 1, Mingqian Wen 1,* , Taotao Xiong 2, Tianyan Jiang 3, Ming Zhou 1, Xi Ouyang 1 and Lai Xing 1 1 State Key Laboratory of Power Transmission Equipment & System Security and New Technology, School of Electrical Engineering, Chongqing University, Chongqing 400044, China; [email protected] (Q.Z.); [email protected] (M.Z.); [email protected] (X.O.); [email protected] (L.X.) 2 State Grid Chengdu Power Supply Company, Chengdu 610000, China; [email protected] 3 School of Electrical and Electronic Engineering, Chongqing University of Technology, Chongqing 400050, China; [email protected] * Correspondence: [email protected]; Tel.: +86-136-784-20200 Received: 22 September 2018; Accepted: 23 October 2018; Published: 25 October 2018 Abstract: The widely distributed interconnects in printed circuit boards (PCBs) easily couple with high voltage under the action of electromagnetic pulses, which leads to insulation failure. In this study, the dielectric breakdown characteristics of four typical PCBs are studied under continuous square impulse voltage conditions. First, the electric field distribution in the four electrode models is simulated with the ANSYS software (ANSYS Maxwell 17.0). Electric field simulation results show the weak area of electric field distribution. On this basis, the possible breakdown patterns of PCB are analyzed. Second, the influence of factors, such as temperature, pulse duty ratio, interconnect insulation distance, and air pressure, on PCB breakdown voltage is studied through a breakdown test on the PCBs. Results show that the discharge between the single-layer electrodes of the PCBs is surface discharge, and the breakdown is that of a “gas–solid composite medium”. Meanwhile, the breakdown of a double-layer PCB is solid breakdown. Finally, scanning electron microscopy (SEM) produced by Tescan (Brno, Czech Republic) is performed to study the carbonization channel after PCB breakdown. SEM results reveal that the PCB carbonization channel is influenced by temperature and pressure in varying degrees. Keywords: PCB; continuous square impulse voltage; electric field simulation; breakdown test; SEM 1. Introduction With the development of high-density, high-integration, multi-function power electronic equipment, the insulating medium between metal tracks and layers on printed circuit boards (PCBs) is facing increasingly severe insulation problems [1]. Moreover, on PCBs in spacecraft power systems, microwave weapons, and other fields, the insulating medium is affected by severe external factors, such as high temperature, low pressure, and electromagnetic pulse interference. Research has shown that high-power electromagnetic pulses can easily couple the metal interconnects in PCBs with high voltages, which can reach nearly thousands of volts, resulting in insulation failure [2,3]. Thus, the influence of PCB insulation design, external environment, electric field form, and other factors on the insulation characteristics of PCBs should be studied systematically to provide theoretical guidance for insulation design and protection. The waveform of electrostatic discharge (ESD), which causes PCB insulation failure in actual operation, is randomly formed. This waveform includes sine, saw tooth, and attenuation sine waves. The insulation damage caused by ESD is thus difficult to simulate Energies 2018, 11, 2908; doi:10.3390/en11112908 www.mdpi.com/journal/energies Energies 2018, 11, x FOR PEER REVIEW 2 of 13 Energies 2018, 11, 2908 2 of 13 tooth, and attenuation sine waves. The insulation damage caused by ESD is thus difficult to simulate directly. At present, the method of device damage threshold in the National Army Standard [4] injects squaredirectly.-wave At present,pulses into the device methods. ofReference devices damage [5,6] show thresholded that in the the breakdown National Army characteristics Standard of [4 ] integratedinjects square-wave electronic devices pulses into under devices. ESD and References those under [5,6 ]continuous showed that square the breakdown-wave pulse characteristics voltages can beof equivalent. integrated electronicIn addition, devices continuous under s ESDquare and-wave those pulse under voltage continuous can be used square-wave to simulate pulse the voltagesimpact ofcan PCB bes equivalent.caused by ESD. In addition,On the basis continuous of these research, square-wave continuous pulse voltage square- canwave be pulse used voltage to simulate was adoptedthe impact in this of PCBs study caused to simulate by ESD. the On dielectric the basis breakdown of these research, characteristic continuouss of PCB square-waves in a complex pulse environment.voltage was adopted in this study to simulate the dielectric breakdown characteristics of PCBs in a complexThe dielectric environment. breakdown characteristics of PCBs under square-wave pulse voltage have been studiedThe by dielectric scholars. breakdownReference [7] characteristics compared the of influence PCBs unders of temperature, square-wave insulation pulse voltage distance have, beenand pulsestudied width by scholars.on PCB charge Reference accumulation [7] compared and the failure influences time at of atmospheric temperature, and insulation low pressure distance,s. Referenceand pulses [8 width,9] present on PCBed chargethe effect accumulation of salt spray and concentration failure time on at atmosphericthe discharge and characteristics low pressures. of PCBReferencess and indicate [8,9] presentedd that fog the conductivity effect of salt sprayaffects concentration the discharge on energy the discharge of PCBs characteristics. By using the of maximumPCBs and indicatedlikelihood that method fog conductivity to fit the Weibull affects parameters the discharge of energyPCB breakdown of PCBs. By field using strength, the maximum Meng [10]likelihood obtained method the cumulative to fit the Weibull probability parameters distribution of PCB and breakdown fitting curve field of strength, a PCB Mengunder [ 10continuous] obtained squarethe cumulative-wave pulse probability voltage condition distributions. and fitting curve of a PCB under continuous square-wave pulseIn voltage consideration conditions. of the actual insulation structure of a PCB, four typical PCB electrode models were designedIn consideration in this study of the. The actual electric insulation field distribution structure of of a the PCB, four four electrode typical models PCB electrode was simulated models andwere examined designed with in this the study. ANSYS The software electric to field analyze distribution the weak of insulation the four electrode area and models possible was breakdown simulated patternsand examined of the withPCBs the. The ANSYS effects software of temperature, to analyze pulse the weakduty insulationratio, interconnect area and insulation possible breakdown distance, airpatterns pressure of, the and PCBs. breakdown The effects times of on temperature, the breakdown pulse voltage duty ratio, of the interconnect four electrode insulation models distance, were studiedair pressure, through and experiments breakdown times in view on theof the breakdown practical voltageinsulation of the problems four electrode caused models by severe were exte studiedrnal factorsthrough in experimentscomplex environments in view of the. Then practical, the change insulation in the problems morphology caused of byinsulating severe external polymer factors media in betweencomplex PCB environments. electrodes Then,on the the surface change was in the observed morphology and analyzed of insulating through polymer scanning media electron between microscopyPCB electrodes (SEM on) theto explain surface the was formation observed mechanism and analyzed of throughthe carbon scanningization electron channel microscopy in the process (SEM) of PCBto explain breakdown the formation. mechanism of the carbonization channel in the process of PCB breakdown. 2.2. Electrode Electrode Model Model Design Design and and Simulation Simulation Analysis Analysis TheThe designed designed PCB PCB electrode electrode model modelss are are shown shown in in Figure Figure 1.1. The The electro electrodede structures structures designed designed by by modelmodelss ( (a),a), ( (b),b), and (c)(c) werewere placed placed on on a single-layera single-layer PCB. PCB Considering. Considering that that the commonthe common wiring wiring in PCBs in PCBis parallels is parallel wiring, wiring, we used we thisused type this in type the correspondingin the corresponding design modeldesign shown model in shown Figure in1a. Figure The “arc” 1a. Thestructure “arc” structure at the two at ends the two ofthe ends parallel of the parallel interconnect interconnect can effectively can effectively avoid the avoid “edge the effect”“edge effect caused” causedby the by concentration the concentration of the electricof the electric field at field the endat the and end ensure and ensure that breakdown that breakdown occurs occurs in the in region the regionbetween between the two the parallel two parallel lines when lines the when square-wave the square pulse-wave voltage pulse is voltage injected. is Meanwhile, injected. Meanwhile the corners, thein acorner PCB layouts in a arePCB usually layout obtuseare usually or chamfered obtuse or to chamfered avoid unnecessary to avoid radiation. unnecessary The radiation. corresponding The correspondingdesign model fordesign this ismodel
Details
-
File Typepdf
-
Upload Time-
-
Content LanguagesEnglish
-
Upload UserAnonymous/Not logged-in
-
File Pages13 Page
-
File Size-