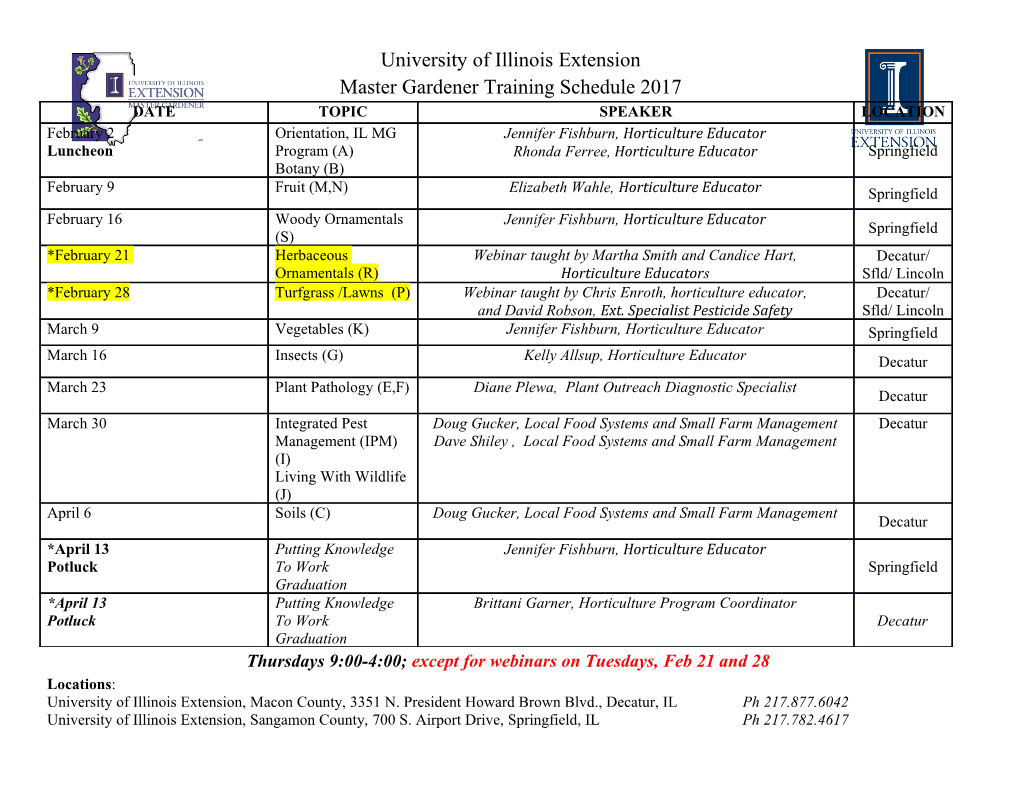
Journal of the Ceramic Society of Japan 129 [3] 187-194 2021 -Japan DOI http://doi.org/10.2109/jcersj2.20211 JCS FULL PAPER Fabrication and mechanical properties of boron nitride nanotube reinforced boron carbide ceramics Bingsai LIU1,2, Yuanping GU3, Yuchun JI1,2, Guoyuan ZHENG1,2, Jilin WANG1,2,³,YiWU1,2, Fei LONG1,2,‡ and Bing ZHOU1,2 1 School of Materials Science and Engineering, Key Laboratory of New Processing Technology for Nonferrous Metals and Materials of Ministry of Education, Guilin University of Technology, Guilin 541004, China 2 Guangxi Key Laboratory of Optical and Electronic Materials and Devices, Guilin University of Technology, Guilin 541004, China 3 Affiliated Stomatological Hospital, Guilin Medical University, Guilin 541004, China A series of boron nitride nanotubes (BNNTs)/ boron carbide (B4C) composite ceramics were prepared using spark plasma sintering (SPS) technology, which uses B4C powders as the matrix and BNNTs as the toughening phase. X-ray diffraction (XRD) and scanning electron microscope (SEM) were then used to characterize the B4C ceramic samples. The effects of the sintering temperature, the BNNTs content, and the matrix particle size on the microstructure and mechanical properties of the B4C composite ceramics were investigated in detail. The experimental results showed that the ceramic samples obtained by adding a 5 wt % BNNTs content sintered at 1750 °C displayed the best mechanical properties. The relative density, microhardness, and fracture toughness were 99.41 %, 32.68 GPa, and 6.87 Mpa·m1/2, respectively. The fracture toughness was 54.59 % higher than that of the composite without the BNNTs. The toughening mechanism of the BNNTs was also studied. The pulling-out of the BNNTs, bridging, and crack branch contributed to the toughness property of the B4C-based ceramic. ©2021 The Ceramic Society of Japan. All rights reserved. Key-words : Boron carbide, Boron nitride nanotubes, Spark plasma sintering, Mechanical property, Toughening mechanism [Received November 20, 2020; Accepted December 10, 2020] toughness. These issues limit further improvements of its 1. Introduction mechanical properties and greatly limit the application 9) Boron carbide (B12C3 or B4C) is a type of light oxide range of B4C ceramics as structural ceramics. solid material, and its single hexahedron diamond crystal Currently, particle toughening and whisker (fiber) cell contains 15 atoms. The composition is a B11C icosa- toughening are effective methods to improve the fracture hedron and a linear C-B-C three atomic chain, both of toughness of ceramics. Baris et al. used spark plasma which have a covalent bond connection to form a stable sintering (SPS) technology to prepare CNTs/B4C ceramic structure.1),2) The highly stable covalent bond between the composites using carbon nanotubes (CNTs) as a toughen- 10) B and C atoms in B4C and its special crystalline structure ing phase. The results showed that the addition of CNTs makes B4C have many excellent physical and chemical or increasing the heating rate improved the fracture tough- properties, such as low density, high hardness, a high melt- ness of the B4C ceramics. In recent years, some studies ing point, high temperature wear resistance, a low thermal have found that BNNTs displayed better comprehensive expansion coefficient, and good thermoelectric perform- mechanical properties, chemical stability, and oxidation ance, among other properties.3)­6) These properties make resistance than CNTs, making them an ideal toughening 11),12) B4C have broad application prospects in high-performance material. Zeng et al. studied the microstructure and engineering ceramics, composite armor, body armor, and mechanical properties of BNNTs/B4C composite ceramics other national defense and military industry products. It is using the hot pressing (HP) sintering process. The results an important strategic material in today’s national econ- showed that the bending strength and fracture toughness omy and for national defense.7),8) However, the high of the composite with the 1.5 wt % BNNTs increased by 28 13),14) covalent bonds of the B4C content and high melting point and 31.5 %, respectively. However, Zeng’s work had results in B4C ceramic sintering difficulties and poor the following shortcomings. (1) The B4C raw material powder used in this work was at the micron level, with ³ Corresponding author: J. Wang; E-mail: jilinwang@glut. large particles, low powder sintering activity, and high sin- edu.cn tering densification temperature (2050 °C). (2) This work ‡ Corresponding author: F. Long; E-mail: [email protected] used the traditional HP sintering process to prepare the ©2021 The Ceramic Society of Japan 187 This is an Open Access article distributed under the terms of the Creative Commons Attribution License (https://creativecommons.org/licenses/by-nd/4.0/), which permits unrestricted use, distribution, and reproduction in any medium, provided the original work is properly cited. JCS-Japan Liu et al.: Fabrication and mechanical properties of boron nitride nanotube reinforced boron carbide ceramics Fig. 1. The typical SEM images of (a) commercial B4C, (b) homemade B4C and (c), (d) homemade BNNTs. BNNTs/B4C composite ceramics. The sintering cycle of the sintering process is long, and the long-term heat pre- 2. Experimental section servation (1 h) at a high temperature promotes the growth 2.1 Experimental reagents of B4C crystal grains. This results in the inability to The commercially available micron-sized B4C powders improve the mechanical properties of the B4C ceramic were purchased from the Mudanjiang Boron Carbide Co., products further, and the product density is low. However, PR China [particle size of approximately 3.5 ¯m, purity compared with HP sintering technology, SPS sintering >95 %, Fig. 1(a)]. In addition, the B4C nano-powders technology has the advantages of a fast heating speed, [particle size of approximately 100 nm prepared using the short sintering time, and low sintering temperature. In SHS-RC method, purity >99 %, Fig. 1(b)]15) and the addition, due to the combined effect of plasma activation BNNTs [these nanotubes had a bamboo-like structure with and rapid heating sintering, the growth of crystal grains is uniform diameters approximately 90 nm and lengths of inhibited, and the microstructure of the original particles is more than 10 ¯m prepared using the self-propagating high- maintained. Hence, the performance of the sintered body is temperature synthesis method, as shown in Figs. 1(c) and essentially improved, and it is more conducive to obtaining 1(d)16),17)] were homemade in the laboratory. high dense boron carbide ceramics. Therefore, in 2016, our research group prepared high-activity B4C nano-powders 2.2 Preparation of the BNNTs/B4C composite by coupling the self-propagating high temperature syn- ceramics thesis method (SHS-RC) to prepare high-density B4C The raw materials and pre-heat treatment consisted of ceramics (the relative density reached 99.8 %) using SPS the following. First, the B4C and BNNTs were mixed at a 15) technology and B4C nano-powders as raw materials. certain proportion. The mixture was then put into a mix- However, this work did not explore the strengthening of ing tank and ground for 6 h. Finally, the obtained mixture the toughening of the B4C ceramic. was pickled using hydrochloric acid (12 mol/L, 20 ml, to Therefore, in this study, high performance BNNTs/B4C remove impurities), water washed, ethanol washed, suc- composite ceramics are prepared using SPS low- tion filtrated, and vacuum dried and stored. temperature rapid sintering technology with high-activity The SPS procedure consisted of taking the mixture out homemade B4C nano-powders on the basis of the previous of the vacuum drying oven, weighing an appropriate work. The influences of the sintering temperature, BNNTs amount of the mixture and grinding for 15 min, and then content, and matrix particle size on the microstructures and placing the ground mixture into a graphite mold with a mechanical properties of B4C composite ceramics are diameter of 15 mm for the SPS. The temperature, heating investigated. In addition, the toughening mechanism is rate, sintering atmosphere, sintering pressure and the hold- also investigated in detail. ing time were 1700 °C, 200 °C/min, vacuum-sintering, 30 188 Journal of the Ceramic Society of Japan 129 [3] 187-194 2021 JCS-Japan Table 1. Experimental technical parameters of the sample B C content/wt % Sintering Formulation B C types 4 4 BNNTs content/wt % temperature/°C S1 C-B4C 100 0 1700 S2 C-B4C 95 5 1700 S3 C-B4C 90 10 1700 S4 H-B4C 100 0 1700 S5 H-B4C 95 5 1700 S6 H-B4C 90 10 1700 S8 H-B4C 95 5 1600 S9 H-B4C 95 5 1750 S10 H-B4C 95 5 1800 MPa, and 5 min, respectively. After the sintering, the graph- ite layer on the surface of the sintered sample was Fig. 2. XRD patterns of B4C samples fabricated by sintering at removed, then polished, ultrasonically cleaned and dried 1700 °C with different content of BNNTs (wt %). to perform related test and characterization. The experi- mental technical parameters are shown in Table 1. amorphous carbon contained in the H-B4C powders was 2.3 Characterization transformed into crystalline carbon (graphite) under high- The microstructure of the BNNTs powders, B4C pow- temperature conditions. ders, and fracture surfaces of the ceramic bulk sample was The fracture morphologies of the ceramic samples with characterized using a scanning electron microscope (SEM, different ceramic matrices and different BNNTs contents FEI Quanta FEG 250 and Hitachi S-3400). The sample are shown in Fig. 3. It can be seen from Fig. 3 that all the preparation process consisted of sticking the powders or sample sections showed low porosities and high densities. block sample directly on the conductive tape and then It can be seen from Fig. 3(a) that there were some pores of spraying with platinum.
Details
-
File Typepdf
-
Upload Time-
-
Content LanguagesEnglish
-
Upload UserAnonymous/Not logged-in
-
File Pages8 Page
-
File Size-