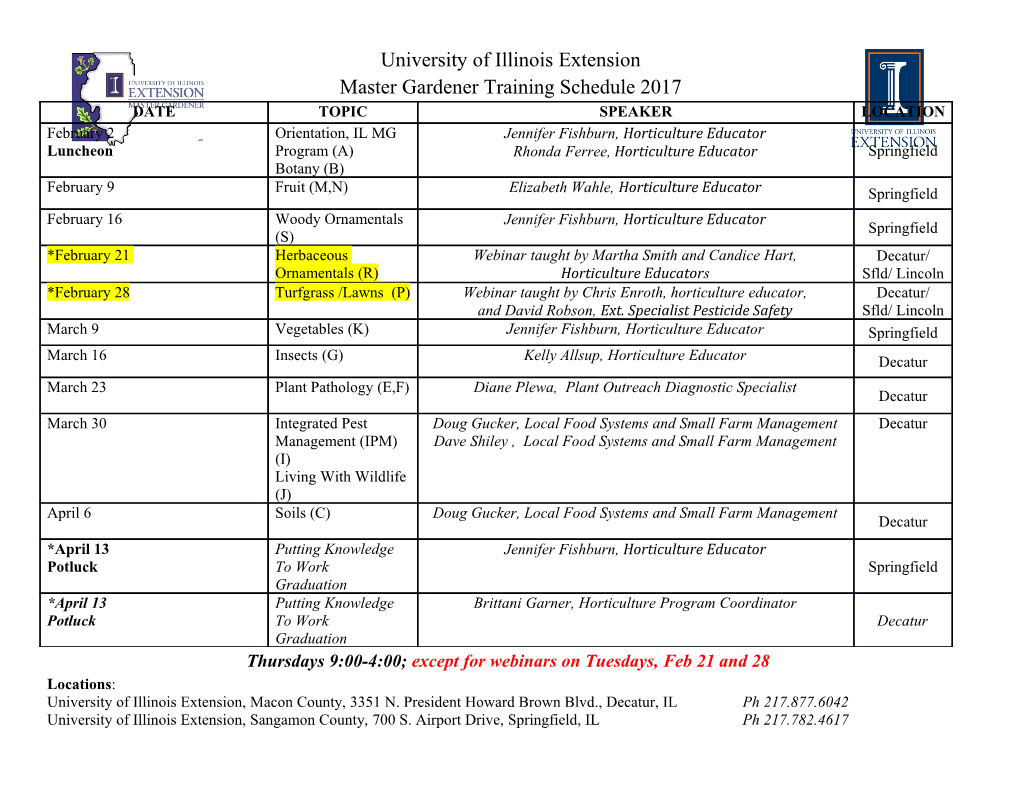
actuators Article Effect of Optimal Placement of Permanent Magnets on the Electromagnetic Force in the Horizontal Direction Yasuaki Ito 1, Yoshiho Oda 1, Takayoshi Narita 2,* ID and Hideaki Kato 2 1 Course of Mechanical Engineering, Tokai University, Kitakaname 4-4-1, Hiratsuka-shi, Kanagawa 259-1292, Japan; [email protected] (Y.I.); [email protected] (Y.O.) 2 Department of Prime Mover Engineering, Tokai University, Kitakaname 4-4-1, Hiratsuka-shi, Kanagawa 259-1292, Japan; [email protected] * Correspondence: [email protected]; Tel.: +81-463-58-1211 Received: 15 June 2018; Accepted: 24 August 2018; Published: 29 August 2018 Abstract: The surface quality of steel plates is deteriorated as they contact rollers while being conveyed during manufacturing processes. To solve this problem, we previously proposed a hybrid electromagnetic levitation system comprising electromagnets, permanent magnets, and a horizontal positioning control system for steel plates. Moreover, to increase stability, we proposed integrating these levitation systems. In this study, we aim to determine the optimal placement of permanent magnets in the levitation system to suppress the deflection of a levitated steel plate for cases where the magnetic field in the horizontal direction changes. Using a genetic algorithm, the optimal gap, number, and placement of permanent magnets in the system are obtained. Keywords: magnetic levitation; genetic algorithm; permanent magnet 1. Introduction Permanent magnets can generate constant attractive force and are actively used in various industrial fields. Several studies on electromagnetic levitation technology for ferromagnetic objects have been performed focusing on this feature [1]. In the current steel plate production line, transportation is achieved by contact conveyance by rollers. However, the surface of the steel plate is damaged by this method, and the surface quality of the steel plate deteriorates. With non-contact magnetic levitation transport using the electromagnet proposed by us, these problems can be prevented. These studies consider using the attractive force generated by permanent magnets as a constant suspension force for levitation [2,3]. Although this technology is expected to be applied in the production of high-surface-quality steel plates, the thickness of the steel plate must be decreased to reduce its weight. A steel plate with reduced flexural rigidity owing to its thinness is difficult to levitate in a conventional magnetic levitation system because of exciting elastic vibration. To solve this problem, we proposed a hybrid electromagnetic levitation system for thin steel plates where permanent magnets are installed around electromagnets for levitation [4]. This system can suppress the elastic vibration of levitated steel plates by generating an attractive force on the entire surface of the steel plate using electromagnets and permanent magnets [5]. However, the number of arrangement patterns of the permanent magnets is very enormous, and it is difficult to experimentally obtain a more effective arrangement. Therefore, we focused on genetic algorithm (GA) which is one of optimization algorithms effective for nonlinear objective function [6], which is used to obtain optimum shape of electrical motor in several studies [7,8]. Furthermore, we confirmed that the GA we used to obtain the optimal placement of permanent magnets, considering the interactions of the magnets with each other, improved the levitation stability of the system [9,10]. In addition, we proposed adding another Actuators 2018, 7, 54; doi:10.3390/act7030054 www.mdpi.com/journal/actuators Actuators 2018, 7, x FOR PEER REVIEW 2 of 10 controls to the electromagnetic levitation system using vertical electromagnets for levitation [7]. This system generates tension on the edge of the steel plate due to the electromagnetic field generated by the horizontal electromagnets. This tension further suppresses the vibration of the steel plate and improves levitation. In this study, we propose using a hybrid electromagnetic levitation system by applying horizontal positioning control and determine the optimal placement of permanent magnets Actuatorsusing a 2018GA, for7, 54 a case where a horizontal electromagnetic field is acting on the steel plate. Furthermore,2 of 10 we performed a levitation experiment and considered the levitation stability of the optimal placement. electromagnet in the horizontal direction and positioning controls to the electromagnetic levitation 2. Outline of the Electromagnetic Levitation System Integrating Permanent Magnets and the system using vertical electromagnets for levitation [7]. This system generates tension on the edge of the Horizontal Positioning Control System steel plate due to the electromagnetic field generated by the horizontal electromagnets. This tension furtherThe suppresses hybrid electromagnetic the vibration of levitation the steel system plate and integrating improves positioning levitation. Incontrol this study, in the we horizontal propose usingdirection a hybrid is shown electromagnetic in Figure 1. The levitation object of system electromagnetic by applying levitation horizontal is a positioningrectangular, controlzinc-coated and determinesteel plate (SS400) the optimal with placementlength of 800 of mm, permanent width of magnets 600 mm, using and thickness a GA for of a case0.24 wheremm. To a accomplish horizontal electromagneticnoncontact support field of is this acting plate, on theas if steel it were plate. hois Furthermore,ted by strings, we we performed use five apairs levitation of electromagnets experiment and(No. considered 1–5 in Figure the levitation1). The displacement stability of theof the optimal steel placement.plate is measured using five eddy-current gap sensors. Here, the electric circuits of paired electromagnets are connected in series, whereas an eddy- 2.current Outline gap of sensor the Electromagnetic is positioned between Levitation the two System magnets Integrating of each Permanentpair. The detected Magnets displacement and the is Horizontal Positioning Control System converted to velocity using digital differentiation. A regulated voltage from the digital-to-analog converterThe hybrid is supplied electromagnetic to a current-su levitationpply amplifier system integratingto control the positioning attractive control force of in the the five horizontal pairs of directionelectromagnets is shown to inensure Figure that1. The the object steel of plate electromagnetic is levitated levitationby 5 mm is abelow rectangular, the surface zinc-coated of the steelelectromagnets. plate (SS400) In with this lengthmodel, of independent 800 mm, width control of 600 is used, mm, andwherein thickness information of 0.24 mm. on detected To accomplish values noncontactof displacement, support velocity, of this and plate, coil as current if it were of hoistedthe electromagnet by strings, under we use study five pairsare fed of back electromagnets only to the (No.same 1–5 electromagnet. in Figure1). The displacement of the steel plate is measured using five eddy-current gap sensors.The horizontal Here, thedisplacement electric circuits of the of plate paired is electromagnetsmeasured using are four connected laser beam in series, displacement whereas ansensors. eddy-current The four gap velocities sensor isof positioned the plate betweenare detected the twoby magnetsdifferentiating of each the pair. signals The from detected the displacementdisplacement issensors converted using to a velocity computer. using The digital current differentiation. flowing the Aelectromagnet regulated voltage is obtained from theby digital-to-analogmeasuring the voltage converter of isthe supplied resistor to connected a current-supply in series amplifier to the electric to control circuit. the attractive The permanent force of themagnets five pairs are installed of electromagnets around electromagnet to ensure that unit the for steel levitation plate is levitatedas shown by in 5Figure mm below 2. The the size surface of the ofpermanent the electromagnets. magnet for Inlevitation this model, assistance independent is 30 mm control × 30 mm is used, × 15 mm wherein and the information material is on ferrite. detected The valuessurface of magnetic displacement, flux density velocity, is 0.12 and T. coil Permanent current of magnets the electromagnet are placed undersuch that study the are deflection fed back of only the tofloating the same steel electromagnet. sheet is suppressed while using the above system. Levitation controller AMP5 AMP4 D/A DSP AMP3 AMP2 converter (ADSP674-00)150MHz AMP1 A/D converter iz1 iz2 iz3 iz4 iz5 z1 z2 z3 z4 z5 y Laser type sensor Eddy current type sensor Electromagnet for levitation control Permanent magnet z (30 mm×30 mm×15 mm) Steel plate (800 mm×600 mm×0.24 mm) x Electromagnet for horizontal positioning control x1 x2 x3 x4 ix1 ix2 ix3 ix4 A/D converter AMP4 DSP D/A AMP3 (ADSP324-00A)50MHz converter AMP2 AMP1 Horizontal positioning controller FigureFigure 1.1. HybridHybrid electromagnetic electromagnetic levita levitationtion system system integrating integrating positioning control in thethe horizontalhorizontal direction.direction. The horizontal displacement of the plate is measured using four laser beam displacement sensors. The four velocities of the plate are detected by differentiating the signals from the displacement sensors using a computer. The current flowing the electromagnet is obtained by measuring the voltage of the resistor connected in
Details
-
File Typepdf
-
Upload Time-
-
Content LanguagesEnglish
-
Upload UserAnonymous/Not logged-in
-
File Pages10 Page
-
File Size-