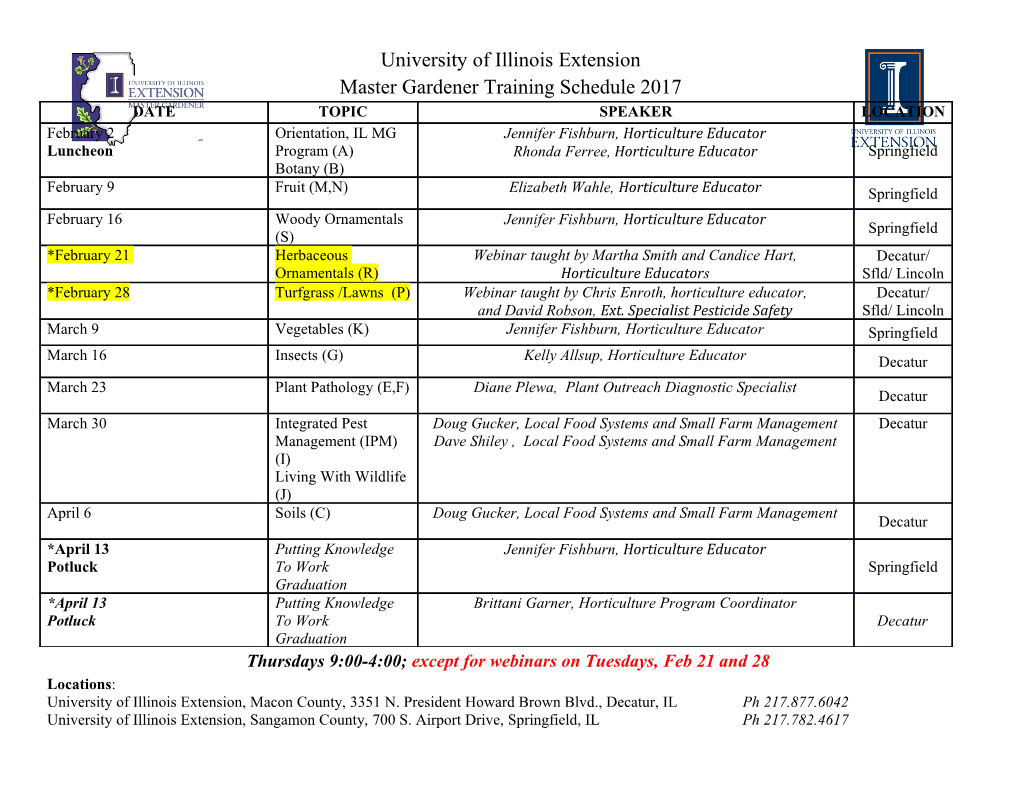
Diaphragm Valve Development Challenging traditional thinking The traditional diaphragm valve has long been a workhorse for controlling different flow types. In ancient Rome, diaphragm valves were used to control the water flow and temperature of the hot baths. In 1928, South African mining engineer P. K. Saunders invented the industrial diaphragm valve that is still used today.1 Initially this diaphragm valve was primarily used for non-hygienic applications. However its simplicity, combined with a hygienic and aseptic design, transformed the diaphragm valve into a widely used valve for hygienic applications. Since the invention of the industrial diaphragm valve, enhancements have continually improved upon Saunders’ original. These include the introduction of new material suitable for hygienic applications, new valve configurations such as the T, tank-outlet and multi-port valves, and a wide variety of valve automation and control units for enhanced regulation. However, today’s diaphragm valve technology – and performance – are essentially the same as that of ancient Rome. Today the diaphragm valve is widely used in the pharmaceutical industry, and it works well. However, it has its shortcomings, such as high maintenance costs, contamination and batch loss, and issues with pressure drop and flow regulation. Maintenance costs Diaphragm valve maintenance costs can potentially be high. The diaphragm, for instance, may require frequent replacement, depending on the types of applications and duties. For critical duties, pharmaceutical companies may need to replace the diaphragm every third month. In fact, the BioPhorum Operations Group (BPOG) estimates that “up to 40% of preventative maintenance tasks originate from diaphragm valve maintenance”.2 Contamination and lost batches In the pharmaceutical industry, contaminated and lost batches are expensive. The diaphragm valve has very high demands on tightening the diaphragm to the valve body. Proper cross- tightening of the four casing bolts using the appropriate torque is critical. Improper tightening results in sub-optimal sealing of the diaphragm to the valve body, which increases the risk of diaphragm crevices and cracking. The diaphragm itself also presents the risk for error. In a diaphragm valve, the diaphragm elastomer is stretched and compressed, which puts very high demands on the elastomer quality. The BPOG also notes that elastomer quality may vary widely from supplier to supplier.3 Furthermore, variations in diaphragm quality may increase the risk of cracking, which can lead to batch contamination. Página 1 de 6 It is therefore difficult to determine which diaphragm valve supplier offers the diaphragm with the longest service lifetime. Each supplier has its own test methods to evaluate the lifetime of a diaphragm. According to the BPOG, the industry is therefore looking to standardize tests to determine diaphragm lifetime; some major biopharmaceutical companies have invested in developing their own test skids to assess diaphragm materials.2 Pressure drop The traditional diaphragm valve has a pressure drop that is approximately 20 times higher than a full bore valve, such as a ball valve. In a pharmaceutical water system distribution loop, water velocity is vital to securing the correct temperature and minimizing biofilm buildup in the system. With several diaphragm valves in the system, both the pump and installation components, including valves, tubes and fittings, must be dimensioned accordingly in order to secure the minimum velocity. This significantly increases the overall system costs as well as operating costs compared to a valve with a lower pressure drop. Flow regulation Today traditional diaphragm valves are used as flow regulating valves based on the valves’ high hygienic integrity. However the flow curve of the traditional diaphragm valve is only linear up to approximately 40% of the stroke opening; thereafter, the flow curve flattens out (Figure 1). This makes it very difficult to control the flow using a traditional diaphragm valve. Página 2 de 6 Next-generation diaphragm valves Alfa Laval has now developed the next generation of diaphragm valves. This next-generation diaphragm valve is designed to address many of the shortcomings of the traditional diaphragm valve. It meets industry demands for innovative features that provide longer diaphragm lifetime, increase efficiency and reduce the industry’s carbon footprint. This next-generation diaphragm valve has three product enhancements that differentiate it from traditional diaphragm valve design: 1. A smoother valve interior design, free from sharp corners (Figure 2). 2. A single centre thread instead of the traditional four-bolt design (Figure 3). 3. A round, instead of a square, diaphragm (Figure 4). Tests show that these improvements dramatically improve overall valve performance compared to the traditional diaphragm valve.4 Página 3 de 6 Maintenance cost The next-generation diaphragm valve reduces the time required for diaphragm replacement by more than 50%. Replacement of the next-generation diaphragm requires less than a minute instead of more than two minutes, which is required for diaphragm replacement on a traditional valve.4 For a single pharmaceutical manufacturing site, which typically has between 1,000 and 5,000 diaphragm valves onsite, an estimated 17 to 85 man-hours can be saved by using the next- generation diaphragm valves instead of the traditional ones. Another advantage of the new diaphragm valve: no retightening is required after steam sterilization. The traditional diaphragm valve contains more elastomer between the valve body and handle/actuator compared to the new valve. The elasticity of the rubber is affected when the rubber is sterilized with steam or exposed to high temperatures. As a result, the valve therefore requires retightening in order to compensate for the reduced elasticity of the rubber material. The round diaphragm in the next-generation valve enables a minimal amount of rubber material to be used between the body and the handle/actuator. This minimizes the negative effect of reduced elasticity, which in turn eliminates the need to retighten. It also delivers tangible savings that can be measured through more uptime and fewer downtime hours. Advanced Finite Element Method (FEM) analysis on the round diaphragm design shows more even distribution of forces and stress throughout the diaphragm compared to the square diaphragm. Steam tests according to the American Society of Mechanical Engineers’ Bioprocessing Equipment Standard, Revision 2009 (ASME BPE 2009), Appendix J, Sub-section J- 2, Simulated Steam-in-Place (SIP) for diaphragm valves indicates that the round diaphragm in the next-generation diaphragm valve has about twice the lifespan of the traditional square diaphragm.4 This reduces the cost of diaphragm valve spare parts and further reduces maintenance and downtime. With these improvements, it should be possible to reduce the high maintenance costs now associated with the traditional diaphragm valve. Just how great a reduction remains to be seen. Contamination and lost batches Incorrect assembly and over-tightening of the bonnet over the diaphragm and valve body is one of the primary causes of diaphragm valve failure and leakage. It is therefore important to tighten all of the bolts according to the torque requirements in order to distribute the load evenly. Uneven distribution of the forces can lead to leakage between the atmosphere and the product as well as premature and unforeseen cracking of the diaphragm. The next-generation diaphragm valve with its centre thread makes it very safe and easy to assemble and tighten the bonnet (Figure 2). The centre thread ensures proper tightening of the bonnet and even distribution of forces over the diaphragm every time. This minimizes the risk of leakage to the atmosphere as well as the risk of diaphragm cracking due to uneven tightening. The traditional diaphragm valve is generally viewed as very easy to clean. However sharp corners in the weir and especially in the connection between the body and the diaphragm reduce flow velocity, which makes these areas hard to clean. For very high demands on cleanability, these areas require extensive cleaning in order to become residue-free. Página 4 de 6 The next-generation diaphragm valve features a smoother interior design with virtually no sharp corners (Figure 6). This meets the highest demands on cleanability using a quick and simple cleaning procedure. Pressure drop and flow regulation Next-generation diaphragm valves essentially minimize sharp corners thereby reducing pressure drop and turbulence (Figure 5). This has two main benefits: 1. It provides a more linear flow curve over a wider area of the valve’s opening stroke (Figure 6). This now makes it possible to use a diaphragm valve for more exact flow regulation. 2. It improves the flow rate across a range of sizes (Figure 7). The improved flow rate reduces system costs and operating costs, since the entire installation can be made using smaller dimensions, for instance, with smaller valves, pipe sizes and pumps. As an example a tank be emptied faster with same size of valve or a smaller valve could be chosen, if time is not of importance. Página 5 de 6 Conclusion The design of the diaphragm valve, which has changed little over the last 90 years, has survived the test of time. Not surprisingly, however, it has its shortcomings. By challenging traditional ways of thinking, the next-generation of diaphragm valves can
Details
-
File Typepdf
-
Upload Time-
-
Content LanguagesEnglish
-
Upload UserAnonymous/Not logged-in
-
File Pages6 Page
-
File Size-