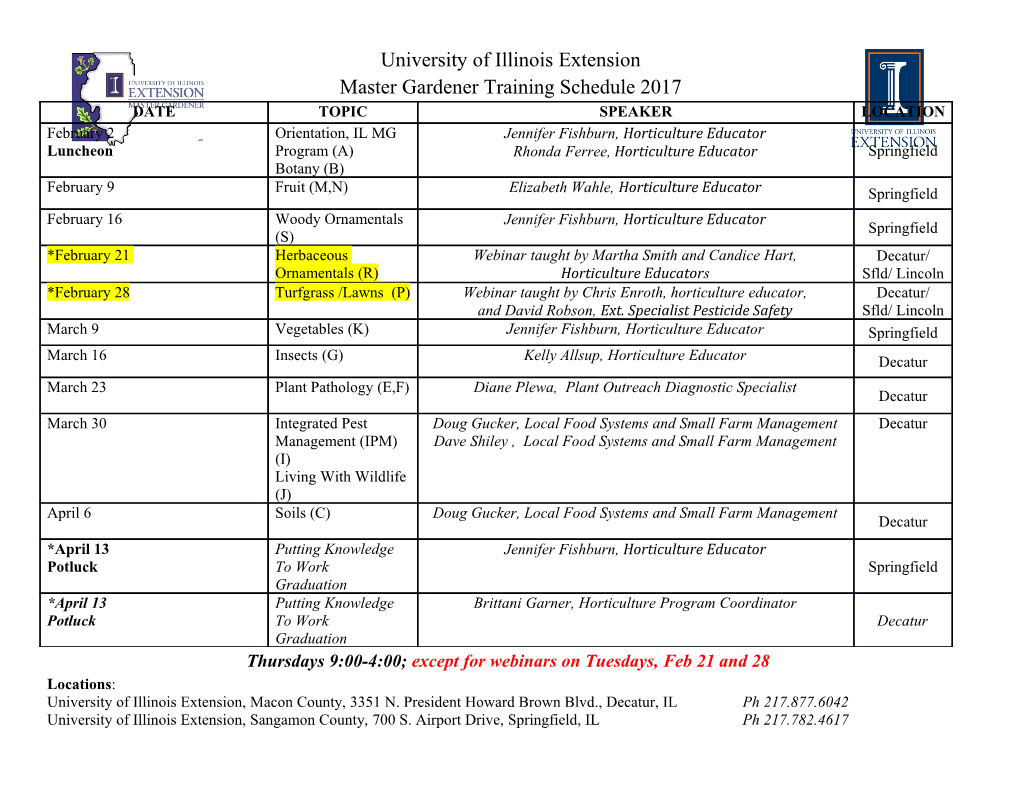
HIGH EFFICIENCY BASE DRIVE DESIGNS FOR POWER CONVERTERS USING SILICON CARBIDE BIPOLAR JUNCTION TRANSISTORS By Hui Zhu A thesis submitted for the degree of Doctor of Philosophy in the Department of Electronic and Electrical Engineering, University of Sheffield July 2019 I List of Abbreviations and Acronyms AC Alternative Current CCM Continuous Current Mode DCM Discontinuous Current Mode DUT Device Under Test DC Direct Current EMF Electro-Motive Force EMC Electro-Magnetic Compatibility ER Energy Recovery FPGA Field-Programmable Gate Array HV High Voltage IGBT Insulated Gate Bipolar Transistors IMGT IGBT and MOSFET Gated Transistor JFET Junction Field Effect Transistor MJTE Multistep Junction Termination Extension MOSFET Metal-Oxide Semiconductor Field-Effect Transistor NPT Non Punch Through NTC Negative Temperature Coefficient PCB Printed Circuit Board PF Power Factor PT Punch Through PWM Pulse Width Modulation RBSOA Reverse Biased Safe Operation Area RMS Root Mean Square SiC BJT Silicon Carbide Bipolar Junction Transistor SiO2 Silicon dioxide SPICE Simulation Program with Integrated Circuit Emphasis ZVS Zero Voltage Switching II Nomenclature Symbol Description Unit 퐶퐵퐶 junction depletion capacitance between base F and collector 퐶퐵퐸 junction depletion capacitance between base F and emitter 퐶퐶푆 collector to substrate capacitance F 퐶푝푢푙푠푒 pulse capacitor in the base drive F 퐶3 pulse capacitor in the energy recovery base F drive simulation circuit 퐷푚푎푥 the maximum duty cycle % 퐷푆푊1 duty cycle of SW1 in the active base drive % 퐷푆푊3 duty cycle of SW3 in the active base drive % 퐸푐 critical electric field strength MV/cm 퐸푔 energy band gap eV 퐸표푛 turn-on energy loss J 퐸표푓푓 turn-off energy loss J 퐸푡표푡 total switching energy loss J 퐼퐵 base current A 푖퐵(푡) time-variant base current A 퐼푏,퐴푉 average value of the base current A 퐼푏푅푀푆 RMS value of the base current A Ib_con base current in the conventional base drive A Ib_active base current in the active base drive A 퐼퐶 collector current A 퐼퐷 current sourced from the driver power A supply 퐼퐷퐶 base DC current for the conduction A 퐼퐸 emitter current A 푖푛(푡) input current of the integrated converter A 퐼퐿 inductor current in the energy recovery base A III driver 푖퐿,푝푒푎푘 inductor peak current in the integrated A converter 푖퐿,푎푣푒푟푎푔푒 inductor average current in the integrated A converter 퐼푛푐 current caused by the electrons swept into A the collector 퐼푛푒 current caused by the electrons injection A into the base 퐼푝푒 current caused by the holes injection into A the base 퐼푆 saturation current A 퐼푠ℎ표푟푡 short circuit current when Q1 and Q2 are A both turned on 퐿1 inductor used in the active base drive H 퐿푃푎푟 parasitic inductance nH -3 푁푎 acceptor density cm -3 푁푑 donor density cm 푃퐵퐸 base-emitter power loss W 푃퐸푅 power saving due to the energy recovery W power fed to the base-emitter capacitor W 푃퐶퐵퐸 푃퐶푝푢푙푠푒 power fed by DC source due to 퐶푝푢푙푠푒 in the W conventional base drive 푃푐표푛_푙표푠푠 power loss of the conventional base drive W power supply 푃표푛−푠푡푎푡푒 푙표푠푠 conduction loss of the power devices W 푃푄1 power loss of Q1 W 푃푅 resistive loss in the conventional base drive W W 푃푅1 푅1 loss in the active base drive 푃푝푟표_푙표푠푠 energy recovery base drive loss W 푃푡푢푟푛−표푛 푙표푠푠 turn-on loss of the power devices W 푃푡푢푟푛−표푓푓 푙표푠푠 turn-off loss of the power devices W IV 푄퐵(푡) charges in the base region C 푄퐹 excess carrier charges stored in the base C rC collector internal resistance Ω rE emitter internal resistance Ω rB base internal resistance Ω 푅1 base resistor used to set up base DC current Ω 푅2 base terminal damping resistor in the energy Ω recovery driver 푅3 damping resistor in the energy recovery Ω driver 푅퐿 load resistor of the integrated converter Ω 푅푆푊1 the on-state resistance of the switch (SW1) Ω 푇퐹 half switching period of the integrated s converter 푇표푛 conduction time s 푇푠 switching period of the integrated converter s 푇푆푊3 switching period of SW3 in the active base s drive 푇ℎ푒푎푡 heating period s 푉푎푐(푡) input AC power supply voltage V 푉퐶퐸,푄1 collector-emitter voltage of Q1 V 푉퐶퐸,푄2 collector-emitter voltage of Q2 V 푉퐵퐶 base-collector voltage V 푉퐵퐸 base-emitter voltage V 푉푏푒(푠푎푡) voltage drop across the base-emitter V junction during the on-state Vce_active collector-emitter voltage during the V conduction driven by the active base drive 푉퐶퐸 collector-emitter voltage V 푉퐶1 C1 voltage in the active base drive V Vce_con collector-emitter voltage during the V conduction driven by the conventional drive V 푉퐷퐷 base drive supply voltage V 푉표푢푡 output voltage of the integrated converter V 푉푝푢푙푠푒, 푉푐 voltage across of 퐶푝푢푙푠푒 during the V conduction 푉푝푒푎푘 peak value of the AC input voltage V 푊푛 input energy of the integrated converter J 푊표푢푡 output energy of the integrated converter J 푓푠 switching frequency Hz 훼퐹 common-base current gain 훽 common-emitter current gain 훽푅 reverse current gain 휀 dielectric constant ƛ thermal conductivity W/cmK ρ charge density C/m3 2 휇푛 electron mobility cm /Vs 2 휇푝 hole mobility cm /Vs 휏퐹 forward transit time s 푥푛 space charge width in n region m 푥푝 space charge width in p region m 7 푣푠푎푡 saturation velocity 10 cm/s 휔푑 angular frequency rad/s VI Abstract This thesis explores the base driver designs for Silicon Carbide Bipolar Junction Transistors (SiC BJTs) and their applications for power converters. SiC is a wide bandgap semiconductor which has been the focus of recent researches as it has overcome the several of physical restrictions set by the silicon material. Compared with silicon bipolar devices, SiC BJTs have several advantages including a higher maximum junction temperature, higher current gain and lower switching power losses. Transient power losses are low and temperature- independent in a wide range of junction temperatures. With junction temperature capable of being between 25ºC to 240ºC, SiC BJTs have been of great interest in industry. As a current- driven device, the base driver power consumption is always a major concern. Therefore, high efficiency base drive designs for SiC BJT need to be investigated before this power device can be widely used in industry. Due to the base drive loss analysis, the pulse capacitor that is used in a conventional base drive is the main contributor to power consumption under high switching frequency and low base current conditions. The energy recovery concept can reduce the power losses associated with this capacitor. This concept is firstly used for a SiC BJT drive design. Based on this concept, a drive design termed as the energy recovery base drive is proposed. The experimental results demonstrate lower driver losses compared with the conventional base drive. The proposed driver is verified in a 1.7kW boost converter switching at various frequencies. An active base drive has been firstly proposed to reduce the resistive power losses that dominate the total driver power consumption for applications which implement low switching frequency and high duty cycle. Even if a high-voltage power supply is used in the active base drive unit for fast switching, a low voltage branch composing of a voltage step- down function supplies the required DC base current to maintain the conduction of the BJT. Low driver losses, low switching and conduction losses are achieved experimentally. The integrated converter, which adopts motor winding inductance instead of a bulky and heavy discrete inductor in a conventional power converter, has been developed as a platform to verify both the boundary theory analysis for the converter and the functionality of the active base driver. 1 Publications Hui Zhu, Mark Sweet, E.M. Sankara Narayanan, "A Comparison of Switching Characteristics between SiC BJT and Si IGBT at Junction Temperature above 200ºC," PCIM Asia 2015; International Exhibition and Conference for Power Electronics, Intelligent Motion, Renewable Energy and Energy Management; 24-26 June 2015 Content of Chapter 2 is based on this publication. Hui Zhu, Mark Sweet, E.M. Sankara Narayanan, “Base drive energy recovery for a silicon carbide bipolar junction transistors,” IET Power Electronics, Volume 8, Issue 12, December 2015, p. 2429 – 2434 Content of Chapter 3 is based on this publication. 2 Acknowledgements I would like to thank my colleagues in Rolls-Royce UTC and Electrical Machines and Drives group, for the nice working atmosphere provided by them. Especially to Dr. Mark Sweet, who always had discussions with me on those tough technical difficulties that I confronted. I would like to thank Professor Geraint W Jewell and Dr. Kean-Boon Lee for the corrections and technical support to the thesis. I would also like to thank the Engineering Physical Sciences and Research Council and Rolls Royce for the award of a research studentship and financial support. 3 Contents 1 Power Semiconductor Devices and Drivers ...................................................................... 7 1.1 Aim and Objectives ..................................................................................................... 8 1.2 Bipolar Junction Transistor ......................................................................................... 8 1.2.1 Forward active operation ..................................................................................... 9 1.2.2 Voltage blocking characteristics ........................................................................ 13 1.3 High voltage transistor .............................................................................................. 16 1.4 SPICE model for a BJT device ................................................................................
Details
-
File Typepdf
-
Upload Time-
-
Content LanguagesEnglish
-
Upload UserAnonymous/Not logged-in
-
File Pages215 Page
-
File Size-