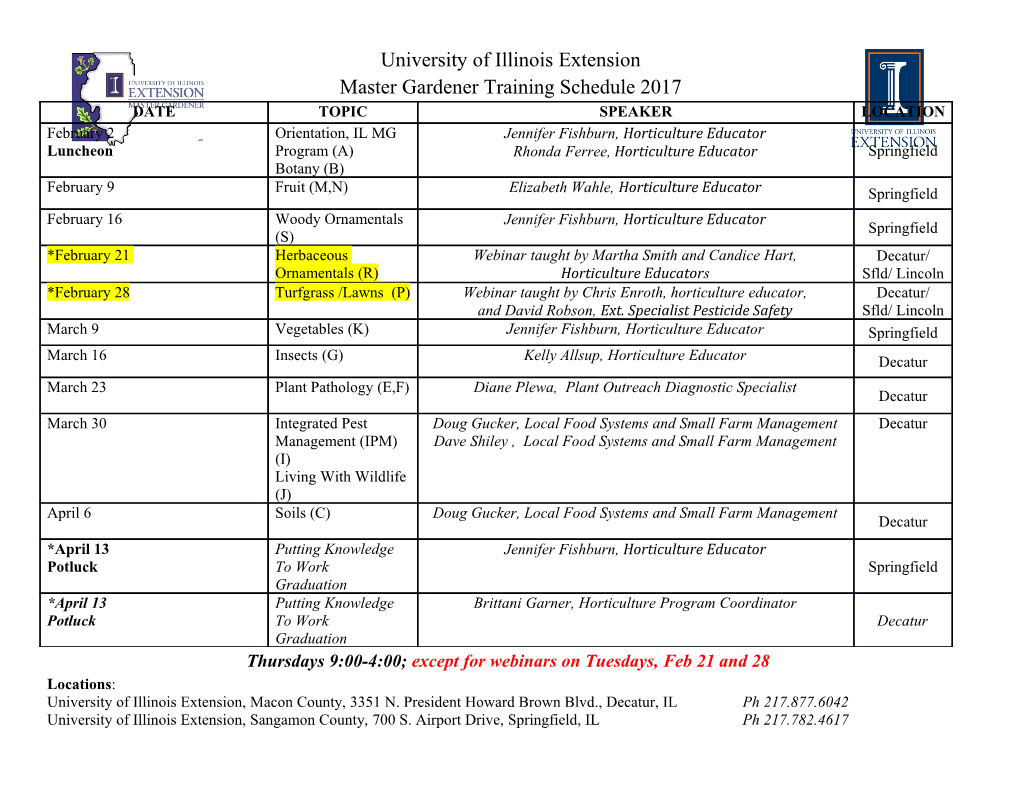
Cartography, data visualisation and presentation New cave survey START visualisation methods Information from IS Technology Systems This article relates to exploration of the Gaping Gill - Britain’s largest cavern. Ground penetrating radar (GPR) and ground light detection and ranging (LIDAR) surveys were tested from 18 - 24 August 2003 in Gaping Gill, Yorkshire. It was suggested that the GPR survey be used, with the aim of exploring the sediments forming the Gaping Gill Main Chambre (GGMC) cave floor. How much have these methods developed in the last two years? Share your comments with us by emailing [email protected] . Three good reasons for carrying out this work emerged, namely: Ground light detection and ranging (LIDAR) Survey Firstly, the unstable nature of the cave floor sediments and Previous work sections of the GGMC rock wall have been recorded for about a century. St. Amand (1999) describes an early application of laser scanner CPC ‘diggers’, such as Mole, have a burning desire to discover technology to create a 3D cave map for the Joaquin Miller Chapel new passageways. The strength of their commitment became room in the Oregon Caves. In three days, they collected 35-million clear when they covered vast tracts of moorland with the points, capturing the detailed 3D geometry of the cave surface. GPR sledge in very little time. Could new technology find Their 3D CAD images show flowstone formations in good detail, passageways? Does the spade still reign supreme? The depth including vertical flutes on fused stalactite-stalagmite columns. scale of Fig. 7 has been calibrated in 2 m spades, as a goodwill gesture. Yordas Cave has been scanned with ground LIDAR. Prior to the Several worthy geological questions could perhaps be Gaping Gill LIDAR survey described here, Graham Hunter acquired addressed by this and any subsequent surveys: a 4,7 MB LIDAR survey of Peak Cavern, to enhance the integrated modelling of Pringle et al. (2002). The putative GGMC winter wash-tub process. The possible Pleistocene stratification of the GGMC Equipment, operation and processing sediments. There are well-preserved, layered sediments elsewhere in the system. In the last few years, ground LIDAR or 3D laser mapping has been The possibility that the Gaping Gill – Ingleborough Cave replacing the previous laser theodolite or Total Station survey system could show several cycles of karstification, some technology. LIDAR technology is developing rapidly and the of which may date back to limestone deposition in the image quality of future surveys with more recent equipment Carboniferous. will doubtless be even better than that achieved at Gaping Gill in 2003. However, the market is receptive and equipment is in short Given typical maximum depths of investigation for GPR in sediments supply. Airborne LIDAR is equally sensational. of up to 25 m and a GGMC shaft depth of about 100 m, there are two levels from which new passageways might be discovered. Graham Hunter borrowed a model LMS-Z210 from Salford From a moorland survey, high-level passageways might be University. The Z210 was Riegl’s first 3D imaging sensor for imaged. industrial applications. Key parameters have a typical measurement accuracy of 25 mm with a line scan range of 80° and a frame scan From the floor of GGMC, passageways through the boulders range of 333°. Graham selected a scan rate of 18 000 points per might be imaged. The visible GGMC is approximately a triangular second. prism, shaped like a ‘Toblerone’ bar so the cavern may continue to widen with depth, hidden by the boulder fill. Compare Figs. 1, 2, 4 and 6. In which case the claim that St. Paul’s Cathedral could almost fit inside might become true, subject to excavation (for which project CPC would have the staff!). The lower paleozoic basement unconformity beneath the great scar limestone would be an even more ambitious and significant GPR target. The unconformity is highly irregular at outcrop, so flow boundaries could control conduit development at lower levels in the cave system. Exactly how the large antennae of a GPR system capable of the necessary penetration could be moved around the passageways is a challenge for the future. Once the parameters have been Fig. 1: Gaping Gill Main Chamber LIDAR Fig. 2: Gaping Gill Main Chamber LIDAR defined the challenge shall be issued. survey 2003. Vertex cloud looking west. survey 2003. Vertex cloud looking east. 29 continue Graham first made a LIDAR scan from the eastern edge of the Gaping Gill sinkhole. This took in the surrounding moorland, the Fell Beck valley and the top of the Gaping Gill shaft. Then three pairs of orthogonal scans were made from the floor of GGMC. Reflector patches were placed in the overlap zones between surveys swaths. Altogether about 15-million xyz points were surveyed during the afternoon. The software is able to recognise the artificial reflectors and register the separate survey scans. An additional ambitious aim was to link the surface and the underground surveys. With hindsight, the surface survey needs to be taken from the northwestern edge of the sinkhole so that the central survey point from the floor of GGMC can ‘see’ reflectors or at least common features on the upper southern edge of the shaft. Then the surface and underground surveys could be joined with an overall accuracy of about 25 mm. The three pairs of underground LIDAR scans were joined to form the data model Fig. 4: Rendered LIDAR survey results for the whole of Gaping Gill Main Chamber provided on CD-ROM. The separate image points were re-sampled and part of the lower shaft as though looking through the rock from the west. to 750 000 original vertices (860 000 with interpolation) for The western boulder slope rises towards the viewer. Note the right-triangular cross-section controlled by fault and joint surface. It is easy to suppose that rendering. The full 30 MB file covers GGMC on a spacing of about the cave walls may continue to widen downwards where hidden below the 6 cm; see Figs. 1 and 2. sediments of the cave floor. Preliminary results Ground penetrating radar (GPR) The 6 cm sample interval and 2,5 cm accuracy of the 2003 LIDAR Most GPR studies in karst have focused on detecting caves within the data model is sufficient to define the main geological features limestone from the surface, rather than the profiling of cave earth controlling the development of the exposed upper part of GGMC. deposits within the caves. The most commonly used system The main faults and joints, the main bedding planes and some is the pulseEKKO PE100. We also planned to use a PE-100 at Gaping Gill. overhangs developed below them are clearly visible. However the Typically, 25 or 50 MHz antennae are used to image down to 25 or 15 m fine detail seen in the previous Peak Cavern LIDAR survey is missing. respectively. Graham Hunter was able to use a more recent Z360 instrument with an accuracy of 12 mm to make the Peak Cavern survey. For Equipment, operation and data processing detailed geological analysis, the higher resolution image volume is needed. For present purposes a 30 MB data model is probably A commercial PE-100 system was hired and successfully tested most suitable. It is difficult to manage a 180 MB data model, at Peak Cavern. It was not working on arrival at Gaping Gill and because the rendering time between poses is tedious. it could not be repaired until early September. As a result a new and specialised GPR system was obtained - the Utsi Electronics A remarkable advantage of a LIDAR cave survey is the ability to GV2. Whereas the Canadian PE-100 system has been a GPR industry view cave morphology from the outside – as though one could see standard for well over 10 years, the Utsi Electronics GV2 represents through the solid rock; see Figs. 3 and 4. The geological features more recent technology developed in the UK. The Utsi GV2 has a controlling cavern development become much more obvious than broader frequency bandwidth from 30 - 100 MHz. Broad bandwidth when the cave is viewed from inside. The inside view is however signals are most desirable for good quality geophysical imaging. better for identifying fine detail and for comparing that detail with The Utsi antennae are about 1,1 m square and about half a metre direct observations; see Figs. 1 and 2. high. They are delicate and difficult to manoeuvre without damage. The GV2 system was transported to and from Gaping Several views of the data have been screen-grabbed. In Figs. 5 and 6 the earlier survey by the Yorkshire Ramblers Club has been overlaid for comparison with Calvert (1899, 1900). Fig. 5: West-east LIDAR section through Gaping Gill Main Chamber (red, or grey Fig. 3: Renedered LIDAR survey results for the whole of Gaping Gill Chamber point cloud) compared with Yorkshire Ramblers Club survey of 1896. There and part of the lower shaft as though looking through the rock from the are discrepancies in the length measurements, compare the upper, LIDAR north. Dubbed HMS GG, the bow and stern are formed from the eastern (left) and lower, YRC scales. The LIDAR survey has been enlarged to fit the YRC and western (right) boulder slopes. Note sub horizontal etch marks along longitudinal section, so that the form of the floor can be compared. The YRC bedding. roof is still too high, compare Fig. 6. 30 continue Gill using a quad bike and trailer. The antenna system remained underground for the duration of the 3-day GGMC survey. There was overnight rain on the first evening and the waterfalls into GGMC made the entire cavern humid.
Details
-
File Typepdf
-
Upload Time-
-
Content LanguagesEnglish
-
Upload UserAnonymous/Not logged-in
-
File Pages4 Page
-
File Size-