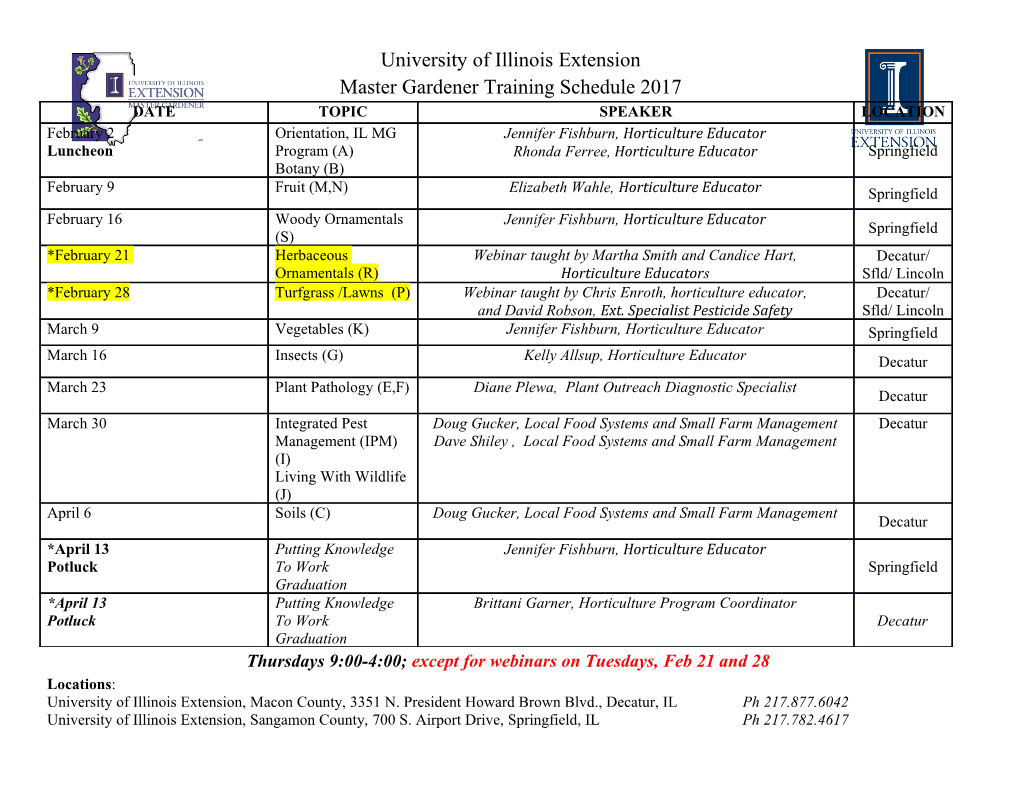
Europäisches Patentamt *EP001371632A1* (19) European Patent Office Office européen des brevets (11) EP 1 371 632 A1 (12) EUROPEAN PATENT APPLICATION (43) Date of publication: (51) Int Cl.7: C07C 253/00, C07C 255/16 17.12.2003 Bulletin 2003/51 (21) Application number: 03253473.7 (22) Date of filing: 03.06.2003 (84) Designated Contracting States: (72) Inventor: Decourcy, Michael Stanley AT BE BG CH CY CZ DE DK EE ES FI FR GB GR Houston, Texas 77059 (US) HU IE IT LI LU MC NL PT RO SE SI SK TR Designated Extension States: (74) Representative: Kent, Venetia Katherine AL LT LV MK Rohm and Haas (UK) Ltd European Operations Patent Dept. (30) Priority: 14.06.2002 US 389015 P Lennig House 2 Mason’s Avenue (71) Applicant: ROHM AND HAAS COMPANY Croydon, CR9 3NB (GB) Philadelphia, Pennsylvania 19106-2399 (US) (54) Process for producing acetone cyanohydrin (57) An improved process for the production of acetone cyanohydrin by the reaction of acetone and HCN under basic pH conditions comprises supplying a metal cyanide composition and an HCN composition to the reaction. EP 1 371 632 A1 Printed by Jouve, 75001 PARIS (FR) 1 EP 1 371 632 A1 2 Description acrylonitrile produced. It is isolated as about 99% anhy- drous hydrogen cyanide before being reacted with caus- [0001] The process for conversion of acetone cyano- tic or other materials. hydrin - H2SO4 to methacrylates, such as methyl meth- [0007] Because of the highly cost-dependent market acrylate or methacrylic acid, has been practiced com- 5 for methacrylates, it would be advantageous to utilize mercially since 1937 and is based on technology pat- multiple sources of HCN to ensure adequate raw mate- ented by ICI in 1934 (British Patent No. 405,699). Al- rial is available for ACH production. In this way, ACH though numerous improvements and alternative pro- production rates can be maximized and can better keep duction methods have been proposed over the years, pace with end-use methacrylates production demand. the acetone cyanohydrin (ACH) route remains the most 10 Although ACH and methacrylates production facilities common production method for methacrylates and are generally located adjacent to one another, the use nearly all of the ACH produced in the world is consumed of multiple HCN sources could result in at least some of in the production of methacrylates. Because of this, the the required HCN being produced far from the ACH pro- great majority of ACH production facilities are located duction site; this situation is particularly common when adjacent to methacrylate production facilities. 15 the HCN is derived as a by-product of an acrylonitrile [0002] All commercial ACH is prepared via the reac- production process. Because of its toxicity, the safe tion of acetone and hydrogen cyanide. Because of in- transport of HCN to a distant ACH/methacrylates pro- creasing demand for methacrylates, in recent years, as duction site is an area of major concern for chemical well as ongoing pressure to minimize manufacturing manufacturers. costs, manufacturers would greatly welcome improve- 20 [0008] The following methods for transporting HCN ments to the ACH production process which improve have been proposed: production capacity, lower costs and provide safer op- eration. 1. Purify the HCN and ship to a distant user [0003] Commercially, high purity HCN (at least 90% pure) for making ACH can be produced in one of three 25 - transportation via truck, rail or waterway raises ways: significant safety issues. 1. By the Andrussow process 2. Convert the HCN to sodium cyanide, ship the so- 2. By the Degussa B-M-A process dium cyanide to the user, acidify the sodium cyanide 3. As a by-product of acrylonitrile production 30 after arrival to release HCN (this may include the optional extra step of distilling the released HCN to [0004] The most common process, known as the An- remove impurities (see Published International Pat- drussow process, involves the reaction of natural gas ent Application No. WO 97/45369 A1) (primarily methane) with ammonia, in the presence of oxygen or air, over a precious metal catalyst. The prod- 35 - this method is energy and capital intensive ucts of this reaction are a diluted stream of hydrogen cyanide, water, hydrogen, carbon dioxide, carbon mon- 3. Convert the HCN to ACH at the source, then ship oxide, as well as the unreacted excess quantities of am- the ACH to a distant user monia and methane, and, possibly, nitrogen which aris- es from the use of air as an oxygen source. Other minor 40 - transportation via truck, rail or waterway raises contaminants may include nitrites formed in the reac- significant safety issues (somewhat less haz- tion. In most cases, the gas stream is purified by isolat- ardous than 100% HCN but nonetheless signif- ing the hydrogen cyanide to a purity of about 99%. icant transportation safety issues) [0005] A second reaction involving natural gas and - high capital cost (building another ACH produc- ammonia was developed by Degussa and is known as 45 tion unit at the HCN source is capital intensive the B-M-A process. The natural gas and ammonia are and may result in inefficient use of total ACH reacted over a precious metal catalyst, but in the ab- production capacity) sence of oxygen. The products of this reaction are sim- ilar to those of the Andrussow process, except that there [0009] It is the intent of the present invention to pro- is no water, carbon dioxide or carbon monoxide. The hy- 50 vide an improved process for the production of ACH. In drogen cyanide is normally purified as anhydrous hydro- this regard, the present invention provides, in one as- gen cyanide through distillation before it is reacted to pect, an improved process for the production of acetone form other cyanide derivatives or metal cyanides. cyanohydrin by the reaction of acetone and HCN under [0006] In a third process, hydrogen cyanide is formed basic pH conditions, the improvement comprising: sup- as a by-product or co-product in the production of acry- 55 plying a metal cyanide composition and an HCN com- lonitrile by the reaction of propylene and ammonia in the position to the reactor. presence of air. Approximately one pound of hydrogen [0010] In another aspect, the present invention pro- cyanide is produced for every ten or eleven pounds of vides a process for the production of crude acetone cy- 2 3 EP 1 371 632 A1 4 anohydrin, wherein the process comprises: feeding a these. metal cyanide to a reactor; feeding a hydrogen cyanide [0015] The metal cyanide is preferably low in carbon- composition to the reactor; feeding acetone to the reac- ate and formate content ( less than 0.5 wt% each, as tor; maintaining a temperature of between 0°C and 50°C measured in dry solid metal cyanide); preferably has a in the reactor; maintaining a pH of at least 7.0 in the 5 minimal nitrile content and is low in other metals, espe- reactor; maintaining a residence time in the reactor of cially iron. between 15 minutes and 120 minutes; recovering a [0016] The metal cyanide is preferably low in chloride product stream from the reactor comprising crude ace- content (especially if the metal cyanide is NaCN, com- tone cyanohydrin. mercially available "low chloride" NaOH can be used to [0011] The production of acetone cyanohydrin suita- 10 produce NaCN or the NaCN may be made directly from ble for use in the production of methacrylates involves Trona as taught in European Published Patent Applica- three primary steps: a reaction to form crude ACH; sta- tion No. 0 360 555 A1) - this minimizes the potential for bilization of the crude ACH; and purification of the crude chloride-induced stress corrosion cracking in stainless ACH to product ACH. steel ACH production process equipment. [0012] In the reaction step, according to the present 15 [0017] The HCN composition may contain water, al- invention, crude ACH is formed by the reaction of ace- though HCN of at least 90 wt% purity is preferred, with tone with a mixed cyanide composition comprising an at least 95 wt% purity being especially preferred. The admixture of a metal cyanide composition and an HCN HCN composition may also contain one or more acid composition. stabilizers, e.g., organic acids or inorganic acids, such 20 [0013] The metal cyanide composition preferably as acetic acid or H2SO4 or H3PO4. comprises an alkali metal cyanide, such as NaCN or [0018] The metal cyanide composition may comprise KCN, or an alkaline earth metal cyanide, such as Ca from 0.5 to 99.5 wt% of the total of the metal cyanide (CN)2 or Mg(CN)2, most preferably NaCN. The metal cy- composition and the HCN composition. anide composition may contain a metal hydroxide sta- [0019] Optionally, water may also be fed to the reac- bilizer, e.g., NaOH. The metal cyanide composition may 25 tor. Such water may take any useable form, e.g., proc- also contain water. Suitable forms of the metal cyanide ess water, fresh deionized water, water present in ma- composition, for use in the present invention, include: terial recycled from the ACH purification system( this re- cycled material may also contain acetone and HCN) or aqueous solution - e.g., commercially available as water present in the metal cyanide composition. 30% aqueous NaCN solution (Cyanco, Winnemuc- 30 [0020] Fresh acetone and the mixed cyanide compo- ca, NV); sition are fed continuously to the reactor, which is cooled slurry (e.g., U.S. Patent No. 4,902,301); (cooling may be effected by any means, e.g., by internal paste (e.g., U.S.
Details
-
File Typepdf
-
Upload Time-
-
Content LanguagesEnglish
-
Upload UserAnonymous/Not logged-in
-
File Pages8 Page
-
File Size-