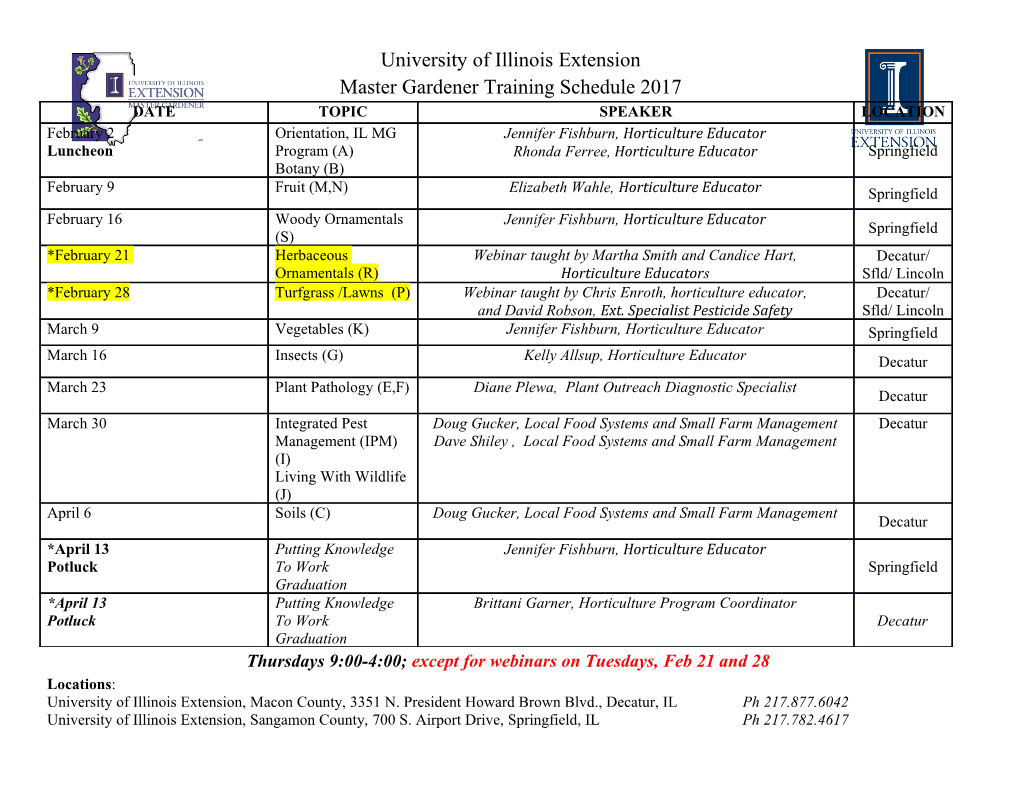
metals Article Development of a Mass and Energy Balance Model and Its Application for HBI Charged EAFs Niloofar Arzpeyma 1,2,*, Rutger Gyllenram 1,2 and Pär G. Jönsson 1 1 Department of Materials Science and Engineering, Royal Institute of Technology (KTH), 10044 Stockholm, Sweden; [email protected] (R.G.); [email protected] (P.G.J.) 2 Kobolde & Partners AB, 11860 Stockholm, Sweden * Correspondence: [email protected]; Tel.: +46-737-585-050 Received: 4 February 2020; Accepted: 26 February 2020; Published: 27 February 2020 Abstract: A static mass and energy balance model combined with a MgO saturation slag model is developed for electric arc furnaces. The model parameters including distribution ratios and dust factors are calibrated for a specific furnace using experimental data. Afterward, the model is applied to study the effect of charging different amounts of hot briquetted iron (HBI) on energy consumption, charged slag former amount, and slag composition. The following results were obtained per each 1% increase of HBI additions: (i) a 0.16 Nm3/t decrease in the amount of injected oxygen for metal oxidation, (ii) a 1.29 kWh/t increase in the electricity consumption, and (iii) a 34 kg increase in the amount of the slag. Keywords: HBI; mass balance; energy balance; MgO saturation 1. Introduction Many studies focusing on electric arc furnace (EAF) operations have been carried out during the last 30 years in order to improve the steel quality and to make the melting process more efficient, economical and environmentally friendly [1–3]. Any improvement to an EAF requires an extensive study of that specific furnace since each furnace is used to produce different steel grades. Apart from installations of equipment such as electromagnetic or inert gas stirrers and advanced oxygen-fuel injectors, even a small modification in the carbon and oxygen injection or in the raw material selection and tuning can result in an improved steel quality and productivity as well as in reduced energy consumption. The focus of this work is on one of these approaches, which is the importance of the material selection with an emphasis on charging hot briquetted iron (HBI) as a secondary complement to scrap. The quality of direct reduced iron (DRI) and HBI materials is more consistent compared to steel scraps since they are produced from iron ore. They can be used in electric arc furnaces to contribute to reduced levels of tramp elements such as copper, nickel and tin, which exist in scraps that are used as raw materials and [3–5]. The amount of the charged DRI and HBI materials is highly dependent on the scrap quality and the limits of tramp elements in the target steel grades. In addition, the usage of DRI/HBI can affect energy consumption, tap–to–tap time, and the iron yield [6–9]. Mass and energy balance models are used to calculate the energy consumption, melt composition and tapping time in EAFs [10–15]. A static EAF model based on mass and energy was proposed by Köhle based on operational data from 14 EAFs in Germany [10]. The model estimated the electrical energy consumption as a function of raw materials, slag formers, other sources of energy inputs as well as power-on and power-off times. Bekker et al. [11] and McRosty et al. [12] developed dynamic models of the EAF based on the heat and mass transfer between the three phases of melt, slag, and gas. A more complex dynamic model was developed by Logar et al. [13], which considered more parameters with respect to the heat transfer between all phases as well as post-combustion. The average Metals 2020, 10, 311; doi:10.3390/met10030311 www.mdpi.com/journal/metals Metals 2020, 10, 311 2 of 22 Metals 2020, 10, 311 2 of 22 A more complex dynamic model was developed by Logar et al. [13], which considered more parameters with respect to the heat transfer between all phases as well as post‐combustion. The predictedaverage predicted power-on power time,‐ tappingon time, temperaturestapping temperatures and final and Fe weights final Fe had weights differences had differences of 0.2 min, of 3 0.2 K, andmin, 1 3 t, K, respectively, and 1 t, respectively, compared tocompared the data to obtained the data from obtained the production from the production furnace. This furnace. is considered This is toconsidered be a good to agreement, be a good which agreement, illustrates which that illustrates a dynamic that model a dynamic can give model an accurate can give prediction an accurate of anprediction EAF process. of an EAF Hay process. et al. [14 Hay] improved et al. [14] the improved accuracy the of accuracy the model of developedthe model developed by Logar et by al. Logar [13] byet al. considering [13] by considering the equilibria the betweenequilibria the between metallic the and metallic oxidic and elements oxidic and elements the dissolved and the oxygendissolved in theoxygen bath in and the also bath by and introducing also by introducing a new zone a at new the zone metal at and the slagmetal interface and slag to interface the model to inthe order model to includein order the to include interfacial the reactions. interfacial reactions. KirschenKirschen etet al.al. [[15]15] usedused aa dynamicdynamic energy–massenergy–mass balance in an EAF to study the eeffectffect of the amountamount ofof chargedcharged DRIDRI withwith aa metallizationmetallization degree of 93% on the EAF energy eefficiency.fficiency. The results showedshowed anan increaseincrease ofof 1.19 kWhkWh/t/t of the required electrical energy, aa slightslight increase of injected oxygen 3 amount,amount, 0.0460.046 mm//tt, and a 13% decrease of thethe metal yield under a constantconstant taptap weight and slag O2 basicitybasicity perper eacheach percentpercent increaseincrease ofof DRIDRI additions.additions. The authors suggested that the increase of the requiredrequired electricalelectrical energyenergy couldcould bebe compensatedcompensated byby thethe chemicalchemical energy due to exothermic reactions whenwhen thethe injectedinjected oxygenoxygen reactedreacted with with dissolved dissolved alloying alloying elements elements originating originating from from scrap. scrap. TheThe aimaim ofof thisthis workwork is to develop a static mass and energy balance model of an EAF operation, integratedintegrated withwith aa MgOMgO saturationsaturation slagslag modelmodel asas aa webweb application.application. Real furnace data are used to calibratecalibrate thethe modelmodel parametersparameters forfor thatthat furnacefurnace and to determine the model accuracy. Afterward, the modelmodel isis appliedapplied inin order to evaluate the eeffectffect of HBI proportions in charged materials on the energy requirements,requirements, slagslag quantities,quantities, andand compositions.compositions. 2.2. Model Development AA black-boxblack‐box approachapproach isis appliedapplied byby usingusing thethe massmass andand energyenergy inputsinputs andand outputs inside EAFs consideringconsidering the the three three states states of of solid, solid, liquid liquid and and gas. gas. The The static static mass mass and energyand energy balance balance and slag and model slag calculationsmodel calculations are implemented are implemented as a Java as web a Java application web application called RAWMATMIX called RAWMATMIX® (Version® (Version 2.16, Kobolde 2.16, &Kobolde Partners & AB, Partners Stockholm, AB, Stockholm, Sweden). Sweden). The main The input main data input are the data quantities are the quantities of raw materials of raw materials and slag formers,and slag distribution formers, distribution factors of metallic factors elements,of metallic tapping elements, temperature, tapping finaltemperature, carbon concentration, final carbon oxygenconcentration, injection oxygen volume, injection burner volume, energy, and burner refractory energy, dissolutions and refractory into dissolutions melt and slag. into Besides, melt and the desiredslag. Besides, values ofthe slag desired properties values are of assigned. slag properties An outline are of assigned. the workflow An inoutline RAWMATMIX of the workflow® is shown in inRAWMATMIX Figure1. ® is shown in Figure 1. ® FigureFigure 1.1. AA flowchartflowchart ofof thethe calculation calculation procedure procedure used used in in RAWMATMIX RAWMATMIX.®. **The The reduced slag elementselements areare MnO,MnO, CrCr22O3,, FeO/Fe FeO/Fe2OO33, ,PP22OO5,5 and, and VO VO2. 2. Metals 2020, 10, 311 3 of 22 3. Model Description The mass and energy balance applied in the model is described below: 3.1. Mass Balance The mass balance is written by considering that all components in input materials and output products in an EAF can be written as follows: j i p i X8 X8 X8 X8 j = p Mi Mi (1) j i=1 p=1 i=1 j p where Mi and Mi are the mass of component i in material j and in product p, respectively. The mass input originates from the following sources: Raw materials, which include different types of scraps, DRI/HBIs, and carbon powders • Hot heel • Slag formers, consisting of lime and dolomite • Refractory components, which can be dissolved into slag • Oxygen injected through lances and consumed during the metal oxidation, decarburization, • powder carbon oxidation, fuel combustion in burners and post-combustion Fuel additions through the burners • The output mass includes the following products: Molten steel • Molten slag, which can also, possibly, contain solid MgO components • Hot heel • Dust components in metal oxide forms • Gas, which can consist of CO, CO , and N . • 2 2 The hot heel amount has been considered as both input and
Details
-
File Typepdf
-
Upload Time-
-
Content LanguagesEnglish
-
Upload UserAnonymous/Not logged-in
-
File Pages22 Page
-
File Size-