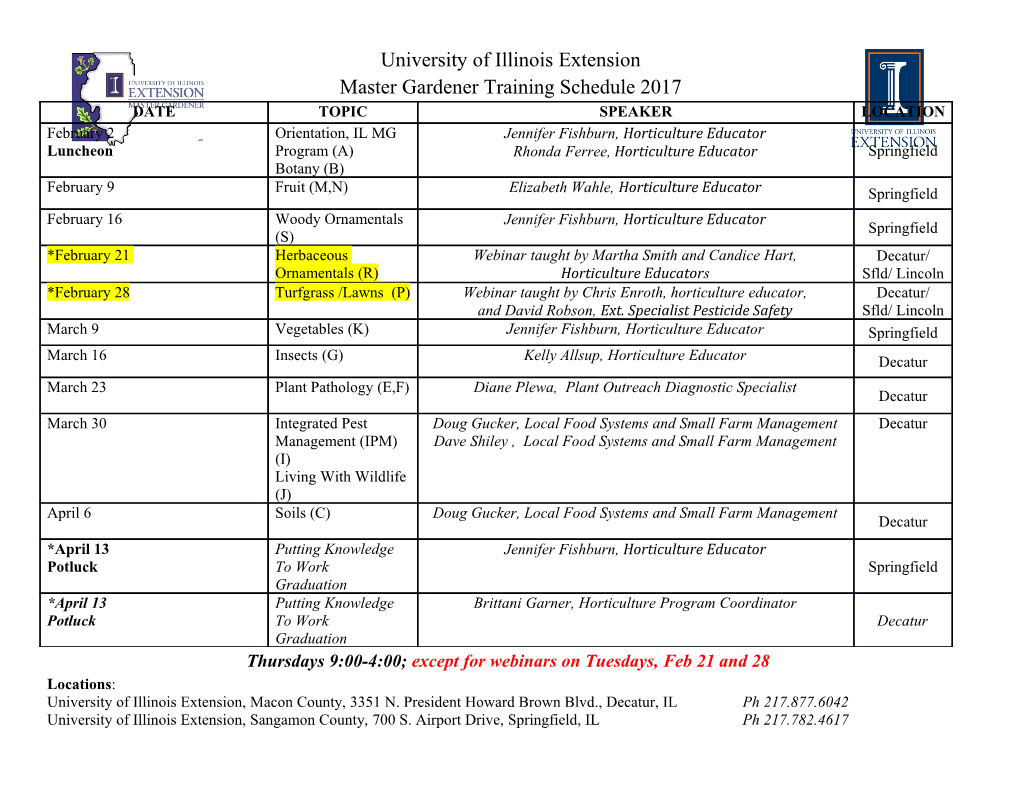
US 20170021385A1 (19) United States (12) Patent Application Publication (10) Pub. No.: US 2017/0021385 A1 SMITH et al. (43) Pub. Date: Jan. 26, 2017 (54) METHODS OF PREPARING SOLID Publication Classification PARTICLE SOLUTIONS FOR FORMING (51) Int. Cl. TEXTURED SURFACES BSD L/12 (2006.01) (71) Applicant: LiquiGlide Inc., Cambridge, MA (US) BOSD 3/02 (2006.01) (52) U.S. Cl. (72) Inventors: J. David SMITH, Arlington, MA (US); CPC ............... B05D 1/12 (2013.01); B05D3/0254 Tao CONG, Quincy, MA (US); (2013.01); B05D 2320/00 (2013.01) Ravikumar VASUDEVAN, Somerville, MA (US); Hamideh Mohammad (57) ABSTRACT ALIPOUR, Cambridge, MA (US); Embodiments described herein relate to methods of forming JiaPeng XU, Newton, MA (US); liquid-impregnated Surfaces, and in particular to methods of Charles W. HIBBEN, Darien, CT preparing Solid particle solutions for forming textured Sur (US); Brian John JORDAN, faces which can be impregnated with an impregnating liquid Winchester, MA (US) to form a liquid-impregnated Surface. In some embodiments, a method of forming a textured Surface includes dissolving (21) Appl. No.: 15/053,660 a solid in a solvent to form a solution. The solid has a concentration, which is less than a first Saturation concen (22) Filed: Feb. 25, 2016 tration of the solid in the solvent at a first temperature and greater than a second saturation concentration of the solid in the solvent at a second temperature. The solution is allowed Related U.S. Application Data to form a solid particle solution. The solid particle solution (60) Provisional application No. 62/120,630, filed on Feb. is then disposed on a Surface and the solvent is allowed to 25, 2015. evaporate to form the textured surface on the surface. OO 24, RCC Patent Application Publication Jan. 26, 2017. Sheet 1 of 14 US 2017/0021385 A1 Fig. 1A s ROC 2 -r % O SRFACE Fig. 1B -- E s Patent Application Publication Jan. 26, 2017. Sheet 2 of 14 US 2017/0021385 A1 , s 3 Patent Application Publication Jan. 26, 2017. Sheet 3 of 14 US 2017/0021385 A1 Fig. 3 200 Heat a sovert to a first temperature r 202 Dissoive a solid in the sovert to foin a solition 204 Dispose the said particia solation of a stiriace N210 Evaporate the sowent to form a textured surface 212 Patent Application Publication Jan. 26, 2017. Sheet 4 of 14 US 2017/0021385 A1 Patent Application Publication Jan. 26, 2017. Sheet 5 of 14 US 2017/0021385 A1 Patent Application Publication Jan. 26, 2017. Sheet 6 of 14 US 2017/0021385 A1 Fig. 6A Patent Application Publication Jan. 26, 2017. Sheet 7 of 14 US 2017/0021385 A1 Patent Application Publication Jan. 26, 2017. Sheet 8 of 14 US 2017/0021385 A1 Patent Application Publication Jan. 26, 2017. Sheet 9 of 14 US 2017/0021385 A1 Patent Application Publication Jan. 26, 2017. Sheet 10 of 14 US 2017/0021385 A1 Patent Application Publication Jan. 26, 2017. Sheet 11 of 14 US 2017/0021385 A1 Patent Application Publication Jan. 26, 2017. Sheet 12 of 14 US 2017/0021385 A1 Patent Application Publication Jan. 26, 2017. Sheet 13 of 14 US 2017/0021385 A1 Patent Application Publication Jan. 26, 2017. Sheet 14 of 14 US 2017/0021385 A1 x goes g i. US 2017/002 1385 A1 Jan. 26, 2017 METHODS OF PREPARING SOLID SUMMARY PARTICLE SOLUTIONS FOR FORMING 0008 Embodiments described herein relate to methods of TEXTURED SURFACES forming liquid-impregnated Surfaces, and in particular to methods of preparing Solid particle Solutions for forming CROSS-REFERENCE TO RELATED textured Surfaces which can be impregnated with an impreg APPLICATIONS nating liquid to form a liquid-impregnated Surface. In some 0001. This application claims priority to and the benefit embodiments, a method of forming a textured Surface of U.S. Provisional Patent Application Ser. No. 62/120,630, includes dissolving a solid in a solvent to form a solution. filed Feb. 25, 2015 and titled “Methods of Preparing Solid The Solid has a concentration, which is less than a first Particle Solutions for Forming Textured Surfaces, the dis saturation concentration of the solid in the solvent at a first closure of which is hereby incorporated by reference in its temperature and greater than a second Saturation concentra entirety. tion of the solid in the solvent at a second temperature. The solution is allowed to form a solid particle solution. The BACKGROUND Solid particle solution is then disposed on a surface and the solvent is allowed to evaporate to form the textured surface 0002 Embodiments described herein relate to methods of on the Surface. forming liquid-impregnated Surfaces, and in particular to methods of preparing Solid particle Solutions for forming BRIEF DESCRIPTION OF THE DRAWINGS textured surfaces which can be impregnated with an impreg nating liquid to form a liquid-impregnated Surface. 0009 FIG. 1A is a schematic cross-section view of a product contacting a conventional non-wetting Surface, and 0003. The advent of micro?nano-engineered surfaces in the last decade has opened up new techniques for enhancing FIG. 1B shows the conventional non-wetting surface such a wide variety of physical phenomena in thermofluids sci that the product has impaled the Surface. ences. For example, the use of micro?nano Surface textures 0010 FIG. 2 is a schematic cross-section of a liquid has provided non-wetting Surfaces capable of achieving less impregnated Surface according to an embodiment. Viscous drag, reduced adhesion to ice and other materials, 0011 FIG. 3 is a schematic process flow diagram of a self-cleaning, and water repellency. These improvements method of forming a textured Surface, according to an result generally from diminished contact (i.e., less wetting) embodiment. between the solid surfaces and adjacent liquids. (0012 FIG. 4 is an image of 75 mL emulsion of rice bran 0004 One type of non-wetting surface of interest is a wax and ethanol in a glass container, prepared using an Super hydrophobic Surface. In general, a Super hydrophobic embodiment of the method described herein. Surface includes micro?nano-scale roughness on an intrinsi 0013 FIG. 5 is an interferometry image of the textured cally hydrophobic Surface. Such as a hydrophobic coating. surface formed by spraying solid solution shown in FIG. 4 Super hydrophobic surfaces resist contact with water by on an inner surface of the PET bottle. virtue of an air-water interface within the microfinano Sur 0014 FIG. 6A is an SEM image of the textured surface face textures. of FIG. 5, and FIG. 6B is a higher magnification SEM image 0005 One of the drawbacks of existing non-wetting of a portion of the textured surface shown in FIG. 6A. Surfaces (e.g., Superhydrophobic, Superoleophobic, and (0015 FIG. 7A is an SEM image of a textured surface supermetallophobic surfaces) is that they are susceptible to formed by spraying a solution of silicone wax dissolved in impalement, which destroys the non-wetting capabilities of heptane and including a silicone based sealant on a PET the Surface. Impalement occurs when an impinging liquid surface. FIG. 7B is a higher magnification SEM image of a (e.g., a liquid droplet or liquid stream) displaces the air portion of the textured surface shown in FIG. 7A. entrapped within the surface textures. Previous efforts to 0016 FIG. 8A is an SEM image of a textured surface prevent impalement have focused on reducing Surface tex formed by disposing a solution of a first component of ture dimensions from micro-scale to nano-scale. beeswax dissolved in ethanol on a PET surface. FIG. 8B is 0006 Another drawback with existing non-wetting sur an SEM image of a textured surface formed by disposing a faces is that they are susceptible to ice formation and Solution of a second component of beeswax dissolved in adhesion. For example, when frost forms on existing Super ethyl acetate on a PET surface. hydrophobic surfaces, the surfaces become hydrophilic. 0017 FIGS. 9-11 are interferometry images showing Under freezing conditions, water droplets can Stick to the particle size distribution of textured surfaces formed on a Surface, and ice can accumulate. Removal of the ice can be PET Surface by disposing emulsions prepared by dissolving difficult because the ice may interlock with the textures of the rice bran wax in ethanol, diisoproyl ether, and isopropyl the surface. Similarly, when these surfaces are exposed to alcohol, respectively. Solutions Saturated with salts, for example as in desalination 0018 FIG. 12 is an interferometry image of a textured or oil and gas applications, Scale builds on the Surfaces and surface formed on a PET surface by disposing a water based results in loss of functionality. Similar limitations of existing emulsion of carnauba wax in water and including a sodium non-wetting Surfaces include problems with hydrate forma chloride additive, on the surface. tion, and formation of other organic or inorganic deposits on 0019 FIG. 13 is an interferometry image of a textured the Surfaces. Surface formed on a PET surface by disposing a first coating 0007 Thus, there is a need for non-wetting surfaces that of a water based emulsion of carnauba wax in water and are more robust. In particular, there is a need for non-wetting including a sodium chloride additive which is allowed to Surfaces that are more durable and can maintain highly dry, and a second coating of the water based emulsion of non-wetting characteristics even after repeated use. carnauba wax in water is then disposed on the first coating. US 2017/002 1385 A1 Jan. 26, 2017 0020 FIG. 14 is an interferometry image of a textured liquid-impregnated Surfaces facilitate an increased evacua surface formed on a PET surface having superhydrophobic tion speed of product-containing containers (e.g., making it properties by depositing a solution of isotactic polypropyl possible to use higher viscosities of certain products in ene in xylene and 2-butanone on a PET surface.
Details
-
File Typepdf
-
Upload Time-
-
Content LanguagesEnglish
-
Upload UserAnonymous/Not logged-in
-
File Pages34 Page
-
File Size-