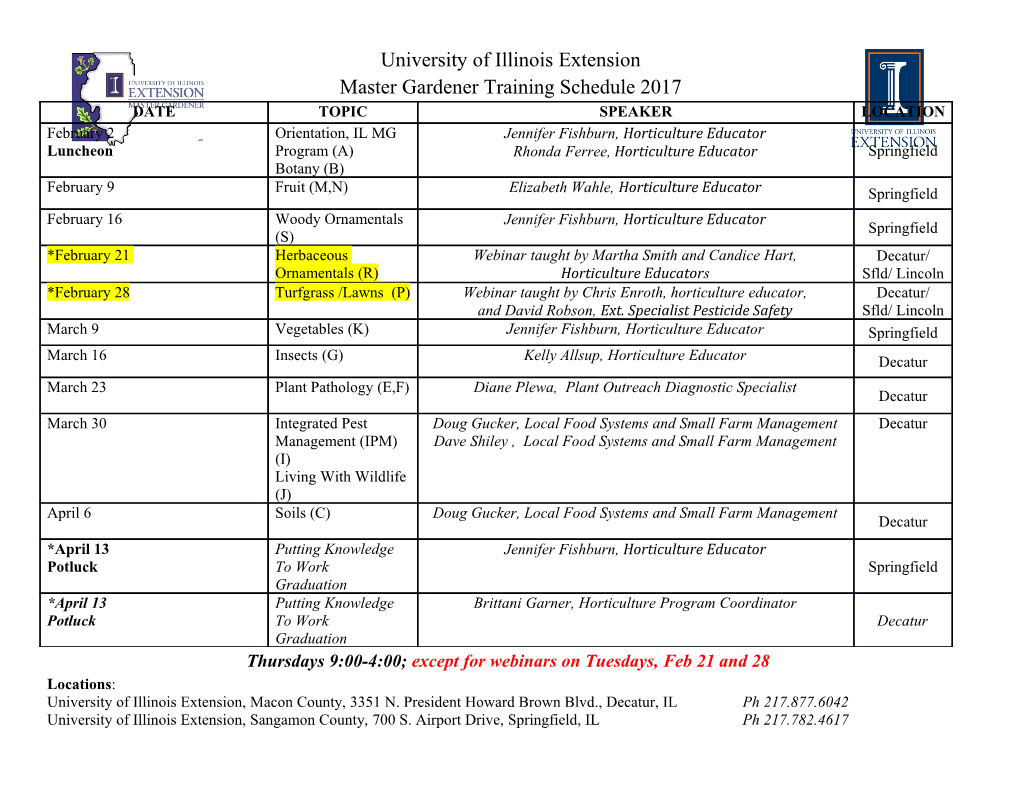
How to control a motor Control Using Pulses Electric Motor The first direct current electric motor was invented by William Sturgeon in 1832.This breakthrough followed by subsequent advances in the field , facilitated improvements in industrial processes by improving the efficiency of mechanized systems . Direct Current electric motors are based on the principles of electromagnetic induction and are typically comprised of six major components . An Armature, a Commutator , Brushes, an axle, a field magnet and a power supply. The commutator is a single metallic ring that is split into two. It allows the current to flow into the armature. The field magnet is fixed in place and is sometimes called a stator. The armature is the moving coil at the center of the motor that rotates on the axle .The armature becomes an electromagnet when current is flowing through it .This current carrying wire experiences a force which is given by Flemings left hand rule. This force causes the armature to rotate around the axle. The commutator effectively reverses the direction of the current and hence the force on the armature and allows it to keep spinning . Figure 1.1 Simple DC Motor DC Motor Control using Pulses By increasing or decreasing the width of pulses we can control the average voltage across the load. By switching voltage to the load , the output will approximate a voltage at the desired level. The following block diagram shows the system that we will implement to control the motor. Figure 1.2 Speed Controller Block Diagram The PWM block shown above can be implemented with the use of a Micro-Controller such as the MSP430 from Texas Instruments. Analogue Electronics can also be used to generate a PWM pulse to control the switching of the motor. Building MOSFET Bridge Fig 1.3 Simple Motor Controller When pulses are connected, Q1 turns on and off and we can control the average voltage . La is added to the model to represent that the motor is an inductive load . Though this circuit will function correctly as a motor controller we can add improvements to aid with efficiency. We will add three more transistor .The resulting structure is called an H bridge. Full Implementation The above figure shows a schematic of the Motor control system . We combine the bridge system implemented earlier with a current protection system . The U1A Op- Amp amplifies the voltage drop across the sense resistor .The output of the UA1 amplifier is fed to a comparator with a reference voltage V5 .If the current high. The LM324 comparator will “Turn ON” and clamp the PWM signal causing both transistor to turn off thus preventing any damage. References http://homepages.which.net/~paul.hills/SpeedControl/SpeedControllersBody.html http://www.magnet.fsu.edu/education/tutorials/java/dcmotor/index.html http://fab.cba.mit.edu/classes/MIT/961.04/topics/pwm.pdf .
Details
-
File Typepdf
-
Upload Time-
-
Content LanguagesEnglish
-
Upload UserAnonymous/Not logged-in
-
File Pages4 Page
-
File Size-