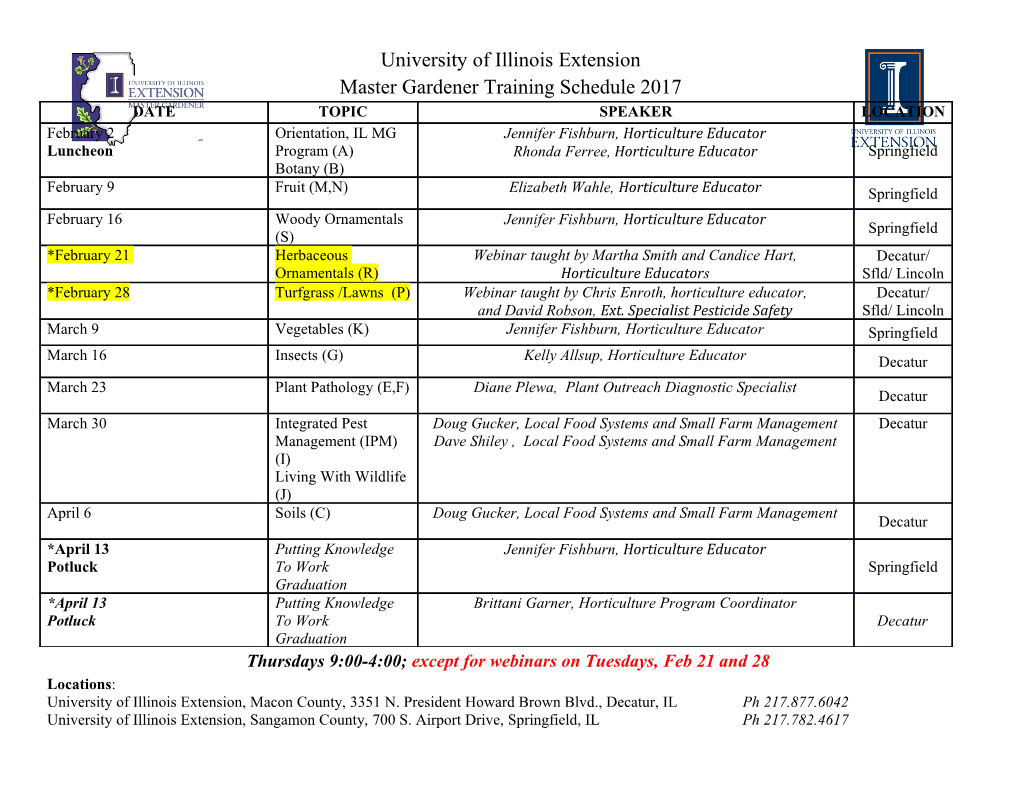
Modern Advances in Fan and Compressor Design Using CFD Riccardo Balin1 University of Colorado Boulder, Boulder, CO 80309 In this paper a literature review of the state of the art of fan and compressor blade design is presented. In particular, the role played by CFD simulations in the understanding of fully three-dimensional flow is reviewed, as well as the 3-D design features that can be studied with high fidelity simulations. The paper focuses on the effects of leading edge recambering, sweep, dihedral, and endwall contouring on the secondary flow structures typical of turbomachinery, in order to provide a guideline to the most efficient design solutions. The effect of blade sweep is also considered in the context of fan and compressor surge. I. Introduction OMPRESSOR and fan design for air breathing machines applied to aircraft propulsion has made some drastic C leaps forward since the beginning of the jet era with the Jumo 004 and Whittle engines. At the core of the continuous development and research being carried out in this field is the everlasting search for high efficiency, low noise, durable and safe machines to improve air travel. In the world of commercial air travel, some of these aspects are extremely important, and can define the immense success or drastic failure of a design. Commercial air travel is a multi-trillion dollar business, driven mainly by airline companies and their desire to profit. In recent years, airline companies have been pushing aircraft and engine manufacturers to design more efficient, safer and quieter products. As a consequence, manufacturers are forced to stretch the design limits of their products and come up with new and creative designs to meet the requirements set by their customers. In addition, regulatory agencies such as the FAA and the European counterpart EASA are constantly raising the demands set on aircraft and engines with the goal of making travel safer and more comfortable. Some of these requirements involve the amount of production of nitrogen oxides during combustion, some involve noise levels at airports, and some involve the robustness of the engines to ingestion of foreign bodies. Focusing on the fan and compressor components of an air a) breathing engine, the requirements that drive most of the research in the field are minimizing losses, or equivalently maximizing efficiency, minimizing noise production, and increasing the reliability of the engine. Given the increase in fuel prices of the last couple decades, as well as the increased general awareness towards environmental issues, airlines are always demanding a reduction in the specific fuel consumption of the engines. Similarly, both airlines and regulatory agencies are demanding that the engines by quieter in order to make air travel and locations with dense air traffic more appeasable to the public. Engine reliability specific to fans and compressors can be thought as an increased surge and stall margin, thus reducing the possibility of engine failure. b) All of the aforementioned requirements (reduced fuel Figure 1. Comparison between a) modern consumption, reduced noise, increased stall margin) can be met 1 with blade and endwall design. Until recent years, blade design and b) legacy turbofan engine rotors. 1 Graduate student, Department of Aerospace Engineering Sciences, Student Member AIAA. 1 was very much limited to a two-dimensional analysis of the flow over an airfoil. The analysis would be iterated in order to achieve the airfoil profile which would produce the desired flow, and then the blade would be constructed by stacking the airfoils on top of each other. The two-dimensional profile of the blade could be optimized for different spanwise locations, but only a few locations were chosen for practicality. With this design methodology, three-dimensional effects such as sweep and dihedral could not be analyzed. Experimental tests could be conducted to study such 3-D effects, however this approach is expensive and time consuming. Regardless of these limitations that prevent full 3-D design of fan and compressor blades, the state of the art in the field has made incredible progress. Figure 1 shows a comparison between a modern high bypass ratio fan (Fig. 1a) and a legacy fan (Fig. 1b). The differences are obvious, and it is clear that blades are now fully three- dimensional. The main factor that allowed such progress is the advent of Computational Fluid Dynamics (CFD) and the development of turbulence models that can reproduce high fidelity results even for complex flows, while not requiring incredibly expensive simulations. More specifically, it is the combined effect of high speed computers with the development of accurate and efficient CFD codes that enabled fully 3-D flow analysis to be introduced into the design process, even at early stages. The fact that it is now possible to study a complex, fully 3-D flow in simulations with fast turn-around time means that blade design is no longer limited to airfoil profiling, but instead a number of other possibilities are introduced. Researchers have been exploiting this new technology to span the 3-D design space, and have been able to understand the 3-D properties of flows across fans and compressor, and how 3- D blades affect them. This paper consists of a literary review of the state of the art of 3-D fan and compressor blade and endwall design using CFD. It will focus both on characterizing the three-dimensionality of the flow across fans and compressors, and on the changes that can be made to the geometry in order to affect the flow properties. The rest of the paper is divided in to four sections, namely twist, sweep, dihedral and endwall contouring. The first three relate to changes to the blade geometry directly, while the last is focused more on the interaction between blade and endwall. In these sections, the effects of 3-D blade design on noise, losses and surge margin are outlined. II. Twist One three-dimensional design feature that can be implemented in compressor and fan blades is geometric twist. Note that this feature is implemented in rotor blades, and not as often on stator blades. The main effect of blade twist is to ensure that every section of the blade operates at the desired incidence angle with the incoming flow. The relative wind seen by a blade airfoil is the vector sum of the incoming absolute velocity and the velocity of the blade generated by its rotation. The latter is a function of the radial distance of the airfoil section to the hub of the rotor, so the direction of the relative wind changes with radial distance. At the hub, where the blade tangential speed is small, the direction of the incoming Figure 2. Contours of relative velocity measured flow is almost axial, while at the tip it is almost experimentally at a rotor exit. 4 entirely in the tangential direction.2 In order to maintain the angle of attack of the blade section at good operating values, it is necessary for the blade to be twisted. An example of twist on a fan blade is seen in Fig. 1a. It is noticed that closer to the hub, the chord of the blade section is almost parallel to the axial direction in accordance with the direction of the relative velocity. Instead, the tip blade section is almost at 90° to the axial direction. One interesting difference between blade twist for fans and compressors is the fact that for a fan, the amount of twist is dictated by the design free stream Mach number, the design fan rpm and by the fan dimensions. However, a compressor blade is fairly short compared to a fan blade, especially at the last stages of a high pressure compressor. At these reduced dimensions, the height of the boundary layer that develops on the casing walls becomes significant relative to the blade length. This is particularly true because regions of secondary flow create at the endwall of a compressor due to tip vortices and possible separation of the flow on the blades of the previous stage. In addition, for rotating components, the boundary layer which forms on the surface of the blades is subject to significant centrifugal forces. This results in the boundary layer flow being pushed radially outward towards the trailing edge of the tip of the blades.3 This accumulation of low energy fluid at the tip of the blade promotes flow separation. Figure 2 2 shows contours of velocity measured experimentally at the exit of a rotor stage, from which the secondary flow region at the junction between the tip of the blade and the casing endwall is clear. Because of this accumulation of low energy, secondary flow on the wall of the casing, the tip of rotor and stator blades see a reduction in axial velocity, which increases significantly the incidence angle. Consequently, it is desirable to twist the sections of compressor blades near the tip to achieve the desired incidence angle and loading on the whole blade.5 This type of blade twisting, which is specific to compressor blades and not fan blades, is given the name of leading edge recambering (LER). As the name suggests, LER involves more than a simple twist of the airfoil about its centroid. The airfoil camber, chord and thickness are redesigned to optimize performance in this region of the flow. It is Figure 3. Effect of LER on velocity contorus (original 6 extremely difficult to predict the physics of these blade on left, LER modified on right). secondary flow structures without the use of a CFD simulation. In fact, it can be stated that secondary flow effects on turbomachinery can only be understood with CFD analysis5, which is essential for proper LER design.
Details
-
File Typepdf
-
Upload Time-
-
Content LanguagesEnglish
-
Upload UserAnonymous/Not logged-in
-
File Pages8 Page
-
File Size-