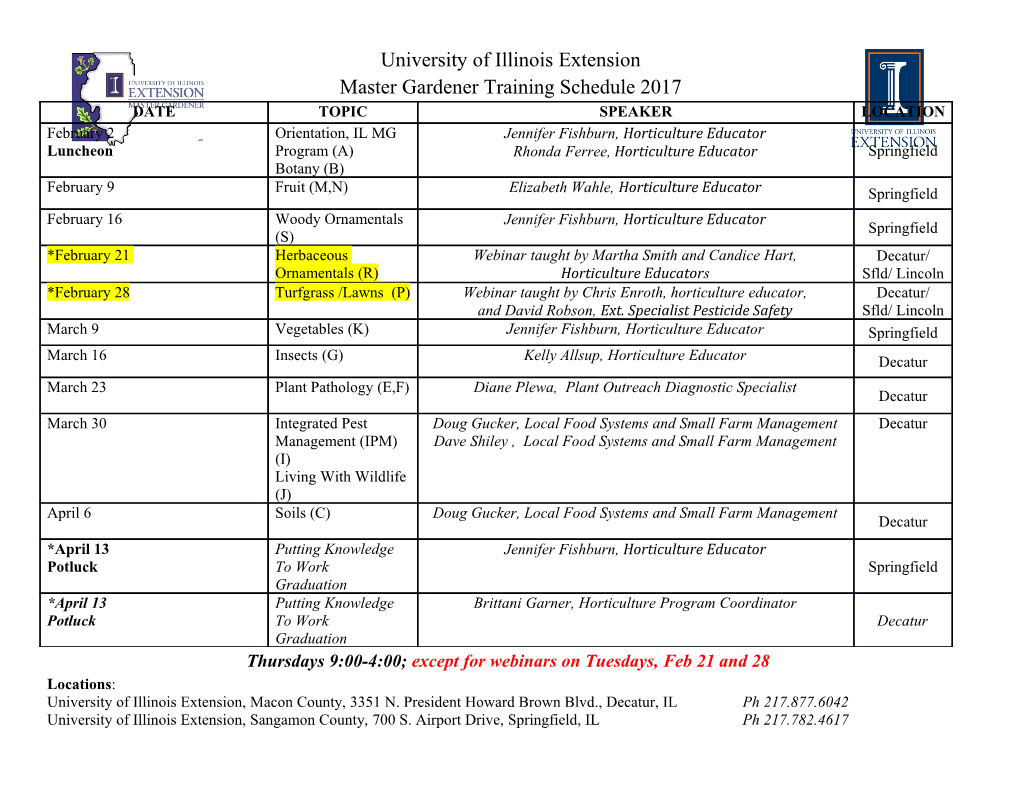
COMPUTER-AIDED DESIGN & APPLICATIONS, 2017 VOL. 14, NO. 6, 734–741 https://doi.org/10.1080/16864360.2017.1287675 Future trends in CAD – from the perspective of automotive industry Mario Hirz a, Patrick Rossbacher a and Jana Gulanová b aGraz University of Technology, Austria; bSlovak University of Technology in Bratislava, Slovakia ABSTRACT KEYWORDS Computer-aided design (CAD) plays a central role in automotive development. 3D-CAD models Future CAD; visualization not only provide geometry information, but also serve as a basis for configuration of modules and technology; adaptable systems, as well as for different simulation and verification processes. Product assemblies within models; generic CAD-platforms include structure-related information, are used for digital mock-up (DMU) investiga- programming; development processes tions and provide lots of data for production and manufacturing engineering. Since first CAD systems have been applied in automotive industry in the 1980s, design software has been developed steadily, so that today’s CAD programs are able to provide far-reaching possibilities for integrated product development. The present paper includes an introduction and evaluation of existing and upcoming technolo- gies for their use in future CAD programs and discusses different scenarios of implementation into automotive development. Vehicle architects, design engineers, project managers, IT-administrators for CAD, stylists as well as styling engineers have contributed to a survey at automotive manufacturer and supplier. The results of this survey are brought into this paper to discuss the future role of CAD in the development of new cars and to define requirements for the next generation of CAD software. 1. Introduction: CAD in automotive development different disciplines are shown in relation to the cor- responding phases. The diagram highlights the deep Through the middle 1980s, automotive development pro- integration of CAD into automotive development: all cesses were characterized by a high degree of hardware development disciplines are related to CAD data or pro- and prototype-based optimization cycles. At that time, cesses.Mostofstyling,designandsimulationworksis full-vehicle development had a duration of about 6 years done in CAD or based on CAD data (e.g. in case of and included three prototype phases. The integration of computer-aided engineering, CAE). Even disciplines that virtual, computer-aided methods into automotive devel- do not include CAD work show a certain involvement of opment led to significantly revised processes. In the mid- CAD data: for evaluation purposes, prototyping and data dle of the 1980s, computer-aided design and simulation exchange with supplier. methods began taking over engineering tasks that had In the upcoming years, the share of conceptual work formerly been done via hardware based development. in the area of electronics and communication technology In the closing years of the twentieth century, integrated will increase rapidly. During the past decade, the signifi- CAD/CAE processes enabled network-based develop- cance of these mechatronics technologies has been raised ment in automotive engineering. Virtual prototypes were from comfort-related features to integrated modules with generated, which replaced at least one physical prototype a strong impact on drivetrain, vehicle safety and auto- generation. The application of virtual engineering in full- mated driving functionalities [13]. The high complexity vehicle development fostered worldwide collaboration by ofelectronicsnetworkschallengesestablisheddevelop- bringing together partners and markets from different ment processes and requires new approaches for the inte- countries and regions. Today, full-vehicle development gration of traditional mechanical oriented development projects take 4 years (in case of derivate development and electronics & software development. less than 3 years) and the trend is moving towards an The Definition Phase includes a compilation of additional decrease [11]. characteristics of the new car to be developed. This Figure 1 shows a typical automotive full-vehicle devel- contains market research of future trends, customer opment process. In addition to the main process phases, demands and legislative boundary conditions. In CONTACT Mario Hirz [email protected] © 2017 CAD Solutions, LLC, http://www.cadanda.com COMPUTER-AIDED DESIGN & APPLICATIONS 735 Figure 1. Process phases and development disciplines in a typical state-of-the-art full-vehicle development process, according to [11]. addition, manufacturer-related strategic aspects are con- The Pre Development Phase includes a continuation sidered, e.g. integration of the planned model into exist- of concept development under consideration of detailed ing platforms. At the end of the Definition Phase,the technological and economical aspects. This covers final- specification list is defined, which provides requirements ization of styling works, 3D-CAD engineering of all com- definition for subsequent vehicle development. In this ponents and modules, as well as far reaching valida- initial phase, CAD - data of existing car models and plat- tion. In addition to virtual development, prototypes of forms is involved for technical and economic potential- modules and even vehicles are tested and investigated evaluation of the planned new car. on test beds and on road. In this phase, the new car The development process itself starts with the Con- model is completely developed in 3D-CAD including a cept Phase, which comprises the complete vehicle lay- detailed representation in DMU as a basis for produc- out, including styling, vehicle packaging and ergonomics, tion engineering tasks. In this way, supplier are increas- as well as body and component development. Begin- ingly involved into the development. In view of CAD, ning with initial styling works, the vehicle architecture this phase challenges data transfer from the central CAD is build up and all components are integrated. Drive- model to simulation procedures and vice versa, as well as train modules are taken over from existing platforms or between car manufacturer, external engineering partner developed newly, including new technologies, e.g. elec- and module supplier. At the end of the Pre Develop- tric or hybrid drivetrains. The entire concept phase is ment Phase, the new car model is developed including strongly related to CAD in its different types of occur- all modules and technologies, exempt from E/E compo- rence. There are computer-aided styling (CAS) for shap- nents. Due to the different development cycles of elec- ing works, computer-aided design (CAD) as engineering tric/electronic components and software, these elements discipline, as well as related computer-aided engineering are still under development, even after the hardware (CAE). CAE comprises digital mock-up (DMU) and dif- models are finished so far. ferent types of simulation, e.g. multi-body simulation for The Series Development Phase hasastrongrela- kinematics (MBS), finite-elements simulation (FEM) for tion to production development and supplier integra- stress, durability and crash simulation, as well as com- tion including logistics, assembling processes and qual- putational fluid dynamics simulation (CFD) for aerody- ity engineering. In this phase, the virtual vehicle model, namics and heat management investigations. All these represented in a complex CAD structure, serves as a CAE tasks are supplied with geometrical and functional basis for far reaching investigations of production-related data from a central CAD model. Simulation results are procedures. This requires extensively data exchange transferred back into the CAD model and used for design between vehicle engineering and production engineer- confirmation or modification jobs on certain compo- ing, whereby the final design is influenced by require- nents and modules. In this way, the CAD model plays a ments from production. At the end of this phase, both centralroleintheconceptphaseofanewcar. the new car model and its production are completely 736 M. HIRZ ET AL. developed and all interactions with manufacturing facil- design applications. Parameterized CAD programs offered ities and supplier are defined. The development status of additional functionalities, such as data interfaces, inte- the central CAD vehicle model is frozen for production. gration of catalogue and knowledge ware functions, and The final phase of car development includes Pre Series the possibility of macro-based procedures. All of these and Series Production. Final settings of the assembly line functionalities characterize state of-the-art CAD pack- and in the logistics management are done during the pro- ages, which come into use in automotive development. duction of initial pre series models. This includes final adjustmentofmachinesandrobotsaswellasquality- 2.1. Future CAD systems: easy to handle design related investigations, e.g. in the paint shop or in view software or integrated development platform? of tolerancing. As during the entire production devel- opment, the central CAD vehicle model provides data One trend in software industry is going into the direc- for manufacturing and assembling fine-tuning. After tion of integrated packages, which combine parametric homologation of the new car in target markets, series design programs (CAD) and simulation software (CAE) production phase starts. During series production, the in the same environment. Although this strategy reduces central
Details
-
File Typepdf
-
Upload Time-
-
Content LanguagesEnglish
-
Upload UserAnonymous/Not logged-in
-
File Pages8 Page
-
File Size-