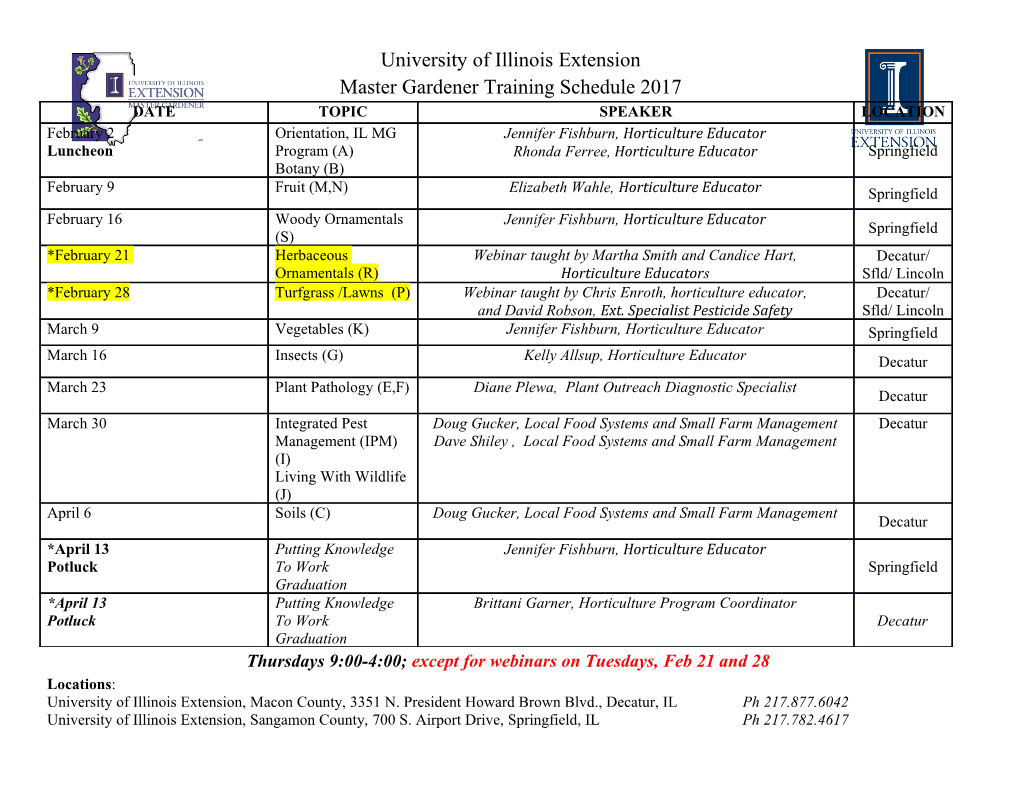
ADVISORY CIRCULAR 43-16A AVIATION MAINTENANCE ALERTS ALERT SEPTEMBER NUMBER 2007 350 CONTENTS AIRPLANES BEECH ........................................................................................................................................1 CESSNA ......................................................................................................................................3 MAULE .......................................................................................................................................7 HELICOPTERS EUROCOPTER ...........................................................................................................................7 SIKORSKY..................................................................................................................................7 ACCESSORIES AEROTECH ALTERNATOR.....................................................................................................9 ECI CYLINDER........................................................................................................................10 WIPAIRE...................................................................................................................................10 AIR NOTES INTERNET SERVICE DIFFICULTY REPORTING (iSDR) WEB SITE...............................10 IF YOU WANT TO CONTACT US.........................................................................................11 AVIATION SERVICE DIFFICULTY REPORTS ...................................................................12 September 2007 AC 43-16A U.S. DEPARTMENT OF TRANSPORTATION FEDERAL AVIATION ADMINISTRATION WASHINGTON, DC 20590 AVIATION MAINTENANCE ALERTS The Aviation Maintenance Alerts provide a common communication channel through which the aviation community can economically interchange service experience, cooperating in the improvement of aeronautical product durability, reliability, and safety. This publication is prepared from information submitted by those who operate and maintain civil aeronautical products. The contents include items that have been reported as significant, but have not been evaluated fully by the time the material went to press. As additional facts such as cause and corrective action are identified, the data will be published in subsequent issues of the Alerts. This procedure gives Alerts’ readers prompt notice of conditions reported via a Malfunction or Defect Report (M or D) or a Service Difficulty Report (SDR). Your comments and suggestions for improvement are always welcome. Send to: FAA; ATTN: Aviation Data Systems Branch (AFS-620); P.O. Box 25082; Oklahoma City, OK 73125-5029. (Editor’s notes are provided for editorial clarification and enhancement within an article. They will always be recognized as italicized words bordered by parentheses.) AIRPLANES BEECH Beech: A36; Fretting Engine Mount Bolts; ATA 7120 A mechanic with an inspection authorization writes, “I performed an annual inspection on (this aircraft’s) engine and found black fretting corrosion below the center two, L/H aft engine mount bolts. (These) bolts were loose in the mount (even though...) the nuts were tight on the bolts. The problem is the bolts are a little too long—the nuts were running out of threads on the bolts. The solution was to add another washer below the nuts, then re-torque back to specifications.” (The submitter did not indicate whether or not he knew these bolts to be original—their part numbers were not provided.) Page 1 AC 43-16A September 2007 Part Total Time: (1,672.1 hours.) Beech: B24R; Blown Electrical Capacitor; ATA 2340 “(An aircraft operator...) had drawn the battery charge down considerably, trying to start the aircraft,” states a technician. The pilot reported hearing a “pop”—then (seeing) smoke in the cabin. Take-off was aborted and an emergency gear up landing was made, resulting in substantial damage to the aircraft. On inspection a capacitor was found secured to the aft end of the audio control panel...installed in the KN4CB wire. The capacitor had the end blown out and its contents splattered on the windshield air duct. Page 2 September 2007 AC 43-16A “Probable cause: the low battery charge coupled with the high in-rush current demand of the gear motor—over and above the normal demands of the avionics—most likely resulted in an over-voltage condition, causing the capacitor to explode.” (A similar event happened to a cohort flying an experimental several years back. He described smoke so thick in the cockpit both he and his wife were certain the aircraft was on fire. They effected a safe landing in a farmer’s field, later discovering a three dollar part the cause of their near calamity—Ed.) Part Total Time: (unknown). CESSNA Cessna: 172K; Chafing Fuel Line; ATA 2820 A mechanic writes, “During an Annual Inspection, both engine fuel supply lines were found to be chafing on the forward bulkhead of the landing gear box structure at (bulkhead) station 56.70. Cessna has installed a thin plastic sleeve over the lines in the area of the chafe, but after 2,564 hours this sleeve is chafed to the extent the tubes will no longer be protected. I feel the tube integrity would be compromised in the future. Additional chafe protection and line security (hardware) is required. The Cessna 172 IPC (internal parts catalog; figure 167) illustration shows a heavier chafe barrier installed on the tubes in the area noted above. I suggest bonding a length of MIL-H-6000 3/8 inch (inside dimension) over the Cessna line in the chafe areas. Additional adjustment of the existing line clamps may also be required. See the attached illustrations.” Page 3 AC 43-16A September 2007 Page 4 September 2007 AC 43-16A Page 5 AC 43-16A September 2007 (Good eyeballs, Mike...and good advice!—Ed.) Part Total Time: 2,564.6 hours. Cessna: T310Q; Leaking Pitot System; ATA 3411 A mechanic states, “During a routine pitot/static test it was found the pitot system was leaking beyond limits. The leakage was determined to be in the tubing—from the pitot tube to the forward cabin bulkhead fitting. “Upon removing the tube (P/N 0800106-379) severe corrosion was found (on this line) at the aft end, near the fitting. This portion (of the static line) was found half buried in the outer insulation of a heat duct on the left, outboard side—allowing moisture to be trapped. This area is difficult to inspect and damage to the tube could go undiscovered until a leak test is performed. “It is recommended operators of 310 series aircraft have this line inspected, and that chafe protection be applied to the tube where it contacts the insulation of the heat duct.” Part Total Time: (unknown). Page 6 September 2007 AC 43-16A MAULE Maule: M7-235-C; Improper Seal of Main Gear Drag Link; ATA 3213 A repair station submitter writes, “This aircraft came in for its first annual inspection after installation...(of Wipline 3000A floats). Upon inspection (we) found the main gear drag link (P/N 30A04000-091) had not been properly sealed at the lower end, allowing water to enter the assembly. Because of the sealant we are unable to tell if the inside of the tube has some sort of corrosion protection. (One may wish...) to consider doing away with the sealant and applying a corrosion preventative compound, coupled with recurrent inspections and reapplication of CPC (corrosion preventative compounds).” Part Total Time: 86.8 hours. HELICOPTERS EUROCOPTER Eurocopter: EC 130-B4; Engine Chip Detection; ATA 7930 The director of maintenance for an operator states, “A precautionary, off-airport landing (was made) due to an engine oil chip annunciation light in flight. (There was...) an uneventful landing: no injuries; no damage to the aircraft or property. Maintenance investigated and found one small, hair-like dark chip. The plug was cleaned and the engine was test run for ten minutes. The engine run-down time was checked—it was normal. No additional chips were found. The aircraft was flown back to the maintenance base empty (of passengers). The chip plug was re-inspected for additional chips and (another) very small chip was noted. The chip plug was pulled on the accessory case and one small chip was noted there as well. The engine oil was drained, strained, and inspected for chips—none were found. The oil filter was removed and inspected—no chips. (The engine oil and filter were replaced with new, then a ground run was performed for 10 minutes.) No chips were found on either plugs.” “The aircraft was test flown for approximately fifteen minutes. (No chips were found after the flight.) As per the manufacturer’s instructions, the chip detector(s) is to be re-inspected after the first flight of the day for the next 25 flight hours. “Probable cause: the chip detector(s) and support systems worked properly, alerting the pilot of a potential problem. (There was...) a false indication because of the chip detector’s inability to differentiate one versus many chips.” (No part number accompanied this report.) Part Total Time: 1,999.7 hours. SIKORSKY Sikorsky: S92A; Failed Brake Stator; ATA 3242 A submitter from the Great Lakes region says, “During a (left hand, outboard) wheel change, (we) could not remove the wheel off the axle. (We) found one of the center stators (P/N A35579) of the brake assembly to be protruding out of the pack. The stator cut into the wheel, preventing its removal. We did not tear down the brake but suspect either the stator is out of round or has internal diameter damage, or the torque tube is damaged— allowing the stator to shift beyond the pack circumference."
Details
-
File Typepdf
-
Upload Time-
-
Content LanguagesEnglish
-
Upload UserAnonymous/Not logged-in
-
File Pages65 Page
-
File Size-